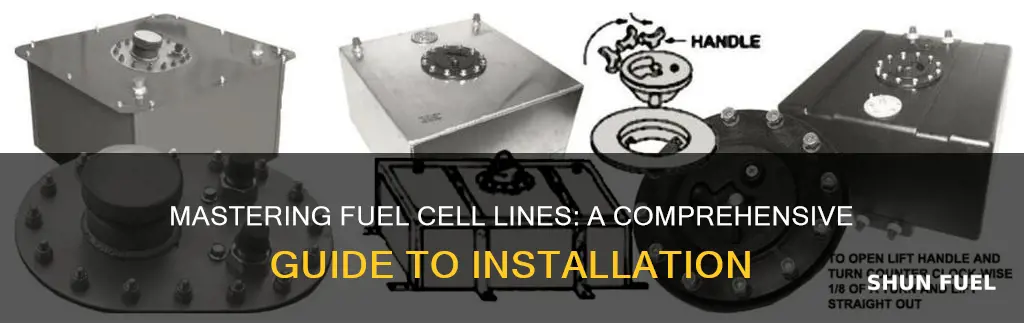
Installing fuel cell lines is a crucial step in setting up a fuel cell system for vehicles or stationary applications. It involves carefully routing and connecting the fuel cell's hydrogen supply, often from a high-pressure tank, to the cell's inlet port and then to the fuel cell stack. The process requires precise measurements and careful consideration of the system's layout to ensure optimal performance and safety. This guide will provide a step-by-step overview of the installation process, covering everything from preparing the necessary tools and materials to ensuring proper sealing and testing of the connections.
What You'll Learn
- Safety Gear: Wear protective clothing, gloves, and eye protection to ensure safety during installation
- Fuel Tank Inspection: Check for leaks and damage before connecting fuel lines
- Line Routing: Plan a secure path for fuel lines, avoiding sharp bends and tight spaces
- Fittings and Connections: Use the right fittings and ensure tight, leak-free connections
- Testing and Verification: Test fuel lines for leaks and pressure to ensure proper functionality
Safety Gear: Wear protective clothing, gloves, and eye protection to ensure safety during installation
When embarking on the installation of fuel cell lines, prioritizing safety is paramount. This entails donning the appropriate protective gear to safeguard yourself from potential hazards associated with this task. Here's a comprehensive guide on the essential safety gear you should consider:
Protective Clothing: Opt for long-sleeved shirts and pants made from durable materials like leather or heavy-duty cotton. These garments provide a barrier against potential splashes or spills of fuel, which can be corrosive and harmful. Ensure the clothing is fire-resistant to minimize the risk of injury in case of any accidental fires. Additionally, consider wearing a full-body suit if the installation process involves extensive contact with the fuel cell or its components.
Gloves: Protect your hands with heavy-duty gloves designed for industrial use. Look for gloves made from materials like nitrile or leather, ensuring they offer a good grip and dexterity. Gloves will shield your hands from direct contact with fuel, preventing skin irritation and potential chemical burns. It's crucial to choose gloves that are fire-resistant as well, especially if you anticipate any potential heat exposure during the installation process.
Eye Protection: Safety goggles or glasses are indispensable when working with fuel cell lines. They create a protective shield for your eyes, guarding against potential splashes or fumes that may contain harmful substances. Choose goggles that offer a secure fit, ensuring they stay in place during the installation process. Look for impact-resistant lenses to protect against any flying debris or particles that might be present in the work area.
By adhering to these safety gear recommendations, you create a protective barrier that minimizes the risks associated with fuel cell line installation. It is essential to stay vigilant and ensure that all protective equipment is properly fitted and maintained throughout the project. Remember, safety should always be the top priority when handling potentially hazardous materials and equipment.
Mastering Fuel Line Sleeving: A Concrete Guide
You may want to see also
Fuel Tank Inspection: Check for leaks and damage before connecting fuel lines
Before you begin the process of connecting fuel lines to a fuel tank, it is crucial to conduct a thorough inspection to ensure the safety and integrity of the system. This step is often overlooked but is essential to prevent potential hazards and costly repairs. Here's a detailed guide on how to inspect the fuel tank for leaks and damage:
- Visual Inspection: Start by visually examining the fuel tank and its surroundings. Look for any signs of corrosion, rust, or damage to the tank's exterior. Check for cracks, especially around the tank's seams and attachments. Inspect the fuel tank's capacity and ensure it is clean and free from any visible contaminants or debris. Over time, fuel tanks can accumulate dirt, water, or sediment, which may indicate potential issues.
- Leak Detection: The primary concern during fuel tank inspection is identifying leaks. Here are some methods to detect leaks:
- Bubble Test: Fill the fuel tank with a small amount of water and carefully observe the surface. If there are any bubbles forming on the water's surface, it indicates a leak. Bubbles will rise to the top, so look for any signs of water accumulation or bubbles around the tank's openings.
- Soapy Water Method: Mix a small amount of dish soap with water and carefully spray it onto the fuel tank's surface. Leaks will create bubbles, allowing you to identify potential problem areas.
- Pressure Test: Use a pressure gauge to measure the tank's pressure. Compare it to the manufacturer's recommended pressure levels. Low pressure or rapid pressure drops may suggest a leak.
- Inspect Connections: Examine all connections and attachments related to the fuel tank. Check for tightness and secure fittings. Ensure that all bolts and fasteners are in place and tightened according to the manufacturer's specifications. Look for any signs of corrosion or damage around these connections, as they can lead to leaks over time.
- Document and Repair: If any leaks or damage is detected during the inspection, it is crucial to address them promptly. Document the issues with notes and photographs for future reference. Repair or replace the affected parts, ensuring they meet the required standards. This may include sealing leaks with appropriate compounds or replacing damaged components.
By following these steps, you can ensure that the fuel tank is in optimal condition before connecting the fuel lines. This preventive measure is vital to maintain the efficiency and safety of your fuel system, reducing the risk of fuel leaks and potential engine damage. Remember, regular maintenance and inspections are key to keeping your vehicle's fuel system reliable.
Find the Perfect Fuel Line Size for Your Husqvarna 128LD
You may want to see also
Line Routing: Plan a secure path for fuel lines, avoiding sharp bends and tight spaces
When installing fuel cell lines, proper line routing is crucial to ensure the system's safety and longevity. The goal is to create a secure path for the fuel lines that minimizes the risk of damage and potential leaks. One of the key principles is to avoid sharp bends and tight spaces, as these can cause stress on the lines and potentially lead to cracks or punctures over time.
Start by identifying the optimal route for the fuel lines, considering the layout of the vehicle or equipment you're working on. The lines should be as straight as possible, especially when running along the length of the vehicle. If a bend is necessary, ensure it is gradual and not sharp. A gentle curve can be achieved by using flexible fuel lines with a suitable radius, allowing the line to bend without excessive stress.
In tight spaces, such as engine compartments or under dashboards, careful planning is essential. Consider the clearance required for the fuel lines and ensure there are no obstacles or protruding components that could cause damage. One effective method is to use line guides or sleeves to protect the fuel lines. These can be made of flexible materials that conform to the shape of the vehicle, providing a smooth and secure path for the lines.
When routing the lines, maintain consistent tension to prevent kinking. Kinks can restrict fuel flow and potentially cause damage to the lines. Use tensioners or clips to keep the lines taut, especially where they cross or turn. Regularly inspect the lines during the installation process to ensure they remain free of any obstructions or damage.
Additionally, consider the material of the fuel lines. Different materials offer varying levels of flexibility and durability. For example, rubber lines are more flexible but may be more susceptible to damage from sharp objects. In contrast, braided lines are more rigid and less flexible but can withstand higher pressures and temperatures. Choose the appropriate material based on the specific requirements of your fuel system.
Frozen Fuel Lines: The Silent Culprit Behind Your Car's Failure to Start
You may want to see also
Fittings and Connections: Use the right fittings and ensure tight, leak-free connections
When installing fuel cell lines, the choice of fittings and connections is critical to ensure a safe and efficient system. The primary goal is to create a secure and leak-free pathway for the fuel to travel from the source to the engine. This involves using specific fittings and employing proper installation techniques to guarantee a tight seal.
The first step is to select the appropriate fittings. These fittings should be designed specifically for fuel cell lines and compatible with the fuel type and system pressure. Common types include barbed fittings, compression fittings, and quick-connect fittings. Barbed fittings are ideal for flexible hoses and provide a secure connection with a simple push-on mechanism. Compression fittings, on the other hand, use a ferrule to create a tight seal around the pipe, offering a more permanent solution. Quick-connect fittings are convenient for temporary or high-vibration applications, allowing for easy disconnection and reconnection.
Ensuring a tight connection is essential to prevent fuel leaks. Start by cleaning the pipe ends and fittings to remove any dirt or debris. Then, apply a suitable lubricant to the threads or sealing surfaces, ensuring it is compatible with the materials used. For compression fittings, insert the pipe into the fitting and use a wrench to tighten it securely, but be careful not to over-tighten to avoid damage. With barbed fittings, simply push the pipe onto the fitting until it is firmly in place. For quick-connect fittings, follow the manufacturer's instructions for assembly, often involving the use of a special tool to create a secure bond.
After installation, it is crucial to test the system for leaks. This can be done using a bubble test or a pressure test, depending on the system's requirements. During the test, inspect all connections and fittings for any signs of leakage. If a leak is detected, carefully identify the source and tighten or adjust the fitting as necessary. Ensure that all connections are secure and that there are no sharp bends or kinks in the fuel lines that could compromise the seal.
In summary, the key to successful fuel cell line installation lies in the choice of fittings and the execution of tight, leak-free connections. By selecting the right fittings for the specific application and following proper installation procedures, you can ensure a reliable and safe fuel supply system. Regular maintenance and inspections will also help identify and rectify any potential issues, contributing to the overall performance and longevity of the fuel cell lines.
Cessna 172 Fuel Line Flush: A Step-by-Step Guide
You may want to see also
Testing and Verification: Test fuel lines for leaks and pressure to ensure proper functionality
When it comes to installing fuel cell lines, testing and verifying the system's functionality is crucial to ensure safety and performance. Here's a detailed guide on how to test and verify the fuel lines for leaks and pressure:
Leak Testing:
- Start by preparing the necessary tools and materials, including a leak detection kit, which typically consists of a soap solution or a specialized foam.
- Isolate the fuel lines by disconnecting them from the fuel cell and any other connected components. Ensure you have access to both the high-pressure and low-pressure sides of the lines.
- Apply the leak detection solution or foam along the entire length of the fuel lines, including connections and fittings. Pay close attention to areas where lines are joined or where potential weaknesses might exist.
- Observe the lines for any bubbles or foam bubbles forming. These bubbles indicate the presence of air or fuel entering the system, which could be a sign of a leak. If you notice any bubbles, carefully inspect the affected area for any cracks, holes, or damage.
- For more accurate detection, use a leak detection stick or a similar tool that changes color when exposed to fuel or air. This method can provide a more precise indication of potential leaks.
- If a leak is suspected, carefully inspect the area and consider temporary repairs or replacements to ensure the system is leak-free before final installation.
Pressure Testing:
- After confirming the fuel lines are leak-free, proceed with pressure testing to ensure the system can handle the required fuel pressure.
- Use a pressure gauge specifically designed for fuel systems to measure the pressure at different points along the lines. Start with the fuel cell and measure the pressure at various intervals, including near the pump and at the fuel injectors.
- Compare the measured pressure values with the manufacturer's specifications for the fuel cell and lines. Ensure that the pressure at all points meets or exceeds the required levels.
- If the pressure is insufficient, consider adjusting the fuel pump settings or checking for any restrictions in the lines that might be causing a drop in pressure.
- Document the pressure readings and make any necessary adjustments to ensure the system operates within the desired pressure range.
Safety Precautions:
- When performing these tests, always prioritize safety. Wear appropriate personal protective equipment (PPE) and ensure proper ventilation, especially when dealing with fuel, as it can be hazardous.
- Keep a fire extinguisher nearby during the testing process, as fuel can be flammable.
- If you are unsure about any aspect of the testing process, consult the fuel cell's manual or seek professional assistance to ensure accurate and safe testing.
By thoroughly testing and verifying the fuel lines for leaks and pressure, you can ensure that the installation is correct and the fuel cell system will operate efficiently and safely. This step is essential to maintain the overall performance and longevity of the fuel cell setup.
Fuel Line Mystery: Locating Injector Lines in 04 Jetta TDI
You may want to see also
Frequently asked questions
Before beginning the installation process, ensure you have the necessary tools and equipment, including fuel cell lines, connectors, and a fuel cell. It is crucial to inspect the vehicle's fuel system to identify any potential issues or leaks.
When connecting the lines, start by aligning the male and female ends of the lines. Use the appropriate connectors and secure them tightly. Ensure a tight seal to prevent any fuel leaks. It is recommended to use a fuel-resistant tape or sealant around the connections for added safety.
Yes, proper routing is essential for a clean and functional installation. Route the lines away from heat sources and sharp edges to prevent damage. Keep the lines as straight as possible to minimize the risk of kinks and ensure smooth fuel flow. Consider using brackets or ties to secure the lines in place.
Safety is paramount. Always wear protective gear, such as gloves and safety goggles, to avoid contact with fuel. Ensure proper ventilation in the work area. Test the connections for leaks using a soapy water solution or a specialized fuel leak detector. Regularly check for any signs of corrosion or damage during and after the installation process.