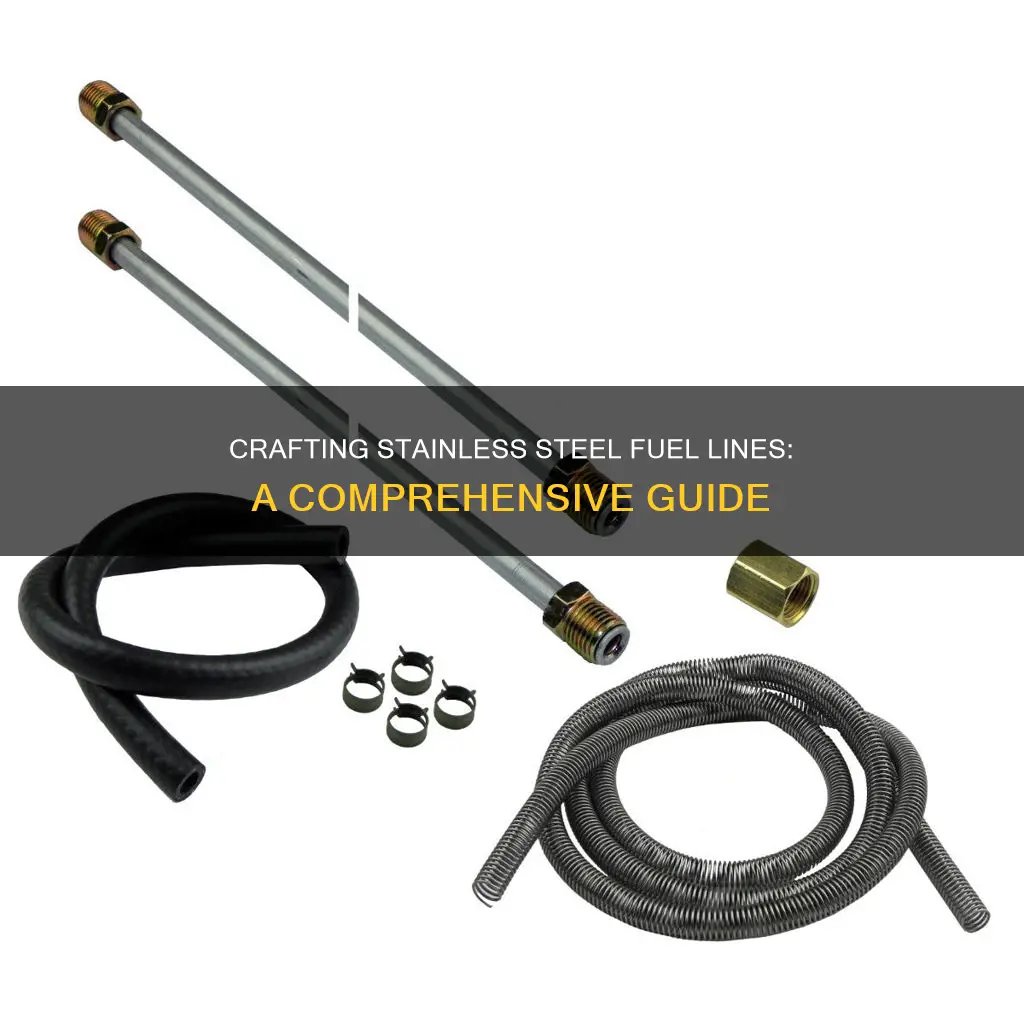
Creating stainless steel fuel lines is a specialized process that requires precision and attention to detail. This guide will explore the essential steps involved in manufacturing these robust and durable fuel lines, which are crucial for various applications, including automotive and industrial settings. From selecting the right stainless steel material to employing specific welding techniques, we will delve into the key considerations and best practices to ensure the production of high-quality, reliable fuel lines.
What You'll Learn
- Materials and Tools: Gather necessary supplies like stainless steel tubing, fittings, and tools
- Cutting and Measuring: Accurately measure and cut the tubing to desired lengths
- Fitting Installation: Securely attach fittings using appropriate methods for a tight seal
- Bending and Forming: Manipulate the tubing to fit fuel line routes and angles
- Testing and Inspection: Ensure fuel lines are leak-free and meet safety standards
Materials and Tools: Gather necessary supplies like stainless steel tubing, fittings, and tools
To begin the process of creating stainless steel fuel lines, you'll need to gather the essential materials and tools required for the project. Here's a detailed breakdown of what you should collect:
Materials:
- Stainless Steel Tubing: Opt for high-quality, food-grade stainless steel tubing with a suitable diameter for your fuel lines. The thickness and gauge should be appropriate for the pressure and temperature requirements of your fuel system. Common diameters for fuel lines range from 3/8" to 1/2" ID (inside diameter).
- Fittings: You'll need various fittings to connect the tubing and ensure a secure and leak-free installation. Common fittings include elbows, tees, couplings, reducers, and caps. Choose fittings made from the same material as the tubing to ensure compatibility.
- Clamps and Gaskets: Stainless steel clamps and gaskets are essential for sealing connections and preventing fuel leaks.
Tools:
- Tube Cutter: A tube cutter is a must-have tool for precisely cutting the stainless steel tubing to the desired length. Ensure it can handle the thickness of your chosen tubing.
- Pipe Threading Tools: If your fuel lines require threaded connections, you'll need a pipe threader and dies to create accurate threads.
- Welding Equipment (Optional): For more advanced projects, you might consider investing in a small welding setup to join sections of tubing. However, this is not always necessary, especially if you're using fittings.
- Pliers and Wrenches: Basic hand tools like pliers and wrenches are essential for gripping, bending, and tightening fittings and connections.
- Sandpaper or Wire Brush: These tools will help remove any burrs or sharp edges from the tubing and fittings, ensuring a smooth and safe installation.
- Measuring Tape or Caliper: Accurate measurement tools are crucial for ensuring the correct sizing of the tubing and fittings.
Having all these materials and tools ready will ensure that you can proceed with the construction of your stainless steel fuel lines efficiently and effectively. It's important to source high-quality materials to ensure the durability and reliability of your fuel system.
Aluminum Fuel Line Straightening: Tips and Tricks for a Smooth Ride
You may want to see also
Cutting and Measuring: Accurately measure and cut the tubing to desired lengths
When it comes to creating custom stainless steel fuel lines, accurate measurements and precise cutting are crucial steps to ensure a professional and safe installation. Here's a detailed guide on how to measure and cut the tubing to your desired lengths:
Step 1: Gather the Materials and Tools
Before you begin, ensure you have all the necessary materials and tools. You'll need the stainless steel tubing, a tape measure or ruler, a marking tool (such as a pencil or marker), a cutting torch or band saw, and safety gear like gloves and eye protection. Having everything ready will make the process smoother.
Step 2: Plan the Layout
Decide on the layout and length of your fuel lines. Consider the distance between the fuel source and the engine, as well as any bends or turns the line needs to make. Measure the total length required, taking into account any additional material needed for connections and fittings. It's better to have a slightly longer piece of tubing and trim it to size later than to cut too short and have to start over.
Step 3: Mark the Tubing
Place the tubing on a flat surface and use your measuring tool to determine the desired length. Mark the tubing at the appropriate points with your chosen marking tool. Ensure the marks are clear and aligned with the tubing's center. For curved sections, you might need to make multiple marks to account for the bend radius.
Step 4: Cut the Tubing
Now, you can start cutting the tubing. If you're using a cutting torch, ensure it is set to the appropriate heat setting for stainless steel. Hold the torch at a slight angle and apply heat to the marked area, then quickly cut through the tubing with a sharp blade or shears. For a more precise cut, a band saw or a good-quality tubing cutter can be used, ensuring a clean and accurate edge. Always cut slowly and carefully to avoid any mistakes.
Step 5: Safety and Precision
Accurate measurements and cutting are essential to avoid any fuel leaks or damage to the engine. Take your time and double-check your measurements before cutting. Consider using a template or a straight edge to ensure straight cuts. Safety should always be a priority, so wear protective gear and work in a well-ventilated area when using cutting tools.
By following these steps, you'll be able to measure and cut the stainless steel tubing accurately, setting the foundation for a successful fuel line installation. Remember, precision is key to a reliable and safe fuel system.
Polyethylene Tubing: A Viable Option for Fuel Lines?
You may want to see also
Fitting Installation: Securely attach fittings using appropriate methods for a tight seal
When installing fittings onto your stainless steel fuel lines, it's crucial to ensure a secure and tight seal to prevent any leaks or potential hazards. Here's a step-by-step guide to achieving this:
Preparation: Before you begin, make sure the fittings and fuel lines are clean and free from any debris or contaminants. Use a suitable solvent or cleaner to remove any old adhesives or residues from previous installations. This step ensures a proper bond between the fittings and the fuel lines.
Fitting Selection: Choose the appropriate fittings that match the diameter and material of your stainless steel fuel lines. Different types of fittings, such as compression, barbed, or quick-connect, offer various methods of attachment. Select the one that best suits your project's requirements, considering factors like pressure, temperature, and ease of installation.
Assembly Technique: Securely attach the fittings to the fuel lines using the recommended methods. For compression fittings, insert the fuel line into the fitting and ensure it is centered. Then, tighten the compression nut or sleeve using a wrench, applying firm pressure to create a tight seal. For barbed fittings, slide the barbed end over the fuel line and secure it with a ferrule or crimping tool. Ensure the fitting is firmly attached without causing damage to the fuel line.
Tightening and Sealing: When tightening the fittings, use the appropriate tools to avoid over-tightening, which can damage the fuel lines. Apply firm, even pressure to create a secure seal. Consider using thread seal tape or pipe compound on the threads to provide an additional layer of protection against leaks. For quick-connect fittings, follow the manufacturer's instructions for proper assembly and tightening.
Testing and Inspection: After the installation, it's essential to test the fittings for any leaks. Apply a small amount of fuel or a suitable sealant to the connections and observe for any signs of leakage. If everything is secure, the fuel lines should be ready for use. Regularly inspect the fittings, especially in high-pressure areas, to ensure the integrity of the seal over time.
By following these detailed steps, you can ensure that your stainless steel fuel lines are properly fitted and sealed, providing a reliable and safe fuel delivery system. Remember, a well-executed fitting installation is crucial for the overall performance and longevity of your fuel line setup.
Crafting Custom Fuel Lines: A Step-by-Step Guide
You may want to see also
Bending and Forming: Manipulate the tubing to fit fuel line routes and angles
When working with stainless steel fuel lines, bending and forming techniques are crucial to ensure a precise and secure fit. This process involves manipulating the tubing to match the desired route and angles, allowing for a seamless integration into your vehicle's fuel system. Here's a step-by-step guide to mastering this aspect of fuel line construction:
Understanding the Material: Before beginning, familiarize yourself with the properties of stainless steel. This material is known for its excellent corrosion resistance and durability, making it ideal for fuel lines. However, it can be challenging to bend due to its hardness. Understanding the material's characteristics will help you anticipate potential issues and choose the appropriate tools and techniques.
Gathering the Right Tools: Bending stainless steel fuel lines requires specialized tools. You'll need a good-quality tube bender, preferably one with adjustable settings to accommodate different diameters. Additionally, consider using a mandrel or a bending die to ensure clean and precise bends. Having the right tools will make the bending process more efficient and accurate.
Measuring and Marking: Accurate measurements are essential. Measure the length of the fuel line required and mark the tubing accordingly. Use a straight edge or a ruler to ensure straight lines. Marking the tubing at regular intervals will help you maintain consistency and make the bending process more manageable.
Bending Techniques: Start bending the tubing by placing it securely in the tube bender. Adjust the bender's settings to match the desired bend radius and angle. Apply pressure gradually, ensuring the material deforms without cracking or breaking. For tighter bends, consider using a mandrel to create a smooth, continuous curve. Practice and precision are key here; take your time to achieve the required angles and curves.
Forming and Shaping: After bending, you might need to further manipulate the tubing to fit specific routes. This could involve shaping the ends or creating custom bends. Use pliers or a hand-held tool to carefully form the tubing without damaging it. Remember, stainless steel can be sensitive to heat, so be cautious during the forming process.
Mastering the art of bending and forming stainless steel fuel lines requires practice and attention to detail. By following these steps and adapting them to your specific fuel line design, you can create a robust and reliable fuel system for your vehicle.
Unclogging Diesel Fuel Lines: A Step-by-Step Guide
You may want to see also
Testing and Inspection: Ensure fuel lines are leak-free and meet safety standards
When it comes to ensuring the safety and reliability of your fuel lines, testing and inspection are crucial steps that should not be overlooked. The process of making stainless steel fuel lines involves several intricate steps, and the final product must be thoroughly evaluated to guarantee its performance and longevity. Here's a detailed guide on how to conduct these essential tests:
Leak Testing: One of the primary concerns when dealing with fuel lines is preventing leaks. Start by using a simple yet effective method: the pressure test. Fill the fuel lines with a suitable pressure gauge and observe for any signs of leakage. Apply pressure gradually and monitor the lines for any hissing or dripping sounds, which could indicate a potential issue. If you detect any leaks, identify the source by tracing the fuel line's path and checking for any damage or weak points. This step is critical as it ensures that the fuel lines can withstand the pressure of the fuel system without compromising safety.
Visual Inspection: A thorough visual inspection is essential to identify any visible defects or damage. Examine the stainless steel fuel lines for any signs of corrosion, pitting, or discoloration. Look for bends, kinks, or any physical damage that might have occurred during installation or manufacturing. Pay close attention to connections and fittings, ensuring they are secure and free from any debris or oxidation. Any visible defects should be addressed immediately, as they could lead to more significant issues during operation.
Fluid Compatibility Testing: Different fuels may have varying chemical compositions, and it's crucial to ensure compatibility with the chosen fuel. Conduct fluid compatibility tests by running the fuel lines through a series of simulations. Use a fuel sample that closely resembles the actual fuel your vehicle will use. Monitor the lines for any signs of degradation, such as rust formation or material softening, which could indicate incompatibility. This test is vital to prevent fuel line deterioration and potential system failures.
Pressure Rating and Flow Testing: Stainless steel fuel lines should be able to withstand the system's pressure and ensure efficient fuel flow. Conduct pressure rating tests by applying the system's maximum pressure to the fuel lines and checking for any leaks or structural integrity issues. Additionally, measure the flow rate through the lines to ensure they meet the required specifications. This testing ensures that the fuel lines can handle the demands of the vehicle's engine without compromising performance.
Compliance with Safety Standards: Adherence to industry safety standards is non-negotiable. Familiarize yourself with the relevant regulations and guidelines for fuel line installations. Ensure that your fuel lines meet or exceed these standards, especially regarding material quality, manufacturing processes, and testing procedures. Compliance ensures that your fuel system is safe and reliable, providing peace of mind to vehicle owners and operators.
By following these testing and inspection protocols, you can guarantee that your stainless steel fuel lines are not only leak-free but also meet the highest safety standards. This meticulous approach to quality control is essential in the automotive industry, where the performance and safety of fuel systems are of utmost importance.
Unraveling the Mystery: Why Animals Chew Fuel Lines
You may want to see also
Frequently asked questions
Stainless steel fuel lines are an excellent choice for fuel delivery systems due to their durability, corrosion resistance, and ability to withstand high temperatures. They are commonly used in high-performance vehicles, racing applications, and marine environments where traditional rubber or plastic fuel lines may not be suitable.
The gauge of the stainless steel fuel line depends on the specific requirements of your project. Thicker gauges offer more durability and are ideal for high-pressure systems or when carrying high-octane fuels. Thinner gauges are lighter and more flexible, making them suitable for intricate routing and custom installations. Consult with a specialist or refer to the manufacturer's guidelines to select the appropriate gauge for your fuel line application.
While it is possible to install stainless steel fuel lines yourself, especially for straightforward projects, it is highly recommended to seek professional assistance for optimal results and safety. Fuel line installation requires precision and knowledge of fuel system components. Professionals have the expertise to ensure proper fitting, sealing, and compliance with safety standards, reducing the risk of leaks or system failures.
The installation process typically involves the following tools and materials:
- Stainless steel fuel lines of the desired length and gauge.
- Fuel line connectors, fittings, and clamps compatible with stainless steel.
- Fuel pump and filter (if not already installed).
- Wrenches, pliers, and other hand tools for assembly.
- Cleaning supplies to prepare the fuel system.
- Safety gear, including gloves and eye protection.
Yes, proper maintenance is essential to ensure the longevity of your stainless steel fuel lines. Here are some tips:
- Regularly inspect the lines for any signs of damage, corrosion, or leaks.
- Keep the fuel system clean by using fuel stabilizers and regularly changing the fuel filter.
- Avoid using harsh chemicals or cleaners that could damage the stainless steel.
- Protect the lines from sharp objects and high-temperature sources to prevent punctures or heat-related damage.
- Consider using a fuel line protector or shield for added safety, especially in harsh environmental conditions.