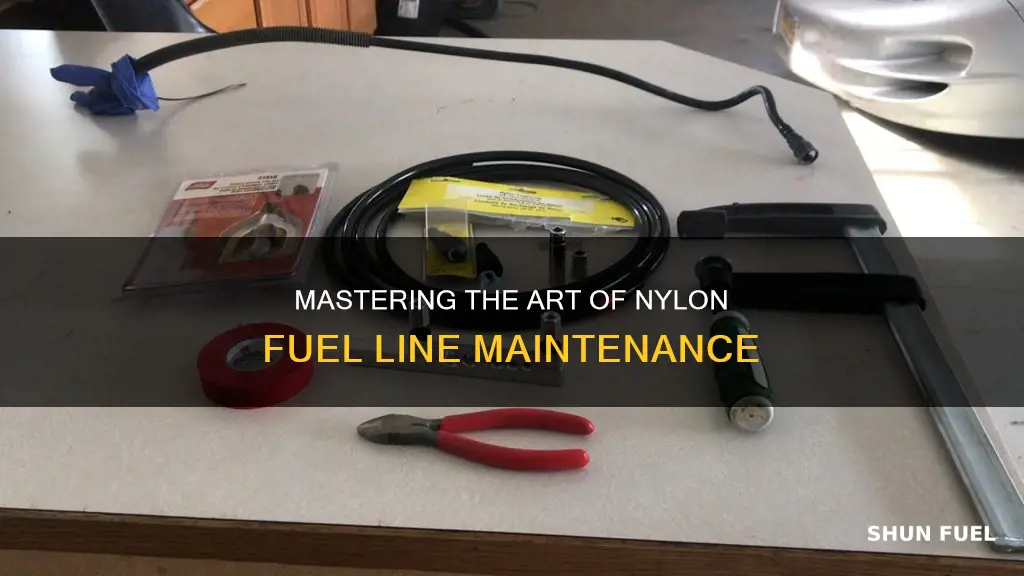
Running a nylon fuel line is a practical and cost-effective solution for fuel delivery systems, especially in applications where flexibility and durability are key. This guide will provide a step-by-step process to ensure a proper installation, covering the necessary tools, preparation, and techniques to create a secure and reliable fuel line connection. By following these instructions, you can effectively manage fuel flow while maintaining the integrity of your vehicle's fuel system.
What You'll Learn
- Preparation: Gather tools and materials, ensuring safety gear is worn
- Line Inspection: Check for damage, cracks, and leaks
- Clamping: Securely attach line to fuel source using appropriate clamps
- Routing: Route line away from heat sources and sharp edges
- Testing: Run diagnostics to ensure proper flow and no leaks
Preparation: Gather tools and materials, ensuring safety gear is worn
Before you begin the process of running a nylon fuel line, it's crucial to prioritize safety and ensure you have the necessary tools and materials ready. This preparation phase is essential to guarantee a smooth and efficient installation while minimizing potential hazards. Here's a step-by-step guide to help you get started:
Gather the Tools and Materials:
- Nylon Fuel Line: Select the appropriate length and diameter of nylon fuel line based on your specific requirements. Ensure it is compatible with the fuel type and pressure you will be working with.
- Fittings and Connectors: Obtain the required fittings, such as elbows, tees, and couplings, specifically designed for nylon fuel lines. These fittings should be made of compatible materials to ensure a secure connection.
- Hose Clamps: Invest in a set of adjustable hose clamps to secure the fuel line in place. Choose a size that can comfortably grip the fuel line without causing damage.
- Fuel Filter: Consider installing a fuel filter to prevent contaminants from entering your fuel system. This is especially important if you are using a nylon fuel line, as it may be more susceptible to fuel-related issues.
- Safety Gear: Prioritize your safety by wearing protective gear. This includes gloves to protect your hands from potential cuts or burns, safety goggles to shield your eyes from fuel splashes, and a respirator or dust mask to avoid inhaling harmful fumes.
Safety Precautions:
- Ensure you are working in a well-ventilated area, especially if you are using fuel-based products. Proper ventilation will help prevent the buildup of harmful gases.
- Keep a fire extinguisher nearby, as a precaution against any potential fuel-related fires.
- Familiarize yourself with the properties of the fuel you are using and any potential hazards associated with it. Different fuels may have varying flash points and combustion characteristics.
By taking the time to gather the necessary tools and materials and prioritizing safety gear, you are setting yourself up for a successful and safe installation process. This preparation phase is a critical step to ensure the longevity and efficiency of your nylon fuel line system.
Optimizing Engine Performance: Choosing the Right Fuel Line Size (6-71)
You may want to see also
Line Inspection: Check for damage, cracks, and leaks
When inspecting your nylon fuel line, it's crucial to be thorough and methodical to ensure the safety and efficiency of your fuel system. Here's a step-by-step guide to inspecting for damage, cracks, and leaks:
- Visual Inspection: Begin by carefully examining the nylon fuel line for any visible signs of damage. Look for cuts, punctures, tears, or any other physical alterations. Nylon fuel lines can be susceptible to damage from sharp objects, road debris, or even rodents. Inspect the entire length of the line, paying close attention to bends, joints, and areas where it connects to other components. Check for any discoloration or swelling, as these could indicate internal damage or potential failure points.
- Flexibility and Movement: Nylon fuel lines should be flexible and able to move with the engine and vehicle. Test the line by gently bending it at various angles and observing if it returns to its original shape. If the line becomes stiff or shows signs of permanent deformation, it may be damaged and require replacement.
- Cracks and Abrasions: Inspect the surface of the fuel line for cracks, small tears, or abrasions. These can be caused by friction against other components, such as the engine block or transmission. Use a bright light source to illuminate the line and look for any hidden cracks that might be difficult to see with the naked eye. Pay extra attention to areas where the line passes over sharp edges or protrusions.
- Leaks and Moisture: Moisture in the fuel line is a serious concern, as it can lead to corrosion and engine damage. Check for any signs of moisture or wetness along the line. If you notice any water accumulation, it could indicate a leak or a compromised seal. Additionally, look for any fuel dripping or seeping from the line, which would be a clear sign of a damaged or cracked section.
- Pressure Testing (Optional): For a more comprehensive inspection, you can perform a pressure test. This involves temporarily disconnecting the fuel pump and applying pressure to the line. Observe if any fuel escapes at the connection points or along the line. This test can help identify internal damage or weak seals.
Remember, regular maintenance and inspection of your fuel line are essential to prevent costly repairs and ensure optimal engine performance. If you notice any issues during the inspection, it's best to consult a professional mechanic for further evaluation and potential replacement of the nylon fuel line.
F250 Fuel Line Disconnect: Choosing the Right Tool Size
You may want to see also
Clamping: Securely attach line to fuel source using appropriate clamps
When it comes to running a nylon fuel line, ensuring a secure and reliable connection is crucial to prevent fuel leaks and maintain optimal performance. Clamping is a critical step in this process, as it provides a strong and durable attachment between the fuel line and the source. Here's a detailed guide on how to securely clamp the nylon fuel line:
Choose the Right Clamps: The first step is to select the appropriate clamps for your specific fuel line and application. Nylon fuel lines often require specialized clamps designed to withstand the unique challenges of fuel systems. Look for clamps made from materials like stainless steel or durable plastics that can handle the corrosive nature of fuel. Consider the size and thickness of your fuel line, as larger diameters might require heavy-duty clamps.
Prepare the Clamps and Fuel Line: Before clamping, ensure the fuel line is clean and free of any debris or contaminants. Use a cloth or brush to wipe down the line, especially if it has been previously used. Inspect the clamps for any signs of damage or wear. If they are old, consider replacing them to ensure a tight and secure connection.
Position the Clamps: Proper positioning is key to a successful clamp. Typically, you'll want to place the clamps at regular intervals along the fuel line, especially at bends or joints. This helps distribute the pressure evenly and prevents the line from being pinched or damaged. For straight sections, a single clamp might be sufficient, but for more complex routes, multiple clamps are essential.
Apply Clamps Firmly: Now, it's time to clamp down. Start by positioning the clamp around the fuel line, ensuring it is centered and aligned with the line's diameter. Use a pair of pliers or a clamp tool to apply firm pressure, tightening the clamp securely. Take care not to overtighten, as this can crimp the line. The goal is to create a tight seal without causing any damage. Repeat this process for each clamp, maintaining consistent pressure.
Test for Leaks: After clamping, it's crucial to test for any potential leaks. Turn on the fuel source and observe for any signs of fuel escaping at the clamp points. If any leaks are detected, carefully inspect the clamps and the fuel line for any imperfections or damage. Adjust or replace the clamps as necessary to ensure a tight seal.
Remember, proper clamping is essential for the longevity and safety of your fuel system. Always refer to manufacturer guidelines and best practices for your specific fuel line and application. By following these steps, you can ensure a secure and reliable connection for your nylon fuel line.
Determine Your Fuel Line Tube Size: A Quick Guide
You may want to see also
Routing: Route line away from heat sources and sharp edges
When installing or replacing a nylon fuel line, proper routing is crucial to ensure the system's longevity and performance. One essential aspect of this process is to route the line away from potential heat sources and sharp edges to prevent damage and ensure a safe operation. Here's a detailed guide on how to achieve this:
Identify Heat Sources and Hazards: Begin by thoroughly inspecting your vehicle's interior and engine compartment. Locate any potential heat sources, such as exhaust manifolds, catalytic converters, or engine blocks, where temperatures can soar. Additionally, identify sharp edges and potential impact areas, like door frames, fender wells, or the underbody, where the fuel line might come into contact. Understanding these hazards is the first step to effective routing.
Plan the Route: Based on your inspection, carefully plan the path of the nylon fuel line. Aim to keep it as straight and direct as possible while maintaining a safe distance from the identified heat sources and sharp edges. Consider the natural flow of the vehicle's structure and any existing lines or hoses to determine the most efficient and secure route. This planning phase is critical to ensure the fuel line is not only well-protected but also functions optimally.
Use Protective Materials: To further safeguard the fuel line, consider using protective materials or sleeves. For areas near heat sources, you can wrap the line with heat-resistant insulation or a protective sleeve made of materials like rubber or plastic. This additional layer of protection adds a barrier between the fuel line and potential heat damage. Similarly, for sharp edges or high-impact areas, use rubber or plastic sleeves to cushion the line and prevent chafing or damage.
Secure the Line: As you route the fuel line, ensure it is securely fastened using appropriate ties or clips. Avoid tight bends or kinks that could restrict fuel flow or cause damage over time. Use ties that are heat-resistant and won't compromise the line's integrity. Properly securing the line also helps maintain its shape and prevents it from coming into contact with sharp edges or heat sources, thus ensuring a longer-lasting installation.
Regular Inspection: Even after the initial installation, regular inspections are vital. Check the fuel line periodically for any signs of wear, damage, or heat-related degradation. Look for soft spots, cracks, or discolored areas, especially where the line is routed near heat sources. Early detection of any issues allows for prompt repairs or replacements, ensuring the continued safe operation of your fuel system.
Understanding the Role of AV in Fuel Lines
You may want to see also
Testing: Run diagnostics to ensure proper flow and no leaks
Before you begin the process of running a nylon fuel line, it's crucial to understand the importance of proper testing and diagnostics. This step is essential to ensure the safety and efficiency of your fuel system. Here's a detailed guide on how to test and diagnose your nylon fuel line for optimal performance:
Flow Testing: Start by checking the flow rate of the fuel through the line. You can use a fuel flow meter or a calibrated container to measure the volume of fuel passing through the line over a specific time period. Compare the measured flow rate with the expected rate based on the engine's specifications. If the flow is inconsistent or lower than expected, it may indicate a restriction or blockage in the line. Inspect the nylon fuel line for any signs of damage, kinks, or clogs that could impede the fuel flow.
Leak Detection: Proper leak testing is critical to ensure the integrity of your fuel system. Begin by applying a small amount of soapy water or a specialized fuel line sealant along the entire length of the nylon fuel line. Then, start the engine and observe for any bubbles or foam forming on the surface. These bubbles indicate the presence of air or fuel leaks. If you notice any leaks, carefully inspect the connections and fittings for damage or corrosion. Tighten or replace any faulty components to eliminate the leaks.
Pressure Testing: Nylon fuel lines should be able to withstand the pressure of the fuel system. Use a fuel pressure gauge to measure the pressure at the fuel pump outlet and compare it to the recommended range. If the pressure is too low, it might suggest a pump issue or a restricted line. Conversely, excessive pressure could indicate a potential failure in the fuel line's integrity. Ensure that the pressure gauge is properly calibrated for accurate readings.
Visual Inspection: While testing, don't forget the power of visual inspection. Look for any visible signs of damage, such as cracks, punctures, or swelling in the nylon fuel line. Inspect the connections for rust, corrosion, or signs of overheating. Check for any signs of fuel contamination, such as discoloration or the presence of water. If any issues are found, address them promptly to prevent further damage.
Remember, proper testing and diagnostics are essential to maintain the performance and longevity of your fuel system. By following these steps, you can ensure that your nylon fuel line is functioning correctly, providing efficient fuel delivery to your engine. Regular maintenance and testing will help identify potential issues early on, saving you from costly repairs and ensuring a reliable power source.
Koler Command Fuel Line Sizes: A Comprehensive Guide
You may want to see also
Frequently asked questions
Nylon fuel lines are commonly used in automotive applications to transport fuel from the tank to the engine. They are preferred for their flexibility, durability, and resistance to fuel-related chemicals, making them a reliable choice for fuel delivery systems.
Installation involves several steps. First, ensure you have the necessary tools and materials, including the nylon fuel line, fittings, and any required adapters. Clean the fuel line and prepare the ends for assembly. Then, use the appropriate fittings to connect the line to the fuel tank and engine. Secure the connections with the recommended fasteners, ensuring a tight and leak-free fit.
You can cut and bend nylon fuel lines yourself using standard cutting and bending tools. However, purchasing pre-cut and pre-bent pieces can save time and ensure a more professional finish. These pre-formed lines are available in various lengths and angles, making it convenient to match your specific routing requirements.