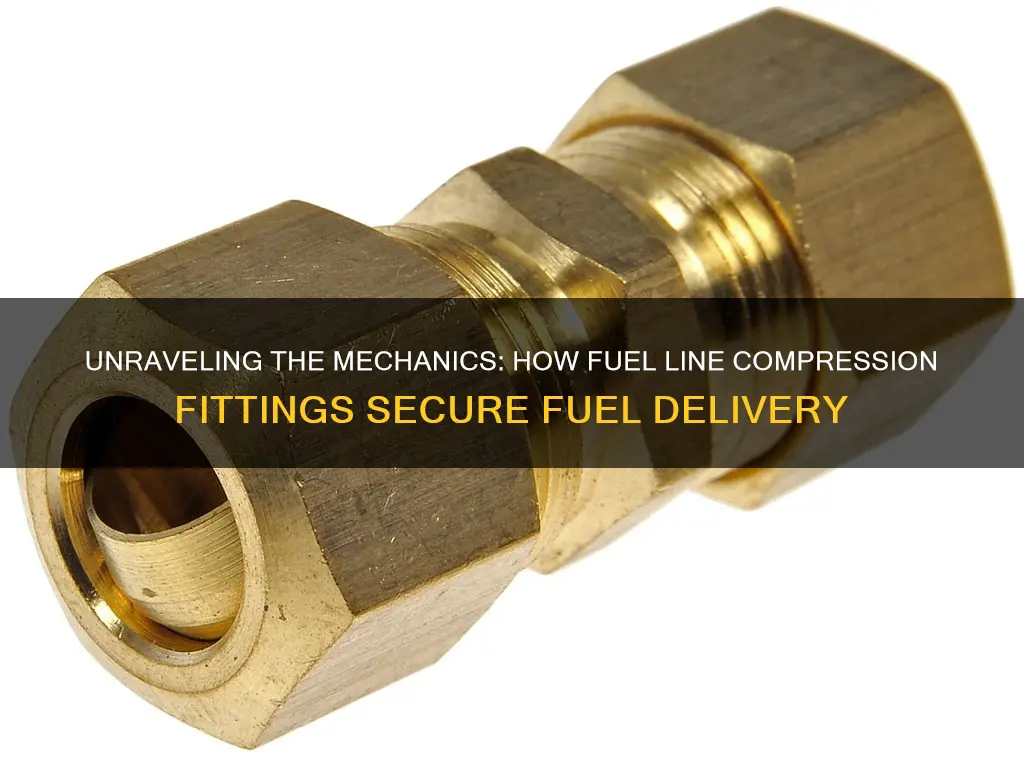
Fuel line compression fittings are an essential component in the automotive industry, providing a secure and reliable method to connect fuel lines to various systems in vehicles. These fittings utilize a compression mechanism to create a tight seal between the fitting and the fuel line, ensuring a safe and efficient transfer of fuel. The process involves inserting a fuel line into the fitting, which then compresses the line's outer casing, creating a secure and leak-proof connection. This method is widely used due to its simplicity, durability, and ability to withstand high pressure, making it a preferred choice for fuel delivery systems in cars, trucks, and other vehicles. Understanding the mechanics of these fittings is crucial for mechanics and enthusiasts alike to ensure proper installation and maintenance.
What You'll Learn
- Design and Structure: Compression fittings are designed to securely connect fuel lines by compressing the fitting onto the fuel line
- Sealing Mechanism: The compression fitting creates a tight seal by deforming the fuel line material, preventing fuel leaks
- Material Compatibility: Different materials are used for fittings to ensure compatibility with various fuel types and temperatures
- Pressure Management: Fittings regulate fuel pressure by allowing excess pressure to escape during the connection process
- Installation Process: Proper installation techniques involve tightening fittings to the correct torque specifications for optimal performance
Design and Structure: Compression fittings are designed to securely connect fuel lines by compressing the fitting onto the fuel line
Compression fittings are an essential component in the system, providing a reliable and secure method of connecting fuel lines. The design and structure of these fittings are crucial to their functionality and performance. The primary principle behind compression fittings is the mechanical compression of the fitting onto the fuel line, creating a tight and leak-free connection. This process involves a series of carefully engineered components and steps.
The fitting consists of a body, typically made of durable materials like brass or steel, with internal threads or a smooth bore. The fuel line, usually made of rubber or a flexible material, is inserted into the fitting. The key to a secure connection lies in the compression process. When the fitting is tightened, it applies pressure to the fuel line, compressing it within the fitting's body. This compression creates a sealing mechanism, ensuring that there is no movement or gap between the fitting and the fuel line. The force exerted by the fitting's threads or a dedicated compression ring compresses the fuel line's material, creating a tight seal.
The design of compression fittings often includes a unique feature called a 'ferrule' or 'compressible ring'. This component is typically made of a soft, durable material that is compressed when the fitting is assembled. The ferrule's material is designed to deform slightly under pressure, creating a reliable seal. As the fitting is tightened, the ferrule compresses around the fuel line, locking it in place and preventing any movement. This design ensures that the connection remains secure even under varying pressure and temperature conditions.
The structure of these fittings also includes a locking mechanism to ensure the connection's integrity. This mechanism can be in the form of a bayonet-style connection, where the fitting is rotated to lock into place, or a dedicated locking ring that secures the fitting onto the fuel line. These locking features prevent accidental disconnection and ensure that the compression force remains constant, providing a long-lasting and reliable seal.
In summary, compression fittings are engineered to create a secure and leak-free connection between fuel lines. The design incorporates compression, often with a ferrule or compressible ring, to apply pressure and seal the fuel line. The structure includes locking mechanisms to maintain the connection's integrity. This detailed design and precise structure make compression fittings a vital component in fuel systems, ensuring efficient and safe operation.
An6 Fuel Line Compatibility: 1997 Ford F150 Upgrade Guide
You may want to see also
Sealing Mechanism: The compression fitting creates a tight seal by deforming the fuel line material, preventing fuel leaks
The compression fitting is a crucial component in the system, designed to ensure a secure and leak-free connection between the fuel line and the engine. Its primary function is to create a tight seal, preventing any fuel from escaping and potentially causing engine misfires or other performance issues. This sealing mechanism is achieved through a simple yet effective process.
When a compression fitting is installed, it applies pressure to the fuel line material, typically a rubber or plastic hose. This pressure causes the material to deform slightly, creating a compression around the fitting. The deformation is carefully controlled to ensure it is not excessive, as this could lead to damage to the fuel line. The key to a successful seal lies in the precise amount of deformation, which must be sufficient to create a tight grip but not so much that it causes the material to tear or become brittle.
The deformation process creates a series of micro-compressions along the length of the fuel line, forming a continuous, tight seal. This seal is critical as it prevents any fuel from seeping through the connection, which could lead to a variety of problems. Fuel leaks can cause engine performance issues, such as reduced power and efficiency, and may even lead to dangerous situations if fuel comes into contact with a hot surface.
The compression fitting's design ensures that the seal is maintained over time, even with the constant expansion and contraction of the fuel line due to temperature changes. This is achieved through the use of durable materials and precise manufacturing processes, ensuring that the fitting can withstand the rigors of the engine environment.
In summary, the compression fitting's sealing mechanism relies on the controlled deformation of the fuel line material, creating a tight, continuous seal that prevents fuel leaks. This simple yet effective design is a vital component in maintaining the performance and safety of the engine fuel system.
Unclogging a Fuel Line: A Home Tank's Quick Fix
You may want to see also
Material Compatibility: Different materials are used for fittings to ensure compatibility with various fuel types and temperatures
When it comes to fuel line compression fittings, material compatibility is a critical aspect that ensures the system's reliability and longevity. Different materials are carefully selected to withstand the unique challenges posed by various fuel types and operating temperatures. This is because the choice of material directly impacts the performance, safety, and durability of the fuel system.
One common material used for these fittings is brass. Brass is an excellent choice due to its inherent corrosion resistance and ability to withstand a wide range of temperatures. It is particularly suitable for gasoline and diesel fuel systems, offering a reliable and cost-effective solution. The malleable nature of brass allows for easy installation and provides a secure connection between fuel lines and fittings.
For applications involving higher temperatures and more aggressive fuel types, such as aviation fuels, stainless steel becomes a preferred material. This metal offers superior corrosion resistance and can handle extreme temperatures without compromising its structural integrity. Stainless steel fittings are ideal for environments where fuel contains additives or impurities, ensuring that the material remains compatible and does not degrade over time.
In some cases, where extreme temperatures and high-pressure conditions are present, such as in racing or industrial applications, aluminum alloys might be considered. These alloys provide excellent thermal conductivity, which helps dissipate heat quickly. However, aluminum is not as corrosion-resistant as brass or stainless steel, so it is crucial to ensure proper maintenance and protection to prevent degradation.
Additionally, the choice of material can also depend on the specific fuel system design and requirements. For instance, in marine environments, where fuel systems are exposed to saltwater, materials like 316 stainless steel are preferred due to their superior corrosion resistance in such conditions. Each material has its advantages and is chosen based on the unique demands of the fuel type, temperature range, and environmental factors.
Visual Guide: Kinked Fuel Line for 2008 LMM Duramax
You may want to see also
Pressure Management: Fittings regulate fuel pressure by allowing excess pressure to escape during the connection process
Fuel line compression fittings are essential components in the automotive industry, particularly for vehicles that rely on internal combustion engines. These fittings play a crucial role in managing fuel pressure, ensuring a steady and controlled supply of fuel to the engine. The primary function of these fittings is to regulate pressure by allowing excess pressure to escape during the connection process, which is vital for the efficient operation of the fuel system.
When connecting fuel lines, the compression fitting acts as a pressure regulator, preventing the fuel from being subjected to excessive force. This is especially important as high-pressure fuel can lead to potential issues such as fuel line damage, leaks, and even engine misfires. By allowing excess pressure to escape, the fitting ensures that the fuel enters the system at a controlled rate, maintaining optimal pressure levels. This process is often referred to as 'pressure relief' and is a critical aspect of fuel system design.
The mechanism behind this pressure management is relatively simple yet effective. As the fuel line is connected to the fitting, the compression of the fitting's internal components creates a sealed connection. This compression process generates pressure, and any excess pressure is released through small vents or openings within the fitting. These vents are strategically positioned to allow pressure to escape without compromising the integrity of the connection. This controlled release of pressure ensures that the fuel line remains intact and functional.
In the context of fuel line compression fittings, the design and material choice are crucial factors. Fittings are typically made from durable materials like brass or stainless steel, ensuring they can withstand the high-pressure environment. The internal structure of the fitting, including the compression rings and seals, is engineered to provide a secure yet flexible connection. This flexibility allows for some movement during the connection process, accommodating potential variations in fuel line positioning.
By incorporating pressure management features, fuel line compression fittings contribute to the overall reliability and performance of the fuel system. They ensure that the engine receives a consistent and controlled fuel supply, optimizing combustion and power output. Additionally, these fittings help prevent fuel-related issues, such as engine knocking or performance degradation, which can occur when fuel pressure is not properly regulated. Understanding the role of these fittings in pressure management is essential for mechanics and enthusiasts alike, as it highlights the importance of proper installation and maintenance to ensure the longevity of the fuel system.
Mastering the Art of Fuel Line Disconnects: A Guide to Using the OEM Tool
You may want to see also
Installation Process: Proper installation techniques involve tightening fittings to the correct torque specifications for optimal performance
The installation process for fuel line compression fittings is a critical step to ensure the efficient and safe operation of your vehicle's fuel system. Proper installation techniques are essential to achieve optimal performance and prevent potential issues. Here's a detailed guide on how to install these fittings correctly:
When installing fuel line compression fittings, it is crucial to follow the manufacturer's guidelines and use the appropriate tools. Start by ensuring that the fuel lines are clean and free of any debris or contaminants. Inspect the fittings for any signs of damage or wear, and replace them if necessary. The process begins by inserting the male end of the fitting into the female port, ensuring a secure and snug fit. This initial step is vital as it sets the foundation for a successful installation.
The next step involves tightening the fittings to the specified torque values. Using a torque wrench, apply the correct amount of force to secure the fittings. Over-tightening can damage the threads or cause leaks, while under-tightening may result in poor sealing. The recommended torque specifications are typically provided by the manufacturer and should be followed precisely. It is an essential practice to ensure that the fittings remain tight and secure over time.
After tightening, inspect the connections for any leaks or signs of damage. Apply a small amount of fuel line sealant to the threads of the fittings to enhance their durability. This extra step provides an additional layer of protection against fuel contamination and potential engine issues. Allow the sealant to cure according to the manufacturer's instructions before reassembling the system.
Proper installation also includes considering the orientation of the fittings. Ensure that they are positioned in a way that allows for easy access during maintenance and avoids any potential interference with other components. By following these installation techniques, you can guarantee that your fuel line compression fittings will function optimally, providing a reliable and efficient fuel supply to your vehicle's engine.
Ethanol's Impact: Fuel Line Damage Explained
You may want to see also
Frequently asked questions
Fuel line compression fittings are used to securely connect fuel lines to fuel tanks, pumps, or other components in a vehicle's fuel system. They provide a tight seal to prevent fuel leaks and ensure efficient fuel transfer.
Compression fittings work by using a mechanical compression technique. The fitting consists of a body with internal threads or a compression nut. When assembled, the fitting compresses the fuel line onto the fitting's surface, creating a tight seal. This compression ensures that there is no movement between the fitting and the fuel line, reducing the risk of leaks and maintaining system integrity.
Yes, compression fittings offer several benefits. They are known for their durability and ability to withstand high-pressure fuel systems. The compression mechanism provides a reliable and long-lasting seal, even in harsh operating conditions. Additionally, compression fittings are relatively easy to install and can be used with various fuel line materials, making them a popular choice for automotive and industrial fuel systems.