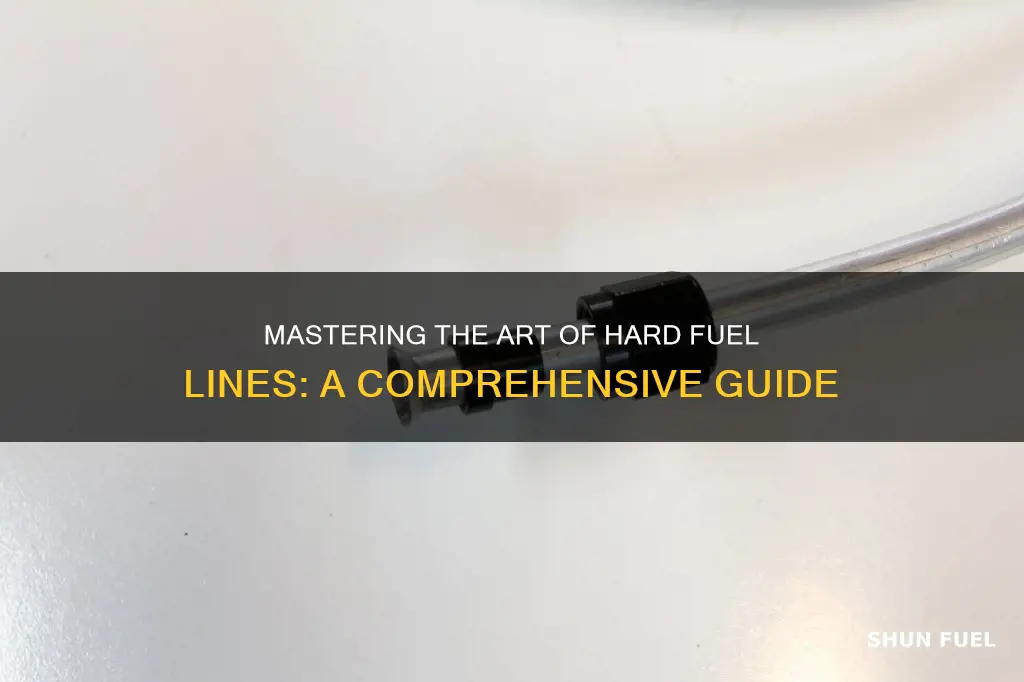
Hard fuel lines are essential components in various industrial and automotive applications, providing a robust and reliable means of transporting fuel. Manufacturing these lines requires careful consideration of materials, design, and construction to ensure they can withstand high pressures, extreme temperatures, and harsh environments. This guide will explore the process of creating hard fuel lines, covering key steps such as selecting appropriate materials, designing the line to meet specific requirements, and implementing manufacturing techniques that ensure durability and performance. By following these guidelines, engineers and manufacturers can produce fuel lines that are both strong and efficient, contributing to the overall reliability of fuel systems in demanding applications.
What You'll Learn
- Material Selection: Choose durable materials like steel or brass for fuel lines
- Hose Reinforcement: Use metal braids or steel wire for added strength
- Fitting Installation: Secure fittings with clamps or welding for a tight seal
- Hose Routing: Route fuel lines away from heat sources and vibrations
- Pressure Testing: Conduct thorough tests to ensure leak-free connections
Material Selection: Choose durable materials like steel or brass for fuel lines
When it comes to creating hard fuel lines, material selection is a critical aspect that ensures the durability and reliability of the system. The primary goal is to choose materials that can withstand the harsh conditions of fuel transport, including high temperatures, pressure, and chemical exposure. Among the various options available, steel and brass stand out as excellent choices for fuel lines due to their inherent strength and resistance to corrosion.
Steel, a robust and versatile material, is highly regarded in the automotive and industrial sectors for its ability to endure extreme environments. It offers exceptional strength, making it ideal for fuel lines that require structural integrity under pressure. Additionally, steel's resistance to corrosion ensures that the fuel lines remain unaffected by the chemicals present in the fuel, preventing degradation over time. This material is commonly used in high-performance vehicles and industrial applications where durability is paramount.
Brass, another excellent option, combines the best of both worlds—the strength of copper and the malleability of zinc. It is known for its superior corrosion resistance, which is crucial for fuel lines as it prevents the material from deteriorating when exposed to fuel. Brass fuel lines are lightweight, flexible, and highly resistant to fatigue, making them an excellent choice for applications where flexibility is required without compromising strength. This material is often used in marine and aviation industries where exposure to harsh environments is common.
Both steel and brass provide excellent protection against the corrosive effects of fuel, ensuring that the lines remain intact and functional over extended periods. The choice between the two may depend on specific application requirements, such as the operating temperature, pressure, and the presence of specific chemicals in the fuel. For high-temperature environments, steel might be preferred, while brass could be more suitable for low-temperature applications or where flexibility is a key consideration.
In summary, when crafting hard fuel lines, opting for durable materials like steel or brass is essential. These materials offer the necessary strength, corrosion resistance, and flexibility required to ensure the longevity and reliability of the fuel system, making them indispensable in various industries.
Mastering Fuel Line Drain: A Step-by-Step Guide
You may want to see also
Hose Reinforcement: Use metal braids or steel wire for added strength
Reinforcing fuel lines with metal braids or steel wire is a crucial step to ensure the longevity and reliability of your vehicle's fuel system. This method is particularly useful for high-performance engines or vehicles operating in harsh conditions where the fuel lines are prone to damage. Here's a detailed guide on how to reinforce your fuel lines using metal braids or steel wire:
Materials and Tools:
- Metal Braids: These are flexible metal wires woven into a braided pattern, providing excellent strength and flexibility. Choose a braid made from stainless steel or a similar corrosion-resistant material to ensure durability.
- Steel Wire: You can use either galvanized or stainless steel wire, depending on your preference and the specific requirements of your project. Steel wire is stronger but less flexible compared to metal braids.
- Hose Clamps: Standard hose clamps or specialized fuel line clamps are essential to secure the reinforcement material around the hose.
- Wire Cutter or Scissors: For cutting the metal braid or steel wire to the desired length.
- Pliers: Useful for gripping and bending the wire during installation.
- Safety Gear: Wear gloves and eye protection when handling sharp tools and metal wires.
Step-by-Step Process:
- Prepare the Fuel Line: Start by inspecting the fuel line for any existing damage or wear. Clean the area where the reinforcement will be applied to ensure a secure bond. Cut the metal braid or steel wire to the length required, considering the length of the fuel line you want to reinforce.
- Apply the Reinforcement: Wrap the metal braid or steel wire tightly around the fuel line, ensuring complete coverage of the hose. Start from one end and work your way to the other, overlapping the wire slightly to create a secure bond. Use hose clamps to hold the wire in place at regular intervals, typically every 6-8 inches. This will prevent the wire from shifting or coming loose over time.
- Secure the Ends: Once you've wrapped the entire length of the fuel line, secure the ends of the wire. You can crimp the ends using pliers or use hose clamps to hold them temporarily. Then, use a wire cutter to trim any excess wire, leaving a small, neat end.
- Test and Inspect: After the reinforcement process, test the fuel line by starting the engine and checking for any leaks. Ensure that the metal braid or steel wire doesn't interfere with the fuel pump or other engine components. Regularly inspect the reinforced fuel lines for any signs of wear or damage, especially in areas with high stress or vibration.
By reinforcing your fuel lines with metal braids or steel wire, you create a robust and durable solution to protect against fuel line failures. This method is especially beneficial for high-performance vehicles or those operating in extreme environments, ensuring a reliable fuel supply to the engine. Remember to follow safety protocols and consider seeking professional assistance if you're unsure about any step during the reinforcement process.
Dodge Ram Fuel Line Removal: A Step-by-Step Guide
You may want to see also
Fitting Installation: Secure fittings with clamps or welding for a tight seal
When it comes to installing fuel lines, ensuring a tight and secure connection is crucial to prevent leaks and maintain the integrity of your fuel system. One effective method for achieving this is by using clamps or welding the fittings in place. Both techniques offer reliable ways to create a robust bond between the fuel lines and the fittings.
Clamps provide a flexible and adjustable solution, allowing for easy installation and removal if needed. To begin, select a clamp that is appropriate for the diameter of your fuel line and the fitting. Ensure it has a secure grip and is made of durable material to withstand fuel pressure. Start by positioning the fitting onto the fuel line, ensuring it is centered and aligned properly. Then, carefully wrap the clamp around the fitting and line, making sure it is snug but not overly tight to avoid damaging the line. Adjust the clamp as necessary to achieve a tight seal. Finally, secure the clamp in place using the appropriate hardware, such as screws or bolts, to ensure it remains firmly attached.
Welding, on the other hand, offers a more permanent solution, creating a strong bond between the fuel line and fitting. This method is particularly useful for high-pressure applications or when a more robust connection is required. Before welding, ensure the surface of the fitting and fuel line are clean and free of any debris or contaminants. Use a suitable welding rod or filler material that matches the fuel line's material to ensure compatibility. Begin the welding process by applying heat to the connection area, ensuring it is evenly heated. Then, carefully add the filler material, following the manufacturer's instructions for the specific welding process. Allow the weld to cool and cure according to the recommended guidelines. Once complete, you'll have a strong, permanent seal.
Both methods require precision and attention to detail to ensure a successful installation. It is essential to follow manufacturer guidelines and safety protocols when using welding equipment or working with high-pressure fuel systems. Regularly inspect the fittings and fuel lines for any signs of wear or damage, especially if you've used welding, as this can provide long-term security. By employing these fitting installation techniques, you can create a reliable and leak-free fuel system, ensuring the performance and safety of your vehicle.
Mastering the Art of Flare GM Fuel Line: A Comprehensive Guide
You may want to see also
Hose Routing: Route fuel lines away from heat sources and vibrations
When designing and installing fuel lines for a vehicle, proper hose routing is crucial to ensure the longevity and reliability of the fuel system. One essential aspect of this process is routing the fuel lines away from heat sources and vibrations to prevent potential damage. Here's a detailed guide on how to achieve this:
Identify Heat Sources: Begin by thoroughly inspecting your vehicle's engine bay and surrounding areas. Locate all potential heat sources, such as exhaust manifolds, catalytic converters, engine blocks, and even the transmission. These components generate significant heat, and placing fuel lines too close to them can lead to deterioration over time.
Route Fuel Lines Strategically: When installing the fuel lines, carefully plan their path to avoid direct contact with hot surfaces. Here are some best practices:
- Elevate the Lines: Consider raising the fuel lines slightly above the ground or mounting them on the upper sides of the engine bay. This elevation helps create a physical barrier between the lines and potential heat sources.
- Use Insulation: Apply heat-resistant insulation or sleeves around the fuel lines that come into contact with hot surfaces. This simple measure can significantly extend the life of the lines.
- Maintain Distance: Keep the fuel lines as far away as possible from the identified heat sources. A general rule of thumb is to maintain a safe distance, ensuring that the lines are not in direct contact or close proximity to any hot components.
Minimize Vibrations: Vibrations from the engine can also take a toll on fuel lines over time. Here's how to address this:
- Secure with Vibration-Dampening Materials: Use vibration-dampening materials or rubber mounts to secure the fuel lines. These materials absorb and reduce the impact of engine vibrations, preventing excessive wear and tear on the lines.
- Route Away from Engine Components: Route the fuel lines away from areas where they might come into contact with moving engine parts. This simple routing decision can help minimize the risk of damage.
- Consider Line Material: Different fuel line materials offer varying levels of flexibility and resistance to vibrations. Choose a material that provides adequate flexibility while also being durable enough to withstand engine vibrations.
By following these guidelines, you can ensure that your fuel lines are properly routed, avoiding potential heat-related damage and minimizing the impact of engine vibrations. This attention to detail will contribute to a more reliable and efficient fuel system in your vehicle. Remember, proper hose routing is a critical aspect of vehicle maintenance that should not be overlooked.
Butyl Rubber: A Safe Choice for Fuel Line Sealing?
You may want to see also
Pressure Testing: Conduct thorough tests to ensure leak-free connections
Pressure testing is a critical step in ensuring the integrity and safety of fuel lines, especially when dealing with hard fuel lines that are designed to withstand high pressures and demanding conditions. This process involves subjecting the fuel lines to controlled pressure to identify and rectify any potential leaks or weaknesses before the system is put into operation. Here's a detailed guide on how to conduct pressure testing for leak-free connections:
Preparation: Before initiating the pressure test, ensure that the fuel lines are properly prepared. Start by cleaning the lines to remove any dirt, debris, or contaminants that could interfere with the test results. Use a suitable cleaning agent recommended for fuel lines and follow the manufacturer's instructions. Rinse the lines thoroughly to eliminate any residue. Additionally, inspect the connections for any signs of damage or corrosion. Tighten any loose fittings and replace any damaged components to ensure a secure and reliable connection.
Test Setup: Set up the pressure testing equipment, which typically includes a pressure gauge, a pump or compressor, and a pressure relief valve. Connect the pressure gauge to the fuel line, ensuring it is securely fastened. The pump or compressor will be used to generate the required pressure, and the relief valve is an essential safety measure to release excess pressure if needed. It is crucial to choose a pressure gauge that can accurately measure the expected pressure range of your fuel system.
Pressure Application: Begin the pressure test by slowly increasing the pressure in the fuel line using the pump or compressor. Start with a low pressure and gradually build up to the maximum operating pressure specified for your fuel lines. Monitor the pressure gauge closely during this process. For each increment of pressure, observe the fuel line for any signs of leakage, such as hissing sounds, moisture accumulation, or visual indicators of damage. Take note of the pressure at which any leaks are detected.
Leak Detection and Repair: If a leak is identified during the test, it is essential to address it immediately. Locate the source of the leak, which could be at a connection, fitting, or any other point along the fuel line. Tighten or replace the affected components as necessary. Ensure that all connections are secure and properly sealed. After making the necessary repairs, re-test the fuel line at the previous pressure increment to confirm that the leak has been resolved. Repeat this process until the fuel line passes the test without any leaks.
Documentation and Safety: Document the entire pressure testing process, including the pressure increments, observation notes, and repair actions taken. This documentation is vital for future reference and can help identify patterns or recurring issues. Always prioritize safety during pressure testing. Ensure that the testing area is well-ventilated and clear of any flammable materials. Have a safety plan in place, including emergency procedures, and ensure that all personnel involved are trained and aware of potential hazards.
Fuel Line Installation: From Tank to Engine in 5 Steps
You may want to see also
Frequently asked questions
Hard fuel lines are an essential component in fuel delivery systems, especially in high-performance engines or applications where fuel needs to be transported over long distances or under high pressure. They are designed to withstand the challenges of fuel transport, such as heat, pressure, and vibration, ensuring a reliable and efficient fuel supply to the engine.
Selecting the appropriate material is crucial for the performance and longevity of your fuel lines. Common materials include steel, stainless steel, and high-density polyethylene (HDPE). Steel and stainless steel offer excellent strength and durability but may be more susceptible to corrosion. HDPE, on the other hand, is lightweight, flexible, and resistant to fuel degradation, making it a popular choice for modern fuel systems.
It is not recommended to use regular fuel lines for high-performance engines or applications requiring high fuel pressure. Regular fuel lines may not withstand the increased stress and may fail prematurely. Hard fuel lines are designed to handle higher pressures and temperatures, ensuring a more reliable fuel supply to meet the demands of high-performance vehicles.
Installation of hard fuel lines requires careful planning and execution. Start by cleaning the fuel lines and ensuring they are free of any debris or contaminants. Then, cut the lines to the desired length and use appropriate fittings and connectors for a secure connection. It is essential to follow the manufacturer's guidelines and ensure proper torque specifications for the fittings to avoid leaks.
Hard fuel lines are generally compatible with most fuel types, including gasoline, diesel, and ethanol blends. However, it is crucial to choose the right material and thickness to withstand the specific fuel's properties and operating conditions. Always refer to the manufacturer's recommendations and consult with experts to ensure compatibility and optimal performance.