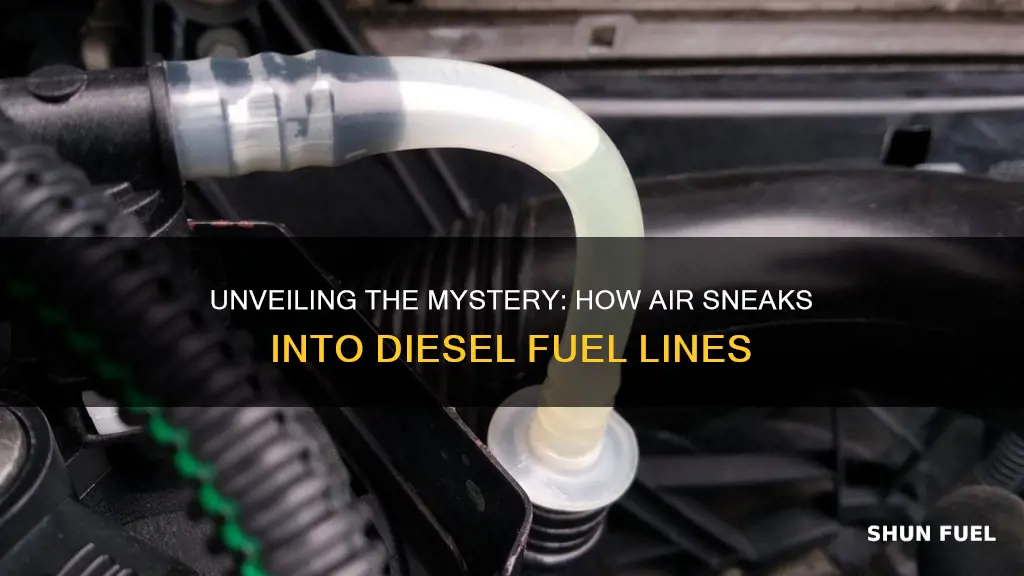
Understanding how air gets into diesel fuel lines is crucial for maintaining the performance and longevity of diesel engines. Air can enter the fuel system through various points, such as the fuel tank, injectors, and even the engine's intake system. This phenomenon is often referred to as air lock or air in the fuel. When air is present in the diesel fuel, it can lead to several issues, including reduced engine performance, increased fuel consumption, and potential damage to the engine's components over time. This paragraph will explore the causes and consequences of air in diesel fuel lines and discuss methods to prevent and address this common problem.
What You'll Learn
- Fuel Injection System: Air enters through the fuel injectors, which spray fuel and air into the engine
- Fuel Pump: The pump draws air into the fuel line to maintain pressure
- Air Filter: Filters out contaminants and ensures clean air for combustion
- Fuel Tank: Air can enter via the tank's breathing system to prevent vacuum
- Engine Operation: The engine's operation creates a vacuum, drawing air into the fuel lines
Fuel Injection System: Air enters through the fuel injectors, which spray fuel and air into the engine
The fuel injection system in a diesel engine is a complex process that ensures precise fuel delivery and combustion. Air plays a crucial role in this system, and its entry is a carefully controlled process. When the engine is running, air is drawn into the engine's intake system through the air filter. This air is then directed to the fuel injectors, which are strategically located to ensure optimal fuel-air mixture distribution.
The fuel injectors are high-pressure devices that spray a fine mist of fuel and air into the engine's combustion chamber. This process is a critical aspect of the fuel injection system's function. The injectors are designed to precisely control the amount of fuel and air entering the engine, ensuring efficient combustion. As the air is forced through the injectors, it mixes with the fuel, creating a homogeneous mixture that is essential for complete and controlled burning.
This mixture is then injected into the engine's cylinders, where the combustion process takes place. The air-fuel mixture is carefully timed and controlled to ensure that the diesel fuel ignites at the right moment, creating a powerful explosion that drives the engine's pistons. This process is highly efficient and allows for better engine performance and fuel economy.
The fuel injectors are designed to handle high-pressure fuel, which is a key feature of diesel engines. This high pressure ensures that the fuel is atomized into very small droplets, allowing for better mixing with air and more efficient combustion. The injectors are also positioned to direct the fuel-air mixture towards the center of the combustion chamber, where the spark plug ignites it, initiating the combustion process.
In summary, the fuel injection system relies on the controlled entry of air through the fuel injectors to create a precise fuel-air mixture. This mixture is then sprayed into the engine's combustion chamber, where it is ignited, powering the engine's operation. This process highlights the importance of air in the diesel fuel line and the intricate design of the fuel injection system to ensure optimal engine performance.
Flexible Fuel Lines: Unlocking the Secret to Engine Efficiency
You may want to see also
Fuel Pump: The pump draws air into the fuel line to maintain pressure
The fuel pump plays a crucial role in the diesel fuel system, ensuring that the engine receives the necessary fuel at the right pressure. One of its primary functions is to draw air into the fuel line, which might seem counterintuitive since air is not a component of the fuel itself. However, this process is essential for maintaining the required pressure and ensuring efficient fuel delivery.
When the engine is running, the fuel pump operates continuously, drawing fuel from the tank and sending it through the fuel lines to the injectors. As the pump moves fuel, it creates a partial vacuum, which is where the air comes into play. The pump is designed with an internal mechanism that allows it to draw air into the fuel line to compensate for the vacuum created. This air is not mixed with the fuel but is essential for maintaining the pressure required to deliver the fuel effectively.
The process can be understood as a balance of pressure and vacuum. As the pump moves fuel, it creates a low-pressure area, or vacuum, in the fuel line. To counteract this, the pump draws air from the atmosphere, which then enters the fuel line. This air is compressed and mixed with the fuel, creating a consistent pressure that ensures the fuel flows smoothly and efficiently to the engine's injectors.
This mechanism is particularly important in diesel engines, where the fuel must be under specific pressure to atomize and ignite properly. The fuel pump's ability to draw air into the system ensures that the pressure remains stable, even when the engine is under varying loads or speeds. This results in a more reliable and efficient combustion process, which is vital for the engine's performance and longevity.
In summary, the fuel pump's role in drawing air into the fuel line is a critical aspect of diesel engine operation. It ensures that the fuel is delivered at the right pressure, allowing for proper atomization and combustion. This simple yet effective process showcases the intricate design of the fuel system, where air and fuel work in harmony to power the engine.
Fuel Injector Cars: The Return Line Mystery
You may want to see also
Air Filter: Filters out contaminants and ensures clean air for combustion
The air filter is a crucial component in the diesel fuel system, serving as the first line of defense against contaminants that could potentially damage the engine. Its primary function is to filter out various particles and impurities from the air before it enters the combustion chamber. This is essential because diesel engines rely on a precise and controlled air-fuel mixture for efficient combustion and power generation.
When air enters the diesel fuel line, it often contains a mixture of dust, dirt, water vapor, and other airborne particles. These contaminants can have detrimental effects on the engine's performance and longevity. For instance, water vapor can condense and lead to the formation of rust and corrosion within the fuel system, while solid particles can cause mechanical damage to the engine components. Therefore, the air filter's role is to trap and remove these unwanted substances.
The air filter is typically designed with a series of pleated media, often made of paper, cotton, or synthetic fibers. These pleats provide a large surface area, allowing for efficient filtration. As air flows through the filter, the contaminants are physically trapped on the surface of the media. The filter's design ensures that the air is forced to pass through a tortuous path, increasing the likelihood of particle capture. Over time, as the filter collects more contaminants, it becomes saturated and requires replacement to maintain its effectiveness.
Regular maintenance and replacement of the air filter are essential to ensure optimal engine performance. Clogged or dirty air filters can restrict airflow, leading to reduced power, increased fuel consumption, and even engine misfires. By keeping the air filter clean and functional, diesel engines can operate efficiently, delivering the required power output while maintaining a longer lifespan.
In summary, the air filter plays a critical role in the diesel fuel system by filtering out contaminants and ensuring that only clean air enters the combustion chamber. This process is vital for maintaining engine performance, preventing damage, and ensuring the overall reliability of the diesel engine. Proper maintenance of the air filter is a simple yet effective way to keep the engine running smoothly and efficiently.
Mastering Fuel Line Taping: A Guide to Inline Fuel Pump Success
You may want to see also
Fuel Tank: Air can enter via the tank's breathing system to prevent vacuum
The fuel tank's breathing system is a crucial component designed to manage the air-fuel mixture within the tank, ensuring optimal combustion in the engine. This system allows air to enter the tank while simultaneously preventing the formation of a vacuum, which could lead to issues with fuel delivery. Here's a detailed explanation of how this process works:
When the engine is running, the breathing system is actively engaged. It consists of a series of components, including a breather pipe, a filter, and a check valve. The breather pipe is designed to allow air to flow into the tank while keeping contaminants out. This pipe is typically located near the top of the tank, where it can easily access the air. As the engine operates, it creates a slight vacuum, which pulls air through the breather pipe and into the tank. This air is then used to replenish the fuel-air mixture, ensuring the engine receives the necessary oxygen for efficient combustion.
The filter within the breathing system plays a critical role in maintaining the cleanliness of the fuel. It captures any dust, dirt, or moisture that might enter the system, preventing these contaminants from reaching the fuel and potentially causing engine damage. This filter is often designed with a fine mesh or a specialized material to trap particles effectively.
To prevent a vacuum, the check valve is an essential component. It is positioned at the end of the breather pipe and is designed to allow air to flow in one direction only. When the engine is running, the check valve opens, allowing air to enter the tank. However, when the engine is turned off, the check valve closes, creating a seal that prevents air from entering the tank. This mechanism ensures that the fuel level remains stable, even when the engine is not in use.
In summary, the fuel tank's breathing system is a well-thought-out design that facilitates the intake of air while maintaining a controlled environment within the tank. By allowing air to enter and preventing vacuums, this system ensures that the fuel remains stable and ready for combustion when the engine is started. Regular maintenance of this system, including checking and replacing filters, is essential to guarantee its effectiveness and the overall performance of the diesel engine.
Fuel Line Flaring: A Double-Edged Decision
You may want to see also
Engine Operation: The engine's operation creates a vacuum, drawing air into the fuel lines
The operation of an engine is a complex process that involves multiple components working in harmony. One crucial aspect of this process is the fuel system, which plays a vital role in ensuring the engine receives the necessary fuel for efficient combustion. When it comes to diesel engines, understanding how air can enter the fuel lines is essential for maintaining optimal performance and preventing potential issues.
As the engine operates, it creates a unique environment within the fuel system. The combustion process generates a significant amount of heat, causing the fuel and air mixture to expand and create a pressure differential. This pressure difference is what drives the engine's ability to draw air into the fuel lines. When the engine is running, it creates a vacuum effect, pulling air from the surroundings into the system. This air is then mixed with the fuel, creating a precise ratio that is critical for efficient combustion.
The fuel lines are designed with specific diameters and lengths to facilitate this process. As the engine's internal components, such as the injectors and pumps, draw fuel, they also inadvertently draw in air. This air is then carried along with the fuel, ensuring a continuous supply of both components to the engine's combustion chambers. The engine's design and the positioning of the fuel injectors are carefully considered to optimize this air-fuel mixture.
It's important to note that this process is a delicate balance. While air is necessary for combustion, excessive air can lead to inefficient fuel usage and potential performance issues. Therefore, the engine's fuel management system, including the fuel injectors and pumps, must be calibrated to deliver the precise amount of fuel and air required for each cylinder. This calibration ensures that the engine operates smoothly and efficiently, meeting the demands of various driving conditions.
Understanding the engine's operation and its impact on the fuel system is crucial for diesel engine maintenance. Regular checks and maintenance, such as replacing fuel filters and ensuring proper fuel line connections, can help prevent air intrusion and maintain the engine's performance. By recognizing the engine's role in creating a vacuum and drawing air into the fuel lines, technicians and enthusiasts can take proactive measures to keep the engine running smoothly and reliably.
Honda 5 HP Outboard: Fuel Line Adapter Guide
You may want to see also
Frequently asked questions
Air can enter the diesel fuel line due to several reasons. One common cause is a faulty fuel pump or filter, which may allow air to be drawn into the system. Additionally, if the fuel tank is not properly sealed, air can seep in, especially when the vehicle is stationary or during fuel level changes.
Air in the diesel fuel line can lead to several performance issues. When air is introduced, it can cause fuel atomization problems, resulting in poor combustion. This may lead to reduced power output, increased fuel consumption, and even engine misfires or stalling.
Yes, if air is left unchecked in the diesel fuel line, it can cause significant engine damage over time. Air bubbles can lead to erratic engine behavior, including rough idling, reduced performance, and potential engine knocking or pinging sounds. In extreme cases, air can cause fuel pump damage or even engine failure.
There are several indicators that air has entered the fuel line. These include engine hesitation or stalling during acceleration, rough or uneven idling, increased fuel consumption, and the presence of fuel vapor or bubbles in the engine's exhaust. In some cases, you might also notice a hissing sound coming from the fuel system.
Preventing air intrusion involves several maintenance and inspection steps. Regularly check and replace fuel filters to ensure they are not clogged or damaged. Inspect the fuel lines for any cracks or leaks, and ensure they are properly secured. Maintaining a tight seal on the fuel tank and using a fuel system cleaner can also help eliminate air bubbles and improve overall fuel system health.