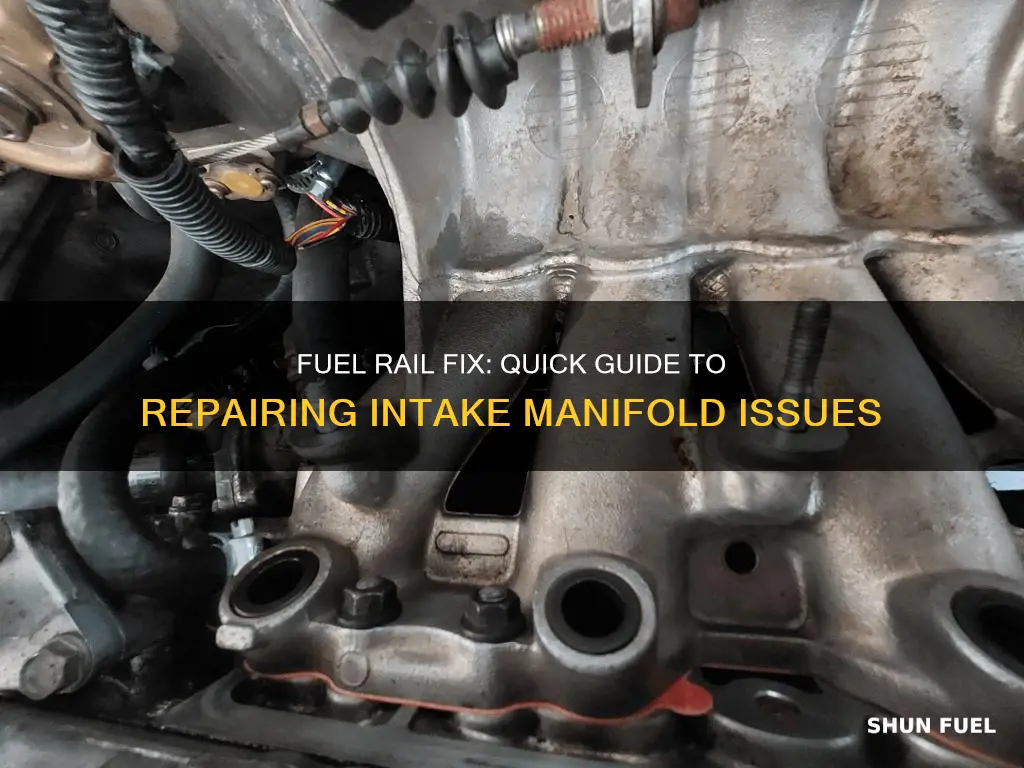
Fixing a fuel rail line that connects to the intake manifold is a crucial task for vehicle maintenance. This process involves replacing or repairing the damaged fuel rail line to ensure optimal fuel delivery to the engine. It requires careful disassembly of the engine components, precise installation of the new fuel rail line, and thorough testing to ensure proper functionality. This guide will provide a step-by-step approach to help vehicle owners or mechanics successfully tackle this repair, ensuring the engine operates efficiently and reliably.
What You'll Learn
- Fuel Rail Inspection: Check for damage, leaks, and proper mounting
- Fuel Pressure Test: Measure pressure using a gauge to ensure correct levels
- Intake Manifold Cleaning: Remove debris and carbon buildup for optimal performance
- Hose Replacement: Replace cracked or damaged hoses to prevent fuel leaks
- Fuel Pump Check: Verify proper operation and adjust as needed
Fuel Rail Inspection: Check for damage, leaks, and proper mounting
Fuel rail inspection is a crucial step in maintaining your vehicle's fuel system, especially when addressing issues related to the fuel rail line connecting to the intake manifold. This inspection ensures that the fuel rail is in optimal condition, preventing potential problems that could arise from damage, leaks, or improper mounting. Here's a comprehensive guide on how to inspect the fuel rail for these common issues:
Damage Assessment: Begin by visually examining the fuel rail for any signs of damage. Look for cracks, bends, or any visible imperfections on the metal surface. Over time, the fuel rail can be susceptible to corrosion or impact damage from road debris. Inspect the mounting points as well; ensure that the brackets and fasteners are secure and free from rust or deterioration. If you notice any damage, it's essential to replace the fuel rail to prevent further complications.
Leak Detection: Leaks in the fuel rail can lead to fuel loss, reduced engine performance, and potential safety hazards. Start by checking for any visible signs of fuel leakage around the connections and fittings. Apply a small amount of diesel fuel or a suitable leak detection fluid to the fuel rail and observe if any seepage occurs. Pay close attention to the areas where the fuel rail connects to the fuel pump, injectors, and the intake manifold. If a leak is detected, it's crucial to identify the source and repair or replace the affected components promptly.
Proper Mounting: The fuel rail's mounting is critical to ensure optimal fuel pressure and engine performance. Inspect the mounting points to ensure they are tight and secure. Check if the fuel rail is aligned correctly and if it moves freely without excessive play. Over time, vibrations from the engine can cause the fuel rail to become loose, leading to improper fuel distribution. If you find any mounting issues, retighten the fasteners or consider replacing worn-out mounting hardware.
During the inspection, it's beneficial to refer to your vehicle's manual for specific mounting requirements and torque specifications. Proper mounting ensures that the fuel rail is securely held in place, preventing any movement that could affect fuel pressure regulation.
Remember, regular maintenance and timely inspections can help identify and rectify fuel rail issues before they escalate. If you're unsure about any aspect of the inspection, consulting a professional mechanic is always a wise decision to ensure the job is done correctly.
Fire Sleeve: Protecting Aircraft Fuel Lines from Hazards
You may want to see also
Fuel Pressure Test: Measure pressure using a gauge to ensure correct levels
To ensure your fuel system is functioning correctly, it's crucial to perform a fuel pressure test. This test will help you identify any issues with the fuel rail line and the intake manifold, ensuring optimal engine performance. Here's a step-by-step guide on how to measure fuel pressure using a gauge:
Step 1: Prepare the Vehicle and Tools
Before you begin, make sure the vehicle is parked on a level surface and the engine is cool. Gather the necessary tools, including a fuel pressure gauge, a wrench, and a fuel pressure regulator. Ensure the gauge is compatible with your vehicle's fuel system and has the appropriate range for your engine's specifications.
Step 2: Locate the Fuel Rail and Gauge Connection
Locate the fuel rail, which is typically located near the engine's intake manifold. Identify the fuel rail line that connects to the intake manifold. This line is usually a high-pressure line and may require some force to disconnect. Carefully remove the fuel rail line from the intake manifold, ensuring you don't damage any surrounding components.
Step 3: Connect the Gauge
Now, it's time to connect the fuel pressure gauge. Attach the gauge's quick-connect fitting to the fuel rail line. Ensure a secure connection by tightening the fitting according to the manufacturer's instructions. Double-check that the gauge is properly aligned and connected to avoid any leaks or incorrect readings.
Step 4: Measure the Fuel Pressure
With the gauge connected, start the engine and allow it to idle. Observe the fuel pressure reading on the gauge. The ideal fuel pressure will vary depending on your engine's specifications, so consult your vehicle's manual for the correct range. If the pressure is too low, it may indicate a restricted fuel supply or a faulty fuel pump. If the pressure is too high, it could suggest a problem with the fuel pressure regulator or a clogged fuel filter.
Step 5: Interpret the Results
Record the fuel pressure reading. If the pressure is outside the recommended range, further investigation is required. You may need to check for any clogs or restrictions in the fuel system, inspect the fuel pump and regulator for defects, or consider consulting a professional mechanic for a more in-depth diagnosis.
Remember, this test is a crucial step in identifying and resolving issues related to the fuel rail line and intake manifold. By measuring the fuel pressure accurately, you can ensure your engine receives the correct amount of fuel, leading to improved performance and efficiency.
Mastering Kicker Motor Fuel Line Connections: A Comprehensive Guide
You may want to see also
Intake Manifold Cleaning: Remove debris and carbon buildup for optimal performance
The intake manifold, a crucial component in your engine's air-fuel delivery system, can accumulate debris and carbon buildup over time, leading to reduced engine performance and potential issues with the fuel rail. Cleaning the intake manifold is an essential maintenance task to ensure optimal engine operation and longevity. Here's a step-by-step guide to effectively remove debris and carbon deposits:
Step 1: Inspection and Preparation
Before beginning the cleaning process, inspect the intake manifold for any visible signs of damage or excessive buildup. Look for cracks, warping, or significant carbon deposits. If you notice any severe issues, it might be necessary to consult a professional mechanic. Ensure you have the necessary tools, including a screwdriver, a small brush, and a compressed air canister.
Step 2: Remove the Intake Manifold
Accessing the intake manifold for cleaning often requires removing it from the engine. This process varies depending on your vehicle's make and model. Typically, you'll need to disconnect the vacuum hose, remove the air intake boot, and carefully detach the manifold from the engine block. Refer to your vehicle's service manual for specific instructions.
Step 3: Cleaning the Intake Manifold
Once the manifold is removed, you can start the cleaning process. Use a small brush or a specialized intake manifold cleaner to gently scrub away carbon deposits and debris. Pay close attention to the areas around the throttle body, vacuum ports, and any crevices. Compressed air can be used to blow out loose particles. For stubborn buildup, consider using a mild acid-based cleaner, but always follow safety guidelines and rinse thoroughly.
Step 4: Reassembly and Testing
After cleaning, ensure all components are properly dried to prevent moisture-related issues. Reinstall the intake manifold, securing it according to the manufacturer's instructions. Start the engine and check for any leaks or unusual noises. Allow the engine to run for a few minutes to ensure proper operation. Monitor the engine's performance, and if you notice any improvements, you've successfully addressed the carbon buildup.
Regular intake manifold cleaning is essential to maintain a healthy engine and ensure optimal fuel-air mixture delivery. By removing debris and carbon buildup, you can improve engine performance, fuel efficiency, and overall longevity. Remember, proper maintenance can save you from potential issues and costly repairs in the future.
Mastering the Art of Fuel Line Removal: A Step-by-Step Guide
You may want to see also
Hose Replacement: Replace cracked or damaged hoses to prevent fuel leaks
When dealing with issues related to the fuel rail line and its connection to the intake manifold, one crucial aspect often overlooked is the condition of the hoses. Hoses play a vital role in the fuel delivery system, and their integrity is essential to ensure optimal engine performance and prevent potential hazards. If you notice any signs of damage or wear, replacing the hoses is a necessary step to maintain the overall health of your vehicle.
The first step in hose replacement is identifying the damaged hoses. Inspect the fuel rail line and the intake manifold area thoroughly. Look for any visible cracks, splits, or signs of deterioration. Cracks may appear as small or large fissures on the hose's surface, often caused by age, heat, or chemical exposure. Over time, hoses can become brittle and prone to cracking, especially if they are old or have been exposed to extreme temperatures. Additionally, check for any signs of fuel leakage around the hose connections and fittings. Even a small crack can lead to significant fuel loss, impacting engine performance and potentially causing dangerous situations.
Once you've identified the damaged hoses, it's time to replace them. Start by disconnecting the old hoses from the fuel rail and the intake manifold. Carefully remove any clips or fasteners that secure the hoses in place. Take note of the hose's orientation and any specific routing to ensure a proper fit for the new hose. When replacing the hoses, opt for high-quality replacements that are compatible with your vehicle's make and model. This ensures a precise fit and optimal performance. Ensure that the new hoses have the same length, diameter, and routing as the originals to maintain the integrity of the fuel delivery system.
After installing the new hoses, reattach them securely to the fuel rail and intake manifold. Tighten the connections firmly but avoid over-tightening, as this can damage the hoses. Double-check all connections to ensure they are tight and secure. Once the hoses are in place, start the engine and check for any leaks. Even a small amount of fuel leakage should be addressed immediately, as it can lead to dangerous situations. If no leaks are detected, test the engine's performance to ensure it runs smoothly and efficiently.
Regular maintenance and inspection of the fuel rail line and associated hoses are essential to prevent fuel leaks and ensure the longevity of your vehicle. By replacing cracked or damaged hoses, you can maintain a reliable fuel supply to the engine, optimizing performance and safety. Remember, addressing hose issues promptly can save you from potential breakdowns and costly repairs in the long run.
Maximizing Engine Performance: The Role of Fuel Coolers in Return Lines
You may want to see also
Fuel Pump Check: Verify proper operation and adjust as needed
When dealing with fuel system issues, it's crucial to start with a thorough inspection of the fuel pump to ensure it's functioning correctly. Here's a step-by-step guide to checking and adjusting the fuel pump as needed:
- Locate the Fuel Pump: Begin by identifying the fuel pump, which is typically located near the fuel tank. It is responsible for supplying fuel to the engine through the fuel rail. Accessing the pump might require removing some components, such as the fuel tank straps or the underbody panels, depending on your vehicle's design.
- Inspect for Visual Damage: Carefully examine the fuel pump for any signs of damage or wear. Look for cracks, leaks, or corrosion around the pump's housing. If any issues are found, the pump may need to be replaced. Even minor damage can lead to improper fuel delivery, exacerbating the problem with the fuel rail line.
- Test Pump Operation: To verify the pump's functionality, you can use a fuel pressure gauge. Disconnect the fuel line from the pump and attach the gauge to measure the pressure. The reading should be within the manufacturer's specified range. If the pressure is too low, the pump might be failing and needs attention.
- Adjust Pump Settings (if applicable): Some vehicles allow for adjusting the pump's settings to optimize fuel delivery. This is often done through the engine control unit (ECU) or a dedicated fuel pump control module. Consult your vehicle's manual to locate the adjustment settings. Fine-tuning these settings can improve fuel flow and potentially resolve the issue with the fuel rail line.
- Check for Clogged Lines: While primarily focused on the pump, don't overlook potential clogs in the fuel lines. Use a fuel line cleaner or a compressed air gun to clear any blockages. Clogged lines can restrict fuel flow, leading to improper operation of the fuel rail and intake manifold.
Remember, if you're unsure about any step or encounter complex issues, it's best to consult a professional mechanic who can provide expert guidance and ensure the problem is resolved safely and effectively.
Mechanic's Guide: Detecting Fuel Line Leaks: A Step-by-Step Process
You may want to see also
Frequently asked questions
The fuel rail line is a crucial component in the fuel injection system, and any issues with it can lead to improper fuel delivery. Common causes include clogs, leaks, or damage to the fuel pump, which can result in reduced fuel pressure and poor engine performance.
Signs of a faulty fuel rail line include engine misfires, reduced power, rough idling, or a noticeable decrease in fuel efficiency. You may also notice a hissing sound or see fuel leaks around the rail or manifold.
Simple issues like clogs can often be resolved by a DIY approach. You can use fuel system cleaner to flush out deposits. However, for more complex problems like leaks or pump issues, it's best to consult a professional mechanic to ensure proper diagnosis and repair.
Start by identifying the source of the issue. If it's a clog, you can use a fuel pressure gauge to check pressure and a fuel pump tester to ensure it's functioning. For leaks, inspect the rail and manifold for damage or cracks. You may need to replace gaskets or seals. Always refer to the vehicle's manual for specific instructions.
In some cases, you can temporarily address the issue by using a fuel additive to improve fuel flow. However, this is a short-term fix and should not be considered a permanent solution. It's essential to get the fuel rail line repaired or replaced to ensure optimal engine performance and prevent further damage.