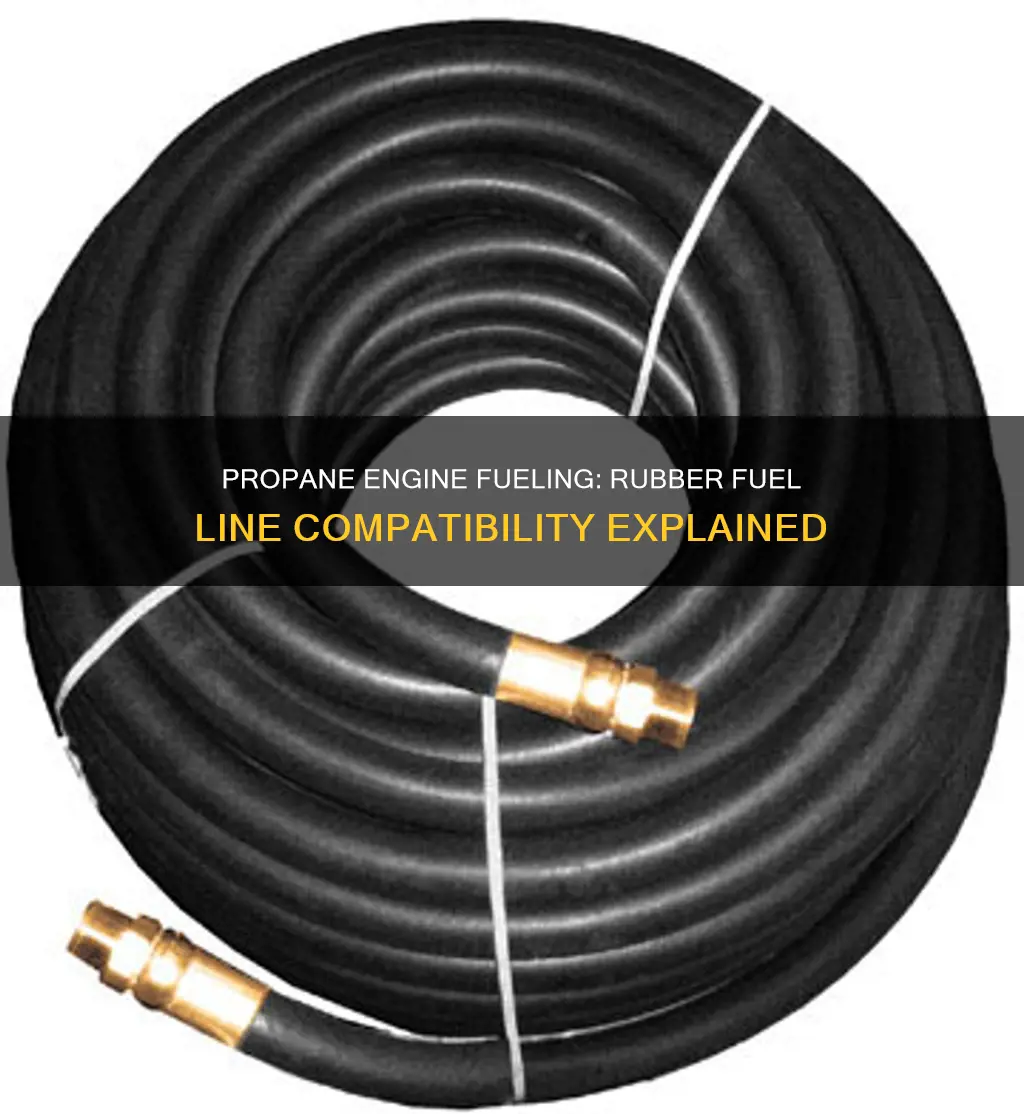
A rubber fuel line is a common component in many vehicle and engine systems, but its use with propane engines is a topic of interest and debate. Propane engines, also known as LPG (Liquefied Petroleum Gas) engines, require specific fuel lines that can handle the unique properties of propane compared to gasoline or diesel. This paragraph will explore the feasibility and potential challenges of using a rubber fuel line for propane engines, considering factors such as flexibility, durability, and compatibility with the fuel's properties.
Characteristics | Values |
---|---|
Material Compatibility | Rubber fuel lines are generally compatible with propane, but the specific type of rubber and additives should be checked to ensure no degradation over time. |
Flexibility | Propane engines often require flexible fuel lines due to the engine's movement and the fuel's low temperature. Rubber lines offer good flexibility. |
Temperature Resistance | Propane can be extremely cold, especially in winter. Rubber fuel lines can handle low temperatures, making them suitable for propane engines. |
Pressure Rating | The fuel line should have a pressure rating sufficient to handle the propane system's operating conditions, typically higher than gasoline systems. |
Chemical Resistance | Propane is less corrosive than gasoline, but the fuel line should still be resistant to the chemicals in the propane. Some rubber compounds may not be ideal. |
Cost | Rubber fuel lines are generally affordable and widely available, making them a cost-effective option for propane engine applications. |
Installation | Rubber lines are easy to install and can be cut to size, providing flexibility during the installation process. |
Maintenance | Regular inspection and maintenance are recommended to ensure the fuel line's integrity, especially in harsh environments. |
Availability | Rubber fuel lines are readily available in various sizes and lengths, making them convenient for propane engine modifications. |
Durability | With proper care, rubber fuel lines can last for several years, providing long-term reliability for propane engines. |
What You'll Learn
- Material Compatibility: Rubber fuel lines must be compatible with propane to prevent degradation
- Pressure Handling: Rubber's flexibility allows it to handle propane's pressure changes effectively
- Temperature Resistance: Rubber fuel lines can withstand propane's temperature range without cracking
- Flexibility: Propane engines benefit from rubber's flexibility for easy installation and movement
- Cost-Effectiveness: Rubber fuel lines are affordable and readily available for propane engine applications
Material Compatibility: Rubber fuel lines must be compatible with propane to prevent degradation
When considering the use of rubber fuel lines for propane engines, material compatibility is a critical factor that cannot be overlooked. Propane, being a highly volatile and flammable fuel, requires specific materials that can withstand its unique properties without compromising performance or safety. Rubber, a common material for fuel lines, must be carefully selected to ensure it is compatible with propane to prevent degradation and potential failures.
The compatibility of rubber with propane is essential to maintain the integrity of the fuel system. Rubber fuel lines are designed to be flexible and durable, allowing them to withstand the pressure and temperature variations associated with fuel transport. However, not all rubbers are created equal, and their chemical composition can vary significantly. Some rubbers may degrade when exposed to propane due to the fuel's ability to dissolve or weaken certain rubber compounds over time. This degradation can lead to fuel leaks, reduced performance, and potential safety hazards.
To ensure compatibility, it is crucial to choose rubber fuel lines made from materials that are specifically formulated to resist propane's corrosive effects. One such material is neoprene, a synthetic rubber known for its excellent resistance to fuels and oils. Neoprene fuel lines are often preferred for propane applications due to their ability to maintain flexibility and structural integrity even in the presence of propane. This compatibility ensures that the fuel lines can withstand the rigors of the engine's operation without compromising the overall system's reliability.
Additionally, the manufacturing process plays a vital role in material compatibility. Rubber fuel lines should be produced using techniques that minimize the risk of contamination and ensure consistent material properties. Proper curing and compounding of the rubber can enhance its resistance to propane, making it more suitable for long-term use in propane-powered engines.
In summary, when using rubber fuel lines for propane engines, material compatibility is key. Selecting the right rubber, such as neoprene, and ensuring proper manufacturing processes will help prevent degradation and ensure the fuel lines' longevity. By understanding the unique challenges posed by propane and choosing materials accordingly, engineers and enthusiasts can create a reliable and safe fuel system for propane-powered vehicles.
Can Brake Line Be Used for Fuel Line?
You may want to see also
Pressure Handling: Rubber's flexibility allows it to handle propane's pressure changes effectively
The use of rubber fuel lines in propane engines is a practical solution for several reasons, particularly when it comes to pressure handling. Propane engines operate under varying pressure conditions, and the flexibility of rubber is a key advantage in this regard. Rubber's inherent pliability allows it to adapt to these pressure changes, ensuring a consistent and reliable fuel supply. This is especially crucial in propane engines, where pressure fluctuations can occur due to the fuel's volatile nature and the engine's operating temperature.
The pressure handling capability of rubber fuel lines is a result of its material properties. Rubber is known for its ability to withstand a wide range of temperatures and pressures without compromising its structural integrity. This is achieved through the material's molecular structure, which enables it to deform and return to its original shape when subjected to external forces, such as pressure variations. This flexibility is particularly beneficial in propane engines, where the fuel system must accommodate rapid pressure changes during engine operation.
In propane engines, pressure fluctuations can occur due to the fuel's vaporization process and the engine's combustion cycle. As the propane vaporizes, it expands, leading to a temporary increase in pressure within the fuel lines. Rubber fuel lines can effectively absorb these pressure spikes, preventing potential damage to the engine or fuel system components. This is a critical aspect of ensuring the longevity and reliability of the engine, as it minimizes the risk of fuel leaks, engine misfires, or other performance issues caused by pressure-related damage.
Furthermore, the flexibility of rubber fuel lines contributes to the overall efficiency of the propane engine system. By effectively managing pressure changes, the fuel lines ensure a consistent fuel flow, optimizing the engine's performance. This consistency in fuel delivery is essential for maintaining the engine's power output and overall efficiency, especially during rapid acceleration or high-load conditions.
In summary, the pressure handling capability of rubber fuel lines is a significant advantage for propane engines. Its flexibility allows it to adapt to the dynamic pressure changes associated with propane fuel, ensuring a reliable and efficient engine operation. This makes rubber a suitable and practical choice for fuel lines in propane-powered applications, providing a cost-effective and durable solution for fuel delivery systems.
Mastering the Fuel Line: A Step-by-Step Guide to Removing It from Your Petcock
You may want to see also
Temperature Resistance: Rubber fuel lines can withstand propane's temperature range without cracking
The use of rubber fuel lines in propane engines is a practical solution for those seeking to optimize their vehicle's performance and longevity. One of the critical considerations when using propane as a fuel source is the material's ability to withstand the unique temperature variations it presents. Propane engines operate within a specific temperature range, and the fuel lines must be designed to handle these fluctuations without compromising their structural integrity.
Rubber, a versatile material, excels in this regard due to its inherent flexibility and resilience. It can accommodate the expansion and contraction of the fuel lines as the engine operates, ensuring a secure and reliable connection. This flexibility is crucial, especially in high-performance applications where rapid temperature changes are common. The rubber fuel lines can effectively bridge the gap between the fuel tank and the engine, providing a consistent and efficient fuel supply.
Furthermore, the temperature resistance of rubber is a key advantage. Propane engines often generate significant heat, and the fuel lines must be able to withstand these elevated temperatures without cracking or deteriorating. Rubber's ability to maintain its shape and structure under varying thermal conditions makes it an ideal choice. It can endure the extreme temperatures associated with propane combustion, ensuring a continuous and safe fuel supply to the engine.
In the context of propane engines, where temperature control is essential, rubber fuel lines offer a reliable and cost-effective solution. They provide a flexible and durable connection, allowing for efficient fuel delivery while withstanding the unique challenges posed by propane's temperature range. This makes rubber fuel lines a popular choice among enthusiasts and professionals alike, seeking to optimize their propane-powered vehicles.
When selecting rubber fuel lines for propane engines, it is essential to consider the specific requirements of the application. Factors such as line length, diameter, and reinforcement can be tailored to meet the demands of the engine and operating conditions. With proper installation and maintenance, rubber fuel lines can provide a long-lasting and reliable solution, ensuring optimal performance and safety in propane-powered systems.
Fuel Filter's Role: Ensuring Supply Line Efficiency
You may want to see also
Flexibility: Propane engines benefit from rubber's flexibility for easy installation and movement
The flexibility of rubber fuel lines is a crucial advantage when it comes to propane engines, offering a range of benefits that enhance performance and ease of use. Propane engines, known for their versatility and efficiency, often require fuel lines that can accommodate the unique demands of this fuel type. Rubber, with its inherent pliability, provides an ideal solution.
One of the key advantages is the ease of installation. Propane engines often have compact spaces, and the flexibility of rubber allows for quick and efficient connections. This is particularly useful when retrofitting existing engines or when space is limited. The rubber fuel line can be easily bent and shaped to fit the engine's layout, ensuring a secure and reliable connection without causing any strain or damage.
Furthermore, the flexibility of rubber is beneficial during the engine's operation. Propane engines may experience vibrations and movement, especially in mobile applications. Rubber's ability to absorb and dampen these vibrations ensures that the fuel line remains intact and secure. This feature prevents potential leaks and maintains a consistent fuel supply, which is essential for optimal engine performance.
In addition, the flexibility of rubber fuel lines allows for easier maintenance and repairs. Over time, fuel lines may need to be adjusted or replaced due to wear and tear. The pliable nature of rubber enables technicians to manipulate the lines, making it simpler to access and replace damaged sections without the risk of kinking or breaking rigid fuel lines.
In summary, the flexibility of rubber fuel lines is a significant advantage for propane engines. It simplifies installation, accommodates engine movement, and facilitates maintenance. This characteristic of rubber ensures that propane engines can operate efficiently and reliably, providing a cost-effective and environmentally friendly power source for various applications.
Silverado Z71 Fuel Drain: Location and Access
You may want to see also
Cost-Effectiveness: Rubber fuel lines are affordable and readily available for propane engine applications
Rubber fuel lines offer a cost-effective solution for propane engine applications, providing an affordable and readily available option for those seeking to upgrade their engine's fuel delivery system. The affordability of rubber fuel lines is a significant advantage, especially for DIY enthusiasts and those on a budget. These lines are often more budget-friendly compared to other materials like stainless steel or braided hoses, making them an attractive choice for those looking to enhance their engine's performance without breaking the bank.
In terms of availability, rubber fuel lines are widely accessible and can be sourced from various automotive suppliers and hardware stores. This ease of access ensures that engine owners can quickly find the necessary components to upgrade their propane engines. The convenience of purchasing these lines locally or online further contributes to their cost-effectiveness, as there is no need for extensive searching or specialized ordering.
The cost-effectiveness of rubber fuel lines extends beyond their initial purchase price. These lines are known for their durability and longevity, ensuring that the investment made in them will provide long-term value. Rubber is a flexible and resilient material, capable of withstanding the demands of fuel transport without compromising performance. This durability means that the fuel lines will not require frequent replacements, saving engine owners money over time.
Furthermore, the ease of installation is another factor that enhances the cost-effectiveness of rubber fuel lines. These lines are designed to be user-friendly, allowing engine owners to perform the installation themselves without the need for specialized tools or extensive knowledge. The simplicity of the installation process reduces labor costs, making the overall cost of upgrading to rubber fuel lines very competitive.
In summary, rubber fuel lines offer a cost-effective and practical solution for propane engine applications. Their affordability, wide availability, durability, and ease of installation make them an excellent choice for engine owners seeking to enhance their fuel delivery system without incurring significant expenses. By providing a reliable and budget-friendly option, rubber fuel lines contribute to the overall accessibility and affordability of propane engine modifications.
Fuel Hose Line Suppliers in Lansing, Michigan: Your One-Stop Shop
You may want to see also
Frequently asked questions
Yes, rubber fuel lines can be used for propane engines, but it's important to choose the right type of rubber and ensure proper installation. Propane fuel lines require specific materials that can withstand the unique properties of propane, such as its higher pressure and temperature compared to gasoline. Look for fuel lines made from high-temperature-resistant rubber compounds like EPDM (Ethylene Propylene Diene Monomer) or neoprene.
Rubber fuel lines offer several benefits for propane engines. They are flexible, allowing for easier routing and installation, especially in tight spaces. Rubber is also a cost-effective material, making it an affordable choice for propane systems. Additionally, rubber fuel lines are generally resistant to corrosion and can handle the chemicals present in propane fuel, ensuring a reliable connection.
While rubber fuel lines are suitable for propane, there are a few factors to keep in mind. Propane's higher pressure and temperature can cause rubber to degrade over time, so it's crucial to select a fuel line with an appropriate service temperature rating. Regular inspections and maintenance are recommended to identify any signs of wear or damage. It's also essential to ensure proper bonding or clamping techniques during installation to prevent leaks.