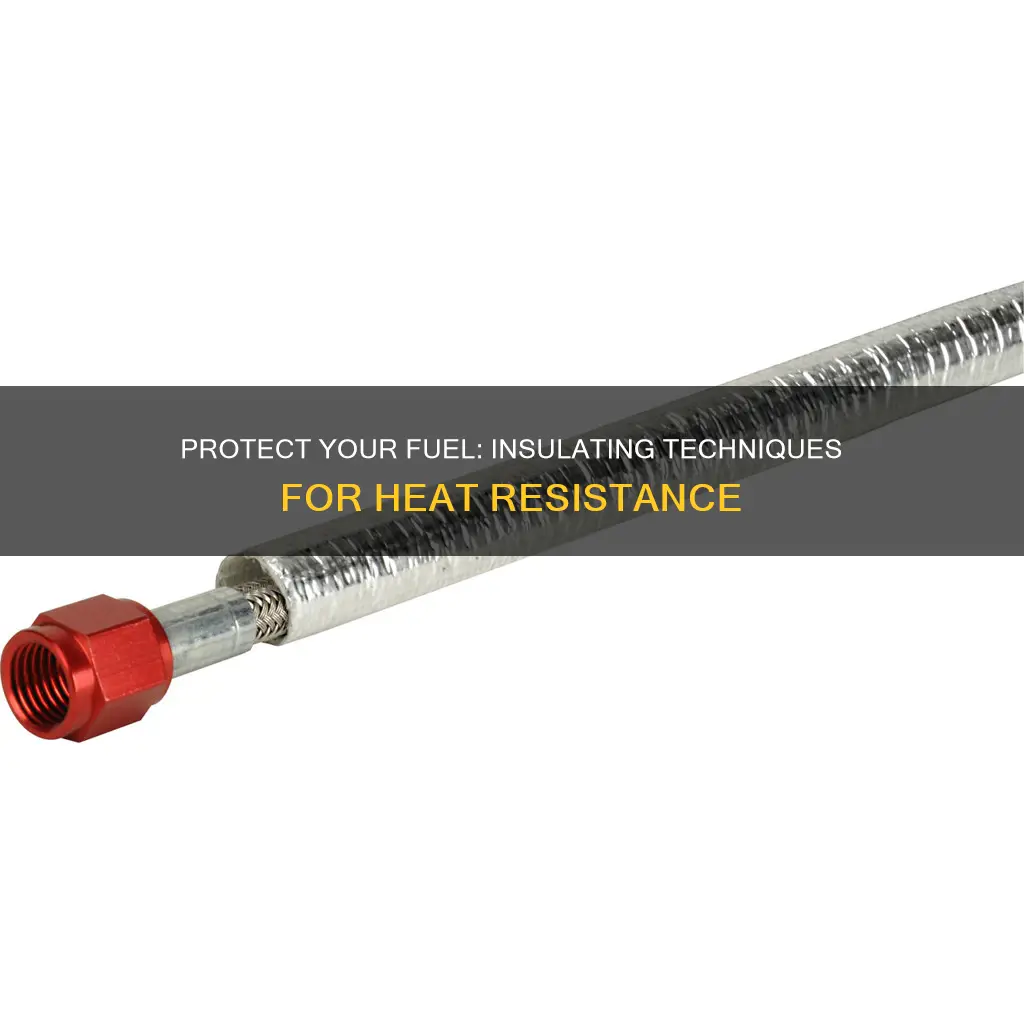
Insulating fuel lines from heat is a crucial step in maintaining the performance and longevity of any vehicle's fuel system. This process involves using specialized materials to protect the fuel lines from excessive temperatures, which can cause damage over time. By implementing proper insulation techniques, you can ensure that the fuel remains stable and the engine operates efficiently, leading to improved fuel economy and reduced emissions. This guide will explore various methods and materials to effectively insulate fuel lines, providing a comprehensive approach to safeguarding your vehicle's fuel system.
What You'll Learn
- Materials: Choose materials like foam, rubber, or plastic for insulation
- Routing: Route fuel lines away from hot surfaces and underfloor
- Cladding: Use protective cladding to shield fuel lines from direct heat
- Insulated Hoses: Opt for insulated hoses with built-in insulation
- Heat Shield: Install a heat shield to protect fuel lines from radiant heat
Materials: Choose materials like foam, rubber, or plastic for insulation
Insulating fuel lines from heat is a crucial step in maintaining the performance and longevity of your vehicle's fuel system. The primary goal is to prevent the fuel from overheating, which can lead to reduced fuel efficiency, engine misfires, and even potential engine damage. One of the most effective methods to achieve this is by using appropriate insulation materials.
When it comes to choosing the right materials for insulation, foam, rubber, and plastic are the most commonly used options. Each of these materials offers unique advantages and is suited to different types of fuel lines and environmental conditions.
Foam Insulation:
Foam insulation is a popular choice due to its lightweight and flexible nature. It is available in various forms, including open-cell and closed-cell foam. Open-cell foam is more breathable and allows for some air circulation, which can be beneficial in certain applications. However, it may not provide the same level of protection against heat as closed-cell foam. Closed-cell foam, on the other hand, is denser and offers excellent thermal insulation, making it ideal for high-temperature environments. This type of foam is often used in fuel lines that are exposed to direct sunlight or high-temperature exhaust systems.
Rubber Insulation:
Rubber is another effective material for fuel line insulation. It is naturally flexible and can conform to the shape of the fuel line, ensuring a snug fit. Natural rubber is known for its excellent thermal insulation properties and can withstand a wide range of temperatures. However, it may degrade over time due to exposure to sunlight and oxygen, leading to a loss of flexibility. To combat this, some manufacturers use compounded rubber that includes stabilizers to enhance its durability. This type of rubber insulation is commonly used in fuel lines that are not exposed to extreme temperatures.
Plastic Insulation:
Plastic insulation is lightweight and offers good thermal resistance. It is often used in fuel lines that are not subjected to high temperatures. Plastic insulation is available in various forms, including rigid and flexible varieties. Rigid plastic insulation provides a more rigid barrier against heat, making it suitable for fuel lines that need to maintain their shape. Flexible plastic insulation, such as plastic tape or sleeves, is easy to apply and can conform to the fuel line's shape, ensuring a secure fit. This type of insulation is commonly used in fuel lines that are routed through engine compartments or under the vehicle's body.
When selecting insulation materials, consider the specific requirements of your fuel lines, including the operating temperature, exposure to sunlight, and the overall length of the fuel line. Additionally, ensure that the chosen materials are compatible with the fuel type and do not pose any health or environmental risks. Proper insulation will not only protect your fuel lines but also contribute to a more efficient and reliable vehicle performance.
Fixing a Fuel Line Collar Leak: A Step-by-Step Guide
You may want to see also
Routing: Route fuel lines away from hot surfaces and underfloor
When it comes to insulating fuel lines from heat, proper routing is a critical aspect of the process. The goal is to ensure that the fuel lines are not exposed to excessive temperatures, which can lead to degradation of the fuel and potential safety hazards. One of the key principles is to route the fuel lines away from hot surfaces and underfloor areas.
To achieve this, start by identifying the hot spots in your vehicle's engine bay or compartment. These are typically areas where components like the exhaust manifold, catalytic converter, or engine block are located. These components generate a significant amount of heat, and it's essential to keep the fuel lines at a safe distance. Begin by carefully planning the path of the fuel lines, ensuring they are not directly adjacent to these hot surfaces.
The next step is to physically separate the fuel lines from the heat sources. You can achieve this by using heat shields or protective sleeves. Heat shields are metal or ceramic barriers that can be attached to the fuel lines and positioned between the lines and the hot surfaces. These shields act as a barrier, absorbing and deflecting heat away from the fuel lines. Alternatively, you can use flexible heat-resistant sleeves that can be slipped over the fuel lines, providing insulation and protection.
When routing the fuel lines under the vehicle, it's crucial to avoid direct contact with the floor. The underfloor area can be particularly challenging due to limited space and potential obstacles. Consider raising the fuel lines slightly above the floor or using rubber or plastic insulation to create a buffer between the lines and the underfloor surface. This simple measure can significantly reduce the risk of heat transfer to the fuel lines.
Additionally, ensure that the fuel lines are not pinched or kinked, as this can restrict fuel flow and potentially cause damage. Allow sufficient space for the lines to move and flex, especially in areas where the vehicle may experience vibrations or movement. Proper routing and insulation will not only protect the fuel lines but also contribute to the overall reliability and longevity of your vehicle's fuel system.
Fuel Line Sizing for Older Mercury Outboards: A Guide
You may want to see also
Cladding: Use protective cladding to shield fuel lines from direct heat
Protecting fuel lines from heat is crucial to ensure the efficient and safe operation of any fuel-powered system. One effective method to achieve this is by utilizing protective cladding, a simple yet powerful technique to safeguard these vital components. Cladding involves wrapping or applying a protective layer around the fuel lines, creating a barrier between the fuel and the heat source. This method is particularly useful in applications where fuel lines are exposed to high temperatures, such as in engines, industrial machinery, or even in outdoor environments.
The primary benefit of cladding is its ability to insulate the fuel lines, preventing direct contact with heat sources. This insulation is essential as it reduces the risk of fuel line damage, which can lead to costly repairs or system failures. By using materials with good thermal resistance, such as metal, plastic, or specialized thermal insulation, you create a robust shield around the fuel lines. This protective layer acts as a barrier, dissipating heat away from the fuel lines and maintaining optimal operating temperatures.
When implementing cladding, it is important to consider the specific requirements of the fuel line and the surrounding environment. The cladding material should be chosen based on its ability to withstand the expected temperature range and its compatibility with the fuel being used. For instance, in high-temperature industrial settings, metal cladding might be preferred for its durability and heat resistance. In contrast, for applications where flexibility is key, such as in automotive systems, plastic or rubber cladding could be more suitable.
The process of cladding involves carefully wrapping the fuel lines with the chosen material, ensuring complete coverage and a secure fit. This may require specialized tools or techniques, especially for fuel lines in hard-to-reach areas. Proper installation is critical to the success of this method, as it ensures the fuel lines are adequately protected from heat-related damage. Additionally, regular inspections and maintenance are recommended to check for any signs of wear or damage to the cladding, allowing for prompt repairs or replacements.
In summary, cladding is a practical and effective solution for insulating fuel lines from heat. By employing protective cladding, you create a robust barrier that shields the fuel lines, ensuring their longevity and optimal performance. This method is a valuable addition to any fuel management strategy, providing an extra layer of protection against the detrimental effects of heat. With careful consideration of material selection and proper installation, cladding can significantly contribute to the overall reliability and efficiency of fuel-powered systems.
Understanding Fuel Line Capacity: Gallons and More
You may want to see also
Insulated Hoses: Opt for insulated hoses with built-in insulation
Insulated hoses are an excellent solution for protecting fuel lines from heat damage, especially in high-temperature environments or applications where heat sources are nearby. These hoses are designed with an integrated insulation layer, providing a robust defense against extreme temperatures and potential heat sources. When selecting insulated hoses, it's crucial to consider the specific requirements of your fuel line setup.
The insulation material used in these hoses is typically a high-performance, heat-resistant foam or rubber compound. This insulation acts as a barrier, preventing heat from directly affecting the fuel line. It is engineered to withstand high temperatures, ensuring that the fuel remains stable and safe even in challenging conditions. Insulated hoses are particularly useful in automotive applications, such as in engines or under the hood, where fuel lines are susceptible to heat from nearby components.
One of the key advantages of insulated hoses is their ability to maintain the integrity of the fuel line over time. Without insulation, fuel lines can degrade due to heat exposure, leading to potential leaks or fuel contamination. Insulated hoses provide a protective layer, ensuring that the fuel remains contained and secure, even when exposed to high temperatures. This is especially important in industrial settings or during outdoor operations where temperature fluctuations are common.
When choosing insulated hoses, it's essential to select the right size and type for your specific application. Hoses come in various diameters and lengths to accommodate different fuel line configurations. Ensure that the hose's insulation is compatible with the fuel type and temperature range you are working with. Properly insulated hoses will not only protect the fuel line but also contribute to overall system efficiency and longevity.
In summary, insulated hoses with built-in insulation are a practical and effective way to safeguard fuel lines from heat-related damage. They offer a reliable solution for various industries and applications, ensuring that fuel remains safe and secure even in challenging environmental conditions. By investing in high-quality insulated hoses, you can minimize the risk of fuel-related issues and maintain optimal performance in your equipment or vehicles.
Fuel Line Routing: A Step-by-Step Guide to Carb Installation
You may want to see also
Heat Shield: Install a heat shield to protect fuel lines from radiant heat
Insulating fuel lines from heat is crucial to prevent fuel degradation, ensure optimal engine performance, and maintain the integrity of your vehicle's fuel system. One effective method to achieve this is by installing a heat shield, a protective barrier designed to deflect radiant heat away from the fuel lines. Here's a step-by-step guide on how to install a heat shield for this purpose:
Step 1: Choose the Right Heat Shield
Start by selecting a heat shield that is compatible with your vehicle's fuel lines. Consider the size and shape of the fuel lines, as well as the heat source they need to protect against. Heat shields are available in various materials, such as aluminum, stainless steel, or ceramic-coated metal, each offering different levels of heat resistance. Choose a material that can withstand the expected temperatures in your engine bay.
Step 2: Prepare the Work Area
Before installation, ensure you have a clean and well-lit workspace. Remove any debris or old insulation from the area where the heat shield will be placed. This step is essential to ensure a proper fit and prevent any obstructions.
Step 3: Locate the Fuel Lines
Identify the fuel lines that require protection. These lines typically run from the fuel tank to the engine and may be located beneath the vehicle or along the engine bay. Carefully inspect the fuel lines for any signs of damage or wear, as this will help you determine the most effective placement of the heat shield.
Step 4: Measure and Mark the Shield's Position
Place the heat shield in the position where it will cover the fuel lines. Use a measuring tape to ensure it fits snugly around the lines. Mark the points where the shield will be attached using a permanent marker or tape. This step is crucial to ensure accurate placement.
Step 5: Attach the Heat Shield
Using the marked positions, secure the heat shield in place. You can use mechanical fasteners like screws or bolts, ensuring they are tight enough to hold the shield firmly. Alternatively, some heat shields may use adhesive backing, which can be applied to the shield and then pressed onto the fuel lines. Follow the manufacturer's instructions for the chosen attachment method.
Step 6: Finish and Test
Once the heat shield is installed, ensure it is securely fastened and does not interfere with any other components. Test the fuel system to verify that the heat shield is effectively protecting the fuel lines. Check for any leaks or unusual noises, and ensure that the fuel pressure is stable.
By following these steps, you can effectively insulate your fuel lines from heat using a heat shield, contributing to the longevity and efficiency of your vehicle's fuel system. Remember to choose the right materials and ensure a proper fit for optimal results.
Mastering Fuel Line Antifreeze: A Comprehensive Guide to Winter Car Care
You may want to see also
Frequently asked questions
Insulating fuel lines is crucial to prevent fuel degradation and maintain the performance of the vehicle. Fuel lines can be susceptible to heat from various sources, such as the engine, exhaust, or surrounding environment. Insulation helps to protect the fuel from these high temperatures, ensuring the fuel remains stable and compatible with the engine components.
Heat can cause fuel to break down and degrade over time. This process, known as thermal degradation, can lead to the formation of varnish and sludge, which can clog fuel injectors, reduce engine performance, and even cause engine damage. Insulation acts as a barrier, minimizing the direct contact between the fuel and heat sources.
Insulation materials for fuel lines typically include rubber, foam, or specialized thermal barriers. Rubber is a common choice due to its flexibility and ability to conform to various fuel line shapes. Foam insulation provides a lightweight and effective barrier, while thermal barriers, often made of metal or composite materials, offer superior heat resistance.
It is not recommended to use regular insulation materials like fiberglass or mineral wool for fuel lines. These materials may not provide adequate protection against heat and can be flammable. Specialized fuel line insulation is designed to withstand the specific challenges of fuel systems, ensuring safety and performance.
Insulating fuel lines involves a few steps. First, ensure the fuel lines are clean and free of any debris. Then, cut the insulation material to fit the length of the fuel line. Wrap the insulation around the line, ensuring it is secure and smooth. Consider using adhesive or tape to hold the insulation in place. Regularly inspect and replace the insulation to maintain its effectiveness.