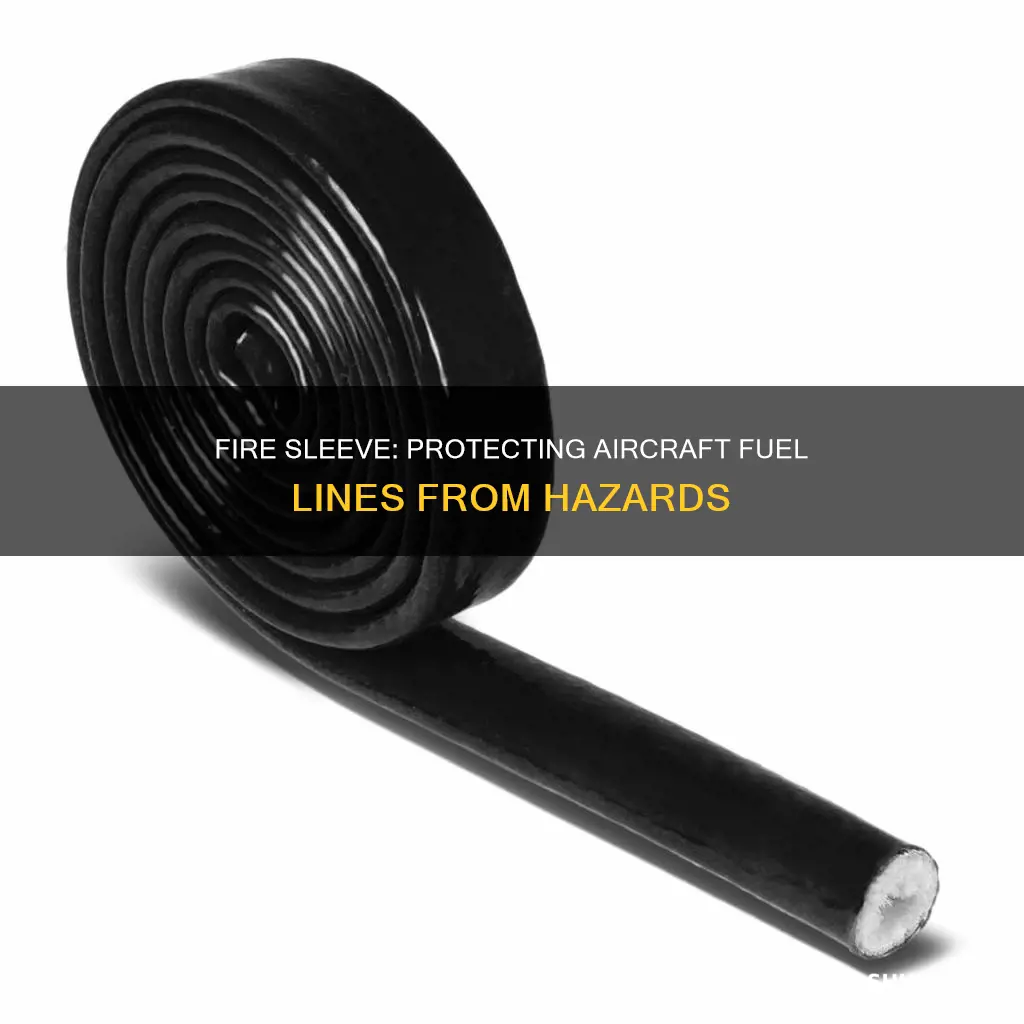
A fire sleeve is a crucial component in the safety and functionality of aircraft fuel lines. It serves as a protective barrier, safeguarding the fuel lines from potential heat sources and fire hazards. The primary reason for incorporating a fire sleeve is to prevent fuel leaks and ensure the overall safety of the aircraft. By encapsulating the fuel lines with a fire-resistant material, the sleeve acts as a protective shield, reducing the risk of fire damage and potential fuel leaks in case of an emergency. This design feature is essential for maintaining the integrity of the fuel system and ensuring the aircraft's safety during various flight conditions.
Characteristics | Values |
---|---|
Fire Protection | A fire sleeve is designed to provide an additional layer of insulation and protection against heat and flames. It helps prevent fuel lines from overheating and reduces the risk of fire damage in case of an accident or malfunction. |
Insulation | The sleeve acts as an insulator, maintaining the temperature of the fuel line and preventing rapid cooling or heating, which could lead to condensation and potential issues. |
Flexibility | It allows for some flexibility in the fuel line, accommodating movement during flight and providing a buffer against mechanical stress. |
Corrosion Resistance | Fire sleeves are often made from materials that resist corrosion, ensuring the fuel line's integrity over time, especially in harsh environments. |
Weight | The weight of the sleeve is minimal, ensuring it does not significantly impact the aircraft's performance or fuel efficiency. |
Compatibility | These sleeves are typically designed to fit various fuel line sizes and types, making them versatile for different aircraft models. |
Maintenance | Regular inspection and replacement of the fire sleeve are recommended to ensure ongoing protection, especially after any fuel system maintenance or repairs. |
What You'll Learn
- Fire Safety: Fuel lines with sleeves provide an extra layer of protection against fire hazards
- Material Choice: The sleeve is typically made of heat-resistant materials like Kevlar or Nomex
- Insulation: It acts as insulation to prevent fuel from overheating and causing damage
- Impact Resistance: Sleeve design offers protection against impacts and vibrations during flight
- Compliance: Aircraft fuel lines with sleeves meet industry standards and regulations for safety
Fire Safety: Fuel lines with sleeves provide an extra layer of protection against fire hazards
Fire safety is a critical aspect of aircraft maintenance and operation, and one crucial element is the use of fire sleeves on fuel lines. These sleeves are an essential component designed to safeguard aircraft fuel systems from potential fire risks. By implementing this protective measure, aviation professionals can significantly enhance the overall safety of their aircraft.
The primary purpose of a fire sleeve is to act as a barrier between the fuel line and potential heat sources or fire-prone areas. In the event of a fire or high-temperature incident, the sleeve material, often made of heat-resistant fabric or composite materials, can withstand extreme temperatures, preventing the fuel line from coming into direct contact with flames or intense heat. This simple yet effective design feature is vital, especially in high-risk environments where aircraft operate.
In the context of aviation, fuel lines are often exposed to various hazards, such as engine heat, exhaust gases, and even potential impact damage during takeoff and landing. A fire sleeve provides an additional layer of insulation, ensuring that the fuel lines remain protected even in the most challenging conditions. This extra protection is especially important given the highly flammable nature of aviation fuels.
The installation of fire sleeves on fuel lines is a standard practice in aircraft maintenance, requiring careful consideration and precision. Technicians must ensure that the sleeves are properly secured and aligned to maintain the structural integrity of the fuel system. This process involves careful routing of the sleeves to avoid any potential interference with other aircraft components, ensuring a seamless and safe integration.
By incorporating fire sleeves into aircraft fuel line design and maintenance, aviation authorities and maintenance teams can significantly reduce the risk of fire-related incidents. This simple yet effective safety measure contributes to the overall reliability and safety of aircraft operations, allowing pilots and passengers to travel with increased confidence.
Understanding Flaring: A Fuel Line Emergency
You may want to see also
Material Choice: The sleeve is typically made of heat-resistant materials like Kevlar or Nomex
The use of a fire sleeve on aircraft fuel lines is a critical safety measure, especially in the context of aviation, where the consequences of fuel line failures can be catastrophic. The primary purpose of this sleeve is to provide an additional layer of protection against the risk of fire, which is a significant concern in the aviation industry. When designing and implementing these sleeves, engineers and manufacturers carefully consider the choice of materials to ensure optimal performance and safety.
Heat-resistant materials are the cornerstone of these sleeves, and two prominent choices are Kevlar and Nomex. Both are renowned for their exceptional thermal properties, making them ideal for withstanding extreme temperatures that may occur during a fire event. Kevlar, a synthetic fiber known for its high strength-to-weight ratio, offers excellent heat resistance and can effectively dissipate the intense heat generated by a fire. It is also lightweight, ensuring that the sleeve does not add unnecessary weight to the aircraft's fuel system. Nomex, on the other hand, is a heat-resistant fabric that has been a staple in aviation safety for decades. It is known for its ability to retain its structural integrity even at extremely high temperatures, providing a robust barrier against fire.
The choice between Kevlar and Nomex often depends on specific application requirements. For instance, in high-temperature environments, Nomex might be preferred due to its superior heat tolerance. In contrast, Kevlar could be chosen for its lightweight nature, which is advantageous in aircraft design, where weight reduction is crucial for fuel efficiency and overall performance. Both materials are designed to withstand the harsh conditions of a fire, but their unique properties cater to different needs, ensuring that the fire sleeve is tailored to the specific demands of the aircraft's fuel system.
Incorporating these heat-resistant materials into the design of fuel lines is a proactive approach to aviation safety. It ensures that in the event of a fire, the fuel lines are less likely to fail, thereby reducing the risk of fuel leaks and potential ignition. This is particularly important in the context of aviation, where the consequences of a fire can be devastating, leading to aircraft damage, injuries, or even loss of life.
The use of Kevlar and Nomex in fire sleeves is a testament to the industry's commitment to safety and innovation. These materials, with their unique properties, play a vital role in safeguarding aircraft and their occupants, demonstrating the importance of meticulous material selection in critical aviation components.
Marine Fuel Line: Choosing the Right Option for Your Boat
You may want to see also
Insulation: It acts as insulation to prevent fuel from overheating and causing damage
Insulation plays a critical role in the design of aircraft fuel lines, particularly in preventing fuel from overheating and causing potential damage to the aircraft's systems. The primary purpose of a fire sleeve is to provide a protective layer around the fuel lines, ensuring the safe and efficient operation of the aircraft.
In the context of aviation, fuel lines are exposed to various environmental factors, including high temperatures, vibrations, and potential hazards. Overheating is a significant concern as it can lead to fuel degradation, reduced performance, and even catastrophic failures. The fire sleeve, often made from specialized materials like fire-resistant rubber or fabric, acts as a barrier between the fuel and the surrounding hot surfaces. This insulation layer helps regulate the temperature of the fuel, preventing it from reaching critical levels that could cause damage.
The design of the fire sleeve takes into account the specific requirements of the aircraft's fuel system. It is carefully constructed to fit snugly around the fuel lines, ensuring complete coverage and protection. This insulation is particularly important in areas where fuel lines are in close proximity to heat sources, such as engines, exhaust systems, or other hot components. By providing a thermal barrier, the fire sleeve minimizes the risk of fuel overheating and potential ignition, which could lead to fires or other hazardous situations.
Furthermore, the insulation properties of the fire sleeve contribute to the overall safety and reliability of the aircraft. It helps maintain the integrity of the fuel system, ensuring that the fuel remains stable and performs optimally. This is crucial for aircraft operations, especially during high-altitude flights or extreme weather conditions, where temperature variations can be extreme. Proper insulation prevents fuel expansion or contraction, which could lead to pressure buildup and potential damage to the fuel system.
In summary, the fire sleeve's insulation function is essential for safeguarding aircraft fuel lines. It effectively prevents fuel overheating, reduces the risk of damage, and ensures the overall safety and efficiency of the aircraft's fuel system. This simple yet critical component is a testament to the meticulous engineering and safety measures implemented in aviation design.
Optimizing Fuel Delivery: Choosing the Right Fuel Line Size for 5/16 Nipple Applications
You may want to see also
Impact Resistance: Sleeve design offers protection against impacts and vibrations during flight
The design of sleeves on aircraft fuel lines is a critical aspect of aviation safety, especially when considering the impact resistance required during flight operations. These sleeves are strategically placed to safeguard the fuel lines from potential damage caused by various factors, including impacts and vibrations. The primary purpose is to ensure the integrity of the fuel system, which is essential for the aircraft's performance and overall safety.
During flight, aircraft experience a multitude of dynamic forces, including turbulence, rapid acceleration, and deceleration. These forces can subject the fuel lines to significant stress, potentially leading to damage or failure. Impact resistance is a crucial feature of the sleeve design, as it provides a protective barrier that absorbs and dissipates the energy from impacts, thus preventing the fuel lines from sustaining damage. The sleeves are typically made from durable materials that can withstand the extreme conditions encountered in the aviation environment.
The sleeve's structure is carefully engineered to offer optimal protection. It often consists of multiple layers, each serving a specific purpose. For instance, the outer layer might be made of a high-impact-resistant polymer, designed to absorb and redistribute the force of an impact. This layer acts as a buffer, preventing the fuel line from direct contact with any sharp or hard objects that might come into contact with the aircraft during flight. The inner layers could include cushioning materials to minimize the risk of damage to the fuel line itself.
Additionally, the sleeve's design takes into account the natural movement and flexibility of the fuel lines. It allows for a certain degree of movement while maintaining its protective function. This flexibility is crucial to accommodate the various stresses and strains the fuel lines undergo during flight, ensuring that the sleeve does not restrict the normal operation of the fuel system.
In summary, the impact resistance provided by sleeve design is a vital safety feature in aircraft fuel lines. It safeguards the fuel system from potential damage caused by impacts and vibrations, contributing to the overall reliability and safety of the aircraft during its operational life. This design consideration is a testament to the meticulous engineering that goes into ensuring the well-being of both passengers and crew.
Optimizing Performance: Choosing the Right Fuel Line for Your 50 HP Outboard
You may want to see also
Compliance: Aircraft fuel lines with sleeves meet industry standards and regulations for safety
The inclusion of a fire sleeve on aircraft fuel lines is a critical safety measure that aligns with industry standards and regulations. This design feature is essential to mitigate the risks associated with fuel line failures, which can lead to hazardous situations, especially in the context of aviation. The primary purpose of the fire sleeve is to provide an additional layer of protection against potential fires that could arise from fuel line damage or leaks.
In the event of a fuel line breach, the fire sleeve acts as a barrier, containing the fuel and preventing it from coming into contact with ignition sources, such as hot engine components or electrical systems. This is particularly important in aircraft, where the consequences of a fire can be catastrophic. By encapsulating the fuel line with a protective sleeve, manufacturers ensure that any potential fire is localized and contained, reducing the risk of widespread damage and enhancing passenger and crew safety.
Compliance with industry standards is a key aspect of aircraft design and maintenance. Regulatory bodies, such as the Federal Aviation Administration (FAA) and the European Union Aviation Safety Agency (EASA), have established guidelines and requirements for fuel system design, including the use of fire sleeves. These standards are designed to ensure that aircraft fuel systems are robust and reliable, capable of withstanding various operating conditions and potential failures.
The fire sleeve's design and installation must adhere to these regulations, ensuring that it provides an effective barrier without compromising the fuel line's functionality. This includes considerations for material compatibility, thickness, and flexibility to accommodate the dynamic nature of aircraft operations. By meeting these compliance standards, aircraft manufacturers demonstrate their commitment to safety and adhere to the necessary legal and regulatory frameworks.
Furthermore, the use of fire sleeves in aircraft fuel lines is a proactive approach to safety, addressing potential hazards before they become critical issues. This methodical approach to design and compliance ensures that aircraft fuel systems are among the most rigorously tested and regulated components, contributing to the overall safety and reliability of aviation operations.
Toro Trimmer Fuel Line Sizing: A Comprehensive Guide
You may want to see also
Frequently asked questions
A fire sleeve is a protective covering designed to safeguard aircraft fuel lines from potential heat sources and fire hazards. It is typically made of a heat-resistant material and is installed around the fuel line to ensure the fuel remains safe and protected during various flight conditions.
The primary role of a fire sleeve is to provide an extra layer of insulation and protection against fire. In the event of a fire or high-temperature exposure, the fire sleeve acts as a barrier, preventing direct contact between the fuel line and the heat source. This reduces the risk of fuel line damage, fuel leakage, and potential fire outbreaks, thus improving overall aircraft safety.
Yes, fire sleeves come in various designs and materials to suit different aircraft and fuel line requirements. Some common types include metal fire sleeves, which offer excellent heat resistance, and flexible fire sleeves made from materials like silicone or rubber, providing flexibility and ease of installation. The choice of fire sleeve depends on factors such as fuel type, aircraft design, and specific safety regulations.