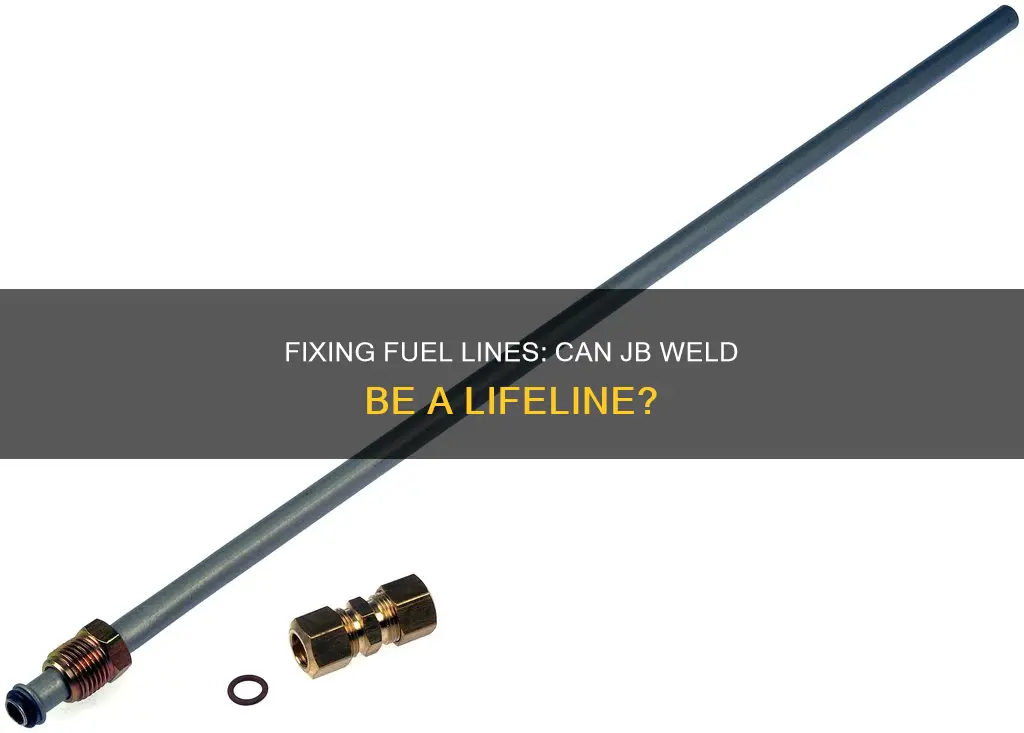
Can you JB Weld a fuel line? This question might seem odd, but it's a common dilemma for car enthusiasts and DIYers. JB Weld, a brand known for its epoxy-based adhesives and sealants, is often used for quick fixes and temporary repairs. However, when it comes to fuel lines, which are crucial for the engine's performance and safety, the answer is not as straightforward. While JB Weld can be used in a pinch to seal small leaks or cracks, it's not the best solution for a fuel line. Fuel lines require a high-temperature, fuel-resistant material to ensure they can withstand the engine's heat and the corrosive nature of fuel. For a more permanent and reliable fix, it's recommended to consult a professional mechanic or use specialized fuel line repair kits.
Characteristics | Values |
---|---|
Material Compatibility | JB Weld is generally not recommended for fuel lines due to its potential incompatibility with fuel. It may not adhere well to the fuel-resistant materials commonly used in fuel lines. |
Strength and Durability | While JB Weld can provide a strong bond, it may not be as durable as specialized fuel line repair kits. Fuel lines require materials that can withstand high pressure and temperature changes. |
Flexibility | JB Weld is a semi-permanent repair solution and may not offer the flexibility needed for fuel lines, which can expand and contract with temperature changes. |
Longevity | The longevity of the repair depends on the quality of the application and the specific fuel line material. It might not last as long as a professional repair. |
Regulations and Safety | Using JB Weld for fuel lines might not comply with vehicle manufacturer guidelines and could potentially void warranties. Safety standards for fuel systems are stringent, and non-approved repairs may pose risks. |
Alternative Methods | Consider using specialized fuel line repair kits or consulting a professional mechanic for a more reliable and safe solution. |
What You'll Learn
- JB Weld Application: How to use JB Weld for fuel line repairs
- Safety Precautions: Essential safety measures when working with JB Weld
- Fuel Line Material: Best JB Weld types for various fuel line materials
- Curing Time: Optimal curing time for JB Weld on fuel lines
- Post-Weld Inspection: Methods to inspect and test JB Welded fuel lines
JB Weld Application: How to use JB Weld for fuel line repairs
JB Weld, a brand of epoxy-based adhesive, can be a useful tool for repairing fuel lines in vehicles, especially in emergency situations or when specialized tools are not available. However, it's important to note that JB Weld is not a replacement for professional repairs and should be used with caution, as improper application can lead to further issues. Here's a step-by-step guide on how to use JB Weld for fuel line repairs:
Preparation: Before attempting any repair, ensure you have the necessary tools and materials, including JB Weld epoxy, a heat gun or hairdryer, a clean cloth, and a small brush (optional). It is crucial to clean the fuel line and the area where the repair will be made. Use the cloth to wipe away any dirt, grease, or debris. If the fuel line is damaged, cut it a few inches away from the break to create a clean, straight edge.
Application of JB Weld: Once the area is prepared, it's time to apply the JB Weld. Start by mixing the epoxy according to the manufacturer's instructions. Typically, you'll need to combine two separate components, often referred to as Part A and Part B. Mix them thoroughly until they form a consistent, smooth paste. Take a small amount of the mixed epoxy and apply it to the fuel line, ensuring it covers the damaged area and any surrounding areas that need reinforcement. Be generous with the application, but avoid overloading the area, as it may cause the epoxy to ooze and create a mess.
Setting Time: After applying the JB Weld, you'll need to wait for it to set. The setting time can vary depending on the temperature and humidity, but it typically takes around 24-48 hours to reach full strength. During this time, avoid any pressure or stress on the repaired area. You can use a temporary fix, such as a rubber band or a piece of hose, to hold the fuel line in place while the epoxy sets.
Testing and Reinforcement: Once the JB Weld has set, test the fuel line by applying pressure and checking for leaks. If the repair is successful, you can further reinforce it by wrapping the repaired section with a piece of cloth or tape. This additional layer of protection can help prevent future damage. However, remember that JB Weld is not a permanent solution, and it is recommended to have the fuel line professionally repaired as soon as possible.
Important Considerations: While JB Weld can be a temporary solution, it is not ideal for long-term fuel line repairs. The epoxy may not provide the same level of flexibility and durability as the original fuel line material. Therefore, it is crucial to seek professional assistance for a more permanent fix. Additionally, always wear protective gear, such as gloves and goggles, when handling JB Weld to avoid skin and eye irritation.
Fuel Line Removal: A Guide for 87 Crown Victoria Owners
You may want to see also
Safety Precautions: Essential safety measures when working with JB Weld
Before you begin any work with JB Weld, it's crucial to prioritize safety. JB Weld is a two-part epoxy system that can be used for various applications, including repairing fuel lines. However, due to the potential hazards associated with fuel systems, it's essential to take the following safety precautions:
Ventilation: Ensure you are working in a well-ventilated area or outdoors to avoid inhaling fumes. JB Weld can release volatile organic compounds (VOCs) during application, which can be harmful if inhaled. Proper ventilation helps to disperse these fumes and reduce the risk of respiratory issues.
Protective Gear: Always wear appropriate personal protective equipment (PPE). This includes gloves to protect your hands from the epoxy and any potential spills or splashes. Safety goggles are essential to shield your eyes from any debris or splatters, as the epoxy can cure rapidly and create a mess. Consider wearing a respirator mask to minimize the inhalation of fumes, especially in enclosed spaces.
Fuel Line Isolation: When working with fuel lines, it's critical to isolate the section you intend to repair. Turn off the fuel supply to the affected area and ensure it is completely shut off before proceeding. This step is vital to prevent accidental fuel leaks, which can be extremely dangerous. Allow sufficient time for the fuel to dissipate from the line before starting the repair.
Fire Safety: JB Weld and its curing process can generate heat, and fuel lines are flammable. Keep a fire extinguisher nearby and ensure you have a clear understanding of how to use it. Avoid open flames or heat sources while working with the epoxy, as it can cause the fuel to ignite.
Follow Instructions: Adhere to the manufacturer's instructions provided with the JB Weld product. These guidelines will include specific details on mixing, application, and curing times. Following the instructions ensures you use the product safely and effectively, minimizing the risk of errors or accidents.
Remember, working with JB Weld for fuel line repairs requires caution and attention to detail. By implementing these safety measures, you can minimize potential hazards and ensure a successful and safe repair process.
Understanding the Role of Fuel Line Pumps in Vehicles
You may want to see also
Fuel Line Material: Best JB Weld types for various fuel line materials
When it comes to repairing fuel lines, JB Weld is a popular choice due to its versatility and ease of use. However, the choice of JB Weld product depends on the material of the fuel line. Here's a breakdown of the best JB Weld types for various fuel line materials:
Rubber Fuel Lines:
- Best Option: JB Weld Plastic Welder. This product is specifically designed for bonding plastics and rubbers, making it ideal for fuel lines. It creates a strong, flexible bond that can withstand fuel pressure and temperature fluctuations.
- Application: Clean the fuel line thoroughly and ensure both surfaces are dry. Apply a thin layer of JB Weld Plastic Welder to the joint, following the manufacturer's instructions. Allow it to cure according to the recommended time.
Vinyl Fuel Lines:
- Best Option: JB Weld Plastic Welder or JB Weld Medium-Strength Epoxy. Both products offer good bonding strength for vinyl.
- Application: Similar to rubber lines, clean and dry the surfaces. Apply the chosen JB Weld product, following the instructions.
Metal Fuel Lines (Commonly Aluminum or Steel):
- Best Option: JB Weld Medium-Strength Epoxy. This epoxy provides excellent bonding strength to metal surfaces.
- Application: Ensure the metal surfaces are clean, dry, and free of any corrosion. Apply a generous amount of JB Weld Medium-Strength Epoxy to both surfaces, following the manufacturer's guidelines for mixing and application.
Important Considerations:
- Fuel Line Material Compatibility: Always check the manufacturer's recommendations for your specific fuel line material. Some materials may require specialized JB Weld products.
- Surface Preparation: Proper surface preparation is crucial for a successful bond. Remove any dirt, grease, or old adhesive residue.
- Curing Time: Allow sufficient curing time for the chosen JB Weld product. Follow the instructions carefully to ensure a strong and durable bond.
- Safety: When working with fuel lines, prioritize safety. Wear protective gear, ensure proper ventilation, and follow all safety precautions provided by the product manufacturer.
Remember, JB Weld is a temporary repair solution. For long-term reliability, consider professional fuel line replacement or consult a mechanic for expert advice.
Crafting Your Own Fuel Line: A Step-by-Step Guide
You may want to see also
Curing Time: Optimal curing time for JB Weld on fuel lines
When it comes to repairing fuel lines with JB Weld, understanding the optimal curing time is crucial for a successful and safe repair. JB Weld, a two-part epoxy system, is known for its strong bonding capabilities and is often used in automotive applications, including fuel line repairs. However, the curing process requires careful attention to ensure the material sets properly and provides long-lasting results.
The curing time for JB Weld on fuel lines can vary depending on several factors. Firstly, the specific product you are using matters; different JB Weld formulas may have slightly different curing times. It's essential to consult the manufacturer's instructions for the particular epoxy you have. Typically, JB Weld's standard epoxy systems require a curing time of around 24 to 48 hours. This duration allows the epoxy to reach its maximum strength and bond securely to the fuel line.
During this curing period, it is imperative to avoid any stress or load on the repaired area. Fuel lines are under constant pressure and movement, so ensuring the weld is fully cured before reinstalling the line is vital. Applying excessive force or pressure too soon can compromise the bond and potentially lead to failure.
To optimize the curing process, consider the following tips. Firstly, ensure the fuel line is clean and free of any contaminants before applying the epoxy. Remove any old adhesive, grease, or debris to create a clean surface for the weld. Secondly, mix the two-part epoxy according to the instructions, as improper mixing can affect the curing time and quality. Finally, apply the epoxy in a thin, even layer, ensuring complete coverage of the fuel line section to be repaired.
After the initial curing time, it is recommended to test the bond by gently flexing the fuel line. If the repair holds up without any issues, you can proceed with reinstalling the line. However, if any problems arise, such as leaks or weak spots, additional time may be required for further curing or reinforcement. Remember, patience is key when working with JB Weld to ensure a robust and long-lasting fuel line repair.
Unrusting the Fuel Line: A Step-by-Step Guide to Removing Corroded Fittings
You may want to see also
Post-Weld Inspection: Methods to inspect and test JB Welded fuel lines
When it comes to JB Welding fuel lines, post-weld inspection is crucial to ensure the integrity and safety of the system. Here are some methods to thoroughly inspect and test the welded connections:
Visual Inspection: Begin with a thorough visual examination of the welded area. Check for any visible defects such as cracks, voids, or uneven weld beads. Look for signs of contamination or debris that might have affected the weld quality. Ensure that the weld is free from any visible defects and that the fuel line is securely attached to the component without any gaps or misalignments.
Dimensional Analysis: Measure the welded fuel line connection to ensure it meets the required specifications. Use precision tools like calipers and micrometers to verify the dimensions of the weld and the surrounding area. Check for any deviations from the expected thickness, diameter, or length. This step is critical to ensure the structural integrity of the connection and to identify any potential issues that might affect the performance of the fuel line.
Leak Testing: After the visual and dimensional inspections, perform a leak test to identify any potential issues. Fill the fuel line with a suitable pressure-sensitive liquid or use a specialized fuel line testing kit. Apply pressure to the system and observe for any leaks around the welded connection. This test is essential to detect any cracks or imperfections that might allow fuel to escape, which could lead to dangerous situations.
Ultrasonic Testing: For a more comprehensive inspection, consider using ultrasonic testing. This non-destructive testing method employs high-frequency sound waves to detect internal flaws in the weld. By placing the ultrasonic probe on the welded area, you can identify any voids, inclusions, or defects within the weld bead and its surrounding region. Ultrasonic testing provides a detailed analysis of the weld's quality and can help ensure that the connection is sound and free from internal defects.
Pressure Testing: Subject the welded fuel line to a pressure test to simulate real-world conditions. Apply pressure gradually and monitor the system for any signs of leakage or failure. This test helps identify any weaknesses in the weld or fuel line that might not be apparent during visual inspection. It is a critical step to ensure the system's reliability and safety.
By following these post-weld inspection methods, you can ensure that the JB-welded fuel lines are secure, leak-free, and structurally sound. Each step contributes to a comprehensive evaluation, providing confidence in the quality and safety of the fuel system.
Optimizing Fuel Delivery: Choosing the Right Line Size for Your Subaru
You may want to see also
Frequently asked questions
While JB Weld is a versatile epoxy-based adhesive and sealant, it is not recommended for fuel line repairs. Fuel lines require a specific type of material that can withstand the corrosive nature of gasoline and other fuels. JB Weld may not provide the necessary durability and could potentially lead to fuel leaks or other issues.
Using JB Weld on a fuel line can pose several risks. Firstly, the adhesive may not create a strong bond with the fuel line material, leading to potential failure over time. Secondly, the epoxy can be sensitive to fuel, and prolonged exposure might cause it to degrade, resulting in cracks or leaks. It is crucial to use products designed for fuel line repairs to ensure safety and reliability.
Yes, there are specialized products available for fuel line repairs. These include fuel line repair kits, which often include a primer, adhesive, and a heat-shrink sleeve. These kits are designed to create a secure and long-lasting repair. It is always best to consult with professionals or refer to manufacturer guidelines for suitable repair methods.
JB Weld is not intended for temporary fixes. While it can provide some immediate adhesion, it may not be strong enough to withstand the pressure and movement associated with fuel lines. A temporary solution might be better, and it is advisable to seek a more permanent repair method as soon as possible to avoid further complications.