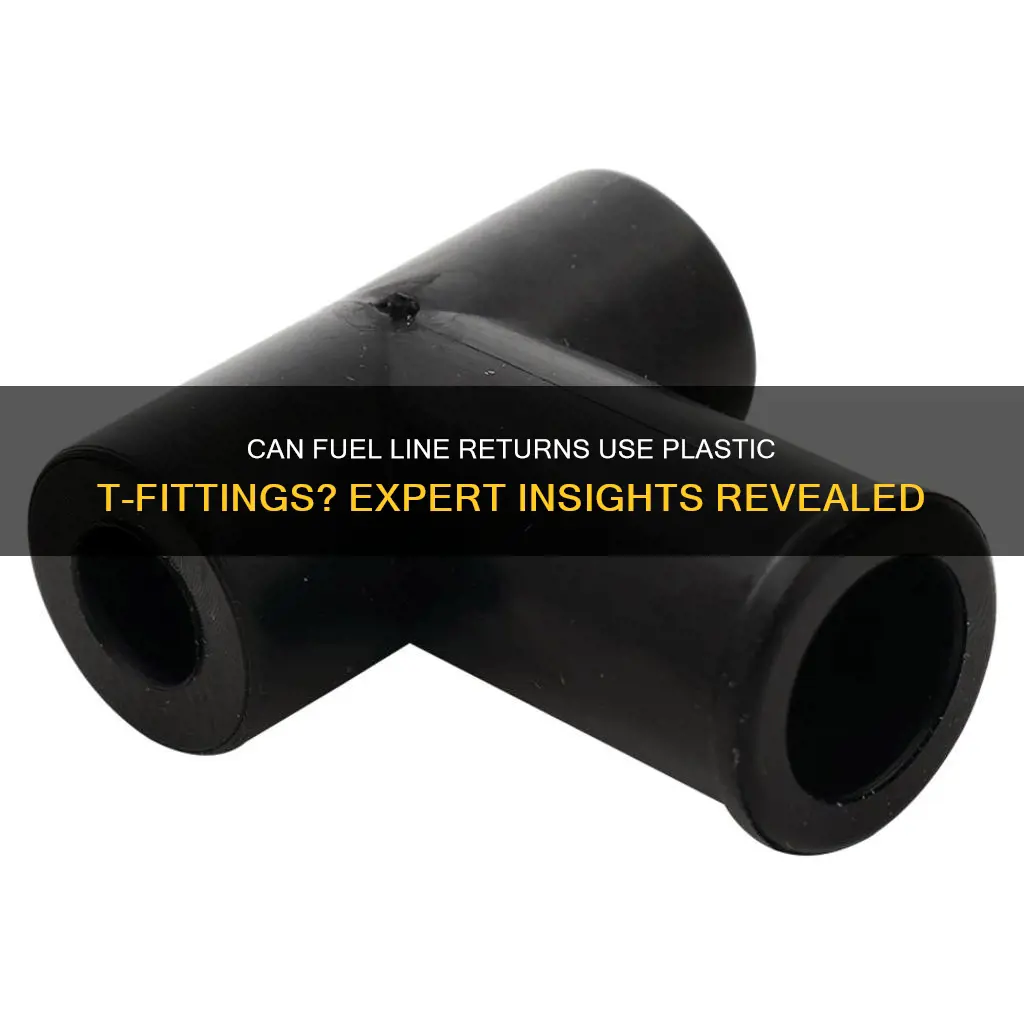
When it comes to automotive maintenance, understanding the compatibility of different materials is crucial. One common question that arises is whether a fuel line return can use a plastic T-fitting. This query delves into the feasibility of using plastic components in a critical system, considering the potential risks and benefits. Plastic T-fittings, known for their durability and ease of installation, are often preferred for their cost-effectiveness. However, when it comes to fuel lines, the choice of materials becomes even more critical due to the potential hazards of fuel leaks and the need for materials that can withstand the corrosive effects of gasoline. This paragraph aims to explore the practicality and safety considerations of using plastic T-fittings in fuel line returns, shedding light on the factors that determine their suitability in automotive applications.
Characteristics | Values |
---|---|
Material | Plastic |
Compatibility | Fuel Line Return |
Application | Automotive |
Type | T-Fitting |
Function | Connects fuel lines |
Advantages | Lightweight, corrosion-resistant, easy to install |
Considerations | May not be suitable for high-pressure systems |
Availability | Widely available in automotive stores |
Cost | Affordable |
Maintenance | Low maintenance required |
What You'll Learn
- Material Compatibility: Plastic T-fitting's compatibility with fuel line return materials
- Durability: Long-term durability of plastic T-fitting in fuel line return systems
- Temperature Resistance: Ability to withstand fuel line return temperatures without degradation
- Flexibility: Plastic T-fitting's flexibility for easy installation and maintenance
- Cost-Effectiveness: Plastic T-fitting's cost compared to metal alternatives in fuel line returns
Material Compatibility: Plastic T-fitting's compatibility with fuel line return materials
When considering the use of plastic T-fittings for fuel line returns, it's crucial to evaluate the compatibility of these fittings with the materials commonly used in fuel lines. The primary concern is ensuring that the materials used in the T-fittings are compatible with the fuel being transported, as well as the overall system's integrity.
One of the key materials used in fuel lines is rubber or synthetic rubber compounds. These materials are chosen for their flexibility and ability to withstand the corrosive nature of fuel. When using plastic T-fittings, it is essential to select a type of plastic that is compatible with rubber. Certain plastics, such as polypropylene (PP) or certain grades of polyvinyl chloride (PVC), can be compatible with rubber when properly bonded or sealed. However, it is important to note that not all plastics are suitable, and some may lead to degradation or leaching of chemicals into the fuel over time.
Another critical aspect is the compatibility of the plastic T-fitting with the specific fuel being used. Different fuels have varying chemical compositions, and some may be more aggressive than others. For instance, ethanol-blended fuels can be more corrosive and may require specific plastic materials that can withstand these conditions. Common plastics like ABS or certain polyolefins might not be suitable for ethanol-blended fuels and could lead to premature degradation or failure.
Additionally, the temperature range of the fuel should be considered. Fuel lines and returns can experience varying temperatures, especially in different climates. Some plastics may become brittle or lose their flexibility at lower temperatures, while others may not withstand high temperatures without deformation. It is essential to choose a plastic T-fitting that can handle the expected temperature range of the fuel system.
In summary, when using plastic T-fittings for fuel line returns, careful consideration of material compatibility is necessary. The chosen plastic should be compatible with the fuel's chemical properties and the overall system's operating conditions, including temperature and pressure. Consulting manufacturer guidelines and industry standards can provide valuable insights to ensure the safe and efficient operation of the fuel system.
Fuel Line Degradation: A Hidden Threat in Transmission Fluids
You may want to see also
Durability: Long-term durability of plastic T-fitting in fuel line return systems
The long-term durability of plastic T-fittings in fuel line return systems is a critical consideration for vehicle owners and mechanics alike. These fittings are used to connect the fuel line return to the fuel tank, ensuring that excess fuel is properly directed back to the tank. While plastic T-fittings offer several advantages, such as ease of installation and lightweight design, their durability in the harsh environment of a fuel system is a concern.
One of the primary factors affecting the durability of plastic T-fittings is the material used. Common materials include polypropylene and nylon, which are known for their resistance to fuel degradation and chemical corrosion. These materials are chosen for their ability to withstand the corrosive effects of fuel, including ethanol blends, which are increasingly common in modern vehicles. The resistance to corrosion ensures that the T-fitting remains intact and functional over the long term, preventing leaks and potential engine damage.
Another aspect of durability is the design and construction of the T-fitting. High-quality fittings are often designed with robust internal threads and a sturdy body to withstand the pressure and vibrations encountered in the fuel system. Some manufacturers use reinforced materials or add internal support structures to enhance the fitting's strength. These design considerations are crucial, especially in high-performance vehicles or those operating in extreme conditions, where the fuel system experiences more stress.
Environmental factors also play a significant role in the long-term durability of plastic T-fittings. Temperature fluctuations, especially in colder climates, can cause fuel to expand and contract, putting pressure on the fittings. Plastic materials with good temperature resistance can maintain their structural integrity under these conditions. Additionally, exposure to sunlight and UV radiation, particularly in outdoor environments, may lead to degradation over time. Fittings with UV-resistant coatings or materials can mitigate this issue.
In summary, the long-term durability of plastic T-fittings in fuel line return systems is achievable through the use of appropriate materials and design considerations. Polypropylene and nylon, with their fuel resistance and chemical stability, are excellent choices for these fittings. Proper design, including robust construction and internal support, ensures the fitting can withstand pressure and vibrations. Furthermore, addressing environmental factors such as temperature and UV exposure is essential to guarantee the fitting's longevity. By selecting high-quality materials and fittings, vehicle owners and mechanics can ensure reliable and safe fuel system operation.
Braided Fuel Lines: Unraveling the Benefits of Braiding
You may want to see also
Temperature Resistance: Ability to withstand fuel line return temperatures without degradation
The temperature resistance of a fuel line return system is a critical factor in ensuring the longevity and reliability of the fuel system in an engine. When considering the use of plastic T- fittings in the fuel line return, it is essential to understand the temperature range these components can withstand without degradation.
Fuel line returns often operate at elevated temperatures due to the engine's heat and the combustion process. The return lines carry the fuel-air mixture post-combustion, which can be significantly hotter than the ambient temperature. Therefore, the materials used in these lines and fittings must be able to handle these high temperatures without compromising their structural integrity.
Plastic T- fittings, while lightweight and cost-effective, have varying temperature resistance properties. Some common types of plastics used in these fittings include polyvinyl chloride (PVC), polypropylene (PP), and nylon. PVC, for instance, has a relatively low temperature resistance, typically rated for temperatures up to 140°F (60°C). Beyond this, it can start to degrade, leading to potential fuel leaks and system failures. On the other hand, PP offers better temperature resistance, with a typical rating of up to 220°F (104°C), making it more suitable for higher-temperature applications.
Nylon, another popular choice, provides excellent temperature resistance, often rated for temperatures up to 400°F (204°C) or higher. This makes nylon an ideal material for fuel line returns, as it can withstand the extreme temperatures encountered in engine operations. However, it is crucial to check the specific ratings for the particular brand and grade of plastic used in the T- fitting to ensure it meets the engine's temperature requirements.
In summary, when using plastic T- fittings in the fuel line return, it is imperative to select materials with adequate temperature resistance. This ensures that the fittings can withstand the high temperatures of the fuel-air mixture without degradation, thus maintaining the efficiency and safety of the engine's fuel system. Always refer to the manufacturer's specifications and consult with experts to make informed decisions regarding the choice of materials for critical engine components.
Duramax Fuel Line Pressure: Testing and Troubleshooting Guide
You may want to see also
Flexibility: Plastic T-fitting's flexibility for easy installation and maintenance
The use of plastic T-fittings in fuel line returns offers a significant advantage in terms of flexibility, making installation and maintenance processes more efficient and less complex. This flexibility is particularly beneficial when dealing with fuel systems that require intricate routing or when working in confined spaces.
One of the key advantages of plastic T-fittings is their ability to conform to various shapes and angles. This feature allows technicians to navigate around obstacles and fit the fuel lines into tight spaces without the need for extensive bending or manipulation. The flexibility of these fittings ensures that the fuel lines can be routed efficiently, reducing the risk of damage and ensuring a neat and organized system.
During installation, the flexibility of plastic T-fittings simplifies the process. Technicians can easily manipulate the fittings to reach the desired connection points, even in hard-to-reach areas. This ease of installation saves time and effort, making the overall setup process more efficient. Additionally, the flexibility allows for quick adjustments, ensuring a secure and tight connection without the need for excessive force, which could potentially damage the fuel lines.
Maintenance and repairs also benefit from the flexibility of these fittings. When a fuel line needs to be replaced or repaired, the plastic T-fitting can be easily removed and replaced without causing extensive disruption to the entire system. This capability is crucial for minimizing downtime and ensuring that the fuel system remains operational during maintenance activities. The flexibility allows for a more straightforward disassembly and reassembly process, making it a preferred choice for professionals working on fuel systems.
Furthermore, the flexibility of plastic T-fittings contributes to the longevity of the fuel system. By accommodating minor movements and vibrations, these fittings help to reduce stress on the fuel lines, preventing potential damage over time. This feature is especially important in applications where fuel lines may experience thermal expansion or contraction due to temperature changes. The flexibility ensures that the fittings can adapt, providing a more reliable and durable connection.
Unraveling the Ultimate Marine Fuel Line Flexibility: A Comprehensive Guide
You may want to see also
Cost-Effectiveness: Plastic T-fitting's cost compared to metal alternatives in fuel line returns
When considering the use of plastic T-fittings for fuel line returns, one of the primary factors to evaluate is the cost-effectiveness compared to metal alternatives. Plastic T-fittings offer a more affordable option, especially when used in fuel line returns. The cost of plastic fittings is generally lower than that of metal fittings, making them an attractive choice for those looking to reduce expenses without compromising on quality. This is particularly beneficial for projects with tight budgets or for those who require a large quantity of fittings.
The cost advantage of plastic T-fittings becomes even more apparent when considering the long-term savings. Plastic fittings are known for their durability and resistance to corrosion, which means they can withstand the harsh conditions often present in fuel systems. This durability ensures that the fittings will have a longer lifespan, reducing the need for frequent replacements and subsequent costs. Over time, the initial lower cost of plastic fittings can add up to significant savings compared to metal alternatives, especially in applications where fuel lines are exposed to varying temperatures and environmental conditions.
In addition to the initial cost, the ease of installation and maintenance should also be considered. Plastic T-fittings are typically lightweight and easy to manipulate, making the installation process quicker and less labor-intensive. This can result in reduced labor costs, especially in complex fuel line systems. Furthermore, the maintenance of plastic fittings is generally simpler, as they are less prone to rust and degradation, ensuring that the fuel line returns remain efficient and functional over an extended period.
While the initial investment in plastic T-fittings might be lower, it is essential to consider the overall quality and performance. Modern plastic fittings are engineered to meet or exceed the performance standards of their metal counterparts. They can handle high-pressure fuel systems and provide a secure connection, ensuring that the fuel line returns are reliable and safe. The combination of cost-effectiveness, durability, and ease of use makes plastic T-fittings a compelling choice for fuel line returns, offering a practical and economical solution for various applications.
In summary, when evaluating the cost-effectiveness of plastic T-fittings for fuel line returns, the initial lower cost and long-term savings are significant advantages. The durability and ease of installation of plastic fittings contribute to a more efficient and cost-efficient fuel system. By considering these factors, engineers and project managers can make informed decisions, ensuring that the chosen fittings provide both economic and practical benefits for their fuel line return applications.
Evo Fuel Line Size: Essential Guide for Optimal Performance
You may want to see also
Frequently asked questions
Yes, a plastic T-fitting can be used for a fuel line return, but it is important to consider the specific requirements and compatibility with the fuel system. Plastic fittings are generally suitable for fuel lines in non-corrosive environments and can provide a secure connection. However, it is crucial to ensure that the plastic T-fitting is designed for fuel applications and meets the necessary pressure and temperature requirements.
Plastic T-fittings offer several benefits for fuel line returns. They are lightweight, easy to install, and provide a reliable connection. Plastic fittings are often more flexible than metal ones, allowing for easier routing and adjustment. Additionally, they are resistant to corrosion and can help prevent fuel contamination from metal fittings over time.
While plastic T-fittings are generally reliable, there are a few considerations. Plastic can be more susceptible to cracking or degradation over time, especially in high-temperature or UV-exposed environments. It is essential to choose a high-quality, fuel-rated plastic material to ensure longevity. Additionally, plastic fittings may not be as robust as metal ones, so they might not be suitable for high-pressure or extreme conditions. Proper maintenance and regular inspections are recommended to identify any potential issues.