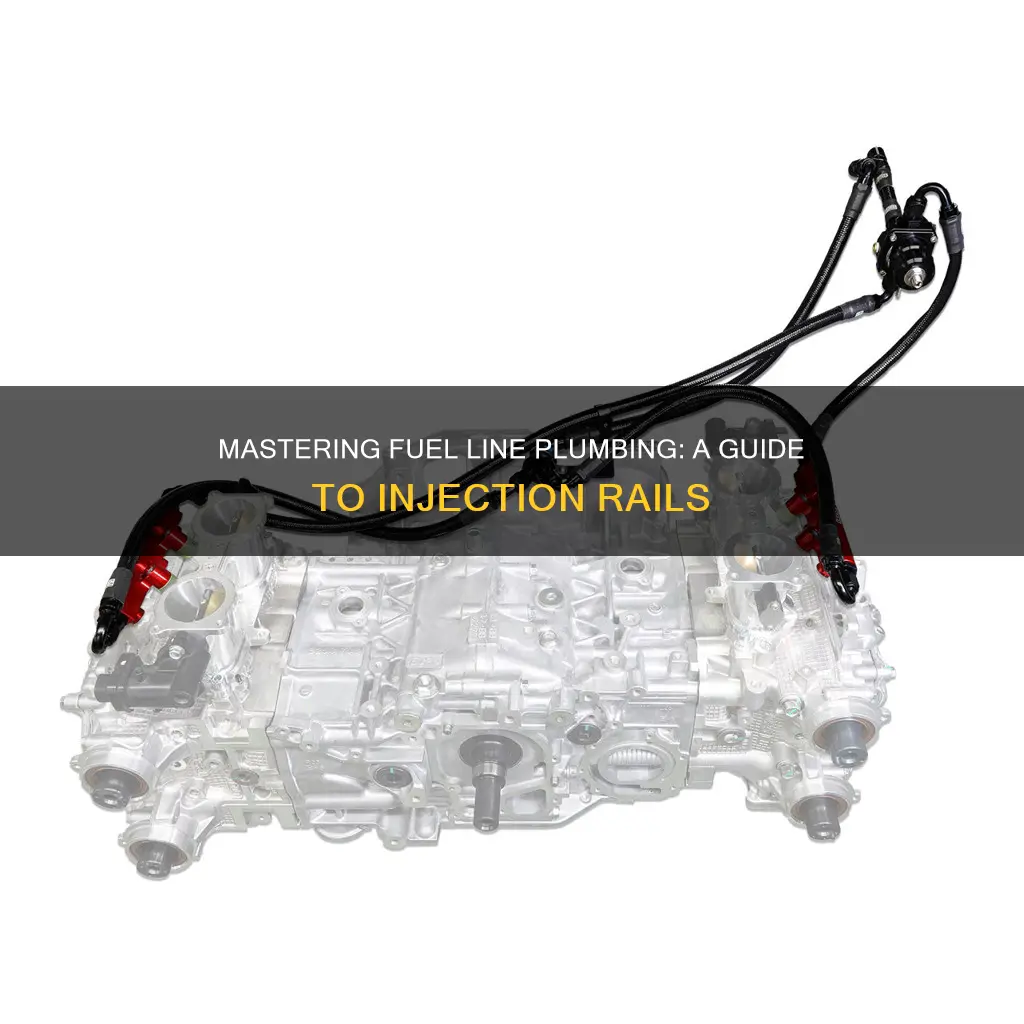
Plumbing fuel lines for injection rails is a crucial step in the process of setting up a fuel injection system for your vehicle. This process involves carefully routing the fuel lines from the fuel pump to the engine's injection rails, ensuring a precise and efficient fuel supply to the engine's cylinders. It requires attention to detail, understanding of engine mechanics, and adherence to specific guidelines to ensure optimal performance and reliability. This guide will provide a step-by-step approach to help you successfully plumb the fuel lines, covering important considerations such as material selection, routing techniques, and installation best practices.
What You'll Learn
- Fuel Line Material Selection: Choose appropriate materials for fuel lines, considering durability and compatibility with fuel type
- Routing and Support: Route fuel lines away from heat sources and secure them to prevent damage and ensure proper flow
- Fittings and Connections: Use high-quality fittings and ensure tight, leak-free connections for reliable fuel delivery
- Pressure Testing: Conduct thorough pressure testing to identify leaks and ensure the system's integrity
- Safety and Regulations: Adhere to local regulations and safety standards for fuel line installation and maintenance
Fuel Line Material Selection: Choose appropriate materials for fuel lines, considering durability and compatibility with fuel type
When it comes to plumbing fuel lines for injection rails, the choice of material is critical to ensure optimal performance and longevity. The fuel lines must be able to withstand the corrosive nature of fuel, as well as the high temperatures and pressures involved in the fuel injection process. Here's a guide to selecting the right materials:
Durability and Flexibility: Fuel lines should be made from materials that offer excellent durability and flexibility. Rubber or synthetic rubber compounds are commonly used due to their ability to withstand fuel's corrosive properties. Look for materials with high tear resistance and flexibility to accommodate the various angles and bends in the fuel line routing. Silicone-based materials are also a good choice as they can handle extreme temperatures and provide a durable barrier against fuel degradation.
Compatibility with Fuel Type: Different types of fuel require specific considerations. For gasoline applications, rubber or synthetic rubber-based fuel lines are often used. These materials are compatible with gasoline and can withstand the volatility of this fuel type. For diesel engines, fuel lines made from materials like high-density polyethylene (HDPE) or cross-linked polyethylene (PE-X) are preferred. These materials offer excellent chemical resistance and can handle the higher pressures and temperatures associated with diesel fuel. Always ensure that the chosen material is compatible with the specific fuel type to prevent degradation and potential engine issues.
Resistance to Fuel Abrasion: Fuel lines should also be resistant to abrasion, especially in high-wear areas like under the vehicle or near moving parts. Consider materials with reinforced construction, such as braided rubber or synthetic rubber with a woven fabric core. This reinforcement provides added strength and durability, ensuring the fuel lines can withstand the physical stresses of the engine environment.
Temperature and Pressure Considerations: The operating temperature and pressure of the fuel system should be taken into account. For high-temperature applications, materials like silicone or HDPE can handle the extreme conditions. If the fuel system operates under high pressure, materials with excellent pressure-bearing capabilities, such as PE-X or specialized fuel line compounds, are recommended.
Installation and Maintenance: Choose materials that are easy to install and maintain. Some materials may require specific tools or techniques for bending and joining. Additionally, consider the availability of replacement parts and the overall maintenance requirements to ensure long-term reliability.
By carefully selecting the appropriate fuel line materials, you can ensure a reliable and efficient fuel injection system. Remember to consult manufacturer guidelines and consider the specific requirements of your engine to make the best material choices for your plumbing project.
Reviving Your Ride: A Guide to Softening Hardened Fuel Lines
You may want to see also
Routing and Support: Route fuel lines away from heat sources and secure them to prevent damage and ensure proper flow
When plumbing fuel lines for injection rails, proper routing and support are crucial to ensure optimal performance and longevity. The primary goal is to protect the fuel lines from potential heat sources and physical damage, which could lead to fuel leaks or reduced system efficiency. Here's a detailed guide on how to achieve this:
Routing Away from Heat Sources:
Start by identifying potential heat sources in your engine bay. These could include exhaust manifolds, engine blocks, transmission components, or even the intake manifold. Fuel lines should be routed as far away from these areas as possible. The ideal route should be along the top or sides of the engine bay, where temperatures are generally cooler. Avoid running fuel lines directly over hot surfaces or near components that generate significant heat. This practice helps prevent the fuel lines from overheating, which can lead to fuel degradation and potential blockages.
Using Heat Shielding Materials:
Consider using heat shielding materials to further protect the fuel lines. These materials, often made of metal or heat-resistant fabrics, can be wrapped around the fuel lines to act as a barrier against heat transfer. For example, you can use metal heat shields that are bolted or taped to the engine bay, creating a protective layer between the hot components and the fuel lines. This additional layer of protection ensures that the fuel lines remain at optimal temperatures, maintaining the quality of the fuel and the overall performance of the injection system.
Securing the Fuel Lines:
Proper securing of fuel lines is essential to prevent damage and maintain a consistent fuel flow. Use appropriate tie-downs or clips to secure the lines to the engine bay. These should be placed at regular intervals along the length of the fuel lines to ensure even tension and prevent kinking or bending. Avoid securing the lines too tightly, as this can restrict fuel flow and cause stress on the lines. Instead, aim for a secure yet flexible arrangement that allows for slight movement without causing damage.
Considering Flexibility and Accessibility:
While securing the fuel lines, also ensure that they have enough flexibility to accommodate engine movement without kinking. This is particularly important for older engines or those with more complex designs. Additionally, maintain accessibility for future maintenance. Allow enough clearance for tools and maintenance personnel to work around the fuel lines without causing accidental damage. Proper routing and securing should not compromise the ease of accessing critical components.
By following these routing and support practices, you can ensure that your fuel lines are well-protected, maintain optimal fuel flow, and contribute to the overall reliability of your injection rail system. Remember, proper plumbing is a critical aspect of engine performance and longevity.
Mastering the Art: Removing Diesel Fuel Lines from Transfer Pumps
You may want to see also
Fittings and Connections: Use high-quality fittings and ensure tight, leak-free connections for reliable fuel delivery
When plumbing fuel lines for injection rails, the quality of fittings and connections is paramount to ensure a reliable and efficient fuel delivery system. High-quality fittings are essential to maintain the integrity of the fuel system and prevent potential issues down the line. Here's a detailed guide on this crucial aspect:
Fitting Selection: Choose fittings specifically designed for fuel lines and compatible with the fuel type you are using. Common materials include stainless steel, brass, and aluminum, each offering different advantages. For instance, stainless steel provides excellent corrosion resistance, making it ideal for long-term fuel systems. Brass fittings are lightweight and easy to install, while aluminum offers good heat dissipation, which can be beneficial in high-performance applications. Ensure the fittings have a smooth interior surface to minimize fuel flow restriction and potential pressure drops.
Thread Quality: Pay close attention to the threads of the fittings. High-quality fittings will have precise, uniform threads that are easy to start and tighten. Threading should be free of any burrs or sharp edges to prevent damage to the fuel line. Consider using thread seal tape or pipe compound on the male threads to ensure a tight, leak-free connection. Properly sealed threads are critical to maintaining the system's integrity.
Connection Techniques: When connecting the fittings, employ the right techniques to ensure a secure bond. For compression fittings, ensure the fuel line is properly inserted and compressed evenly. Over-tightening can damage the fuel line, so use a torque wrench to achieve the recommended tightening force. For barbed fittings, insert the fuel line into the barb and ensure it is fully seated. Barbed fittings should be secured with a ferrule or crimp to prevent the line from pulling out. Always follow the manufacturer's instructions for each type of fitting.
Leak Testing: After making all connections, perform a thorough leak test to ensure there are no hidden issues. Fill the system with fuel and use a bubble trap or a leak detector to identify any potential leaks. Even a small leak can lead to fuel loss, reduced performance, and potential engine damage. Tighten connections further if necessary and retest until all connections are leak-free.
Regular Maintenance: Regularly inspect and maintain the fuel system's fittings and connections. Over time, fuel lines and fittings can degrade due to fuel quality, temperature fluctuations, and vibration. Check for signs of corrosion, cracks, or damage, especially at connection points. Replacing worn-out fittings and fuel lines proactively will ensure the system's longevity and reliability.
1966 Ford Mustang Fuel Line: A Comprehensive Guide
You may want to see also
Pressure Testing: Conduct thorough pressure testing to identify leaks and ensure the system's integrity
Pressure testing is a critical step in ensuring the integrity and reliability of fuel injection systems, especially when plumbing fuel lines for injection rails. This process involves applying pressure to the system to check for any leaks or weaknesses that could compromise the system's performance and safety. Here's a detailed guide on how to conduct thorough pressure testing:
Preparation: Before initiating the pressure test, ensure that the fuel injection system is properly prepared. This includes cleaning all components, such as fuel lines, rails, and injectors, to remove any contaminants or debris that might interfere with the test results. Inspect the system for any visible damage or corrosion, and make necessary repairs or replacements. It is crucial to have a clean and well-maintained system to ensure accurate testing.
Pressure Source and Gauge: Utilize a reliable pressure source, such as an air compressor or a dedicated fuel pressure tester, capable of generating the required test pressure. Connect a precision pressure gauge to the system, ensuring it is securely attached to the fuel lines or rails. The gauge should have an accurate reading capacity to measure the system's pressure effectively. Calibrate the gauge if necessary to ensure precise measurements.
Test Procedure: Start the pressure test by slowly increasing the pressure in the system using the pressure source. Monitor the pressure gauge reading and record the initial pressure value. Gradually increase the pressure to the specified test pressure, typically the system's operating pressure or a predetermined value. Maintain this pressure for a sufficient duration, usually several minutes, allowing the system to stabilize. During this time, closely observe the pressure gauge for any fluctuations or drops, which could indicate potential issues.
Leak Detection: While the pressure is maintained, inspect the system for any signs of leaks. Visually examine the fuel lines, rails, and connections for any visible moisture, condensation, or fuel accumulation. Use a soapy water solution to create a foam and apply it to the system's surfaces. Any bubbles forming on the surface indicate a leak. Additionally, listen for hissing or whistling sounds near connections or potential leak points. Document the location and nature of any leaks found.
Documentation and Analysis: Record all test parameters, including the initial pressure, test pressure, duration, and any observed leaks. Compare the test results with the system's specifications to ensure compliance. If leaks are detected, prioritize addressing them by repairing or replacing the affected components. Analyze the test data to identify any patterns or trends that might suggest underlying issues. This analysis can help in troubleshooting and improving the system's design or installation.
Safety Considerations: Pressure testing should always be conducted in a controlled environment, preferably in a well-ventilated area or outdoors. Ensure proper ventilation to prevent the inhalation of fuel vapors, which can be hazardous. Wear appropriate personal protective equipment, such as gloves and safety goggles, to protect against potential splashes or spills. Always follow safety guidelines and regulations when working with pressurized systems.
By following these steps, you can effectively conduct pressure testing to identify leaks and ensure the overall integrity of the fuel injection system. This process is essential for maintaining optimal performance and safety, especially when plumbing fuel lines for injection rails.
Unveiling the Mystery: How Air Sneaks into Diesel Fuel Lines
You may want to see also
Safety and Regulations: Adhere to local regulations and safety standards for fuel line installation and maintenance
When it comes to plumbing fuel lines for injection rails, safety and compliance with regulations are paramount. Fuel lines are a critical component of any vehicle's fuel system, and improper installation or maintenance can lead to dangerous consequences, including fuel leaks, fires, and even explosions. Therefore, it is essential to adhere to local regulations and safety standards throughout the entire process.
Local regulations and standards often dictate the materials, design, and installation practices for fuel lines. These guidelines are in place to ensure that fuel systems are designed and installed with a high level of safety in mind. For instance, certain areas may require the use of specific types of fuel lines that are resistant to heat, chemicals, and pressure, while others might mandate the use of specific connectors or fittings. It is crucial to consult the relevant codes and standards for your region and ensure that your fuel line plumbing meets or exceeds these requirements.
One of the key safety considerations is the proper routing of fuel lines. The lines should be installed in a way that avoids sharp bends, tight spaces, or areas where they could be damaged by vibrations or impact. Proper routing helps prevent fuel leaks and ensures that the lines remain intact over time. Additionally, fuel lines should be secured to the vehicle's body or frame using appropriate clips or brackets to prevent movement and potential damage.
Regular maintenance is also vital to ensure the safety and longevity of fuel lines. Over time, fuel lines can degrade due to factors such as fuel quality, temperature changes, and mechanical stress. Inspecting the fuel lines periodically for signs of wear, cracks, or corrosion is essential. Any damaged or compromised lines should be replaced immediately to prevent potential hazards.
Furthermore, it is important to stay updated with the latest regulations and industry best practices. Fuel line installation and maintenance standards may evolve, and keeping up with these changes is crucial. Attending training sessions or workshops related to fuel system maintenance can provide valuable insights and ensure that you are following the most current and safe procedures. By adhering to local regulations and safety standards, you can ensure that your fuel line plumbing is reliable, efficient, and safe.
Fixing a Fuel Line Leak: A Step-by-Step Guide for Push Mowers
You may want to see also
Frequently asked questions
Plumbing fuel lines for fuel injection rails is a crucial step in the process of setting up a fuel-injected engine. It involves connecting the fuel pump, fuel rails, and injectors to ensure a precise and controlled fuel supply for optimal engine performance.
The fuel line size should be chosen based on the engine's power output and fuel requirements. Generally, larger engines with higher displacement and power output will require larger-diameter fuel lines to handle the increased fuel flow. It's essential to consult the engine manufacturer's guidelines or seek professional advice to select the appropriate size.
No, it's crucial to use the correct fuel line material to ensure compatibility and longevity. Common materials include steel, aluminum, or specialized fuel-resistant hoses. The choice depends on factors like temperature, pressure, and the specific fuel type used. Always refer to the manufacturer's recommendations or industry standards for the best material selection.
Achieving a secure and leak-free connection is vital. Start by cleaning the surfaces of the fuel lines and fittings. Use the appropriate torque to tighten connections, ensuring they are neither overtightened nor under-tightened. Inspect for any signs of damage or wear, and consider using fuel-resistant tape or sealant for added security.
Yes, having the right tools is essential. You'll need fuel line cutters, crimping tools for fuel line connectors, a fuel line cleaner, and possibly a fuel pressure gauge for testing. Additionally, safety equipment like gloves and safety goggles is recommended. It's always a good idea to have a well-equipped workshop or consult a professional for the necessary tools and guidance.