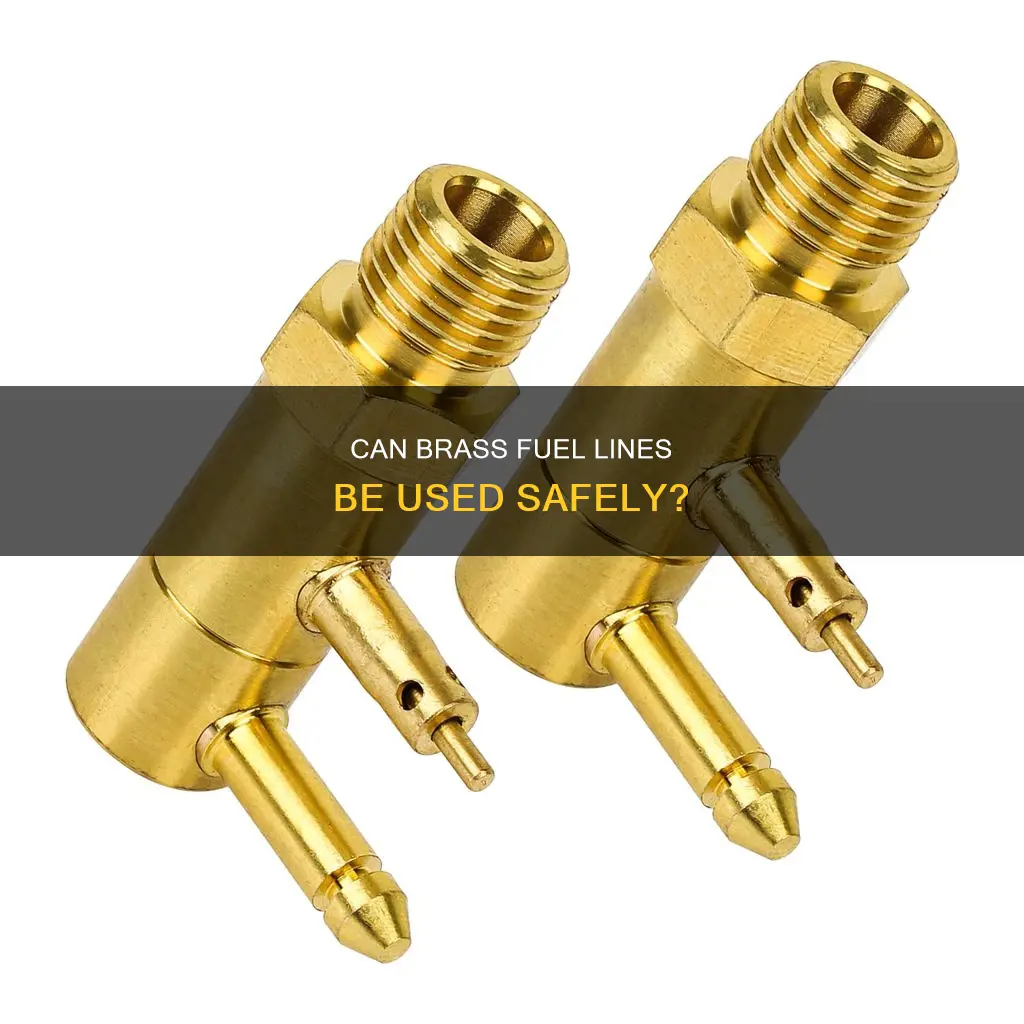
Brass is a versatile metal commonly used in various applications, including plumbing and automotive parts. When it comes to fuel lines, the question arises: Can brass be used effectively in this context? This paragraph will explore the suitability of brass for fuel lines, considering its properties and the specific requirements of fuel systems. By examining its advantages and potential challenges, we can determine whether brass is a viable option for this critical component of a vehicle's fuel delivery system.
Characteristics | Values |
---|---|
Corrosion Resistance | Brass is highly resistant to corrosion, especially in fuel line applications where exposure to gasoline, diesel, and other fuels is common. |
Strength and Durability | It offers good mechanical properties, including strength and durability, making it suitable for withstanding the pressures and temperatures encountered in fuel systems. |
Flexibility | Brass can be more flexible than steel, allowing for easier installation and the ability to accommodate slight movements in the fuel lines. |
Cost | Generally, brass is more affordable than other materials like copper or stainless steel, making it a cost-effective choice for fuel lines. |
Availability | Brass is widely available and can be easily sourced for fuel line manufacturing. |
Weldability | It can be welded, providing a reliable method of joining fuel lines and components. |
Compatibility | Brass is compatible with various fuels, including gasoline, diesel, and aviation fuels, making it a versatile material for fuel systems. |
Ease of Maintenance | Its corrosion resistance and durability contribute to easy maintenance and long-term reliability. |
Visual Inspection | Brass fuel lines can be visually inspected for any signs of damage or wear, ensuring prompt detection of potential issues. |
Regulatory Compliance | Many fuel systems require materials that meet specific standards, and brass often complies with these regulations. |
What You'll Learn
- Material Compatibility: Brass can be used with fuel lines if it's compatible with the fuel type
- Temperature Resistance: Brass withstands temperature changes, making it suitable for fuel lines
- Corrosion Resistance: Brass resists corrosion, ensuring long-lasting performance in fuel line applications
- Flexibility: Brass's flexibility allows it to bend and move with fuel line vibrations
- Cost-Effectiveness: Brass is a cost-effective alternative to other materials for fuel lines
Material Compatibility: Brass can be used with fuel lines if it's compatible with the fuel type
When considering the use of brass in fuel lines, it is crucial to understand the material's compatibility with the specific fuel type. Brass, an alloy of copper and zinc, offers several advantages for fuel line applications. Firstly, it is known for its excellent corrosion resistance, which is vital when dealing with fuels that can be corrosive over time. This property ensures that the brass fuel lines remain intact and functional, even when exposed to various fuel types.
The compatibility of brass with fuel lines is highly dependent on the type of fuel being used. For instance, brass is generally suitable for gasoline and diesel applications due to its ability to withstand the chemical properties of these fuels. However, it is essential to note that brass may not be the best choice for fuels with higher alcohol content, such as ethanol blends. In such cases, alternative materials like stainless steel or specific brass alloys designed for ethanol resistance might be more appropriate.
In the context of fuel lines, the compatibility of brass is often assessed through its ability to resist fuel-related degradation. This includes maintaining its structural integrity, preventing fuel leaks, and ensuring long-term performance. Brass's inherent properties, such as its strength and ductility, make it a reliable material for fuel lines, especially when properly selected and installed.
To ensure compatibility, it is recommended to consult manufacturer guidelines or seek expert advice. Different brass alloys may exhibit varying levels of compatibility, and selecting the right alloy for the specific fuel type is crucial. For instance, some brass alloys might be more resistant to fuel-related degradation, making them more suitable for long-term use.
In summary, brass can be effectively utilized for fuel lines when its compatibility with the fuel type is considered. Its corrosion resistance and structural properties make it a viable option for many fuel applications. However, understanding the specific fuel's characteristics and selecting the appropriate brass alloy is essential to ensure optimal performance and longevity of the fuel lines.
Unclogging the Fuel Flow: A Guide to Removing Tight Fuel Lines
You may want to see also
Temperature Resistance: Brass withstands temperature changes, making it suitable for fuel lines
Brass, an alloy of copper and zinc, is an excellent choice for fuel lines due to its remarkable temperature resistance. This property is crucial in the automotive and industrial sectors, where fuel lines are exposed to varying temperatures, especially in engines and fuel systems. The ability of brass to withstand these temperature changes is a result of its unique material characteristics.
One of the key advantages of brass is its high thermal conductivity. This means it can efficiently transfer heat, which is beneficial in fuel lines as it helps regulate the temperature of the fuel. In fuel systems, maintaining the fuel at an optimal temperature is essential for efficient combustion and engine performance. Brass ensures that the fuel remains at a stable temperature, preventing overheating or cooling down to a point that could affect engine operation.
Additionally, brass has a relatively low coefficient of thermal expansion. This characteristic allows brass fuel lines to maintain their shape and integrity even when subjected to rapid temperature fluctuations. Unlike some other materials, brass does not expand or contract significantly with temperature changes, ensuring a consistent and reliable connection between the fuel source and the engine. This is particularly important in high-performance applications where temperature variations are more pronounced.
The temperature resistance of brass is further enhanced by its ability to resist corrosion and oxidation. Fuel lines are often exposed to fuel, which can be corrosive over time. Brass, with its copper and zinc composition, forms a protective oxide layer on its surface, preventing corrosion and ensuring the longevity of the fuel lines. This resistance to corrosion is vital for maintaining the integrity of the fuel system and preventing potential leaks or performance issues.
In summary, brass is an ideal material for fuel lines due to its temperature resistance. Its thermal conductivity, low coefficient of expansion, and corrosion resistance make it a reliable and durable choice for automotive and industrial fuel systems. By utilizing brass, engineers and manufacturers can ensure that fuel lines can withstand the challenges posed by temperature variations, providing efficient and safe fuel delivery to engines.
Mastering Dorman Steel Fuel Lines: A Guide to Secure Connections
You may want to see also
Corrosion Resistance: Brass resists corrosion, ensuring long-lasting performance in fuel line applications
Brass, an alloy of copper and zinc, is an excellent choice for fuel line applications due to its remarkable corrosion resistance. This property is crucial in the automotive and marine industries, where fuel lines are exposed to harsh environments and various corrosive elements.
The resistance of brass to corrosion is primarily attributed to its composition. Copper, a primary component of brass, forms a protective oxide layer on its surface when exposed to air. This natural layer acts as a barrier, preventing further oxidation and corrosion. The zinc in brass also contributes to its corrosion-resistant nature by forming a protective zinc oxide layer, which further enhances the material's ability to withstand corrosive attacks.
In fuel line systems, where fuel is often a mixture of gasoline, diesel, or other hydrocarbons, the presence of corrosive substances like water, acids, and alkalis is common. Brass's inherent resistance to these corrosive agents ensures that the fuel lines remain intact and functional over extended periods. This is particularly important in high-temperature environments, as the corrosive effects can be exacerbated by heat, leading to rapid deterioration of other materials.
The long-lasting performance of brass fuel lines is a significant advantage. It reduces the need for frequent replacements, saving time and resources. Additionally, the use of brass can prevent fuel contamination, which could occur if other materials corrode and release particles into the fuel. This contamination can lead to engine performance issues and potential damage to the fuel system.
Furthermore, the ease of maintenance and repair is another benefit. Brass fuel lines can be readily replaced or repaired without the need for specialized tools or extensive knowledge, making it a practical and cost-effective solution for fuel line applications. Its durability and resistance to corrosion make brass an ideal material for ensuring the longevity and reliability of fuel systems in various industries.
Understanding Truck Fuel Lines: A Comprehensive Guide to Different Types
You may want to see also
Flexibility: Brass's flexibility allows it to bend and move with fuel line vibrations
The flexibility of brass is a key advantage when it comes to using it for fuel lines. Fuel lines are subject to constant vibrations and movement as the engine operates, and the ability of brass to bend and adapt to these motions is crucial for a reliable and long-lasting installation. This flexibility is particularly important in high-performance engines or vehicles with modified setups, where the fuel lines may need to navigate around various components and experience significant stress.
Brass, being a metal with a relatively low hardness, can easily accommodate the repetitive flexing and twisting that occurs during engine operation. Unlike stiffer materials, brass does not become rigid or brittle over time, ensuring that the fuel lines remain pliable and capable of withstanding the dynamic nature of the fuel system. This flexibility is essential to prevent cracks, leaks, or damage to the fuel lines, which could lead to costly repairs or even dangerous situations.
In addition to its ability to absorb vibrations, brass's flexibility also contributes to the overall durability of the fuel line assembly. By allowing the lines to move freely, brass helps to reduce the risk of damage from sharp bends or kinks, which can occur if the lines were made from less flexible materials. This is especially beneficial in areas where the fuel lines may come into contact with other engine components or suspension elements that could cause localized stress.
Furthermore, the flexibility of brass can simplify the installation process. Fuel lines made from this material can be easily bent and manipulated to fit the unique contours of a vehicle's engine bay, making the job more efficient and less prone to errors. This is particularly useful when working with limited access areas or when retrofitting older vehicles with modern fuel systems.
In summary, the flexibility of brass is a critical factor in its suitability for fuel lines. It enables the material to withstand the constant vibrations and movements of the engine, ensuring the longevity and reliability of the fuel system. Additionally, this flexibility enhances the overall durability and installation ease, making brass an excellent choice for fuel line applications.
Brake Line vs. Fuel Line: Understanding the Differences
You may want to see also
Cost-Effectiveness: Brass is a cost-effective alternative to other materials for fuel lines
Brass, an alloy of copper and zinc, offers a cost-effective solution for fuel lines in various applications. Its affordability is a significant advantage, especially for projects with tight budgets. When compared to other materials like steel or aluminum, brass provides a more economical option without compromising on performance. This is particularly beneficial for automotive and marine industries, where fuel lines are essential but often require a balance between functionality and financial constraints.
The cost-effectiveness of brass is attributed to its ease of manufacturing and the availability of its raw materials. Copper, a primary component of brass, is relatively abundant and affordable, allowing for cost-efficient production. Additionally, the process of casting and forming brass into fuel line shapes is less complex and energy-intensive compared to other materials, further reducing manufacturing costs. This makes brass an attractive choice for fuel line manufacturers and users who aim to optimize their budgets without sacrificing quality.
Furthermore, the durability of brass contributes to its cost-effectiveness over time. Brass fuel lines are known for their resistance to corrosion and fatigue, ensuring a longer lifespan. This durability means that while the initial cost of brass fuel lines might be slightly lower, the long-term savings are substantial. Reduced maintenance and replacement frequencies result in significant cost savings, making brass an economically sound choice for fuel line applications.
In the automotive sector, where fuel lines are subject to varying temperatures and environmental conditions, brass's cost-effectiveness becomes even more valuable. Its ability to withstand corrosion and maintain structural integrity over a wide temperature range ensures that fuel lines remain reliable and efficient. This reliability translates to fewer replacements and repairs, further enhancing the economic benefits of using brass in fuel line systems.
In summary, brass's cost-effectiveness is a compelling reason for its widespread use in fuel lines. Its affordability, ease of manufacturing, and durability make it an attractive alternative to more expensive materials. By providing a balance between performance and price, brass ensures that fuel line systems can be implemented without compromising on quality or long-term cost efficiency. This makes it an ideal choice for various industries, especially those with budget constraints, while still meeting the demanding requirements of fuel line applications.
Nylon Fuel Line: Top Sources for Purchase
You may want to see also
Frequently asked questions
Yes, brass can be used for fuel lines, but it's important to choose the right type. For fuel applications, you should opt for a specific brass alloy like 6262 or 6264, which are commonly used in the automotive industry for fuel systems. These alloys offer good corrosion resistance and can withstand the harsh conditions of fuel.
Brass has several benefits for fuel line applications. Firstly, it is lightweight and easy to work with, making installation and maintenance simpler. Secondly, brass has natural corrosion resistance, which helps prevent fuel leaks and ensures the longevity of the fuel system. Additionally, brass is known for its durability and ability to withstand temperature changes, making it suitable for various weather conditions.
While brass is a reliable choice, it may not be as flexible as some other materials like rubber or plastic. This can make installation in tight spaces more challenging. Additionally, brass can be more expensive than other materials, and over time, it may develop a slight odor due to the presence of zinc. However, these drawbacks are often outweighed by its performance and durability.
Compatibility is crucial to prevent fuel contamination and potential engine damage. Different fuels have varying properties, and some may react with certain metals. It's essential to check the fuel specifications and consult the vehicle's manual or manufacturer guidelines. Using a fuel line made of a compatible material, such as brass with a protective coating, can ensure safe and efficient fuel delivery.