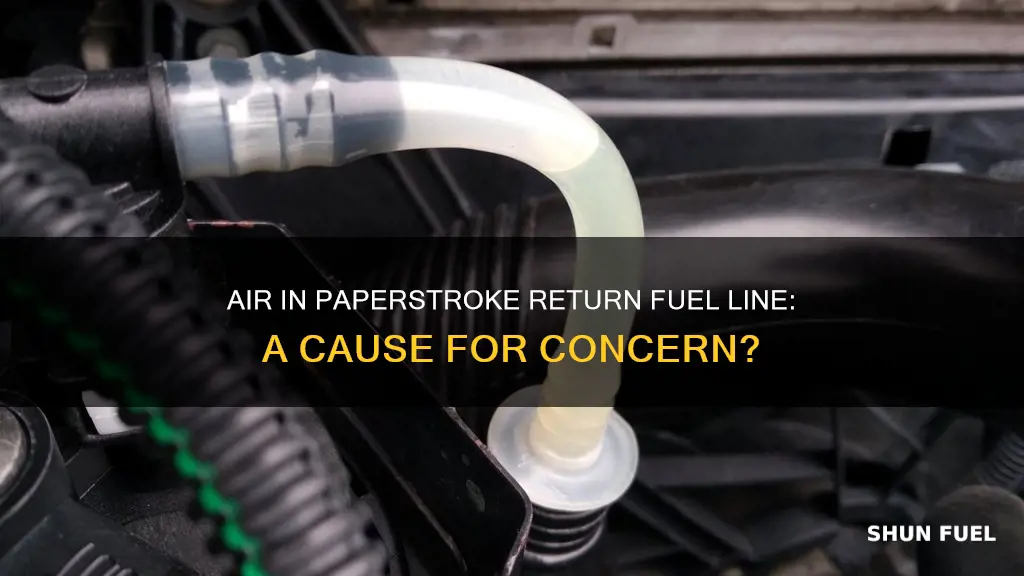
The air in a paperstroke return fuel line is a critical component of engine performance and efficiency. It is essential to understand the role of air in this system to ensure optimal operation. The presence of air in the fuel line can significantly impact the engine's performance, potentially leading to reduced power, poor fuel economy, and even engine damage. This introduction aims to explore the importance of maintaining a proper air-fuel mixture and the potential consequences of air entering the return fuel line.
What You'll Learn
- Air in Fuel Line: Air bubbles in the fuel line can cause engine misfires and reduced performance
- Fuel Pump: The fuel pump should be checked for proper operation to prevent air entry
- Fuel Filter: Clogged fuel filters can trap air, leading to engine issues
- Fuel Injectors: Air in the fuel line can cause improper fuel distribution to injectors
- Engine Performance: Air in the return line affects engine power, fuel efficiency, and overall performance
Air in Fuel Line: Air bubbles in the fuel line can cause engine misfires and reduced performance
Air bubbles in the fuel line can be a common yet often overlooked issue that significantly impacts engine performance. When air enters the fuel line, it can lead to a variety of problems, with engine misfires being one of the most noticeable symptoms. This phenomenon is particularly relevant in engines that use a paperstroke return fuel line, where the fuel is transported from the tank to the engine via a paper-based filter system.
The presence of air bubbles in the fuel line can be caused by several factors. One common reason is the natural expansion and contraction of the fuel as it moves through the system, especially when the engine is idling or when there are rapid changes in temperature. This can lead to the formation of bubbles, which may not be immediately apparent but can have detrimental effects on engine operation.
When air bubbles are introduced into the fuel stream, they can disrupt the precise fuel-to-air mixture required for efficient combustion. This disruption often results in incomplete burning of the fuel, leading to misfires. Misfires occur when a cylinder fails to ignite the air-fuel mixture properly, causing the engine to lose power and potentially stall. Over time, this can cause significant wear and tear on engine components, reducing its overall lifespan.
To address this issue, it is essential to ensure that the fuel line is free from any obstructions or blockages that might trap air. Regularly checking for and removing any air locks in the system is crucial. Additionally, maintaining a consistent and stable fuel pressure can help minimize the introduction of air bubbles. This can be achieved by using a fuel pump that provides a steady flow of fuel, ensuring that any potential air bubbles are quickly dispersed.
In summary, the presence of air in the fuel line, especially in paperstroke return systems, can lead to engine misfires and reduced performance. Understanding the causes and implementing preventive measures can help ensure optimal engine operation and longevity. Regular maintenance and attention to the fuel system's integrity are key to avoiding these common issues.
Air Bubbles in Diesel Fuel Lines: A Cause for Concern?
You may want to see also
Fuel Pump: The fuel pump should be checked for proper operation to prevent air entry
The fuel pump is a critical component in any vehicle's fuel system, and its proper function is essential to ensure optimal engine performance and longevity. One of the primary roles of the fuel pump is to deliver fuel from the tank to the engine at the required pressure. However, if the fuel pump is not operating correctly, it can lead to several issues, including air entering the fuel line, which can cause significant problems.
Air in the fuel line, often referred to as 'air lock' or 'air bubbles', is a common issue that can arise when the fuel pump fails to maintain the necessary pressure. This situation occurs when the pump cannot effectively push fuel through the system, leading to a drop in pressure and the potential for air to enter the line. When air is present in the fuel, it can cause a variety of engine problems, such as poor fuel atomization, reduced power output, and even engine misfires.
To prevent air entry into the fuel line, it is crucial to regularly inspect and maintain the fuel pump. Here are some steps to ensure the fuel pump is functioning correctly:
- Visual Inspection: Start by visually checking the fuel pump for any signs of damage, wear, or leaks. Look for cracks, corrosion, or any visible deterioration. Also, inspect the fuel lines for any bends or kinks that might restrict fuel flow.
- Pressure Testing: Use a fuel pressure gauge to measure the pressure at the fuel pump outlet. The pressure should meet the manufacturer's specifications. If the pressure is too low, it indicates a potential issue with the pump or the fuel line.
- Pump Operation: Listen to the fuel pump while the engine is running. It should produce a steady, rhythmic sound, indicating proper operation. If the pump is silent or makes unusual noises, it may need to be replaced.
- Fuel Filter Check: Inspect the fuel filter for clogs or contamination. A dirty or clogged filter can restrict fuel flow, leading to air entry. Regularly replacing the fuel filter is essential for maintaining the overall health of the fuel system.
- Professional Maintenance: Consider seeking professional assistance for a comprehensive fuel system inspection. Technicians can use specialized tools to measure fuel pressure and flow rates, ensuring the system is functioning optimally.
By following these maintenance practices, you can effectively prevent air from entering the fuel line, thus ensuring the fuel pump operates efficiently and the engine performs at its best. Regular attention to the fuel pump and associated components is vital to avoid potential engine issues caused by air contamination in the fuel.
Outboard Motor Fuel Line: To Disconnect or Not to Disconnect?
You may want to see also
Fuel Filter: Clogged fuel filters can trap air, leading to engine issues
A clogged fuel filter is a common issue that can have significant consequences for your engine's performance. When a fuel filter becomes blocked, it can restrict the flow of fuel, leading to a variety of problems. One of the most common issues associated with a clogged fuel filter is the presence of air in the fuel line.
Air in the fuel line can occur when the fuel filter traps air bubbles, which are then carried along with the fuel. This can happen due to several reasons. Firstly, over time, the filter may accumulate dirt, debris, and contaminants, which can cause it to become blocked. When this happens, the fuel has to pass through the filter, and any air bubbles present in the fuel will be trapped and forced into the fuel line. Secondly, if the fuel filter is not properly installed or is damaged, it may not effectively separate the fuel from the air, allowing air bubbles to enter the system.
The presence of air in the fuel line can lead to several engine problems. One of the most noticeable issues is a loss of power. When air enters the fuel, it can cause the engine to run inefficiently, resulting in reduced power output. You may notice that your vehicle struggles to accelerate, and the overall performance may decline. Additionally, air in the fuel can lead to engine misfires, where the engine fails to ignite the fuel properly, causing it to run roughly and potentially leading to damage over time.
To address this issue, it is essential to regularly inspect and maintain your fuel filter. Clogged fuel filters should be replaced or cleaned to ensure optimal performance. If you suspect that your fuel filter is clogged, it is recommended to consult a professional mechanic who can inspect the filter and the fuel system to identify any further issues. They may also advise on the best course of action, which could include replacing the filter or performing a thorough cleaning.
In summary, a clogged fuel filter can trap air in the fuel line, causing engine problems such as reduced power and misfires. Regular maintenance and timely replacement of the fuel filter are crucial to prevent these issues and ensure your engine operates efficiently. Remember, proper care and attention to the fuel system can help avoid costly repairs and maintain the overall health of your vehicle.
Outboard Fuel Confusion: Diesel or Gasoline? Unraveling the Mystery
You may want to see also
Fuel Injectors: Air in the fuel line can cause improper fuel distribution to injectors
The presence of air in the fuel line, particularly in a paperstroke return fuel line, can have significant implications for the performance and efficiency of a vehicle's fuel injection system. When air enters the fuel line, it can lead to several issues that directly impact the proper functioning of the fuel injectors.
One of the primary consequences is improper fuel distribution to the injectors. Fuel injectors are responsible for precisely metering and delivering fuel to the engine's cylinders. However, when air is introduced into the fuel line, it can cause the fuel to become less dense and more volatile. This change in fuel properties can result in inaccurate fuel measurements, leading to an imbalance in the fuel-to-air mixture. As a result, the engine may not receive the correct amount of fuel at each injection event, causing poor performance, reduced power, and potential engine misfires.
Air bubbles in the fuel line can also lead to fuel atomization issues. Proper atomization is crucial for efficient combustion, as it ensures that the fuel is broken down into small droplets, allowing for better mixing with air and complete combustion. When air is present, the fuel may not atomize effectively, leading to larger fuel droplets. This can result in incomplete burning, increased emissions, and reduced engine performance.
To address this problem, it is essential to maintain a fuel system that is free from air bubbles. One common solution is to use a fuel filter that can trap air and other contaminants. Additionally, ensuring that the fuel pump is functioning correctly and that there are no leaks in the fuel line can help prevent air from entering the system. Regular maintenance and inspection of the fuel system can help identify and rectify any issues related to air in the fuel line, ensuring optimal performance and longevity of the fuel injectors.
In summary, the introduction of air into the fuel line, especially in a paperstroke return fuel line, can significantly impact the fuel injectors' ability to deliver the correct fuel-air mixture to the engine. This can result in poor engine performance, misfires, and increased emissions. Proper maintenance and the use of appropriate filters can help mitigate these issues, ensuring the fuel injectors function optimally.
GSXR 750 Fuel Line Leaks: Normal or Cause for Concern?
You may want to see also
Engine Performance: Air in the return line affects engine power, fuel efficiency, and overall performance
The presence of air in the return fuel line of a piston engine can significantly impact its performance and efficiency. This issue is particularly relevant for diesel engines, where the fuel-air mixture is injected directly into the combustion chamber. When air enters the return line, it can lead to several detrimental effects on engine operation.
One of the primary consequences is a reduction in engine power output. Air bubbles in the fuel line can cause inconsistent fuel delivery to the injectors. This inconsistency results in incomplete combustion, leading to a decrease in power and torque. Engine power is directly related to the efficiency of the fuel-air mixture's combustion, and any disruption in this process can have a noticeable impact on performance.
Moreover, the presence of air can negatively affect fuel efficiency. When air is mixed with the fuel in the return line, it can lead to inefficient fuel usage. This inefficiency occurs because the air dilutes the fuel, requiring more fuel to achieve the same power output. As a result, engines with air in the return line may experience a noticeable drop in fuel economy, which is a critical factor for vehicles and machinery that operate over long distances or require frequent refueling.
Engine performance and longevity can also be compromised. Air bubbles can cause erratic engine behavior, leading to rough idling, poor throttle response, and even engine stalling. Over time, the constant presence of air in the fuel can cause fuel pump wear and potential damage to the injectors, resulting in costly repairs or premature engine failure.
To address this issue, it is essential to ensure that the return fuel line is free from air bubbles. This can be achieved by using a fuel filter with a built-in air separator or by implementing a fuel return line design that minimizes the risk of air intrusion. Regular maintenance, including fuel system checks and the use of high-quality fuel, can also help prevent air from entering the return line, thus maintaining optimal engine performance and longevity.
Braided Fuel Line Protection: Sealing the Deal
You may want to see also
Frequently asked questions
No, it is not necessary or desirable to have air in the paperstroke return fuel line. Air in this line can lead to several issues, such as reduced engine performance, fuel efficiency problems, and potential engine damage. The fuel line should be designed to carry fuel only, ensuring a smooth and efficient flow without any air bubbles.
Engine misfires occur when the air-fuel mixture in the engine's cylinders is not properly ignited. Air bubbles in the fuel line can disrupt the fuel flow, leading to an incorrect air-fuel ratio. This results in incomplete combustion, causing the engine to misfire and potentially leading to performance issues and increased emissions.
To prevent air from entering the fuel line, it is essential to ensure proper installation and maintenance. Check for any leaks or damage to the fuel lines and replace them if necessary. Use fuel filters to trap any contaminants, including air, and regularly inspect the fuel system for any signs of air intrusion. Proper grounding and the use of fuel-line inhibitors can also help minimize air bubbles.
Several indicators can suggest the presence of air in the fuel system. These include engine hesitation or stalling during acceleration, rough idling, and reduced engine power. You might also notice a decrease in fuel efficiency and increased fuel consumption. If you observe any of these symptoms, it is advisable to inspect the fuel lines and system for air bubbles and address any issues promptly.