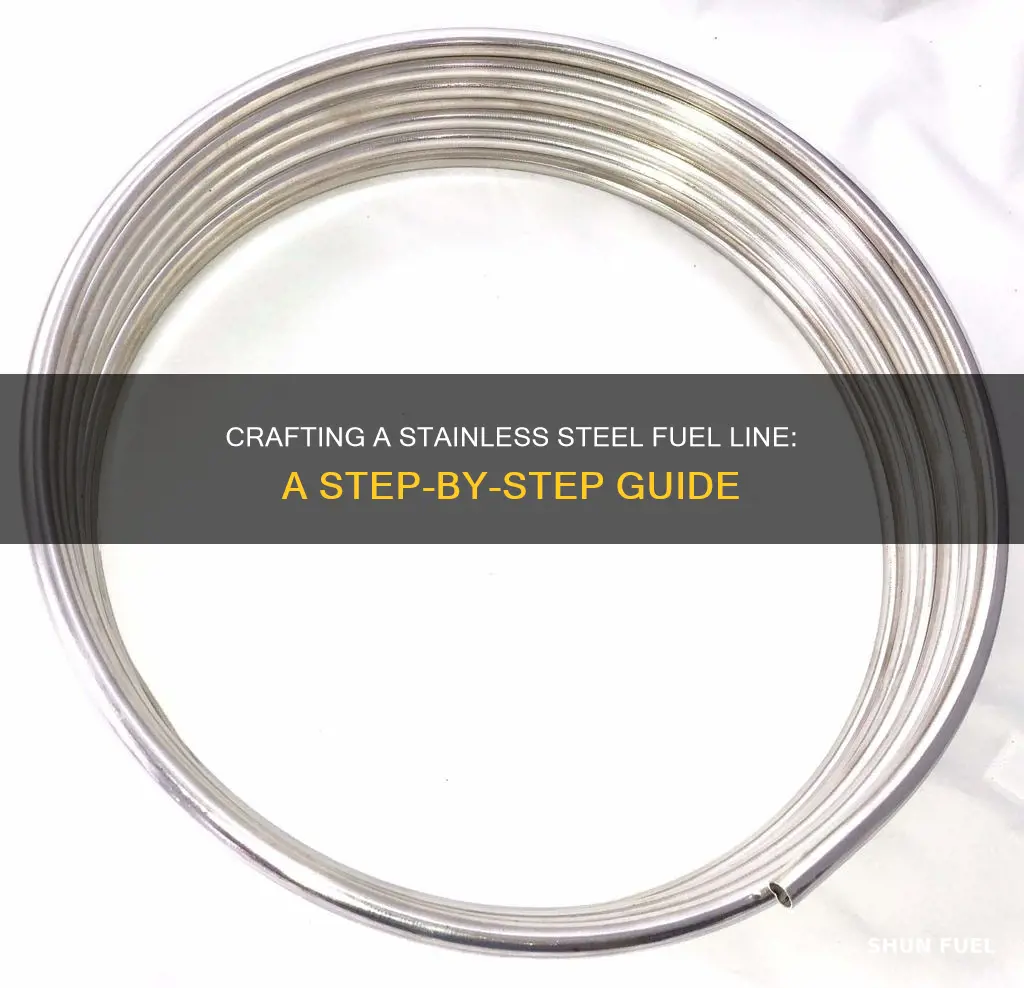
Stainless steel braided fuel lines are a popular choice for vehicle enthusiasts due to their durability and resistance to corrosion. Making these fuel lines involves several steps to ensure a high-quality product. First, you'll need to select the appropriate gauge of stainless steel wire, considering factors like pressure and temperature requirements. The wire is then braided to create a flexible yet strong structure, often with a protective outer layer for added protection. Proper crimping techniques are crucial to ensure a secure connection between the fuel line and fittings. Finally, the braided fuel line is inspected for any defects, ensuring it meets the necessary standards for fuel delivery in vehicles. This process requires precision and attention to detail to create a reliable and long-lasting fuel line.
What You'll Learn
- Material Selection: Choose 304 or 316 stainless steel for durability
- Braiding Process: Twist wires tightly for a strong, flexible fuel line
- Reinforcement: Add a layer of braided steel for extra strength
- Hose Construction: Combine steel braiding with a durable rubber inner tube
- Connection Methods: Use fittings or crimping for secure fuel line attachment
Material Selection: Choose 304 or 316 stainless steel for durability
When it comes to creating a briaded fuel line for your vehicle, material selection is a critical aspect that ensures durability and performance. Among the various options available, stainless steel stands out as an excellent choice due to its exceptional properties. The two most commonly used grades of stainless steel for this purpose are 304 and 316.
304 Stainless Steel: This grade is an excellent choice for fuel lines due to its superior corrosion resistance. It contains a higher chromium content, typically around 18%, and a significant amount of nickel, making it highly resistant to rust and corrosion. This is crucial for fuel lines as they are exposed to various chemicals and contaminants present in gasoline or diesel. 304 stainless steel can withstand the harsh conditions of fuel transport without deteriorating, ensuring a long-lasting and reliable fuel line. Additionally, it offers good formability and weldability, making it easy to work with during the manufacturing process.
316 Stainless Steel: For applications requiring even higher corrosion resistance, 316 stainless steel is the preferred choice. This grade contains a higher level of molybdenum, which further enhances its ability to resist corrosion, especially in chloride-rich environments. While it is more expensive than 304, it is ideal for fuel lines that will be exposed to saltwater or other corrosive substances. The increased molybdenum content provides excellent protection against pitting and crevice corrosion, making it a robust and reliable option for fuel line construction.
Both grades of stainless steel offer excellent mechanical properties, including high tensile strength and good ductility, ensuring the fuel lines can withstand the pressures and vibrations encountered during vehicle operation. The choice between 304 and 316 stainless steel depends on the specific environmental conditions and the level of corrosion resistance required. For most automotive applications, 304 stainless steel is a cost-effective and reliable choice, while 316 stainless steel is reserved for more demanding or corrosive environments.
In summary, when creating a briaded fuel line, opting for 304 or 316 stainless steel ensures durability and longevity. These materials provide excellent resistance to corrosion, ensuring that the fuel lines remain intact and functional over time, even in the presence of various chemicals and contaminants. The choice between the two grades should be based on the specific requirements of the application, balancing performance, cost, and environmental factors.
Nylon Fuel Line: Choosing the Right Material for Optimal Performance
You may want to see also
Braiding Process: Twist wires tightly for a strong, flexible fuel line
The braiding process is a crucial step in creating a sturdy and flexible fuel line from stainless steel wires. It involves twisting and intertwining the wires in a specific pattern to form a strong and durable structure. This technique is essential to ensure the fuel line can withstand the rigors of the fuel delivery system while maintaining flexibility for easy installation.
To begin the braiding process, you'll need a set of stainless steel wires with a suitable diameter for your fuel line application. The wires should be cut to the desired length, ensuring a consistent and even supply for the braiding. Start by laying out the wires in a straight line, with each wire positioned slightly offset from the next, creating a 'V' shape. This initial arrangement sets the foundation for the braiding pattern.
Now, it's time to twist and turn. Take one wire and wrap it tightly around the center of the 'V' shape, creating a small coil. Then, take the next wire and wrap it in the opposite direction, overlapping the first wire slightly. Continue this process, alternating the direction of each wrap, until you've covered the entire length of the wires. The key here is to apply firm pressure and ensure each twist is tight and secure.
As you progress, the pattern will become more intricate. Each twist should be made with precision, ensuring the wires are intertwined tightly but not so much that they become kinked or damaged. The goal is to create a smooth, continuous surface that is both strong and flexible. Take your time with this step, as it directly impacts the fuel line's performance and longevity.
Once you've completed the braiding, carefully examine the fuel line. Ensure there are no sharp bends or kinks in the wire, as these can compromise the line's flexibility. The final product should be a smooth, continuous tube with a uniform diameter, ready for installation in your fuel delivery system. This braiding technique is a critical aspect of creating a high-quality, long-lasting fuel line.
Poulan 5020 Chainsaw: Why Two Fuel Line Sizes Matter
You may want to see also
Reinforcement: Add a layer of braided steel for extra strength
To reinforce the fuel line and ensure its durability, a layer of braided steel can be added to the design. This process involves carefully weaving or braiding steel wires together to create a strong and flexible structure. The braided steel layer provides several advantages. Firstly, it significantly increases the overall strength of the fuel line, making it more resistant to wear and tear, especially in high-pressure environments. The steel's inherent rigidity and tensile strength complement the flexibility of the fuel line, allowing it to withstand bends and twists without compromising its integrity.
The braiding process begins with selecting the appropriate steel wires, typically made from stainless steel due to its corrosion resistance and durability. The wires are then carefully arranged in a specific pattern, often a circular or spiral design, ensuring each wire intertwines with its neighbors. This intricate weaving pattern creates a strong and cohesive structure, where the individual wires collectively bear the load, distributing stress evenly. The braided layer is typically secured to the fuel line using specialized connectors or fittings designed to withstand the additional strength.
When implementing this reinforcement, it is crucial to consider the specific requirements of the fuel line. Factors such as the operating temperature, pressure, and the presence of corrosive substances should be taken into account. The braided steel layer should be able to withstand these conditions without losing its structural integrity. Additionally, the braiding pattern and wire diameter can be customized to meet the desired strength and flexibility balance.
Incorporating braided steel reinforcement offers a reliable solution for enhancing the fuel line's performance. This method is particularly useful in applications where the fuel line is subjected to harsh conditions or requires exceptional strength. By combining the flexibility of the original material with the added strength of steel braiding, the fuel line becomes more robust and capable of withstanding the challenges of its environment.
Remember, when working with steel braiding, precision and attention to detail are essential. Properly securing the braided layer and ensuring compatibility with the fuel line's design will contribute to the overall success of the reinforcement process. This reinforcement technique showcases how innovative design choices can significantly improve the functionality and longevity of fuel lines in various industrial and automotive applications.
Toyota Corolla Fuel Line Location: A Comprehensive Guide
You may want to see also
Hose Construction: Combine steel braiding with a durable rubber inner tube
The construction of a stainless steel-braided fuel line involves a combination of materials and techniques to ensure durability and performance. One crucial aspect is the hose construction, which involves a unique blend of steel braiding and a robust rubber inner tube. Here's a detailed guide on how to achieve this:
Material Selection: Begin by choosing high-quality materials. For the inner tube, opt for a durable rubber compound specifically designed for fuel lines. This rubber should be resistant to fuel degradation and have excellent flexibility to accommodate any movement within the hose. Ensure the rubber meets or exceeds industry standards for fuel hose applications.
Braiding Process: The steel braiding is a critical component for reinforcement and protection. Start by preparing the steel wire, which should be made of a corrosion-resistant stainless steel alloy suitable for fuel transport. The wire should be carefully woven or braided around the rubber inner tube, creating a protective layer. The braiding pattern can vary, but a common approach is to use a tight, uniform weave to ensure structural integrity. The braiding should be tight enough to provide support but not so tight that it restricts the flexibility of the hose.
Assembly and Reinforcement: After braiding, the hose assembly begins. Carefully insert the braided assembly into a suitable outer casing or cover. This casing should be made of a material that complements the inner tube and braiding, such as a flexible, fuel-resistant material. Ensure the hose is securely attached to any necessary fittings or connectors, providing a leak-tight connection. Reinforcement at critical points, such as bends and connections, is essential to prevent damage.
Testing and Quality Control: Once the hose construction is complete, rigorous testing is vital. Subject the hose to pressure tests, flexibility tests, and even fuel compatibility tests to ensure it meets the required standards. Inspect the hose for any defects, such as sharp bends in the braiding or damage to the inner tube. Quality control measures should be implemented to guarantee that each hose meets the specified specifications.
By combining the strength of steel braiding with the flexibility and durability of a rubber inner tube, you create a robust fuel line that can withstand the challenges of fuel transport. This construction method ensures a long-lasting and reliable hose, making it an ideal choice for various applications, including automotive and industrial settings.
Honda Magna 700 Fuel Line Size: 1986 Model Guide
You may want to see also
Connection Methods: Use fittings or crimping for secure fuel line attachment
When it comes to connecting a stainless steel braided fuel line, there are two primary methods to ensure a secure and reliable attachment: using fittings or crimping. Both techniques offer distinct advantages and are chosen based on the specific requirements of the fuel line installation.
Fittings:
Fittings provide a professional and reliable way to join fuel lines. These are typically made of brass or stainless steel and come in various types, such as compression, quick-connect, or barbed fittings. Here's a step-by-step process:
- Prepare the Fitting: Ensure the fitting is clean and free of any debris. If using a new fitting, inspect it for any manufacturing defects.
- Assemble the Connection: Slide the fuel line through the fitting, ensuring it is centered. Tighten the fitting securely using the appropriate tool, following the manufacturer's guidelines for torque specifications.
- Test for Leaks: After assembly, test the connection by applying pressure and checking for any leaks. If a leak is detected, tighten the fitting further or consider using a sealing compound.
- Benefits: Fittings offer a permanent and leak-resistant connection. They are easy to install and provide a tidy appearance, making them ideal for fuel lines that are visible or require frequent access.
Crimping:
Crimping is a mechanical method that involves deforming the fuel line material to create a secure connection. This method is often used for flexible fuel lines and can be advantageous in certain scenarios:
- Prepare the Line: Ensure the stainless steel braided fuel line is clean and free of any contaminants.
- Crimping Tool: Use a crimping tool designed for fuel line connections. Follow the tool's instructions to ensure proper crimping.
- Crimping Process: Apply the crimping tool to the prepared fuel line, following the manufacturer's guidelines for the correct number of crimps and the appropriate force.
- Inspection: After crimping, inspect the connection for a smooth, uniform crimp. Ensure there are no sharp edges or uneven deformations.
- Advantages: Crimping provides a strong and durable connection, especially in high-pressure applications. It offers flexibility and can accommodate slight movements without compromising the seal.
Both methods have their merits, and the choice depends on factors such as fuel line type, installation environment, and personal preference. Fittings offer convenience and a neat appearance, while crimping provides a robust and flexible solution. It is essential to follow manufacturer guidelines and best practices to ensure a successful and long-lasting fuel line installation.
Catalyst Fuel Line Removal: A Step-by-Step Guide for 2006 Jeep Liberty Owners
You may want to see also
Frequently asked questions
Stainless steel braided fuel lines are designed to provide a durable and flexible connection for fuel delivery systems in vehicles. They are commonly used in high-performance engines or applications where traditional rubber hoses may not withstand the heat, pressure, or chemicals present in the fuel. The braiding technique used in these lines offers excellent resistance to abrasion, ensuring a long-lasting and reliable fuel supply.
Installation of a stainless steel braided fuel line typically involves the following steps: First, ensure you have the necessary tools, including a fuel line cutter, crimping tool, and appropriate connectors. Cut the fuel line to the desired length, leaving a small excess for crimping. Slide the fuel line into the connector, ensuring it is centered. Use the crimping tool to apply pressure and secure the connector, creating a tight seal. Repeat this process for each connection, and remember to bleed the fuel system to remove any air bubbles.
Yes, proper maintenance is crucial to ensure the longevity of stainless steel braided fuel lines. Regularly inspect the lines for any signs of damage, such as cracks, punctures, or discoloration. Avoid using sharp objects or tools that could potentially cut or damage the fuel line. In the event of a fuel leak, it is essential to identify and address the cause promptly. Cleaning the fuel system periodically can also help prevent contamination and maintain optimal performance.