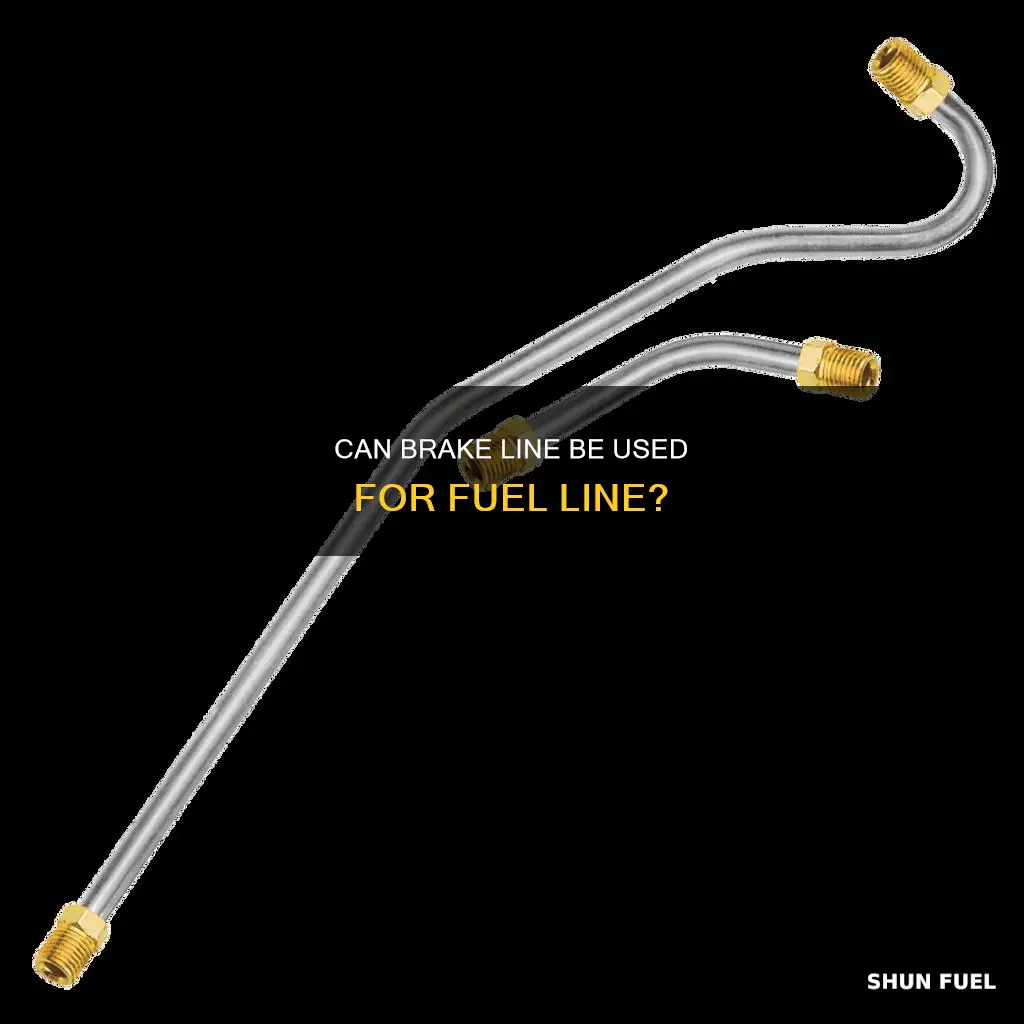
When it comes to vehicle maintenance, understanding the compatibility of different components is crucial. One common question that arises is whether brake lines can be used as fuel lines. While brake lines and fuel lines serve similar purposes in a vehicle, they are designed for different fluids and have distinct functions. Brake lines are specifically engineered to transmit hydraulic brake fluid, which is essential for the braking system's operation. On the other hand, fuel lines are designed to carry gasoline or diesel fuel from the tank to the engine. While both systems involve lines, they require specific fluids and have unique requirements. This introduction aims to explore the feasibility and considerations of using brake lines for fuel lines, highlighting the importance of proper component selection for optimal vehicle performance and safety.
Characteristics | Values |
---|---|
Material | Braided steel or stainless steel |
Diameter | Typically 1/4" to 3/8" |
Working Pressure | Up to 200-300 psi (depending on material) |
Temperature Range | -40°F to 400°F (-40°C to 204°C) |
Flexibility | Good flexibility for easy installation |
Corrosion Resistance | Excellent resistance to fuel-related chemicals |
Compatibility | Suitable for gasoline, diesel, and other fuels |
Ease of Installation | Straightforward and similar to brake line installation |
Cost | Generally more affordable than dedicated fuel lines |
Availability | Widely available in hardware stores and automotive shops |
DIY-Friendly | Can be installed by those with basic automotive skills |
What You'll Learn
- Material Compatibility: Ensure brake line material is compatible with fuel, avoiding corrosion or degradation
- Pressure Handling: Verify brake line can withstand fuel pressure without leaking or failing
- Flexibility: Check if the brake line is flexible enough to accommodate fuel line movement
- Clamping: Proper clamping is crucial to prevent fuel leaks at connections
- Length and Routing: Ensure the brake line is the correct length and routed away from heat sources
Material Compatibility: Ensure brake line material is compatible with fuel, avoiding corrosion or degradation
When considering the use of brake lines for fuel lines, material compatibility is a critical factor to ensure the safety and longevity of the fuel system. The primary concern is to prevent any adverse reactions between the brake line material and the fuel, which could lead to corrosion, degradation, or even fuel contamination. This is especially important as brake lines are designed to withstand high-pressure environments, and any compromise in material compatibility could have severe consequences.
Brake lines are typically made from materials such as steel, stainless steel, or synthetic compounds like polyurethane. These materials are chosen for their strength, durability, and resistance to corrosion. However, when it comes to fuel lines, the choice of material becomes even more crucial. Fuel is a corrosive substance, containing various chemicals that can react with certain materials, leading to deterioration over time.
One of the most common materials used for brake lines that is also compatible with fuel is stainless steel. This material is highly resistant to corrosion and can withstand the harsh conditions of fuel systems. It is important to ensure that the stainless steel used is of a high grade and meets industry standards to guarantee its effectiveness. Another option is polyurethane, which is known for its flexibility and resistance to fuel degradation. This material is often used in fuel lines due to its ability to maintain its integrity over time.
In some cases, brake lines made from synthetic materials may also be suitable for fuel applications. These materials are engineered to be compatible with various fuels and offer excellent resistance to corrosion and chemical degradation. However, it is essential to choose the right type of synthetic material, as not all are created equal, and some may not provide the necessary protection against fuel-related issues.
To ensure material compatibility, it is recommended to consult the manufacturer's guidelines and specifications for both the brake lines and the fuel system. This will help determine the most suitable materials and ensure that the chosen components can work harmoniously without compromising the performance and safety of the fuel system. Regular maintenance and inspections are also vital to identify any signs of corrosion or degradation and take appropriate action.
Marine Fuel Line Sealant: Choosing the Right Material for Your Boat
You may want to see also
Pressure Handling: Verify brake line can withstand fuel pressure without leaking or failing
When considering the use of brake lines for fuel lines, it's crucial to evaluate their ability to handle the unique pressures associated with fuel systems. Fuel lines operate under significantly higher pressures compared to brake lines, often ranging from 50 to 100 psi (pounds per square inch) or more, depending on the vehicle's specifications. Therefore, the brake line must be capable of withstanding these elevated pressures without compromising its structural integrity or leaking fuel.
To verify the pressure-handling capacity of a brake line, a comprehensive inspection and testing process should be conducted. Start by examining the brake line for any visible signs of damage, such as cracks, punctures, or corrosion. These issues can weaken the line's ability to contain pressure, leading to potential leaks or failures. Look for any signs of deterioration, especially in areas where the line connects to the fuel tank, fuel pump, or other fuel system components.
One effective method to assess pressure handling is to perform a pressure test. This involves connecting a pressure gauge to the brake line and gradually increasing the pressure to the expected fuel system levels. Monitor the line for any leaks or changes in pressure readings. If the line holds the pressure without any leaks, it can be considered suitable for fuel line applications. However, if leaks occur or the pressure drops significantly, the line may require replacement or reinforcement.
Additionally, consider the material and construction of the brake line. Some materials, such as steel or high-strength polymers, offer superior pressure resistance compared to others. Ensure that the chosen brake line is designed to handle the specific fuel pressures of the vehicle in question. Reinforcement techniques, such as braiding or spiral wrapping, can also enhance the line's ability to withstand pressure.
In summary, when using brake lines for fuel lines, it is essential to focus on pressure handling capabilities. Thorough inspections, pressure testing, and material selection are key to ensuring the brake line can safely and effectively contain fuel pressures without leaking or failing. This approach helps maintain the integrity of the fuel system and ensures the vehicle's overall performance and safety.
Powerful Engine Demands: Choosing the Right Fuel Line for 650HP Big Block
You may want to see also
Flexibility: Check if the brake line is flexible enough to accommodate fuel line movement
When considering the use of a brake line as a temporary fuel line, it's crucial to evaluate its flexibility to ensure it can accommodate the movement and vibrations associated with the fuel system. The brake line's flexibility is a critical factor in determining its suitability for this purpose.
To check the flexibility, start by examining the brake line's construction. Look for lines made from flexible materials such as rubber or a composite blend, which are designed to bend and move with the vehicle's components. These materials allow the brake line to adjust to the fuel line's position changes without becoming rigid or prone to damage.
Next, perform a visual inspection. Carefully examine the brake line for any signs of stiffness or rigidity. A flexible brake line should be able to bend around corners and contours without kinking or bending at sharp angles. If you notice any sections that appear stiff or rigid, it may indicate a lack of flexibility, which could lead to potential issues when accommodating the fuel line's movement.
Additionally, consider the length and routing of the brake line. Longer lines might require more flexibility to accommodate the fuel line's path, especially if it needs to traverse different vehicle compartments or follow complex routes. Ensure that the brake line's length and routing allow for sufficient movement without putting excessive strain on the material.
Finally, if possible, test the brake line's flexibility by gently bending and moving it. Try to mimic the fuel line's expected movement and observe if the brake line responds accordingly without showing signs of excessive stress or damage. This practical test can provide valuable insights into the line's ability to work as a temporary fuel line.
Optimizing Performance: Choosing the Right Fuel Line for Your 3/8 ID Engine
You may want to see also
Clamping: Proper clamping is crucial to prevent fuel leaks at connections
Clamping is an essential technique in fuel line installation and maintenance, ensuring a secure and leak-free connection. When working with fuel lines, proper clamping is crucial to prevent any potential leaks, which can lead to dangerous situations, including engine damage and fire hazards. The primary purpose of clamping is to create a tight seal around the fuel line connections, ensuring that the fuel remains contained within the system.
The process begins with selecting the appropriate clamp for the specific fuel line application. Clamps come in various types, such as metal, rubber, or plastic, each with unique characteristics. For fuel lines, metal clamps are commonly used due to their durability and ability to withstand high pressure. These clamps are designed with a serrated edge or a smooth finish, depending on the application, to provide a secure grip around the fuel line. It is vital to choose the right size and type of clamp to ensure a proper fit.
Once the clamp is selected, the clamping process involves several steps. First, the fuel line and any associated fittings or adapters should be thoroughly cleaned to remove any dirt, debris, or old sealant. This step is critical to ensure a clean and dry surface for the clamp. Next, the clamp is positioned around the fuel line, ensuring it is centered and aligned with the connection. The clamp should be tightened securely, but not excessively, to avoid damaging the fuel line or creating an overly tight seal that could restrict fuel flow.
Proper clamping technique requires the use of the right tools. A torque wrench is essential to ensure the clamp is tightened to the manufacturer's recommended specifications. Over-tightening can lead to fuel line damage, while under-tightening may result in leaks. The torque value for clamping should be consulted in the vehicle's service manual or the fuel line manufacturer's guidelines.
In addition to the initial clamping, regular maintenance and inspections are necessary. Over time, clamps can loosen due to vibration and fuel line movement. It is recommended to check the clamping system periodically, especially after any significant engine work or if the vehicle has been driven over rough terrain. Tightening the clamp as needed will help maintain a secure connection and prevent fuel leaks, ensuring the vehicle's safety and performance.
The Ultimate Guide to Thread Sealants for Fuel Lines
You may want to see also
Length and Routing: Ensure the brake line is the correct length and routed away from heat sources
When considering the use of a brake line for a fuel line, it is crucial to pay close attention to the length and routing of the brake line. The primary goal is to ensure the system's functionality and safety. Firstly, the brake line should be the appropriate length to reach the desired location without excessive tension or strain. This is essential to maintain the integrity of the line and prevent potential leaks or damage. Measure and compare the length required for the fuel line against the available brake line to ensure a proper fit.
Routing the brake line away from heat sources is a critical aspect of installation. Heat can cause the brake line to expand and contract, leading to potential damage or reduced performance. Identify and avoid any areas where the brake line might come into contact with hot components, such as exhaust systems, engine blocks, or transmission components. Proper insulation or protective sleeves may be necessary to shield the brake line from excessive heat.
The routing should also consider the flexibility and movement of the vehicle. The brake line should be able to move freely with the suspension and body of the vehicle without being kinked or pinched. Allow for adequate clearance and avoid sharp bends that could restrict flow or cause damage over time. Proper routing ensures that the brake line functions optimally and maintains its structural integrity.
In addition to length and routing, consider the material of the brake line. Different materials offer varying levels of flexibility and heat resistance. Choose a material that can withstand the specific conditions of your vehicle, including temperature extremes and potential chemical exposure. This ensures the brake line's longevity and reliability.
By carefully selecting the correct length and routing the brake line away from heat sources, you can ensure a functional and safe fuel line system. This attention to detail is vital for maintaining the performance and safety of your vehicle's critical components. Always refer to manufacturer guidelines and seek professional advice if needed to ensure a proper installation.
80 CB750 Fuel Line: Location and Connection Guide
You may want to see also
Frequently asked questions
While brake lines and fuel lines are both made of similar materials, they serve different purposes and have distinct requirements. Brake lines are designed to withstand high pressure and temperatures associated with braking systems, whereas fuel lines need to be flexible and resistant to fuel degradation. Therefore, it is generally not recommended to use brake lines for fuel lines as it may compromise the safety and performance of the fuel system.
Using brake lines for fuel lines can lead to several issues. Firstly, brake lines are not flexible enough to accommodate the movement of the engine and fuel tank, which can cause leaks or damage over time. Secondly, brake lines are not designed to handle the corrosive nature of fuel, which may lead to premature degradation and potential engine issues. It is crucial to use the correct type of line for each application to ensure optimal performance and safety.
No, standard brake lines are not suitable for fuel lines. Fuel lines require a different type of material that is flexible, resistant to fuel corrosion, and can withstand the temperature variations associated with fuel systems. It is important to consult the vehicle's manual or seek professional advice to determine the appropriate type of line for your specific fuel line application.
Modifying existing brake lines for fuel lines is not recommended. The original design and materials of brake lines are tailored for braking applications and may not meet the requirements of fuel lines. Attempting to modify them can lead to safety hazards and may void warranties. It is best to install the correct type of fuel lines as per the manufacturer's guidelines to ensure a reliable and safe fuel system.