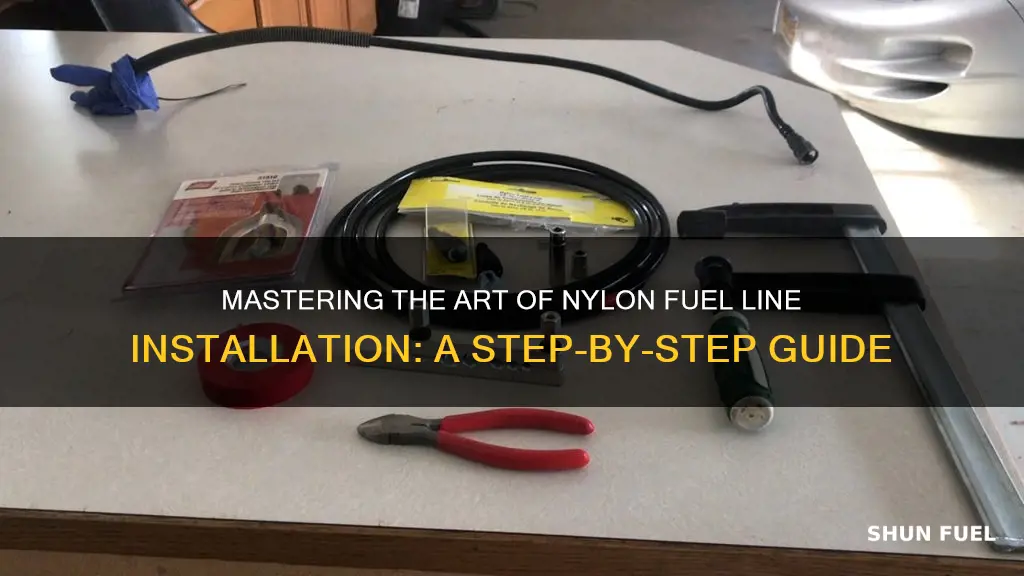
Pressing a nylon fuel line onto a factory fuel line is a common task in vehicle maintenance, especially when upgrading or replacing fuel lines. This process requires careful technique to ensure a secure and leak-free connection. The procedure involves cleaning the factory fuel line, preparing the nylon fuel line by cutting it to the appropriate length, and then using a press tool to force the nylon line onto the factory line. This methodical approach ensures a tight seal, preventing fuel leaks and promoting efficient fuel delivery to the engine.
Characteristics | Values |
---|---|
Material | Nylon |
Compatibility | Factory fuel lines |
Process | Pressing |
Purpose | Connecting fuel lines |
Advantages | Flexibility, durability, resistance to fuel permeation |
Tools Required | Press tool, crimping die |
Steps | 1. Clean the ends of the fuel lines. 2. Measure and cut the nylon fuel line to the appropriate length. 3. Insert the nylon line into the factory line, ensuring a snug fit. 4. Use the press tool to apply pressure and create a secure connection. 5. Repeat for any additional connections. |
Considerations | Ensure a tight fit to prevent fuel leaks. Check local regulations and vehicle specifications for compatibility. |
What You'll Learn
- Prepare Tools: Gather necessary tools like fuel line cutter, solvent cleaner, and crimping pliers
- Clean Lines: Ensure both lines are clean and free of debris using a solvent cleaner
- Measure and Cut: Accurately measure and cut the nylon line to the correct length
- Crimp Connections: Use crimping pliers to secure the nylon line to the factory line
- Test for Leaks: Inspect the connection for leaks and ensure a tight fit
Prepare Tools: Gather necessary tools like fuel line cutter, solvent cleaner, and crimping pliers
Before you begin the process of connecting a nylon fuel line to the factory fuel line, it's crucial to have the right tools ready. This ensures a smooth and efficient installation, minimizing the risk of errors or damage. Here's a breakdown of the essential tools you'll need:
Fuel Line Cutter: This tool is indispensable for precisely cutting the nylon fuel line to the desired length. It allows you to achieve a clean and accurate cut, ensuring a proper fit. Look for a cutter with adjustable settings to accommodate different fuel line diameters.
Solvent Cleaner: Cleaning the fuel lines is vital to ensure a secure connection. A solvent cleaner will help remove any dirt, grease, or contaminants that could interfere with the bonding process. Opt for a cleaner specifically designed for fuel lines to ensure effectiveness.
Crimping Pliers: Crimping pliers are essential for creating a secure and reliable connection between the nylon fuel line and the factory fuel line. These pliers apply pressure to the line, forming a crimp that prevents leaks. Choose a pair with adjustable settings to accommodate different fuel line sizes.
Additionally, consider having a few extra tools on hand for backup:
- Pipe Wrench: A pipe wrench can be useful for tightening connections, especially if you encounter resistance.
- Sandpaper or Emery Cloth: Lightly sanding the ends of the fuel lines can create a rough surface for better adhesion.
- Safety Gear: Safety goggles and gloves are essential to protect your eyes and hands during the installation process.
Having these tools ready will make the installation process much more manageable and increase the likelihood of a successful and long-lasting connection.
Fuel Hose Line Suppliers in Lansing, Michigan: Your One-Stop Shop
You may want to see also
Clean Lines: Ensure both lines are clean and free of debris using a solvent cleaner
To ensure a successful and secure connection when pressing a nylon fuel line onto the factory fuel line, it is crucial to start with a clean and debris-free installation. This step is often overlooked but is essential for a reliable and long-lasting fuel delivery system. Here's a detailed guide on how to achieve clean lines:
Prepare the Materials: Begin by gathering the necessary tools and materials. You will need a solvent cleaner specifically designed for fuel lines, which can be purchased from automotive supply stores. Ensure you have a small spray bottle or a similar container to apply the cleaner. Additionally, have a clean rag or cloth ready for wiping and drying the lines.
Clean the Factory Fuel Line: Start by disconnecting the factory fuel line from the engine or any other component it is currently connected to. Use the solvent cleaner generously on the factory fuel line, ensuring an even coating. Allow the cleaner to sit for a few minutes to effectively dissolve any contaminants. Then, use the rag to wipe the line, removing any debris, old fuel, or grime. Pay attention to the threads and fittings, as these areas may require extra cleaning.
Clean the Nylon Fuel Line: Similarly, prepare the nylon fuel line for installation. If it is a new line, ensure it is free of any manufacturing debris or excess material. For an existing line, disconnect it from its previous connection and clean it thoroughly. Apply the solvent cleaner and let it work its magic, then wipe the line to remove any residue. This step is crucial to ensure a clean and smooth surface for the press-fit connection.
Wipe and Dry: After cleaning both lines, it is essential to wipe them down again to remove any remaining solvent. Use a clean, dry rag to ensure there is no moisture left on the lines. This step helps to prevent any potential issues caused by wet surfaces during the installation process.
By following these steps, you create a clean and prepared environment for pressing the nylon fuel line onto the factory fuel line. This process ensures a tight and secure connection, minimizing the risk of fuel leaks and maximizing the efficiency of your fuel delivery system. Remember, taking the time to clean and prepare the lines is a vital part of any fuel line installation or repair.
Fuel Filter Lines: Understanding the Connections and Their Roles
You may want to see also
Measure and Cut: Accurately measure and cut the nylon line to the correct length
To begin the process of installing a nylon fuel line, it is crucial to measure and cut the nylon line with precision. This step ensures a proper fit and functionality of the new fuel line. Here's a detailed guide on how to measure and cut the nylon line accurately:
Step 1: Measuring the Existing Fuel Line: Start by carefully examining the factory fuel line that you will be replacing. Measure the length of the existing line, ensuring you include any bends or curves. Take note of the overall length required to match the factory setup. Accurate measurement is key to avoiding any unnecessary adjustments or potential issues during installation.
Step 2: Determining the Nylon Line Length: Consider the length of the nylon fuel line you intend to use. This line should be slightly longer than the measured length of the factory fuel line to allow for any necessary adjustments and to ensure a secure connection. Typically, a few inches of extra length is added to accommodate potential variations in the installation process.
Step 3: Marking the Cutting Line: Once you have the measurements, mark the nylon line with a permanent marker or a sharpie. Identify the precise spots where you need to make the cuts. Ensure that the marks are aligned with the bends or curves of the factory fuel line to maintain the correct shape and fit.
Step 4: Cutting the Nylon Line: Utilize a sharp and clean cutting tool, such as a utility knife or a specialized fuel line cutter. Carefully cut along the marked lines, ensuring a straight and clean cut. Take your time with this step to avoid any uneven edges that could affect the installation process.
Step 5: Precision and Fit: Pay close attention to the fit of the nylon line. Ensure that the cut ends match the shape and size of the factory fuel line connectors. Any discrepancies may require further adjustments, so precision is essential at this stage.
By following these steps, you can accurately measure, mark, and cut the nylon fuel line, setting the foundation for a successful installation. Remember, taking the time to measure and cut the line correctly will contribute to a seamless and efficient process when pressing the nylon fuel line onto the factory fuel line.
Motorcycle Carburetor Fuel Line Routing: A Visual Guide
You may want to see also
Crimp Connections: Use crimping pliers to secure the nylon line to the factory line
To ensure a secure and reliable connection when pressing a nylon fuel line onto the factory fuel line, crimping pliers are an essential tool. This method provides a strong and durable bond, ensuring the lines remain tightly coupled without the risk of fuel leaks. Here's a step-by-step guide on how to achieve this:
First, gather the necessary tools and materials. You'll need crimping pliers specifically designed for this task, a nylon fuel line, and the factory fuel line. Ensure the nylon line is the correct size and length to fit the factory line. Clean the ends of both fuel lines to remove any dirt or debris, ensuring a smooth surface for the crimping process.
Next, position the nylon fuel line onto the factory line. Start by inserting the nylon line into the crimping sleeve, ensuring it is centered and aligned with the factory line. The sleeve should be long enough to accommodate the desired crimp length. Use your fingers or a small tool to hold the nylon line in place while you prepare the crimp.
Now, it's time to use the crimping pliers. Place the crimping sleeve over the nylon line and factory line, ensuring it is positioned correctly. Apply pressure to the crimping pliers, squeezing the handles together firmly. The pliers should have a series of indentations or notches along the handle, allowing you to adjust the pressure and create a secure crimp. Aim for a firm, even pressure to ensure a tight connection.
After crimping, inspect the connection. The crimp should be smooth and free of any sharp edges. It should also be flush with the surface of the nylon line and factory line. If the crimp is not secure, repeat the process, applying more pressure to ensure a tight bond.
Remember, practice makes perfect. Crimping may take a few attempts to master, but it is a crucial skill for any fuel line installation or repair. Always ensure you have the right tools and take the time to prepare the lines properly for the best results.
Alcohol Fuel Line Sizing: Expert Guide to Optimal Performance
You may want to see also
Test for Leaks: Inspect the connection for leaks and ensure a tight fit
When working with fuel lines, ensuring a secure and leak-free connection is crucial to prevent any potential issues. Here's a step-by-step guide on how to test for leaks and ensure a tight fit when pressing a nylon fuel line onto the factory fuel line:
Step 1: Prepare the Materials
Before you begin, gather the necessary tools and materials. You'll need the nylon fuel line, the factory fuel line, a fuel line connector or adapter (if required), and a small amount of fuel or a suitable testing liquid. It's essential to have a clean workspace to avoid any contamination.
Step 2: Clean and Prepare the Connections
Start by cleaning the ends of both the nylon and factory fuel lines. Remove any dirt, debris, or old fuel residue to ensure a proper seal. If the factory fuel line has a fitting, ensure it is in good condition and free from damage. You might need to use a fuel line cleaner or a suitable solvent to remove any contaminants.
Step 3: Apply a Lubricant (Optional)
Consider applying a small amount of fuel line lubricant or tape around the nylon fuel line's end. This step can make it easier to insert the line and ensure a tight connection. However, be cautious not to use too much lubricant, as it might interfere with the sealing process.
Step 4: Press the Nylon Fuel Line
Now, carefully press the nylon fuel line onto the factory fuel line. Apply firm pressure and ensure the line is fully inserted. The key is to create a tight seal without forcing the connection, as this might damage the lines. You should feel a secure connection when the line is properly seated.
Step 5: Inspect for Leaks
After pressing the connection, it's crucial to test for leaks. Here's how:
- Visual Inspection: Look for any signs of fuel escaping around the connection. Check for wet spots or fuel residue on the surface.
- Bubble Test: Fill a small container with the testing liquid (fuel or water) and carefully place the factory fuel line's end into the container. If there are no leaks, you should see no bubbles forming around the connection.
- Pressure Test: Using a fuel pressure gauge, apply pressure to the system and monitor for any leaks. This method is more advanced and might require professional tools.
Step 6: Ensure a Tight Fit
If the connection passes the leak test, verify that it is indeed tight. You can do this by gently wiggling the nylon fuel line. It should not move or feel loose. A secure connection will provide a solid feel and ensure that the fuel line is properly sealed.
Remember, taking the time to inspect and test the connection is essential for safety and the longevity of your fuel system. Always follow manufacturer guidelines and best practices when working with fuel lines.
Can Brass Fuel Lines Be Used Safely?
You may want to see also
Frequently asked questions
To achieve a tight and reliable seal, it's crucial to follow a few steps. First, ensure both lines are clean and free of any debris or contaminants. Use a fuel line cleaner or a mild solvent to remove any old fuel residue. Then, apply a thin layer of fuel line tape or a specialized fuel line adhesive around the nylon line, starting about 1 inch from the end. This provides a smooth surface for the factory line to grip onto. Next, insert the factory fuel line into the nylon line, ensuring it is centered. Apply firm pressure with a fuel line press or a pair of pliers to create a tight connection. Finally, wrap the connection with additional fuel line tape or adhesive to reinforce the bond.
A fuel line press is the most effective tool for this task. You can find various sizes and models suitable for different fuel line diameters. If a press is not available, a pair of adjustable pliers can be used, but it may require more force and skill to achieve a secure connection. It's important to use the right tool to avoid damaging the fuel lines or creating an inadequate seal.
Yes, a few pitfalls can compromise the connection. Firstly, avoid applying excessive force, as it may lead to line damage or an uneven connection. Secondly, ensure the lines are properly aligned and centered to prevent kinks or misalignment. Lastly, do not skip the cleaning and preparation steps, as contaminants can interfere with the bonding process. Always take your time and follow the recommended techniques for a successful and long-lasting fuel line connection.