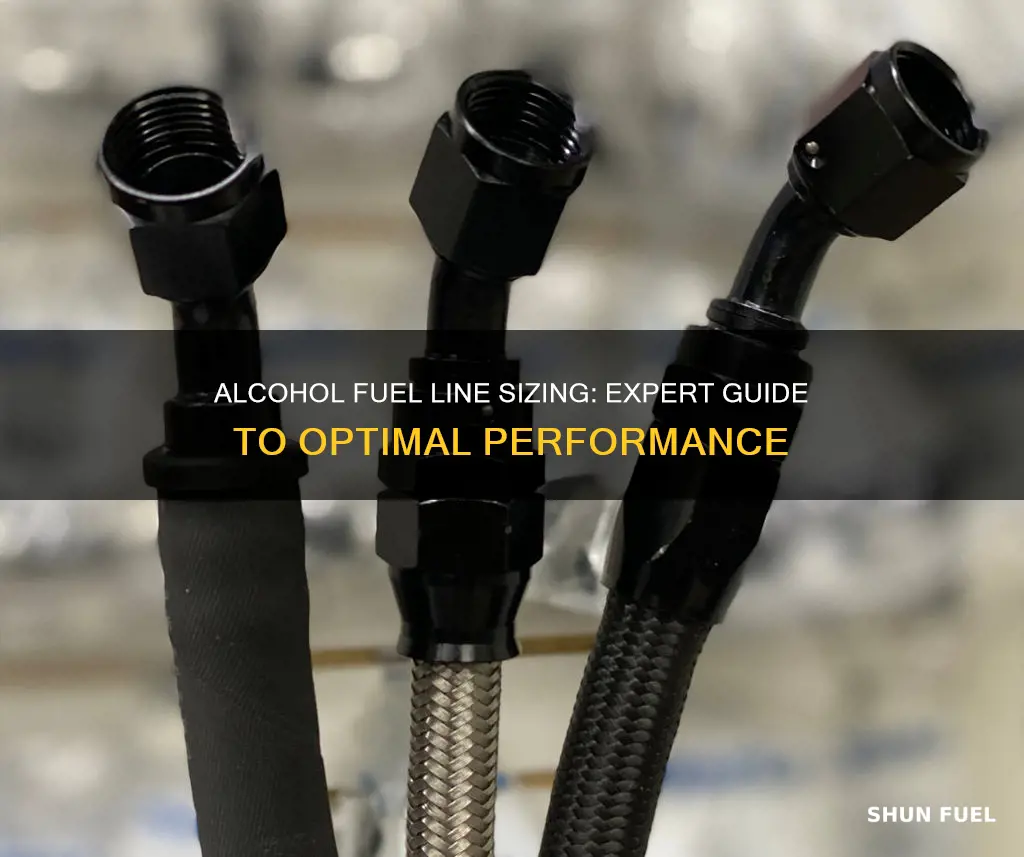
When it comes to modifying a vehicle to run on alcohol fuel, one crucial aspect is selecting the appropriate fuel line size. The size of the fuel line directly impacts the performance and efficiency of the engine. This paragraph will delve into the considerations and guidelines for determining the right fuel line size for alcohol-powered engines, ensuring optimal performance and safety.
Characteristics | Values |
---|---|
Fuel Line Diameter | Typically 3/8" to 1/2" for ethanol fuel systems. |
Material | Stainless steel or aluminum is commonly used for ethanol fuel lines due to their corrosion resistance. |
Length | The length of the fuel line depends on the vehicle's fuel tank location and the engine's fuel inlet. It's crucial to measure or consult the vehicle's manual for accurate sizing. |
Flexibility | Ethanol fuel lines should be flexible to accommodate engine movement and vibrations. |
Pressure Rating | Choose a fuel line with a pressure rating suitable for the fuel system's requirements, often higher than conventional gasoline systems. |
Compatibility | Ensure the fuel line is compatible with ethanol fuel and the vehicle's fuel system components. |
Routing | Properly route the fuel line to avoid sharp bends, kinks, or interference with other components. |
Quality | Opt for high-quality fuel lines from reputable manufacturers to ensure reliability and longevity. |
What You'll Learn
- Fuel Line Material: Choose the right material for alcohol fuel lines, considering durability and compatibility
- Line Diameter: Determine the appropriate diameter based on flow rate and pressure requirements
- Length Considerations: Account for the length of the fuel line and its impact on performance
- Fittings and Connections: Select fittings that are compatible with alcohol fuel and ensure secure connections
- Pressure Rating: Ensure the fuel line has a pressure rating suitable for alcohol fuel systems
Fuel Line Material: Choose the right material for alcohol fuel lines, considering durability and compatibility
When it comes to fuel lines for alcohol-based fuel systems, selecting the appropriate material is crucial for ensuring optimal performance and longevity. Alcohol fuel lines need to withstand the unique challenges posed by the corrosive nature of ethanol and the varying temperatures it can experience. Here's a guide to help you choose the right material:
Durability and Corrosion Resistance: Ethanol, a common alcohol fuel, is highly corrosive to certain materials. It can cause degradation and weakening of the fuel line over time. Therefore, it is essential to choose a material that offers excellent corrosion resistance. Materials like stainless steel, 304 stainless steel in particular, are highly recommended due to their inherent corrosion-resistant properties. This type of steel can withstand the harsh conditions of alcohol fuel, ensuring the longevity of your fuel system.
Flexibility and Temperature Tolerance: Fuel lines need to be flexible to accommodate engine vibrations and movement during operation. Look for materials that provide a good balance between flexibility and strength. Braided stainless steel is an excellent choice as it offers flexibility while also being durable. Additionally, ensure that the material can handle the temperature extremes alcohol fuel systems may encounter, from cold starts to high-temperature operation.
Compatibility with Alcohol Fuel: Some materials may not be compatible with alcohol fuel, leading to potential issues. For instance, certain plastics can become brittle when exposed to ethanol, leading to cracks and leaks. Opt for materials specifically designed for alcohol fuel systems, such as ethanol-resistant rubber compounds or specialized fuel line materials that have been tested and proven to work effectively with alcohol-based fuels.
Consideration of Application: The specific requirements of your fuel system should also be considered. For high-pressure applications, you might need thicker fuel lines with more robust materials. In contrast, for low-pressure systems, a thinner, more flexible material might suffice. Always refer to the manufacturer's guidelines and recommendations for the best material and size options for your particular alcohol fuel setup.
In summary, when selecting fuel line material for alcohol-based fuel systems, prioritize durability, corrosion resistance, and compatibility with ethanol. Materials like 304 stainless steel, braided stainless steel, and ethanol-resistant rubber compounds are excellent choices. By choosing the right material, you can ensure a reliable and efficient fuel system that can handle the unique demands of alcohol fuel.
Understanding Fuel Oil Line Requirements: A Comprehensive Guide
You may want to see also
Line Diameter: Determine the appropriate diameter based on flow rate and pressure requirements
When it comes to choosing the right fuel line for an alcohol-based system, determining the appropriate line diameter is a critical factor. The diameter of the fuel line directly impacts the flow rate and pressure requirements of your setup. Here's a detailed guide on how to determine the suitable line diameter:
Flow Rate Considerations: The flow rate, measured in gallons per minute (GPM) or liters per minute (LPM), is a primary determinant. Higher flow rates typically require larger-diameter lines to ensure efficient and uninterrupted fuel delivery. For instance, if your engine demands a minimum of 5 GPM for optimal performance, you should consider a fuel line with a diameter that can accommodate this flow rate without significant pressure drop. It's essential to consult the manufacturer's specifications for your engine to ensure you meet the required flow rate.
Pressure Drop and Line Diameter: As the flow rate increases, the pressure drop across the fuel line also rises. A pressure drop occurs when the fuel encounters resistance as it travels through the line, leading to a decrease in pressure. To minimize this effect, a larger-diameter line is preferred as it provides a smoother path for fuel flow, reducing the pressure drop. This is particularly crucial in high-performance applications where maintaining optimal pressure is essential for efficient combustion.
Pressure Requirements: Different engines and fuel systems have varying pressure needs. Some systems operate best with higher pressures, while others require lower pressures. When selecting the line diameter, consider the maximum and minimum pressure requirements of your specific setup. For high-pressure systems, a larger diameter will help maintain the necessary pressure throughout the fuel line.
Calculations and Guidelines: Engineers often use empirical data and calculations to determine the optimal line diameter. One common method is the Darcy-Weisbach equation, which considers factors like flow rate, line length, and material properties to predict pressure drop. Additionally, industry guidelines and standards can provide a starting point for selecting the right diameter. These guidelines often suggest specific diameters based on flow rates and pressure ranges, ensuring a well-balanced and efficient fuel system.
In summary, the line diameter is a critical aspect of designing an alcohol-based fuel system. By carefully considering flow rate, pressure drop, and pressure requirements, you can select the appropriate diameter to ensure efficient and reliable fuel delivery. It is always advisable to consult with experts or refer to manufacturer guidelines for precise recommendations tailored to your specific engine and fuel system.
Fram G3727 Inline Fuel Filter: Compatibility and Benefits
You may want to see also
Length Considerations: Account for the length of the fuel line and its impact on performance
When it comes to fuel lines for alcohol-based fuel systems, length is a critical factor that can significantly impact performance and efficiency. The length of the fuel line determines the distance between the fuel source and the engine, and it plays a crucial role in maintaining optimal fuel pressure and flow. Here's a detailed look at how length considerations come into play:
Fuel Line Length and Pressure Drop: Longer fuel lines can lead to increased pressure drop, especially in systems with higher flow rates. As the fuel travels through the line, it encounters resistance, which can cause a decrease in pressure. This pressure drop can result in reduced fuel atomization and potentially lead to poor engine performance. To mitigate this issue, it is essential to use fuel lines with appropriate diameters and materials that minimize internal friction.
Flow Rate and Line Diameter: The length of the fuel line is directly related to the flow rate of the fuel. Longer lines may require larger-diameter fuel lines to maintain sufficient flow. This is because longer paths can lead to increased resistance, and a larger diameter helps to reduce the pressure drop. It's important to strike a balance between line length and diameter to ensure optimal fuel delivery without causing unnecessary restrictions.
Engine Performance and Efficiency: The impact of fuel line length on engine performance is significant. Longer lines can introduce delays in fuel delivery, affecting the engine's ability to respond quickly to throttle inputs. This delay may result in reduced power output and less responsive acceleration. Additionally, longer lines can lead to increased heat absorption from the engine, which can impact fuel volatility and potentially cause performance issues.
Installation and Routing: Proper installation and routing of the fuel line are essential to minimize the impact of length. The line should be routed away from hot surfaces and sharp bends to prevent damage and maintain optimal flow. Consider the engine's layout and available space to ensure the fuel line is installed efficiently, reducing unnecessary length and potential restrictions.
In summary, when designing or modifying an alcohol-powered fuel system, it is crucial to carefully consider the length of the fuel line. Longer lines may require careful selection of line materials and diameters to maintain adequate pressure and flow. Proper installation and routing are also key to ensuring optimal engine performance and efficiency. By addressing these length considerations, you can create a reliable and high-performing fuel system for your alcohol-powered vehicle.
Choosing the Right Fuel Line for Your 128LD Trimmer
You may want to see also
Fittings and Connections: Select fittings that are compatible with alcohol fuel and ensure secure connections
When dealing with alcohol fuel systems, it's crucial to pay close attention to the fittings and connections to ensure optimal performance and safety. The choice of fittings is a critical aspect that can significantly impact the efficiency and reliability of your fuel system. Here's a detailed guide on selecting the right fittings and ensuring secure connections:
Compatibility with Alcohol Fuel: Alcohol-based fuels, such as ethanol or methanol, have unique properties that require specific materials and designs in fittings. Look for fittings made from materials that are resistant to corrosion and degradation caused by these fuels. Common materials include stainless steel, brass, and certain types of plastics. Avoid fittings made from aluminum or other materials that may react with alcohol, leading to potential leaks or performance issues.
Thread and Connection Types: Consider the thread types and connection methods commonly used in alcohol fuel systems. The most prevalent threads are 3/8-24 UNF (Unified National Fine) and 1/4-20 UNF. These threads are widely accepted in the industry and provide a secure fit. Additionally, look for fittings with female threads on the inlet side and male threads on the outlet side to ensure proper orientation. Common connection types include quick-connect fittings, barbed fittings, and compression fittings, each with its own advantages and use cases.
Secure Connections: Ensuring a tight and secure connection is vital to prevent fuel leaks and maintain system integrity. When installing fittings, use the appropriate torque to ensure a firm bond. Over-tightening can damage the fittings, while under-tightening may lead to leaks. Consider using thread seal tape or pipe compound on the threads to provide an additional layer of protection against leaks. For quick-connect fittings, ensure that the O-rings or seals are in good condition and properly seated to create an effective seal.
Pressure Rating and Flow Capacity: Alcohol fuel systems can operate under varying pressure and flow rates, so it's essential to select fittings with appropriate pressure ratings and flow capacities. Check the specifications of the fittings to ensure they can handle the expected pressure and volume of your fuel system. This is particularly important when dealing with high-pressure fuel lines or systems with high flow rates.
Testing and Inspection: After installation, it's crucial to test the fittings and connections thoroughly. Perform visual inspections to check for any signs of damage, cracks, or deformations. Use pressure testing methods to ensure the integrity of the connections. This step is essential to identify and address any potential issues before they cause problems during operation.
By carefully selecting fittings that are compatible with alcohol fuel and ensuring secure connections, you can build a reliable and efficient fuel system. Remember, the right materials, thread types, and connection methods will contribute to the overall performance and longevity of your alcohol-powered vehicle or equipment.
Evap Line's Role in Fuel Filter Maintenance
You may want to see also
Pressure Rating: Ensure the fuel line has a pressure rating suitable for alcohol fuel systems
When it comes to alcohol fuel systems, one crucial aspect often overlooked is the pressure rating of the fuel line. This is a critical component in ensuring the safe and efficient operation of your vehicle's engine. The pressure rating of a fuel line determines its ability to withstand the forces exerted by the fuel as it flows through the system. In the case of alcohol-based fuels, these can be highly volatile and may require specific considerations.
Alcohol fuel systems typically operate under higher pressure compared to conventional gasoline or diesel engines. This is because alcohol, such as ethanol, has a lower energy density and requires more pressure to maintain a steady flow into the engine. Therefore, the fuel line must be designed to handle this increased pressure to prevent leaks, explosions, or other hazardous situations.
The pressure rating of a fuel line is usually indicated in pounds per square inch (psi) or bars. For alcohol fuel systems, it is essential to choose a fuel line with a pressure rating that exceeds the expected operating pressure. This safety margin ensures that the fuel line can handle any potential fluctuations or increases in pressure, providing a reliable and secure connection.
When selecting a fuel line, it is recommended to consult the manufacturer's guidelines or specifications for your vehicle's alcohol fuel system. These guidelines will provide the exact pressure rating required for your engine. Using a fuel line with an inadequate pressure rating can lead to serious consequences, including engine damage, loss of power, and potential safety hazards.
In summary, when dealing with alcohol fuel systems, paying attention to the pressure rating of the fuel line is vital. It ensures the system's integrity, prevents potential failures, and guarantees the safe operation of your vehicle. Always prioritize safety and consult the appropriate resources to choose the right fuel line for your alcohol-powered engine.
Fuel Line Fabrication: Cost Breakdown for Custom Solutions
You may want to see also
Frequently asked questions
The size of the fuel line depends on various factors, including the engine's power output, the alcohol concentration, and the desired flow rate. Generally, a 3/8-inch fuel line is a common choice for most automotive applications, but for high-performance engines or systems with a higher alcohol content, a 1/2-inch line might be necessary to handle the increased pressure and volume.
To find the right fuel line size, consider the engine's displacement and power output. Larger engines with higher performance may require a larger diameter to accommodate the increased fuel flow. You can also refer to the manufacturer's specifications or consult a fuel system expert to ensure you choose the correct size for your specific setup.
While using a smaller fuel line might reduce some weight, it is not recommended as it can lead to performance issues. A smaller line may restrict fuel flow, causing potential engine misfires, reduced power, and poor fuel efficiency. Always prioritize performance and safety by using the appropriate size fuel line for your alcohol-powered engine.
Using an incorrect fuel line size can result in various symptoms, such as poor engine performance, reduced power, and fuel leaks. You may also notice engine misfires, rough idling, or a decrease in fuel efficiency. If you suspect an issue, it's best to inspect the fuel line and consult a professional to ensure you have the right size for your alcohol fuel system.