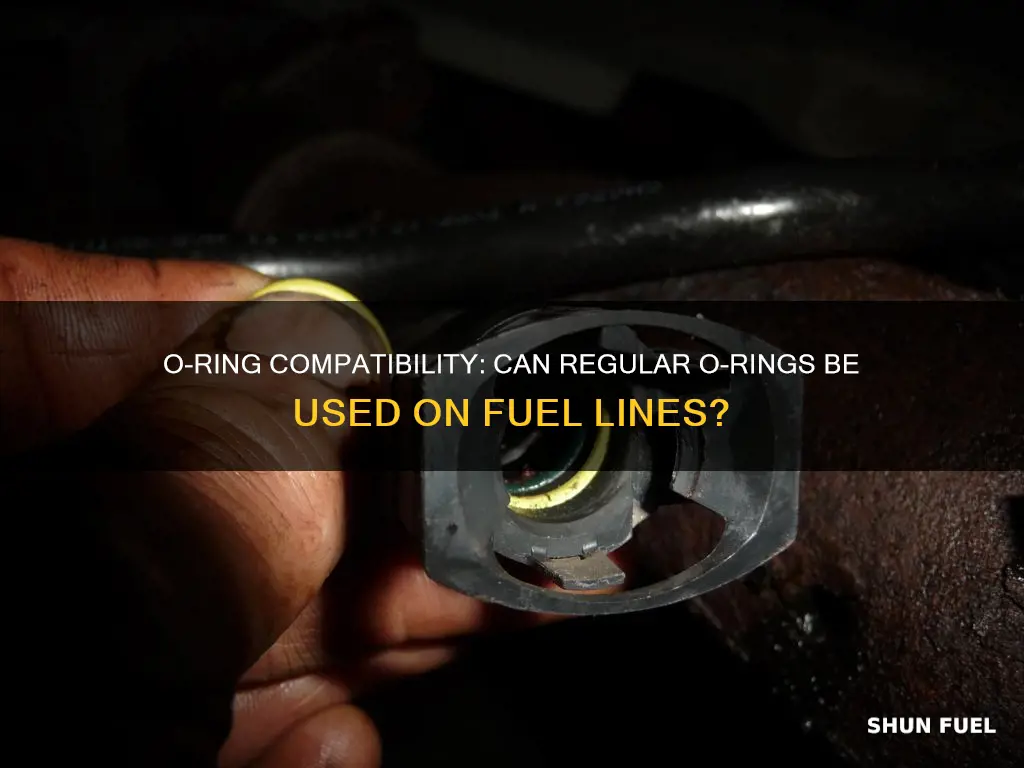
When it comes to fuel lines, choosing the right components is crucial for safety and performance. One common question that arises is whether regular O-rings can be used for fuel lines. This paragraph aims to shed light on this topic, providing insights into the suitability of standard O-rings for fuel line applications and exploring the factors that determine their effectiveness.
Characteristics | Values |
---|---|
Compatibility | Regular O-rings are not typically compatible with fuel lines due to the corrosive nature of fuel. |
Durability | O-rings designed for fuel lines are more durable and resistant to fuel degradation. |
Material | Special fuel-resistant materials like nitrile or EPDM are used for fuel line O-rings. |
Temperature Range | Fuel line O-rings can withstand a wider temperature range, including extreme temperatures. |
Chemical Resistance | They offer excellent resistance to fuel chemicals, unlike regular O-rings. |
Application | Specifically designed for fuel systems, ensuring a secure and leak-free connection. |
Cost | May be more expensive than regular O-rings due to specialized materials and design. |
Availability | Can be sourced from automotive or industrial suppliers, often in kits for fuel lines. |
Installation | Requires precise installation to ensure a tight seal and prevent leaks. |
Maintenance | Regular inspection and replacement are recommended to maintain the integrity of the fuel system. |
What You'll Learn
- Material Compatibility: O-rings must match fuel line material to prevent leaks
- Temperature Tolerance: Check O-ring temperature limits to avoid fuel line damage
- Pressure Resistance: Ensure O-rings can withstand fuel line pressure without failure
- Vibration Resistance: O-rings should withstand engine vibrations without compromising seals
- Environmental Factors: Consider weather conditions and fuel type when choosing O-rings
Material Compatibility: O-rings must match fuel line material to prevent leaks
When it comes to using O-rings in fuel line applications, material compatibility is a critical factor to ensure the safety and efficiency of your system. O-rings are commonly used to seal connections and prevent leaks, but not all O-rings are suitable for fuel lines. The primary concern is the potential for fuel to degrade the O-ring material over time, leading to leaks and potential hazards.
The material of the fuel line is crucial in determining the appropriate O-ring type. Different fuels have varying chemical compositions, and some materials are more susceptible to degradation than others. For example, gasoline and diesel have different properties, and the O-ring used for one may not be compatible with the other. Therefore, it is essential to consider the specific fuel type and its potential impact on the O-ring material.
Rubber O-rings are a common choice due to their flexibility and ability to form a tight seal. However, natural rubber O-rings may not be suitable for fuel lines as they can be susceptible to fuel degradation, leading to cracks and leaks over time. On the other hand, synthetic rubber O-rings, such as those made from neoprene or butyl rubber, offer better resistance to fuel chemicals and are more durable. These synthetic materials can withstand the corrosive nature of fuels, ensuring a longer-lasting seal.
In addition to rubber O-rings, there are other materials to consider, such as silicone and nitrile. Silicone O-rings provide excellent resistance to heat and chemicals, making them ideal for high-temperature fuel systems. Nitrile O-rings, on the other hand, offer good resistance to fuels and oils, making them suitable for a wide range of fuel applications. The choice of material depends on the specific requirements of the fuel line and the operating conditions.
To prevent leaks and ensure the longevity of your fuel system, it is imperative to select O-rings that are specifically designed for the fuel type in use. Always refer to the manufacturer's guidelines and specifications for the fuel lines to determine the recommended O-ring material. By matching the O-ring material to the fuel line material, you can create a reliable seal, minimize the risk of leaks, and maintain the overall performance and safety of your fuel system.
Fuel Line Experts: Who Can Fix Your 1998 F150?
You may want to see also
Temperature Tolerance: Check O-ring temperature limits to avoid fuel line damage
When considering the use of O-rings on fuel lines, it is crucial to understand the critical aspect of temperature tolerance. O-rings are designed to provide a reliable seal, but their performance is highly dependent on the operating conditions, particularly temperature. The temperature limits of O-rings are a critical factor to consider to ensure the longevity and integrity of the fuel lines.
O-rings are typically made from various materials, each with its own temperature range. For instance, common O-ring materials include rubber, silicone, and fluorocarbon. Rubber O-rings generally have a temperature range of around -40°F to 250°F (-40°C to 121°C), while silicone O-rings can withstand temperatures from -40°F to 450°F (-40°C to 232°C). Fluorocarbon O-rings are known for their excellent temperature stability, with a range of -40°F to 500°F (-40°C to 260°C). These temperature limits are essential to know because they define the safe operating environment for the O-rings.
Using O-rings with temperature limits that are not suitable for the fuel line's operating conditions can lead to severe consequences. If the temperature exceeds the O-ring's limits, it can cause the material to degrade, leading to a loss of elasticity and, consequently, a failure to provide an effective seal. This can result in fuel leakage, which is not only dangerous but also environmentally harmful. Moreover, the heat can cause the O-rings to become brittle, leading to cracking and potential fuel line damage.
To avoid these issues, it is imperative to check the temperature limits of the chosen O-rings and ensure they align with the expected operating temperatures of the fuel lines. This includes considering both the maximum and minimum temperatures the system will encounter. For instance, if the fuel lines are used in an engine with a high-performance combustion process, the temperatures can soar, requiring O-rings with a higher temperature tolerance.
In summary, temperature tolerance is a critical aspect when using O-rings on fuel lines. It is essential to select O-rings with temperature limits that match or exceed the operating conditions to ensure a secure and reliable seal, preventing potential fuel line damage and ensuring the safety of the system. Always refer to the manufacturer's specifications and guidelines to make the right choice for your specific application.
Fuel Line Routing: 3-Piece Guide for 1964 Impala Enthusiasts
You may want to see also
Pressure Resistance: Ensure O-rings can withstand fuel line pressure without failure
When considering the use of O-rings in fuel lines, pressure resistance is a critical factor that cannot be overlooked. Fuel lines operate under high pressure, and the O-rings must be able to withstand this pressure without failing or leaking. The integrity of the fuel system relies on the O-rings' ability to maintain a tight seal, even under the stress of pressurized fuel.
O-rings are designed to provide a reliable seal, but not all types are created equal when it comes to pressure resistance. Regular O-rings, often made from standard rubber compounds, may not be suitable for fuel lines due to the corrosive nature of fuel and the potential for pressure-related failures. Fuel, being a highly volatile substance, can cause chemical degradation of the O-ring material, leading to a loss of elasticity and sealing properties.
To ensure pressure resistance, it is essential to choose O-rings specifically designed for fuel line applications. These specialized O-rings are typically made from materials that offer excellent resistance to fuel corrosion and have a higher load-bearing capacity. Look for O-rings made from compounds like nitrile rubber (NBR) or fluorinated polymers (e.g., Viton®), which are known for their superior resistance to fuel-related degradation.
The design of the O-ring itself also plays a role in pressure resistance. Consider O-rings with a larger cross-sectional area, as they provide a more robust seal and can better withstand the forces exerted by pressurized fuel. Additionally, ensure that the O-rings are properly installed and seated within the fuel line fittings to maximize their effectiveness.
In summary, when using O-rings in fuel lines, prioritize pressure resistance by selecting specialized O-rings made from appropriate materials and ensuring proper installation. This will help maintain the integrity of the fuel system and prevent potential leaks or failures caused by the high-pressure environment. Always refer to manufacturer guidelines and consult experts when in doubt to ensure the safe and reliable operation of your fuel system.
Cold Weather's Hidden Enemy: Why Fuel Lines Freeze Up
You may want to see also
Vibration Resistance: O-rings should withstand engine vibrations without compromising seals
O-rings are a common choice for sealing applications, but when it comes to fuel lines in engines, their suitability needs careful consideration, especially regarding vibration resistance. Engine vibrations can be intense and frequent, and the fuel lines are often subjected to these forces, which can compromise the integrity of the seals. Regular O-rings, while effective in many sealing scenarios, may not be the best choice for fuel lines due to their potential to fail under the stress of engine vibrations.
The primary issue with using regular O-rings in fuel lines is their tendency to wear down over time due to the repetitive motion and stress caused by engine vibrations. O-rings are designed to maintain a tight seal, but this can lead to increased friction and wear, especially in the dynamic environment of an engine. As the O-rings wear, the seal may become less effective, potentially allowing fuel to leak or vaporize, which can have serious consequences for engine performance and efficiency.
To address this concern, specialized O-rings designed for fuel lines are available, which are engineered to withstand the unique challenges posed by engine vibrations. These O-rings are typically made from materials that offer superior resistance to wear and tear, ensuring that the seal remains intact even under the most demanding conditions. They are also designed to maintain their shape and flexibility over time, providing a consistent and reliable seal.
In addition to the choice of O-ring material, the installation process is crucial for ensuring vibration resistance. Proper installation techniques, such as using the correct tools and ensuring a tight but not overly tight fit, can help prevent damage to the O-rings and ensure they function optimally. Regular inspections and maintenance can also help identify and replace worn-out O-rings before they lead to fuel leaks or other engine issues.
In summary, while regular O-rings can be used in fuel lines, their performance may be compromised by engine vibrations. Specialized O-rings designed for fuel lines offer a more reliable solution, ensuring that the seals remain intact and effective even under the harsh conditions of an engine. Proper installation and maintenance practices also play a vital role in maximizing the vibration resistance of O-rings in fuel line applications.
Fixing a Rubber ATV Fuel Line: A Step-by-Step Guide
You may want to see also
Environmental Factors: Consider weather conditions and fuel type when choosing O-rings
When it comes to selecting O-rings for fuel lines, environmental factors play a crucial role in ensuring optimal performance and longevity. Weather conditions and fuel type are two essential considerations that can significantly impact the choice of O-rings.
Firstly, weather conditions, such as temperature and humidity, can affect the flexibility and resilience of O-rings. Extreme temperatures, whether hot or cold, can cause O-rings to become brittle or lose their sealing properties. For instance, in regions with harsh winters, O-rings made from materials like natural rubber or silicone may not withstand the low temperatures, leading to cracking or hardening. On the other hand, high temperatures in hot climates can cause O-rings to become soft and lose their shape, compromising their sealing ability. Therefore, it is essential to choose O-rings made from materials that can withstand the specific temperature range of your environment.
Secondly, the type of fuel being used is another critical factor. Different fuels have varying chemical compositions and properties, which can impact the compatibility of O-rings. For example, gasoline and diesel have different boiling points and chemical structures, which can affect the O-rings' resistance to fuel degradation. Gasoline-compatible O-rings, typically made from materials like nitrile or fluorocarbon, are designed to withstand the volatile nature of gasoline. In contrast, diesel-specific O-rings may require materials like neoprene or butyl rubber, which offer better resistance to the higher temperatures and lubricating properties of diesel fuel.
Furthermore, the presence of additives in fuels, such as ethanol or biofuels, can also influence O-ring selection. These additives can alter the fuel's chemical properties, potentially causing compatibility issues with certain O-ring materials. It is crucial to consider the specific fuel blend used in your application and choose O-rings that are compatible with those additives to ensure long-term performance and prevent fuel leakage.
In summary, when choosing O-rings for fuel lines, it is imperative to consider the environmental factors of weather conditions and fuel type. Selecting O-rings made from materials that can withstand the temperature extremes and chemical properties of the fuel being used will ensure reliable sealing and prevent potential fuel leaks. Proper consideration of these factors will contribute to the overall safety and efficiency of fuel systems in various environmental conditions.
Reusing LB7 Fuel Injector Lines: A Practical Guide
You may want to see also
Frequently asked questions
No, it is not recommended to use regular O-rings for fuel lines. Fuel lines require O-rings that are specifically designed to withstand the corrosive nature of fuel, including gasoline, diesel, and aviation fuel. Regular O-rings may not provide the necessary resistance to fuel degradation, leading to potential leaks and damage over time.
Fuel-specific O-rings are formulated with materials that can resist the chemicals present in fuel, ensuring a tight seal without compromising the integrity of the fuel system. Regular O-rings may not have the same level of chemical resistance, which can result in premature failure and potential safety hazards.
Yes, several signs may indicate the use of incorrect O-rings. These include fuel leaks, reduced engine performance, and increased engine emissions. Over time, the O-rings may become brittle and fail to provide an adequate seal, leading to fuel leakage and potential engine damage.
Always refer to the manufacturer's specifications and recommendations for your fuel line setup. Using the correct O-rings designed for fuel applications will ensure optimal performance, safety, and longevity of your fuel system. It is also advisable to consult a professional mechanic or fuel system specialist for guidance.