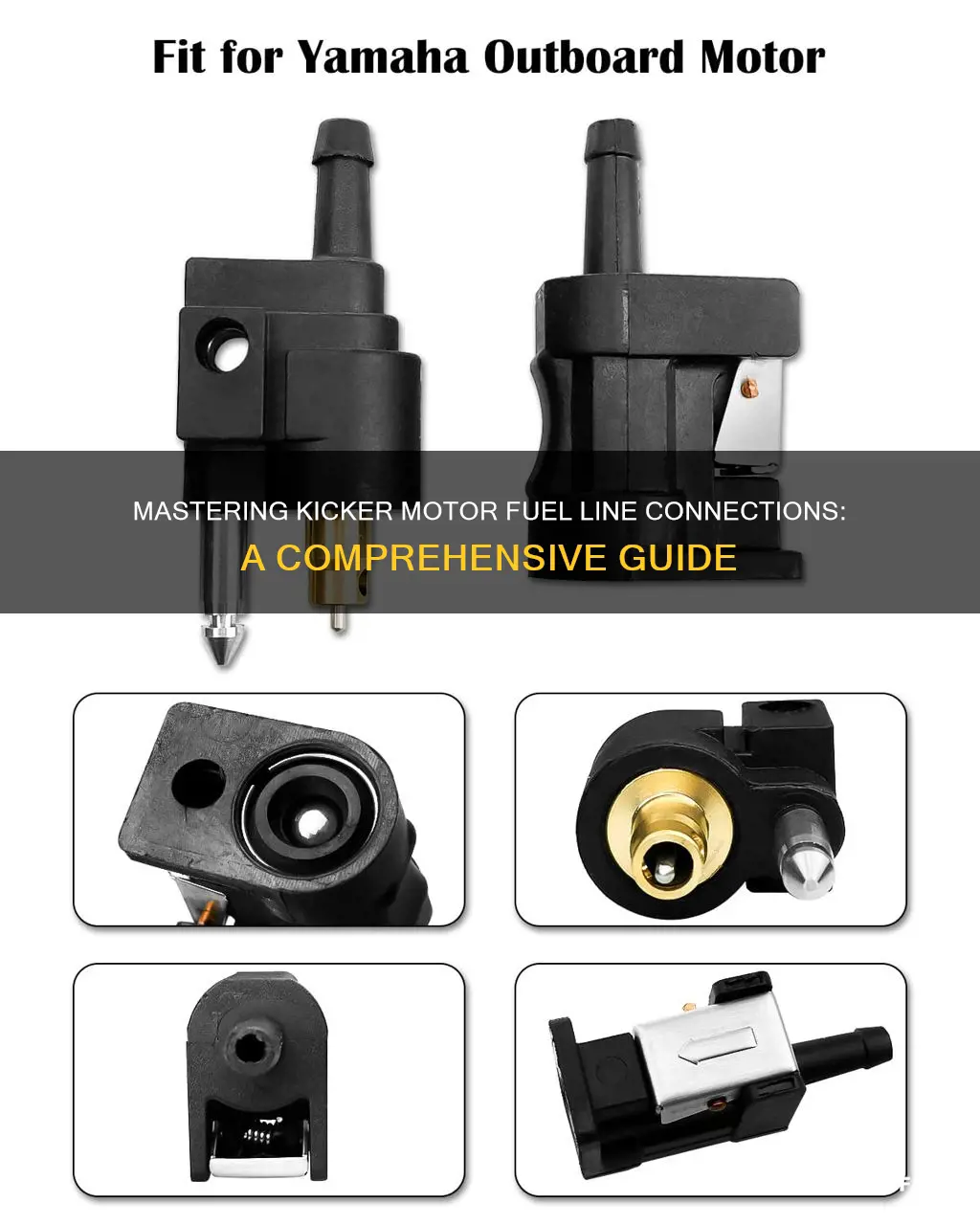
Connecting a fuel line to a kicker motor requires careful attention to detail and adherence to safety guidelines. This process involves several steps, including selecting the appropriate fuel line size and material, ensuring a secure connection at the motor and fuel tank, and properly routing the line to avoid damage. It is crucial to understand the specific requirements of your kicker motor and fuel system to ensure a reliable and safe setup. By following a step-by-step guide and using the right tools, you can effectively connect the fuel line, ensuring optimal performance and longevity of your kicker motor.
What You'll Learn
- Prepare Tools: Gather necessary tools like fuel line, connectors, and a fuel filter
- Locate Fuel Source: Identify the main fuel supply and ensure it's accessible
- Connect Fuel Line: Attach the kicker motor fuel line to the main line securely
- Test for Leaks: Inspect connections for any leaks and tighten if necessary
- Secure Connections: Use clamps or brackets to keep the fuel lines in place
Prepare Tools: Gather necessary tools like fuel line, connectors, and a fuel filter
Before you begin the process of connecting the fuel line to your Kicker motor, it's crucial to ensure you have all the necessary tools and components ready. This preparation will make the installation process smoother and more efficient. Here's a step-by-step guide on what you need to gather:
Fuel Line and Connectors: Start by acquiring the correct fuel line, which is specifically designed for marine or automotive applications, depending on your Kicker motor's requirements. Measure and cut the fuel line to the appropriate length, ensuring it's long enough to reach from the fuel source to the motor. Along with the fuel line, you'll need various connectors to join the line to the motor and the fuel source. These connectors should be compatible with the fuel line material and size. Common types include quick-connect fittings, barbed connectors, and compression fittings.
Fuel Filter: A fuel filter is an essential component to ensure clean fuel delivery to your motor. It helps remove contaminants and debris from the fuel, preventing potential damage to the engine. Choose a fuel filter that is compatible with your Kicker motor's specifications. Consider the filter's capacity and flow rate to ensure it can handle the fuel volume required by your motor.
Other Tools: In addition to the above components, you'll need some basic tools to facilitate the installation. These include a fuel pump primer bulb (if required), a fuel gauge (if applicable), and a fuel pressure gauge (for monitoring). Also, gather some cleaning supplies like fuel line cleaner or a solvent to ensure a thorough cleaning of the fuel system before installation.
Having all these tools and components prepared beforehand will save you time and effort during the installation process. It ensures that you can work efficiently and effectively, minimizing any potential delays or complications. Remember to double-check the compatibility of each part with your Kicker motor to guarantee a successful fuel line connection.
WRX Fuel Line: Discover the Perfect OEM Size
You may want to see also
Locate Fuel Source: Identify the main fuel supply and ensure it's accessible
When connecting a fuel line to your kicker motor, the first crucial step is to locate the main fuel source. This involves identifying the primary fuel supply in your vehicle or marine setup. The fuel source could be a fuel tank, a fuel cell, or a fuel reservoir, depending on your system. It's essential to understand the layout of your vessel or vehicle to pinpoint the exact location of this fuel supply.
Start by consulting your vehicle's manual or the manufacturer's guidelines. These resources will provide detailed information about the fuel system, including the type and location of the fuel tank or reservoir. Look for diagrams or illustrations that show the fuel lines and their connections. This visual representation will help you understand the path the fuel takes from the source to the engine.
If you're working on a marine application, such as a boat or personal watercraft, you might need to inspect the fuel system more closely. Locate the fuel tank, which is typically found in the hull or a designated fuel compartment. Identify the fuel pump, as it is responsible for sending fuel from the tank to the engine. The fuel pump is usually located near the engine or in the fuel tank itself. Understanding the pump's function and its connection to the fuel lines is vital for a successful installation.
Once you've identified the main fuel supply, ensure that it is easily accessible. This accessibility is crucial for maintenance and future refuelling. If the fuel source is in a hard-to-reach location, you might need to consider moving the vehicle or boat to a more convenient spot. Proper access will make the installation process smoother and safer, allowing you to connect the fuel line without any unnecessary complications.
Remember, the key to a successful fuel line connection is thorough preparation. By locating and assessing the main fuel supply, you set the foundation for a well-executed project. This initial step ensures that you have a clear understanding of the fuel system, making the subsequent tasks of connecting the fuel line and securing it in place much more manageable.
Mastering LS Swap Fuel Lines: A Comprehensive Guide
You may want to see also
Connect Fuel Line: Attach the kicker motor fuel line to the main line securely
When connecting the fuel line to your kicker motor, it's crucial to ensure a secure and reliable attachment to prevent any fuel leaks or system malfunctions. Here's a step-by-step guide to help you achieve this:
Start by locating the main fuel line that runs from your fuel tank to the engine. Identify the appropriate port on the engine where the kicker motor's fuel line will connect. Kicker motors typically require a specific fuel supply, so ensure you have the correct fittings and adapters if needed. Clean the fuel line and the engine port to remove any dirt or debris. This step is essential to ensure a tight and leak-free connection. Use a fuel line cleaner or a mild detergent to clean the surfaces. Rinse thoroughly to remove any cleaning agents.
Now, take the kicker motor's fuel line and align it with the engine port. Ensure that the line is positioned correctly and that there is no kinking or bending that could restrict fuel flow. Secure the fuel line using the appropriate fittings and clamps. Tighten the connections securely but be careful not to overtighten, as this can damage the fuel line. Check for any leaks at the connection points. A small amount of fuel should be applied to the connection to ensure there are no leaks. If any fuel is observed, tighten the fittings further or check for any damage to the line.
Once the fuel line is securely attached, double-check all connections to ensure they are tight and won't come loose during operation. Consider using fuel line tape or protective sleeves to safeguard the connection from any potential damage. This is especially important if the kicker motor is used frequently or in harsh conditions. Properly securing the fuel line will ensure that your kicker motor receives the necessary fuel supply, allowing it to function optimally without any fuel-related issues.
Remember, a well-connected fuel line is vital for the efficient operation of your kicker motor. Take the time to inspect and secure the connections properly to avoid any unnecessary complications.
Electric Fuel Pumps: The Case for a Return Line
You may want to see also
Test for Leaks: Inspect connections for any leaks and tighten if necessary
When connecting a fuel line to a kicker motor, it's crucial to ensure a secure and leak-free setup. Start by examining all connections for any signs of leakage. This includes the fuel line itself, the fittings, and the motor's fuel inlet. Look for any wet spots or stains around the connections, as these could indicate a potential leak. If you notice any moisture, it's essential to address the issue promptly.
Use a simple yet effective method to test for leaks. Apply a small amount of diesel fuel or a suitable sealer to the connections and observe for any seepage. If you see fuel seeping out, it's a clear indication of a leak. In such cases, you'll need to tighten the connections or replace the affected parts. Ensure that all fittings are properly tightened to the recommended torque specifications to prevent any potential leaks.
Tightening the connections is a straightforward process. Locate the nuts and bolts securing the fuel line to the motor and the fittings. Use a wrench or a socket to tighten them further if they are loose. Remember, the goal is to achieve a secure fit without overtightening, as this can damage the fuel line or fittings. It's a good practice to torque the connections to the manufacturer's recommended specifications to ensure a reliable seal.
If you encounter persistent leaks despite tightening, it might be necessary to replace the affected components. This could include the fuel line, fittings, or even the motor's fuel inlet. Always refer to the manufacturer's instructions or consult a professional for guidance on replacing these parts to ensure compatibility and proper installation.
Regular maintenance and inspections are vital to keeping your kicker motor reliable. By taking the time to test for leaks and tighten connections, you can prevent potential issues and ensure your motor operates efficiently and safely. This simple yet essential step will help you maintain a well-functioning system and avoid any unwanted fuel-related problems.
Polaris Ranger Fuel Line: Location and Access Guide
You may want to see also
Secure Connections: Use clamps or brackets to keep the fuel lines in place
When connecting fuel lines for your kicker motor, ensuring secure and reliable connections is crucial to prevent leaks and maintain optimal performance. One effective method to achieve this is by using clamps or brackets to keep the fuel lines in place. These simple yet essential tools provide a robust solution to potential movement and vibration-induced issues.
Clamps are an excellent choice for securing fuel lines due to their versatility and ease of use. You can opt for various types, such as hose clamps or band clamps, which offer a tight grip around the fuel lines. When installing, ensure you follow these steps: First, measure and mark the desired length of the fuel line. Then, carefully slide the clamp over the fuel line, positioning it securely. Finally, tighten the clamp using a tool, ensuring it is snug but not overly tight to avoid damage. Place the clamp at regular intervals along the fuel line to provide multiple points of support.
Brackets, on the other hand, offer a more permanent solution, especially for longer fuel lines. These are typically made of sturdy materials like metal or plastic and are designed to attach to the motor or the boat's structure. Here's a simple guide: Measure and mark the mounting points on your kicker motor and the boat's frame. Then, attach the brackets to these points using appropriate hardware. Slide the fuel lines through the brackets, ensuring they are taut and secure. Tighten any screws or fasteners to hold the brackets in place. This method provides a clean and professional look while ensuring the fuel lines remain stable.
Using clamps or brackets is a practical way to prevent fuel line movement, which can lead to potential hazards and performance issues. By keeping the fuel lines secure, you reduce the risk of leaks, ensure a steady fuel supply to the motor, and maintain the overall reliability of your kicker motor setup. Remember, proper installation and regular checks of these securing mechanisms are essential for long-term success.
Classic BMW E28: Metal Fuel Line or Not?
You may want to see also
Frequently asked questions
Connecting the fuel line to your Kicker motor requires careful attention to detail to ensure a secure and leak-free connection. Start by ensuring you have the correct size and type of fuel line for your motor. Then, locate the fuel inlet on the motor, which is usually a dedicated port with a cap or plug. Remove the cap or plug to expose the threads or quick-connect fittings. Clean the threads or fittings to remove any debris or old fuel residue. Apply a thin layer of thread sealant (optional but recommended) to the threads or fittings. Then, thread the fuel line onto the motor's inlet, ensuring a tight and secure connection. Tighten the line with a wrench, being careful not to overtighten, as this can damage the threads or fittings. Once connected, check for any leaks by running your finger around the connection and applying slight pressure. If no leaks are detected, you can secure the fuel line with a clamp or tie-wrap to keep it in place.
If you're having trouble connecting the fuel line, it's important to troubleshoot the issue. First, ensure that the fuel line is the correct size and type for your Kicker motor. Check for any bends or kinks in the line that might be causing interference. If the line is flexible, try straightening it out and reattaching it. If the issue persists, inspect the motor's inlet for any damage or debris. Clean the threads or fittings and reapply thread sealant if necessary. Make sure the fuel line is aligned properly with the inlet. If the line has a quick-connect fitting, ensure it is fully engaged and locked into place. If none of these steps resolve the issue, consider consulting the Kicker motor's manual or contacting their customer support for further guidance.
Regular maintenance of the fuel line connection is essential to ensure optimal performance and longevity. After connecting the fuel line, it's a good practice to run the motor for a short period to allow the fuel to pass through and ensure a proper seal. Periodically inspect the connection for any signs of wear, cracks, or corrosion. If you notice any damage, replace the fuel line promptly. Keep the fuel line and connections clean by using a fuel filter and regularly checking for any clogs or debris. Additionally, avoid using excessive force when tightening connections, as this can lead to damage. It's also a good idea to check the fuel line for any signs of deterioration or damage during routine motor maintenance checks.