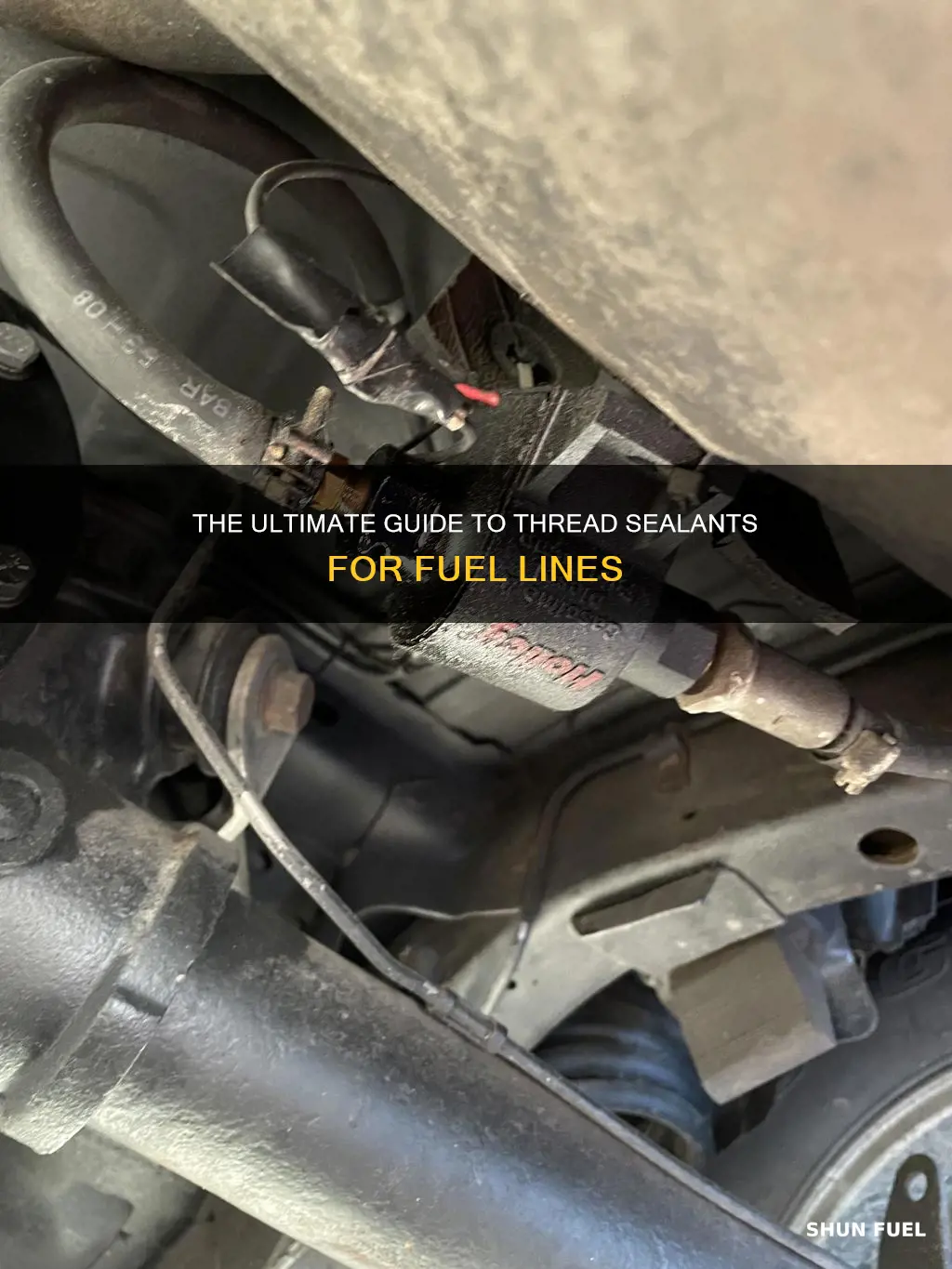
When it comes to maintaining the integrity of fuel lines in vehicles, choosing the right thread sealant is crucial. Fuel lines are vital components that transport gasoline or diesel from the tank to the engine, and any damage or leaks can lead to costly repairs and potential safety hazards. The best thread sealant for fuel lines should provide a strong, durable bond that can withstand the pressure and temperature fluctuations associated with fuel systems. It should also be resistant to fuel degradation and not compromise the flow of fuel. This introduction sets the stage for a detailed exploration of the ideal thread sealant, considering factors such as material compatibility, ease of application, and long-term performance.
What You'll Learn
- Material Compatibility: Ensure the sealant is compatible with the fuel line material to prevent damage
- Temperature Resistance: Choose a sealant that can withstand fuel line temperatures for optimal performance
- Flexibility: Opt for a flexible sealant to accommodate fuel line movement without cracking
- Chemical Resistance: Select a sealant resistant to fuel chemicals to prevent degradation and leaks
- Durability: Prioritize a durable sealant that can withstand fuel line pressure and vibrations
Material Compatibility: Ensure the sealant is compatible with the fuel line material to prevent damage
When it comes to choosing the best thread sealant for fuel lines, material compatibility is a critical factor that cannot be overlooked. Fuel lines are typically made from various materials, including rubber, plastic, and metal, and the sealant must be compatible with the specific material of the fuel line to ensure optimal performance and prevent damage.
One of the primary concerns with using the wrong sealant is the potential for chemical reactions between the sealant and the fuel line material. Some sealants may contain chemicals that can react with the fuel line material, leading to degradation, hardening, or even melting of the fuel line. This can result in fuel leaks, reduced performance, and potential safety hazards. For example, if a sealant is not compatible with a rubber fuel line, it may cause the rubber to become brittle and crack over time, allowing fuel to leak and potentially causing engine misfires or other issues.
To ensure compatibility, it is essential to consider the material composition of the fuel line. Rubber fuel lines, for instance, require a sealant that is specifically formulated for rubber. These sealants are designed to adhere to the rubber surface and create a strong bond without causing any adverse reactions. Similarly, plastic fuel lines may require a sealant that is compatible with the specific type of plastic used, such as polyethene or polypropylene. Using a sealant that is not designed for the particular plastic material can lead to poor adhesion and potential fuel leaks.
Additionally, metal fuel lines, often made from steel or aluminum, require a sealant that can withstand the corrosive nature of fuel and provide a reliable seal. In this case, a sealant with excellent corrosion resistance and the ability to form a strong bond with metal surfaces is necessary. It is crucial to follow the manufacturer's recommendations and choose a sealant that is specifically designed for metal fuel lines to ensure long-lasting performance.
In summary, material compatibility is a key consideration when selecting a thread sealant for fuel lines. By choosing a sealant that is compatible with the specific fuel line material, you can ensure a secure and reliable seal, prevent damage to the fuel lines, and maintain the overall performance and safety of the vehicle's fuel system. Always refer to the manufacturer's guidelines and consult with experts if needed to make an informed decision.
Fuel Line Clog Symptoms: Engine Issues Revealed
You may want to see also
Temperature Resistance: Choose a sealant that can withstand fuel line temperatures for optimal performance
When it comes to choosing the best thread sealant for fuel lines, temperature resistance is a critical factor to consider. Fuel lines operate in harsh environments, and the sealant must be able to withstand the extreme temperatures that these lines experience. High temperatures can cause the sealant to degrade, leading to potential leaks and performance issues. Therefore, it is essential to select a sealant that can maintain its integrity and effectiveness over a wide temperature range.
The fuel system in a vehicle is designed to handle various operating conditions, including cold starts and high-speed travel. During cold starts, the fuel lines can experience rapid temperature drops, which can cause the sealant to become brittle and crack. On the other hand, high-speed travel generates significant heat, which can lead to the sealant softening and losing its sealing properties. To ensure optimal performance, the chosen sealant should have excellent temperature stability.
Look for sealants that are specifically formulated for fuel line applications and can withstand the typical temperature fluctuations in a vehicle's fuel system. Some sealants are designed to remain flexible and resistant to cracking even in sub-zero temperatures, ensuring a reliable seal during cold starts. Others are engineered to maintain their structural integrity at elevated temperatures, preventing leaks and maintaining the efficiency of the fuel system.
Consider the operating temperature range of your vehicle and select a sealant that can handle both extremes. For example, if you live in a region with extreme cold winters, opt for a sealant with superior low-temperature performance. Conversely, if your vehicle operates in high-temperature environments, choose a sealant with excellent heat resistance. This ensures that the sealant will provide long-lasting protection against fuel line leaks regardless of the climate.
Additionally, it is beneficial to choose a sealant that offers a wide temperature range, allowing for versatility in different climates. Some advanced sealants are designed to adapt to varying temperatures, providing consistent performance throughout the year. By selecting a sealant with superior temperature resistance, you can ensure the longevity and reliability of your fuel system, reducing the risk of costly repairs and maintaining optimal vehicle performance.
Unleash Power: Understanding the Cutlass Dual Fuel Line System
You may want to see also
Flexibility: Opt for a flexible sealant to accommodate fuel line movement without cracking
When it comes to choosing the best thread sealant for fuel lines, flexibility is a critical factor to consider. Fuel lines are subject to constant movement and vibration due to the engine's operation, and any sealant used must be able to withstand these conditions without compromising its integrity. A flexible sealant is designed to accommodate these movements, ensuring that the fuel lines remain sealed tightly without the risk of cracking or leaking.
The primary purpose of a fuel line sealant is to provide a reliable barrier against fuel leakage, which can be extremely dangerous and costly. However, if the sealant is not flexible enough, it may become brittle over time, leading to cracks that can allow fuel to escape. This not only poses a safety hazard but can also result in engine performance issues and potential damage to other components.
Opting for a flexible sealant means selecting a material that can move with the fuel lines. This is particularly important in high-temperature environments where traditional, rigid sealants might fail due to thermal expansion. A flexible sealant will maintain its adhesion and sealing properties even when the fuel lines expand and contract with temperature changes.
When choosing a flexible sealant, look for products specifically designed for fuel line applications. These sealants are typically made from synthetic rubbers or elastomers that offer excellent flexibility and resistance to fuel degradation. They should also have a low temperature range to ensure they remain effective in cold climates.
In summary, flexibility is a key attribute of the best thread sealant for fuel lines. It ensures that the sealant can adapt to the dynamic nature of fuel lines, providing long-lasting protection against leaks and potential engine damage. By selecting a flexible sealant, you are taking a proactive approach to maintaining the safety and performance of your vehicle's fuel system.
Understanding the Role of Fuel Line Pumps in Vehicles
You may want to see also
Chemical Resistance: Select a sealant resistant to fuel chemicals to prevent degradation and leaks
When it comes to choosing the best thread sealant for fuel lines, chemical resistance is a critical factor to consider. Fuel lines are exposed to a variety of chemicals, including gasoline, diesel, and other additives, which can cause degradation and potential leaks over time. Therefore, selecting a sealant that is resistant to these fuel chemicals is essential to ensure the long-term integrity and safety of your fuel system.
The primary goal is to prevent the sealant itself from breaking down when exposed to fuel chemicals, as this could lead to the sealant losing its adhesive properties and potentially failing. Look for sealants that are specifically formulated to withstand the harsh environment of fuel systems. These sealants should be able to resist the corrosive effects of various fuel types and their additives, ensuring that they remain effective and reliable over an extended period.
One way to assess chemical resistance is to consider the specific chemicals commonly found in fuels. Gasoline, for example, contains a range of hydrocarbons, aromatic compounds, and oxygenates, while diesel includes alkanes, cycloalkanes, and other hydrocarbons. The sealant should be able to resist the effects of these chemicals, including their potential to cause swelling, softening, or chemical breakdown of the sealant material.
In addition to the fuel itself, consider the additives that are often included to enhance performance and stability. These additives can include detergents, antioxidants, and corrosion inhibitors, among others. A high-quality thread sealant should be resistant to these additives as well, ensuring that it maintains its integrity and effectiveness even in the presence of these compounds.
To achieve optimal chemical resistance, it is recommended to choose a sealant that is specifically designed for fuel line applications. These sealants are typically formulated with materials that are inherently resistant to fuel chemicals, such as certain types of rubbers, polymers, or synthetic resins. By selecting a sealant with this specialized formulation, you can ensure that it will provide long-lasting protection against fuel degradation and potential leaks.
Duromax Fuel Line Diameter: 2003 Model Specs Revealed
You may want to see also
Durability: Prioritize a durable sealant that can withstand fuel line pressure and vibrations
When it comes to choosing a thread sealant for fuel lines, durability is a critical factor to consider. Fuel lines are subjected to constant pressure and vibrations, and any sealant used must be able to withstand these harsh conditions without compromising its integrity. The primary goal is to ensure that the sealant remains effective over the long term, providing a reliable barrier against fuel leaks and potential damage to the vehicle's engine.
One of the key aspects of durability is the sealant's ability to maintain its structural integrity under pressure. Fuel lines carry high-pressure fuel, and the sealant must be able to resist this pressure without cracking or breaking down. Look for sealants that are specifically designed for high-pressure applications and have a proven track record of success in such environments. These sealants should be able to form a strong, flexible bond that can handle the dynamic nature of fuel line movement without failing.
Vibrations are another significant factor, especially in vehicles that experience rough terrain or frequent acceleration and deceleration. The sealant needs to be resilient enough to absorb and dampen these vibrations without losing its effectiveness. A durable sealant will remain intact and continue to provide a secure seal, even when subjected to the constant shaking and movement of the vehicle's components. This is particularly important in high-performance or off-road vehicles where fuel lines may experience more extreme conditions.
In addition to pressure and vibrations, consider the operating temperature range of the vehicle. Fuel lines can experience extreme temperature fluctuations, from cold engine starts to high-speed driving. The chosen sealant should be able to withstand these temperature variations without becoming brittle or losing its sealing properties. Look for sealants with a wide operating temperature range, ensuring they can handle both hot and cold environments without degradation.
Lastly, the longevity of the sealant is essential. A durable sealant will not only withstand the initial installation process but will also maintain its performance over the vehicle's lifetime. This includes resisting fuel degradation, chemical corrosion, and the natural aging process of the sealant itself. By prioritizing durability, you ensure that the fuel lines remain sealed effectively, reducing the risk of costly repairs and potential engine damage due to fuel leaks.
Unveiling the Material Secrets of Diesel Fuel Lines
You may want to see also
Frequently asked questions
When it comes to choosing a thread sealant for fuel lines, there are a few key factors to consider. Firstly, ensure the sealant is compatible with the fuel type and system to avoid any potential chemical reactions or degradation. EPDM (Ethylene Propylene Diene Monomer) based sealants are commonly used and offer good resistance to fuel chemicals. Additionally, look for a sealant with excellent adhesion to metal and rubber, as fuel lines often have both materials. Some popular brands include Loctite, 3M, and Permatex, each offering specialized products for fuel line applications.
Proper preparation is crucial for a successful seal. Start by cleaning the threads with a degreaser to remove any contaminants. Use a thread brush to ensure the threads are smooth and free of debris. Consider using a thread tape or thread sealant primer to enhance adhesion. For best results, apply the primer first, let it dry, and then apply the chosen sealant.
While general-purpose sealants can be used, they may not provide the same level of performance and reliability as fuel-specific sealants. Fuel lines operate under specific conditions, and a sealant designed for this purpose will offer better resistance to fuel chemicals, temperature changes, and vibration. Always opt for a sealant recommended for fuel systems to ensure long-term performance and safety.
Over time, thread sealants can degrade, leading to potential fuel leaks. Look out for these indicators: fuel line corrosion, visible cracks or flakes of sealant, fuel odor or leaks, and engine performance issues. Regular inspections and reapplication of sealant when necessary can help prevent these problems.
The frequency of reapplication depends on various factors, including the fuel line's environment, temperature, and vibration. As a general guideline, consider reapplying the sealant every 6 to 12 months, or more frequently if you notice any signs of degradation. Regular maintenance ensures the fuel system remains sealed and leak-free.