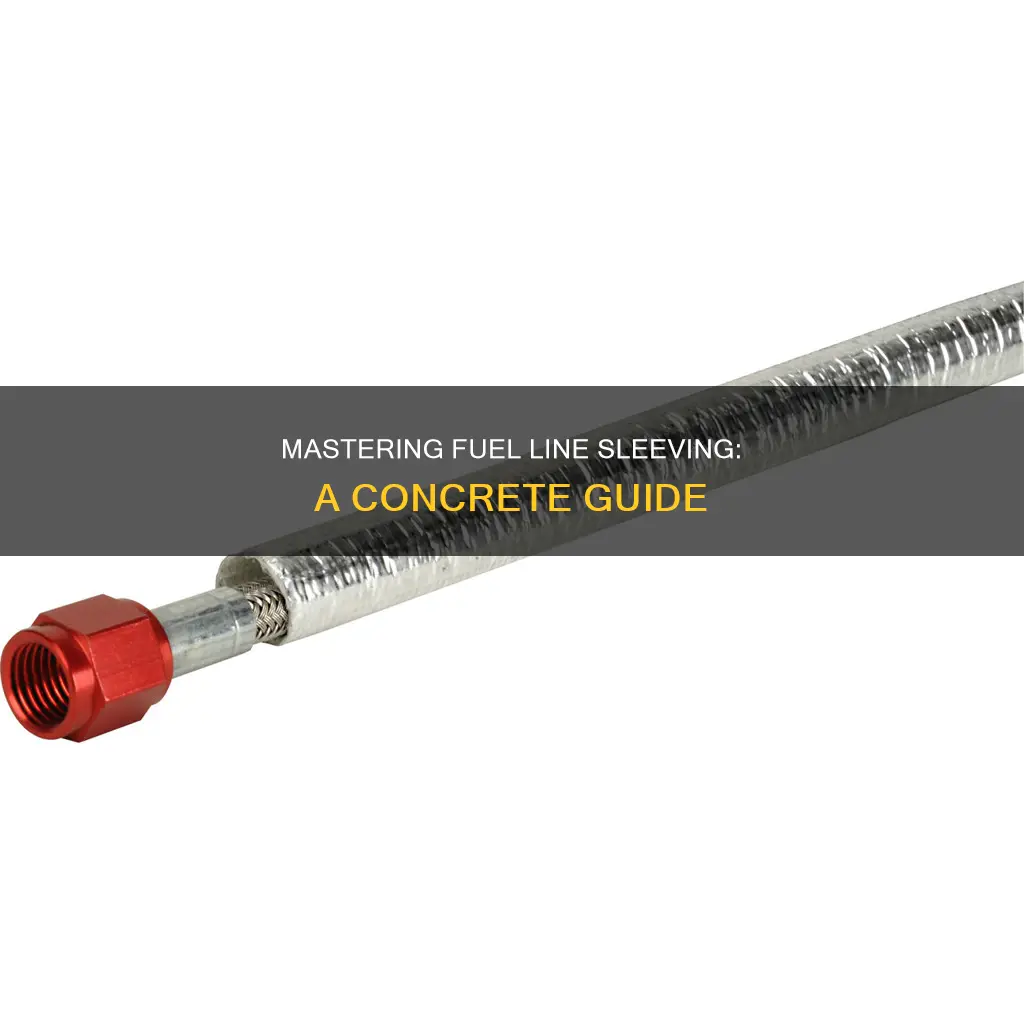
Sleeve siting a fuel line in concrete is a crucial process in construction and maintenance, especially for fuel tanks and pipelines. This technique involves inserting a flexible sleeve, typically made of rubber or plastic, around a fuel line to protect it from damage and ensure a secure fit within a concrete structure. The process requires careful preparation, including cleaning the fuel line, measuring the sleeve length accurately, and using the right adhesive to bond the sleeve to the line. Proper installation is essential to prevent leaks and ensure the long-term integrity of the fuel system. This guide will provide a step-by-step overview of the process, highlighting the importance of each stage to achieve a successful and safe sleeve installation.
What You'll Learn
- Prepare the Line: Clean and cut the fuel line to fit the sleeve, ensuring a precise match
- Choose the Sleeve: Select a sleeve made of durable material suitable for fuel, considering size and flexibility
- Secure the Sleeve: Use mechanical fasteners or adhesive to firmly attach the sleeve to the fuel line
- Install in Concrete: Position the sleeve in the concrete, ensuring it's centered and secure, then pour concrete around it
- Test and Finish: Verify the fuel line's functionality, then seal and finish the concrete to protect the installation
Prepare the Line: Clean and cut the fuel line to fit the sleeve, ensuring a precise match
When preparing the fuel line for sleeving, it's crucial to ensure a clean and precise cut to achieve a proper fit. Start by thoroughly cleaning the fuel line to remove any dirt, debris, or contaminants. This step is essential to ensure a tight seal and prevent any potential leaks. Use a suitable cleaner and a soft brush to scrub the entire length of the line, paying extra attention to any bends or joints. Rinse the line thoroughly to eliminate any residue.
Once the line is clean, measure and mark the desired length for the sleeve. It's important to cut the line to the exact specifications to avoid any unnecessary material or potential misalignment. Use a sharp utility knife or a fuel line cutter for this task, ensuring a clean and precise cut. Take your time and double-check the measurements to avoid any mistakes.
After cutting, inspect the fuel line to ensure it is free from any damage or imperfections. Look for any bends or kinks that might affect the sleeve's installation. If any issues are found, carefully straighten or repair the line before proceeding.
Now, carefully measure and mark the sleeve's inner diameter to ensure it matches the fuel line's diameter. This step is critical to ensure a snug fit. Use a ruler or a caliper to measure and mark the sleeve's inner circumference. Then, cut the sleeve to the specified length, ensuring it is long enough to cover the entire fuel line, including some extra length for a secure fit.
By following these steps, you'll have a well-prepared fuel line that is ready for the sleeving process, ensuring a professional and leak-free installation.
Fuel Line Routing: A Guide to Connecting Your Fuel Cell
You may want to see also
Choose the Sleeve: Select a sleeve made of durable material suitable for fuel, considering size and flexibility
When it comes to sleeving a fuel line in concrete, choosing the right sleeve is crucial for ensuring the longevity and reliability of your fuel system. The sleeve acts as a protective barrier, safeguarding the fuel line from potential damage caused by the harsh environment of concrete. Here's a detailed guide on how to select the appropriate sleeve:
Material Selection: Opt for a sleeve made from a durable and flexible material specifically designed for fuel containment. Common choices include high-density polyethylene (HDPE) or polyvinyl chloride (PVC). These materials are known for their excellent resistance to fuel degradation, ensuring that the sleeve can withstand the corrosive nature of gasoline or diesel over time. HDPE, in particular, offers superior flexibility, making it ideal for accommodating any slight movements or vibrations within the concrete structure.
Size and Fit: The sleeve's size is critical to its effectiveness. Measure the fuel line's diameter accurately and choose a sleeve that provides a snug fit. A well-fitted sleeve prevents fuel leakage and ensures that the line remains secure within the concrete. Consider the length of the fuel line as well; you might need to purchase multiple sleeves and join them together to cover the entire length. Ensure that the sleeve's flexibility allows it to conform to the fuel line's shape without restricting its movement.
Flexibility and Movement: Concrete structures can experience thermal expansion and contraction, especially in varying weather conditions. Therefore, the sleeve should possess adequate flexibility to accommodate these movements without cracking or breaking. Look for sleeves with a certain degree of elasticity, allowing them to bend and stretch without compromising their structural integrity. This flexibility is vital to maintaining a continuous protective barrier around the fuel line.
Consider Environmental Factors: Depending on the specific application, you might need to account for additional environmental factors. For instance, if the fuel line is exposed to sunlight, opt for a sleeve with UV-resistant properties to prevent degradation. In cold climates, choose a material that can withstand freezing temperatures without becoming brittle. The right sleeve will ensure that your fuel line remains protected throughout its entire lifespan.
By carefully considering the material, size, and flexibility of the sleeve, you can effectively sleeve a fuel line in concrete, ensuring a reliable and long-lasting fuel supply system. Remember, the goal is to create a seamless and protective barrier that adapts to the unique challenges posed by the concrete environment.
Optimizing Performance: Choosing the Right Fuel Line for Your Predator 212
You may want to see also
Secure the Sleeve: Use mechanical fasteners or adhesive to firmly attach the sleeve to the fuel line
When it comes to sleeving a fuel line in concrete, ensuring a secure attachment of the sleeve to the fuel line is crucial for the overall integrity and safety of the system. This step is often overlooked, but it plays a vital role in preventing leaks and maintaining the efficiency of the fuel line. Here's a detailed guide on how to achieve this:
Mechanical Fasteners: One of the most common and reliable methods to secure the sleeve is by using mechanical fasteners. This involves drilling small holes along the length of the fuel line and inserting screws or bolts through the sleeve and into the fuel line. The fasteners should be chosen based on their strength and compatibility with the materials used. For instance, stainless steel fasteners are often preferred due to their corrosion resistance. Ensure that the holes are accurately drilled to avoid damaging the fuel line. Tighten the fasteners firmly, but be cautious not to overtighten, as it might cause damage. This method provides a strong mechanical bond, ensuring the sleeve stays in place even under pressure.
Adhesive Bonding: Another effective approach is to use specialized adhesives designed for this purpose. These adhesives are typically applied in a thin layer along the length of the fuel line, creating a bond between the sleeve and the fuel line. The key to success here is to use the right type of adhesive for the specific materials involved. Some adhesives might require activation by heat or light to initiate the bonding process. Follow the manufacturer's instructions carefully for optimal results. Allow sufficient time for the adhesive to cure, ensuring it reaches its full strength before handling the system. This method offers a strong bond and is often preferred for its simplicity and ease of application.
When using either mechanical fasteners or adhesive, it's essential to consider the specific requirements of your project. Factors such as the fuel line's diameter, the sleeve's material, and the environmental conditions will influence your choice. Always refer to the manufacturer's guidelines for the best results and safety. Additionally, regular inspections and maintenance are recommended to ensure the long-term effectiveness of the sleeve and the fuel line's integrity.
Finding the Perfect Fit: Husqvarna 240 Fuel Line Dimensions
You may want to see also
Install in Concrete: Position the sleeve in the concrete, ensuring it's centered and secure, then pour concrete around it
To install a fuel line sleeve in concrete, you must follow a precise process to ensure a secure and reliable connection. Here's a step-by-step guide:
First, locate the area where you want to install the fuel line. Ensure that the surface is clean and free of any debris or contaminants. Measure and mark the spot, ensuring it is centered and aligned with your fuel line's path. The sleeve should be positioned in a way that allows for easy access during installation and future maintenance.
Next, prepare the sleeve by cleaning it thoroughly. Remove any excess material or debris from the sleeve's interior and exterior. Ensure it is free from any sharp edges or protruding parts that could interfere with the concrete pour. The sleeve should be smooth and ready to be embedded.
Now, carefully place the sleeve into the marked position in the concrete. Use a mallet or a similar tool to gently tap the sleeve into place, ensuring it is centered and secure. The sleeve should fit snugly against the fuel line, providing a tight seal. Take extra care to avoid any misalignment, as this could compromise the integrity of the installation.
Once the sleeve is positioned correctly, it's time to pour the concrete. Use a high-quality concrete mix and follow the manufacturer's instructions for preparation and pouring. Start by filling the area around the sleeve with concrete, ensuring it is level with the surface. Then, pour the remaining concrete, filling the sleeve and surrounding area to the appropriate depth. Smooth the top surface with a trowel to create a seamless finish.
Finally, allow the concrete to cure according to the manufacturer's guidelines. This process may take several days, during which you should avoid any heavy traffic or impact on the concrete. Once cured, your fuel line sleeve will be securely embedded, providing a reliable pathway for fuel transport in your concrete structure. This method ensures a strong and durable connection, protecting the fuel line from potential damage.
Perfect Fuel Line Clamp for Honda XR50: Size Guide
You may want to see also
Test and Finish: Verify the fuel line's functionality, then seal and finish the concrete to protect the installation
Once the fuel lines are properly sleeved and installed within the concrete, it's crucial to conduct a thorough test to ensure their functionality and safety. Begin by starting the engine and allowing it to run for a period of time, typically around 15-20 minutes, to ensure the system reaches operating temperature. During this time, closely monitor the engine's performance, checking for any unusual noises, vibrations, or changes in idle quality. A well-functioning fuel system should operate smoothly and efficiently without any issues.
After the engine has been running, shut it off and check for any leaks around the fuel lines. Even a small drip can indicate a potential issue with the installation or the fuel lines themselves. Inspect the entire length of the lines, including connections and fittings, for any signs of damage or corrosion. If any leaks are detected, immediately address the problem by tightening connections or replacing damaged lines.
The next step is to verify the fuel pressure. Using a fuel pressure gauge, measure the pressure at the fuel rail or injectors. The specific pressure requirements will depend on your vehicle's make and model, but generally, a healthy fuel system should maintain pressure within the recommended range. If the pressure is too low, it may indicate a restriction in the fuel lines or a faulty fuel pump. Conversely, excessive pressure could be a sign of a blocked fuel filter or a malfunctioning pressure regulator.
Once the functionality of the fuel lines has been confirmed, it's time to focus on the concrete. The concrete should be sealed and finished to provide an additional layer of protection for the fuel lines. Start by applying a suitable concrete sealer designed for fuel line installations. Follow the manufacturer's instructions for application rates and techniques. Ensure that the sealer is evenly distributed over the entire surface of the concrete, paying extra attention to the areas where the fuel lines are sleeved.
After sealing, the concrete should be finished to create a smooth and durable surface. Use a trowel or a concrete finishing tool to level and smooth the top layer of concrete. Remove any excess sealer and ensure that the surface is free from any debris or contaminants. Properly finished concrete will not only enhance the aesthetics of the installation but also provide a protective barrier against corrosion and fuel contamination.
Finally, allow sufficient time for the concrete to cure and harden according to the manufacturer's guidelines. During this period, avoid any heavy traffic or impact on the concrete surface. Once cured, the fuel lines will be securely protected within the concrete, ensuring their longevity and reliability. Regular maintenance and inspections should still be conducted to identify and address any potential issues promptly.
Scooter Fuel Lines: Powering the Engine's Heart
You may want to see also
Frequently asked questions
Sleeve fitting is a technique used to protect and route fuel lines through concrete structures, ensuring the fuel supply remains intact and safe from damage.
Concrete structures can be harsh environments for fuel lines, as they may be exposed to vibrations, temperature fluctuations, and potential impact damage. Sleeve fitting provides a protective barrier, safeguarding the fuel line and preventing leaks or fuel contamination.
The choice of sleeve material depends on factors such as fuel type, temperature range, and environmental conditions. Common materials include flexible sleeves made of rubber, PVC, or specialized fuel-resistant compounds. It's essential to select a material that offers flexibility, durability, and compatibility with the fuel being transported.
Yes, it is possible to install a sleeve without completely removing the fuel line. This process involves carefully inserting the fuel line into the sleeve, ensuring a snug fit. Some sleeves feature pre-cut openings or adjustable designs to accommodate existing fuel lines, making the installation process more accessible and less invasive.