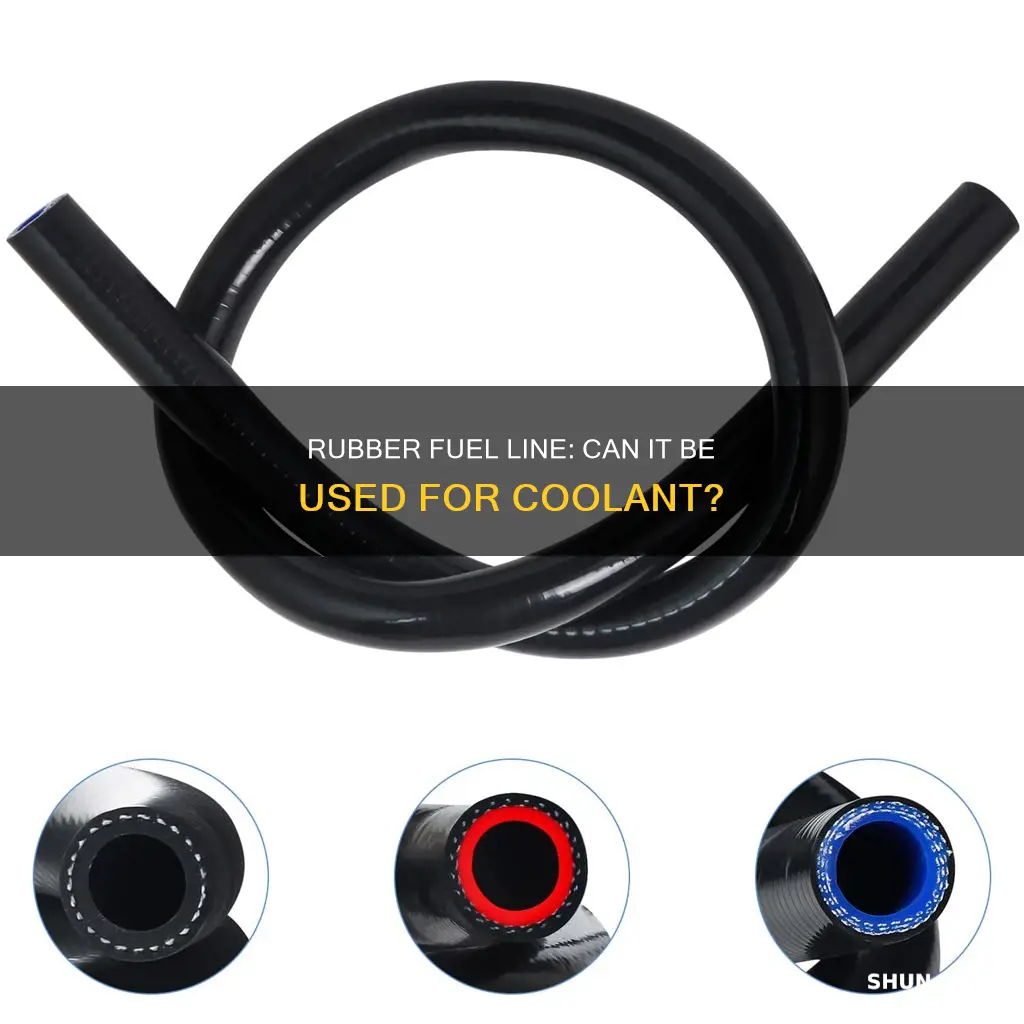
When it comes to vehicle maintenance, understanding the compatibility of different materials is crucial. One common question that arises is whether rubber fuel lines can be used for coolant. This inquiry delves into the feasibility and potential implications of utilizing rubber fuel lines for coolant systems, considering factors such as material properties, temperature resistance, and system compatibility. By exploring these aspects, we can determine if rubber fuel lines are a suitable choice for coolant applications, ensuring optimal performance and longevity of the vehicle's cooling system.
Characteristics | Values |
---|---|
Compatibility | Rubber fuel lines are generally not compatible with coolant due to the risk of degradation and potential leaks. Coolant contains chemicals that can break down the rubber over time. |
Flexibility | While rubber fuel lines offer flexibility, this property can be a disadvantage when used for coolant as it may lead to leaks or damage over time. |
Temperature Resistance | Rubber fuel lines may not withstand the high temperatures coolant can reach, leading to potential failure and leaks. |
Chemical Resistance | Coolant contains various chemicals that can cause the rubber to degrade, leading to cracks and leaks. |
Longevity | Using rubber fuel lines for coolant may result in a shorter lifespan due to the corrosive effects of the coolant. |
Cost | Rubber fuel lines are often more affordable, but the potential for issues and shorter lifespan may offset this advantage. |
Availability | These lines are widely available and easy to source, making them a convenient option for some applications. |
What You'll Learn
- Material Compatibility: Rubber fuel lines can withstand coolant temperatures and chemicals
- Flexibility: Rubber lines offer flexibility, crucial for engine movement and vibrations
- Durability: Rubber fuel lines are resistant to coolant-related wear and tear
- Installation: Proper installation ensures a tight seal and prevents leaks
- Safety: Using the right material prevents engine damage and potential hazards
Material Compatibility: Rubber fuel lines can withstand coolant temperatures and chemicals
When considering the use of rubber fuel lines for coolant, it's crucial to evaluate their material compatibility and performance in various conditions. Rubber is a versatile material known for its flexibility and durability, making it a popular choice for fuel lines in vehicles. However, its suitability for coolant applications requires careful examination.
Coolant, also known as antifreeze, is designed to regulate engine temperature and prevent freezing in cold climates. It contains various chemicals, including ethylene glycol, which can be corrosive to certain materials. Rubber, being a natural polymer, has inherent chemical resistance, which makes it a promising candidate for coolant-carrying applications. The choice of rubber type is critical here. Natural rubber, for instance, has excellent resistance to ethylene glycol, ensuring that the coolant's chemicals do not degrade the material over time. This compatibility is essential to maintain the integrity of the fuel lines and prevent leaks or failures.
The temperature range of coolant is another critical factor. Coolant temperatures can vary significantly, from sub-freezing cold to high-temperature operation. Rubber fuel lines must be able to withstand these temperature extremes without becoming brittle or losing their shape. Synthetic rubbers, such as neoprene or EPDM (ethylene propylene diene monomer), offer improved temperature resistance compared to natural rubber. These synthetic rubbers can handle the wide temperature fluctuations associated with coolant systems, ensuring the fuel lines remain flexible and intact.
In addition to temperature compatibility, the chemical composition of the coolant is vital. Coolants often contain additives and inhibitors to enhance their protective properties. While these chemicals are designed to protect the engine, they can still interact with certain materials. Rubber fuel lines should be able to resist the corrosive effects of these additives, ensuring long-term reliability. Testing and selecting rubber compounds specifically formulated for coolant applications is essential to guarantee the material's compatibility and performance.
In summary, rubber fuel lines can be a viable option for coolant applications when considering material compatibility. Natural rubber's inherent resistance to ethylene glycol and synthetic rubbers' improved temperature stability make them suitable choices. However, it is crucial to select the appropriate rubber type and ensure it has been tested and approved for coolant use to guarantee the system's longevity and performance. Proper material selection and installation will contribute to a reliable and efficient coolant system.
Braided Fuel Line Protection: Sealing the Deal
You may want to see also
Flexibility: Rubber lines offer flexibility, crucial for engine movement and vibrations
The use of rubber fuel lines for coolant is an innovative approach that can offer several advantages, particularly in terms of flexibility. This is a critical aspect of engine design and maintenance, as engines are inherently dynamic and prone to vibrations. Rubber lines provide a much-needed level of flexibility, allowing the engine to move and shift without causing damage to the components.
In an engine, various parts are in constant motion, and the coolant system is no exception. Coolant lines, which carry the liquid through the engine, need to accommodate these movements without compromising the integrity of the system. Rubber fuel lines, with their inherent elasticity, can effectively bridge this gap. They can stretch and contract as the engine operates, ensuring a consistent and secure connection between the coolant reservoir and the engine block. This flexibility is especially important in high-performance engines or vehicles with advanced suspension systems, where engine movement can be more pronounced.
The flexibility of rubber lines is crucial in preventing damage to the engine over time. Without this flexibility, coolant lines could become rigid and brittle, leading to potential cracks or even ruptures. These issues can result in coolant leaks, which, in turn, can cause engine overheating and potential engine failure. By using rubber fuel lines, you create a more durable and reliable coolant system, ensuring that the engine remains cool and efficient even under demanding conditions.
Furthermore, the flexibility of rubber lines contributes to the overall longevity of the engine. The constant vibrations and movements of the engine can cause traditional coolant lines made of other materials to wear out faster. Rubber, with its ability to absorb and distribute vibrations, helps reduce the stress on the engine's components, leading to a longer-lasting and more reliable engine performance.
In summary, the flexibility of rubber fuel lines is a key factor in their suitability for coolant systems. This flexibility allows the engine to move freely, accommodates vibrations, and ensures the long-term durability of the engine. By incorporating rubber lines, vehicle owners can enhance the performance and reliability of their engines, especially in applications where engine movement is a significant consideration.
1988 F150 Fuel Line Sizes: A Comprehensive Guide
You may want to see also
Durability: Rubber fuel lines are resistant to coolant-related wear and tear
When considering the use of rubber fuel lines for coolant, it's important to understand the durability aspect, specifically how rubber fuel lines can withstand the rigors of coolant-related wear and tear. Coolant, also known as antifreeze, plays a crucial role in maintaining the engine's temperature and preventing corrosion. However, it can also be aggressive and potentially damaging to certain materials, especially over time.
Rubber fuel lines are designed to be flexible and durable, making them an excellent choice for this application. The material is inherently resistant to the corrosive effects of coolant, which is a significant advantage. Coolant often contains additives that help prevent rust and corrosion, but it can still cause degradation in some materials, leading to cracks, leaks, and eventual failure. Rubber, with its natural elasticity and resistance to chemical degradation, ensures that the fuel lines remain intact and functional even when exposed to coolant.
The durability of rubber fuel lines is particularly important in high-temperature environments or when the engine operates under extreme conditions. Over time, coolant can cause the rubber to harden or become brittle, but the right type of rubber, often synthetic, can be formulated to resist such changes. This ensures that the fuel lines maintain their flexibility and structural integrity, even after prolonged exposure to coolant.
Furthermore, rubber fuel lines are less prone to cracking and leaking compared to other materials. The constant expansion and contraction of the engine, coupled with the temperature fluctuations, can put immense stress on the fuel lines. Rubber's ability to absorb and distribute this stress helps prevent cracks and leaks, ensuring a reliable fuel supply to the engine. This is especially critical in high-performance or racing applications where engine output is maximized, and any compromise in the fuel system could lead to catastrophic failure.
In summary, rubber fuel lines offer a robust and reliable solution for coolant-related applications. Their inherent durability and resistance to coolant-induced wear and tear make them an ideal choice for maintaining a consistent and safe fuel supply to the engine, even in the most demanding conditions. When selecting fuel lines, it is essential to choose the right type of rubber and ensure compatibility with the specific coolant used to maximize the benefits of this material's durability.
Optimizing Performance: Choosing the Right Fuel Line Size for Trans Lines
You may want to see also
Installation: Proper installation ensures a tight seal and prevents leaks
When using rubber fuel lines for coolant applications, proper installation is crucial to ensure a reliable and leak-free system. The process begins with selecting the appropriate size and type of fuel line that can withstand the temperature and pressure requirements of your engine. It's essential to choose a line with a diameter that matches the existing system or the desired flow rate.
Before installation, ensure that the engine is cool and that the coolant system is drained to prevent any spills. Start by locating the coolant reservoir and removing the old coolant line, being careful not to damage the surrounding components. Clean the mounting surfaces and ensure they are free from any debris or old coolant residue.
Now, it's time to install the new rubber fuel line. Begin by threading the line through the appropriate openings in the engine block or radiator. Ensure that the line is routed in a way that avoids sharp bends or kinks, as these can lead to premature failure. Use the recommended coolant line connectors or clamps to secure the line in place. Tighten the connectors or clamps firmly, but be careful not to overtighten, as this can cause damage to the line or surrounding components.
A crucial step in the installation process is to ensure a tight seal. Check that the connections are secure and that there are no gaps or spaces where coolant could leak. Apply a small amount of coolant-safe sealant or tape to any exposed areas of the line to provide an additional layer of protection against leaks. Once all connections are secure, refill the coolant system and check for any leaks.
Proper installation and regular maintenance will help ensure the longevity of your rubber fuel line used for coolant. Always refer to the manufacturer's guidelines and recommendations for specific instructions and compatibility. By following these detailed steps, you can create a robust and reliable coolant system, maximizing the performance and efficiency of your engine.
Fuel Line: Understanding the Difference Between ID and OD Measurements
You may want to see also
Safety: Using the right material prevents engine damage and potential hazards
When it comes to engine maintenance and repairs, choosing the right materials is crucial to ensure the longevity and safety of your vehicle. One common question that arises is whether rubber fuel lines can be used for coolant. While rubber fuel lines are designed for fuel transport and have their own set of advantages, they are not suitable for coolant due to several reasons.
Coolant, also known as antifreeze, plays a vital role in regulating engine temperature and preventing overheating. It contains additives that help protect the engine's internal components from corrosion and freezing. Rubber, being a flexible and durable material, is commonly used for fuel lines due to its ability to withstand high pressure and temperature variations. However, it is essential to understand that the properties of rubber make it incompatible with coolant. Rubber can absorb moisture over time, leading to swelling and potential leaks, which can result in engine damage. Additionally, the additives in coolant can cause rubber to degrade more rapidly, reducing its lifespan and compromising its structural integrity.
Using rubber fuel lines for coolant can lead to several hazards. Firstly, the absorbed moisture can cause the rubber to become brittle and crack, leading to coolant leaks. These leaks can result in engine overheating, loss of performance, and even potential engine failure. Moreover, the corrosive nature of coolant can accelerate the deterioration of the rubber, leading to a higher risk of leaks and engine damage. In some cases, the rubber may even disintegrate, causing debris to enter the engine and further exacerbating the issues.
To ensure the safety and proper functioning of your engine, it is crucial to use the correct materials for their intended purposes. In this case, using dedicated coolant lines made from materials like nylon or stainless steel is recommended. These materials are designed to withstand the corrosive nature of coolant and provide a reliable seal, preventing any potential hazards. By choosing the right materials, you can avoid costly repairs, maintain engine performance, and ensure a safer driving experience.
In summary, while rubber fuel lines are suitable for fuel transport, they should never be used for coolant. The potential risks and hazards associated with using rubber for coolant lines far outweigh any temporary convenience. Always refer to your vehicle's manual or consult with a professional mechanic to determine the appropriate materials for your engine's specific needs, ensuring optimal performance and safety.
Hayabusa Fuel Line Removal: A Step-by-Step Guide for 2003 Models
You may want to see also
Frequently asked questions
While rubber fuel lines are commonly used for fuel systems, they are not ideal for coolant applications. Coolant is typically more aggressive and can cause rubber to degrade over time, leading to potential leaks and reduced performance.
Using rubber fuel line for coolant can result in several issues. The coolant's heat and chemicals can accelerate the aging process of the rubber, causing it to become brittle and crack. This may lead to coolant leaks, engine overheating, and potential damage to the engine's components.
Yes, there are several materials that are more suitable for coolant lines. Braided stainless steel is a popular choice as it is durable, flexible, and resistant to coolant corrosion. Some manufacturers also offer specialized coolant lines made from materials like silicone or EPDM rubber, which are designed to withstand coolant temperatures and chemical exposure.
It is crucial to consult your vehicle's manual or seek professional advice to determine the recommended materials for coolant lines. Different engines may have specific requirements based on their design and operating conditions. Using the correct material ensures optimal performance and prevents potential engine damage.
Converting an existing rubber fuel line to a coolant line is not recommended. The original design and materials used for fuel lines may not be suitable for coolant, and the conversion could lead to premature failure and potential engine issues. It is best to replace the fuel line with a dedicated coolant line to ensure safety and reliability.