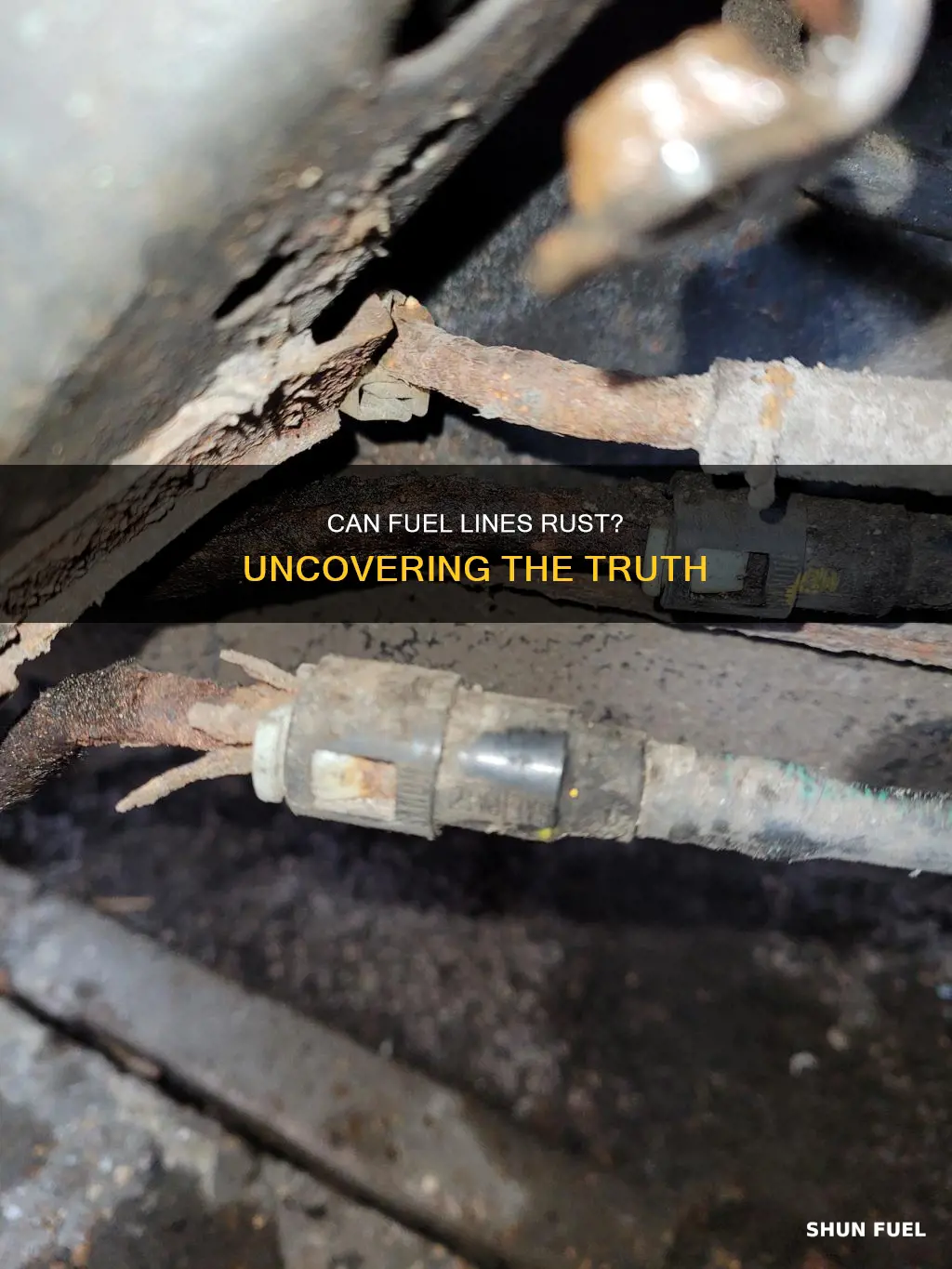
Fuel lines, an often overlooked component of a vehicle's fuel system, are susceptible to rust and corrosion, which can lead to significant performance issues. Over time, the metal in fuel lines can deteriorate due to exposure to moisture, chemicals, and the corrosive effects of fuel itself. This rusting process can result in a variety of problems, including reduced fuel flow, engine misfires, and even complete engine failure in severe cases. Understanding the causes and consequences of rust in fuel lines is essential for vehicle owners to ensure their vehicles run efficiently and safely.
Characteristics | Values |
---|---|
Rusting Potential | Yes, fuel lines can rust over time due to exposure to moisture, contaminants, and the corrosive nature of fuel. |
Factors Affecting Rust | Moisture absorption, fuel type (e.g., ethanol blends), temperature fluctuations, and the presence of corrosive substances like water or fuel contaminants. |
Signs of Rust Damage | Reduced fuel flow, engine misfires, hard starting, or a noticeable decrease in engine performance. |
Prevention Measures | Using fuel line inhibitors, regular fuel line inspections, maintaining a clean fuel system, and ensuring proper fuel storage and handling. |
Replacement Considerations | If rust is detected, it's essential to replace the fuel lines to prevent further damage and ensure optimal engine performance. |
What You'll Learn
Material: Rust susceptibility varies by fuel line material
The material of a fuel line plays a crucial role in determining its susceptibility to rust and corrosion. Different materials have varying levels of resistance to rust formation, which can significantly impact the performance and longevity of the fuel system. Here's an overview of how different materials fare in terms of rust susceptibility:
Metal Fuel Lines: Metal fuel lines, often made of steel or aluminum, are known for their durability. However, they are inherently susceptible to rust due to their metallic nature. Over time, exposure to fuel, moisture, and oxygen can lead to the formation of rust, especially in areas with poor ventilation or where the fuel lines are in close contact with other metal components. Regular inspection and maintenance are essential to prevent rust buildup, as it can compromise the structural integrity of the fuel lines and lead to fuel leaks.
Rubber or Synthetic Rubber Fuel Lines: Rubber and synthetic rubber fuel lines are commonly used due to their flexibility and resistance to abrasion. These materials are generally more resistant to rust compared to metals. The natural oils in rubber act as a barrier, preventing moisture absorption and subsequent rust formation. However, it's important to note that older rubber fuel lines may degrade over time, becoming more susceptible to fuel leaks and cracks, which can indirectly contribute to rust issues.
Braided Fuel Lines: Braided fuel lines, often made of stainless steel or other corrosion-resistant materials, are popular for their flexibility and strength. The braided construction provides excellent protection against abrasion and damage from engine components. Additionally, the use of stainless steel or similar alloys makes these lines highly resistant to rust. This makes braided fuel lines an excellent choice for high-performance vehicles or those operating in harsh environments.
Plastic or Composite Fuel Lines: Plastic and composite fuel lines are gaining popularity due to their lightweight and corrosion-resistant properties. These materials are engineered to withstand the harsh conditions of fuel systems without rusting. The lack of metallic components in these lines makes them ideal for long-term use, especially in modern vehicles with more complex fuel systems. However, it's important to choose high-quality materials to ensure long-lasting performance.
Understanding the material composition of your fuel lines is essential for proper maintenance and longevity. Regular inspections, especially in areas prone to moisture or corrosion, can help identify any signs of rust or degradation. Depending on the material, appropriate measures such as cleaning, coating, or replacement can be taken to ensure the fuel system remains in optimal condition.
Mastering Chevy Fuel Line Disconnect: A Comprehensive Guide
You may want to see also
Environment: Moisture and corrosive elements accelerate rust
Moisture and corrosive elements in the environment play a significant role in the rusting process of fuel lines, which can have detrimental effects on vehicle performance and longevity. When fuel lines are exposed to these conditions, they become susceptible to corrosion, leading to potential issues.
In environments with high humidity or frequent exposure to moisture, the fuel lines are at risk. Moisture acts as an electrolyte, facilitating the flow of electrons and accelerating the electrochemical reaction that causes rust. This reaction is particularly prevalent in areas with high humidity, where the air contains a significant amount of water vapor. Over time, the moisture can penetrate the protective coatings on fuel lines, leading to internal corrosion.
Corrosive elements, such as salt and other minerals, found in coastal regions or areas with high pollution, further exacerbate the problem. These elements can easily adhere to the surface of fuel lines, especially if the lines are not properly sealed or protected. When exposed to moisture, these corrosive substances create an ideal environment for rust formation. The combination of moisture and corrosive elements accelerates the breakdown of the fuel line material, often leading to rust formation and potential damage.
Regular maintenance and inspection are crucial to preventing rust-related issues. Vehicle owners should ensure that fuel lines are properly insulated and sealed to minimize exposure to moisture and corrosive elements. Additionally, keeping the vehicle's fuel system clean and free of contaminants can help prevent internal corrosion. Regularly checking for any signs of moisture or corrosion on the fuel lines and addressing any issues promptly can help maintain the integrity of the fuel system.
In summary, the environment plays a critical role in the rusting of fuel lines. Moisture and corrosive elements accelerate the corrosion process, leading to potential performance issues and damage. By understanding these environmental factors and taking proactive measures, vehicle owners can ensure the longevity and reliability of their fuel systems.
Ford Fuel Line Fitting Removal: A Step-by-Step Guide
You may want to see also
Age: Older fuel lines may show signs of rust
As fuel lines age, they are more susceptible to rust and corrosion, which can lead to a variety of issues in a vehicle's fuel system. Older fuel lines, often made of steel or other metal materials, can develop rust spots or a general deterioration over time, especially if they are exposed to moisture or have been damaged. This is a common problem in vehicles that have been in service for many years, as the constant vibration and movement of the engine can cause stress on the fuel lines, leading to potential weaknesses.
The presence of rust in older fuel lines is often an indication of a more serious issue. When fuel lines rust, it can result in a decrease in fuel flow, as the rusted areas may become blocked or narrowed, restricting the smooth passage of fuel from the tank to the engine. This can lead to poor engine performance, such as reduced power, acceleration issues, and even potential stalling. In some cases, the rust may also cause the fuel lines to become brittle and more prone to cracking or leaking, which can be a dangerous and costly repair.
To address this problem, it is recommended to inspect the fuel lines regularly, especially in older vehicles. Look for any signs of rust, corrosion, or damage along the length of the fuel lines. If you notice any rust spots or a general deterioration, it is advisable to replace the fuel lines with new ones to ensure optimal fuel delivery and prevent further issues. Regular maintenance and timely replacements can help extend the life of the vehicle and maintain its performance.
In addition to visual inspections, it is beneficial to use a fuel line inspection kit, which can help identify any internal issues within the fuel lines. These kits often include a small camera or a mirror that can be inserted into the fuel lines to check for blockages, corrosion, or other internal damage. By using such tools, you can ensure that the fuel lines are in good condition and address any potential problems before they cause significant engine issues.
For those who prefer a more proactive approach, regular fuel line maintenance can be a preventative measure. This may involve using fuel line coatings or inhibitors that help protect the metal from corrosion. These products can be applied to the interior of the fuel lines, creating a protective barrier that reduces the risk of rust formation. However, it is essential to follow the manufacturer's guidelines for application and usage to ensure the effectiveness of these treatments.
Torture Fuel's 99 Ram: Unleashing Power and Performance
You may want to see also
Maintenance: Regular inspections can prevent rust buildup
Regular maintenance and inspections are crucial for preventing rust buildup in fuel lines, which can lead to costly repairs and potential safety hazards. Rust, a natural process of oxidation, can occur in fuel lines over time, especially if the fuel contains moisture or if the lines are not properly maintained. This issue is often overlooked, but it can have significant consequences for vehicle performance and longevity.
The first step in preventing rust is to ensure that the fuel system is regularly checked and maintained. This includes inspecting the fuel lines for any signs of corrosion or damage. Visual inspections are a simple yet effective method; look for any discolouration, pitting, or flaking on the fuel lines' surfaces. These visual cues can indicate the presence of rust, especially in areas where the lines are exposed to moisture or where there is a lack of protective coatings. It is recommended that vehicle owners or mechanics perform these inspections at regular intervals, such as during routine oil changes or at least once a year.
During the inspection, pay close attention to the fuel tank and its surroundings. Over time, fuel tanks can develop internal corrosion, which may lead to rust in the fuel lines. Check for any signs of leakage or moisture accumulation, as these could be indicators of a more serious issue. Additionally, inspect the fuel pump and its connections, as these components are susceptible to rust and can cause performance problems if not maintained properly.
If any signs of rust are detected, immediate action should be taken. Cleaning the fuel lines is often the first step. This can be done by removing the lines and using a suitable cleaner to remove any rust or corrosion. After cleaning, ensure that the lines are thoroughly dried to prevent moisture retention, which can accelerate rust formation. In some cases, replacing the affected fuel lines may be necessary, especially if the damage is extensive.
Furthermore, regular use of fuel stabilizers can be beneficial in preventing rust. These additives help to inhibit oxidation and keep the fuel fresh, reducing the chances of moisture accumulation. By incorporating these preventative measures into a vehicle's maintenance routine, owners can ensure that their fuel lines remain in optimal condition, extending the life of their vehicles and avoiding potential breakdowns caused by rust-related issues.
Fuel Line Tool Size Guide: Scion TC
You may want to see also
Corrosion Inhibitors: Additives can reduce rust in fuel lines
Corrosion inhibitors are an essential component in maintaining the health and longevity of fuel lines in vehicles. These additives play a crucial role in preventing rust and corrosion, which can significantly impact the performance and reliability of a vehicle's fuel system. When fuel lines are exposed to moisture, especially in older vehicles or those with compromised seals, the risk of rust formation increases. This is because moisture acts as an electrolyte, facilitating the flow of electrons and promoting the electrochemical reaction that leads to corrosion.
The primary function of corrosion inhibitors is to create a protective barrier on the surface of the fuel lines, preventing direct contact between the metal and moisture. These additives are typically oil-based and contain various chemical compounds that have a strong affinity for metal surfaces. When introduced into the fuel system, they form a thin, protective layer that adheres to the inner walls of the fuel lines. This layer acts as a physical barrier, preventing water and other corrosive substances from coming into direct contact with the metal, thus inhibiting the electrochemical processes that cause rust.
Inhibitors work by several mechanisms. Firstly, they can form a stable, non-reactive layer on the metal surface, which effectively blocks the moisture and prevents its interaction with the metal. This layer acts as a physical barrier, similar to a protective coat. Secondly, some inhibitors release active molecules that react with the metal surface, forming a stable compound that is less susceptible to corrosion. These active molecules can neutralize the corrosive effects of moisture and other contaminants, ensuring that the fuel lines remain in optimal condition.
The effectiveness of corrosion inhibitors is often measured by their ability to provide long-lasting protection. When added to the fuel system, these additives circulate throughout the engine, ensuring that every part of the fuel line is coated and protected. This comprehensive coverage helps to prevent localized corrosion, which can occur if certain areas of the fuel line are more exposed to moisture than others. By maintaining a consistent protective layer, inhibitors contribute to the overall integrity of the fuel system.
In summary, corrosion inhibitors are a vital tool in combating rust and corrosion in fuel lines. Their ability to create a protective barrier and neutralize corrosive elements ensures that fuel lines remain in excellent condition, even in the presence of moisture. Regular use of these additives, especially in older vehicles, can significantly extend the lifespan of the fuel system and maintain optimal engine performance. It is a simple yet effective method to address the issue of rust in fuel lines, providing peace of mind to vehicle owners.
Toyota Corolla Fuel Line Location: 1989 Model Guide
You may want to see also
Frequently asked questions
Yes, fuel lines can be susceptible to rust, especially if they are made of steel or other ferrous materials. Rusting can occur when the fuel lines are exposed to moisture, especially in environments with high humidity or if there is a leak in the fuel system that allows water to enter.
Rusted fuel lines may exhibit several symptoms. One common sign is a decrease in fuel pressure, which can lead to poor engine performance or stalling. You might also notice a sweet or metallic odor coming from the fuel tank, indicating the presence of rust or corrosion. Additionally, visual inspection may reveal small holes or pitting on the fuel line surface.
Preventive measures are essential to avoid rust-related issues. Firstly, ensure that your fuel tank is properly sealed to prevent moisture absorption. Regularly inspect the fuel lines for any signs of damage or corrosion, especially in areas prone to moisture accumulation. Using fuel line protectors or covers can also provide an extra layer of protection against rust.
While it is possible to use rust removers on fuel lines, it is generally recommended to replace them if rusting is detected. Rust removers can be temporary solutions and may not address the underlying issue. It's best to consult a professional mechanic to determine the best course of action, which may include replacing the fuel lines with new ones made of rust-resistant materials.