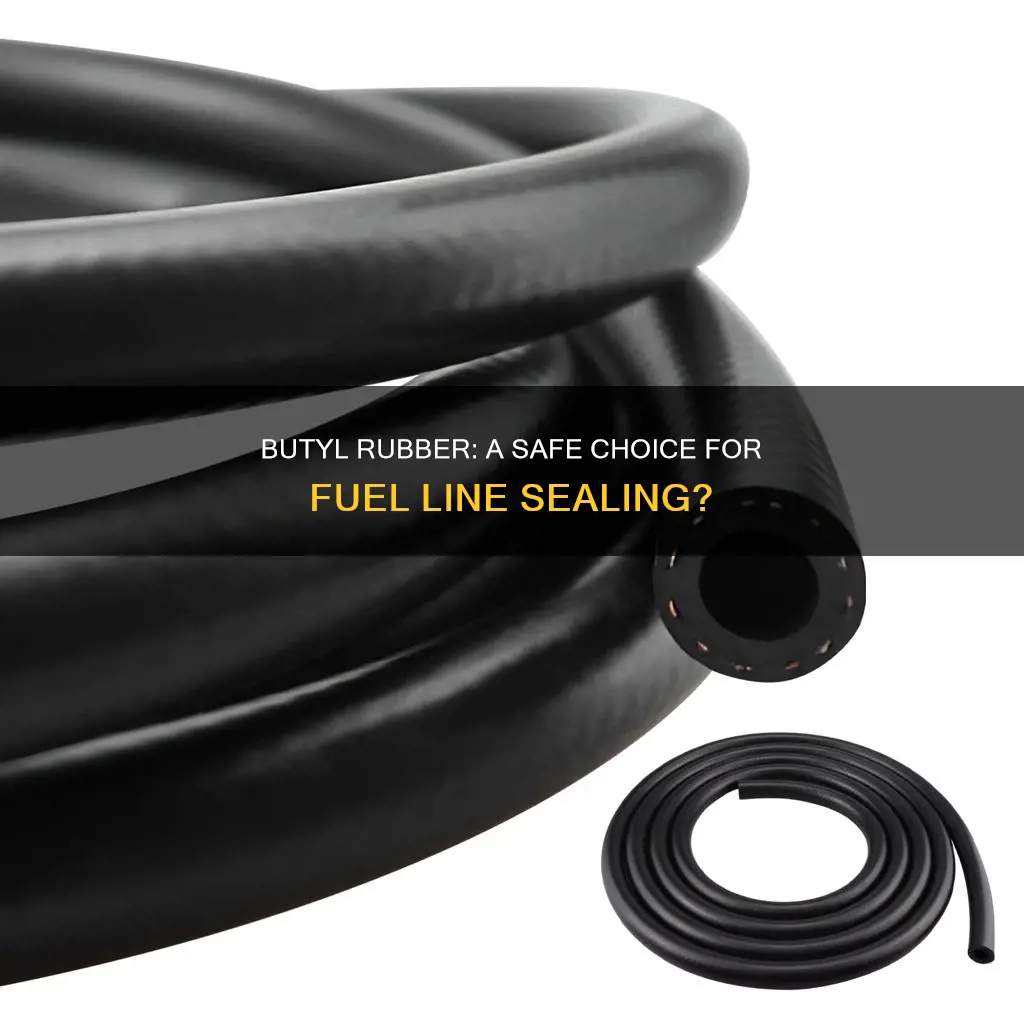
Butyl rubber is a popular choice for sealing fuel lines due to its excellent resistance to fuel degradation and its ability to maintain its integrity over a wide temperature range. This synthetic rubber is known for its superior performance in harsh environments, making it a reliable material for fuel line seals. Its chemical stability and resistance to ozone degradation ensure that it can withstand the corrosive effects of gasoline, diesel, and other fuels, providing long-lasting protection against leaks and potential engine damage. However, it is essential to consider the specific application and consult with experts to ensure the right choice for the job.
Characteristics | Values |
---|---|
Chemical Composition | Butyl rubber is a synthetic polymer made from isobutylene and a small amount of isoprene. |
Temperature Resistance | Excellent resistance to heat and cold, making it suitable for a wide range of temperatures. |
Flexibility | Highly flexible, allowing it to conform to irregular surfaces and withstand mechanical stress. |
Chemical Resistance | Resistant to various chemicals, including fuels, oils, and solvents, which is crucial for fuel line applications. |
Abrasion Resistance | Good resistance to abrasion, ensuring durability in harsh environments. |
Ozone Resistance | Resistant to ozone degradation, which is important for long-term performance. |
Color | Typically white or off-white, providing a visually appealing appearance. |
Thickness | Available in various thicknesses, allowing for customization based on specific requirements. |
Adhesion | Possesses good adhesion properties, enabling strong bonding to metal and other substrates. |
Cost | Generally cost-effective, making it an affordable sealing material. |
Environmental Impact | Consideration of environmental impact is necessary, as some butyl rubbers may contain additives that could be harmful if released into the environment. |
What You'll Learn
- Chemical Compatibility: Butyl rubber can withstand fuel chemicals, making it suitable for fuel line sealing
- Flexibility and Durability: It offers flexibility and durability, ensuring long-lasting fuel line seals
- Temperature Resistance: Butyl rubber maintains sealing integrity across a wide temperature range, including fuel system temperatures
- Resistance to Fuel Evaporation: It resists fuel evaporation, preventing degradation and maintaining sealing performance
- Compliance and Standards: Butyl rubber meets industry standards for fuel line sealing, ensuring safety and reliability
Chemical Compatibility: Butyl rubber can withstand fuel chemicals, making it suitable for fuel line sealing
Butyl rubber is an excellent choice for sealing fuel lines due to its remarkable chemical compatibility with the various components of fuels. This natural rubber compound is known for its ability to resist degradation caused by exposure to different fuel chemicals, ensuring long-lasting performance in automotive applications.
The chemical structure of butyl rubber provides it with exceptional resistance to a wide range of substances commonly found in fuels. It can withstand the presence of gasoline, diesel, kerosene, and even aviation fuels without significant deterioration. This compatibility is crucial for fuel line sealing as it ensures that the rubber material does not break down or become brittle over time, which could lead to leaks and potential engine damage.
One of the key advantages of butyl rubber is its ability to maintain its integrity under both high and low-temperature conditions. This is particularly important in fuel lines, as engines can operate in diverse environments. The rubber's stability at varying temperatures prevents cracking and ensures a reliable seal, even in extreme weather conditions.
Furthermore, butyl rubber's resistance to fuel chemicals is not limited to its physical durability. It also possesses excellent resistance to ozone, which is a significant benefit for fuel line applications. Ozone degradation can lead to the premature aging of rubber, but butyl rubber's unique molecular structure makes it highly resistant, ensuring the longevity of the fuel line seals.
In summary, butyl rubber's chemical compatibility with fuel components, combined with its temperature stability and ozone resistance, makes it an ideal material for sealing fuel lines. Its ability to withstand the harsh conditions of fuel systems contributes to the overall reliability and safety of automotive engines. This makes butyl rubber a preferred choice for manufacturers and mechanics alike when it comes to ensuring secure and long-lasting fuel line connections.
The Dark Motives Behind Fuel Line Cuts: Uncovering Hidden Dangers
You may want to see also
Flexibility and Durability: It offers flexibility and durability, ensuring long-lasting fuel line seals
Butyl rubber is an excellent choice for sealing fuel lines due to its exceptional flexibility and durability. This material is specifically designed to withstand the demanding conditions of fuel systems, ensuring a reliable and long-lasting seal. The flexibility of butyl rubber is crucial in accommodating the various movements and vibrations that fuel lines experience during engine operation. It can easily conform to the shape of the fuel lines, providing a tight and secure seal that prevents fuel leaks. This flexibility is particularly important in high-temperature environments, as it allows the rubber to maintain its integrity without becoming brittle or cracking.
In terms of durability, butyl rubber excels in its ability to resist wear and tear over time. Fuel lines are exposed to harsh chemicals, heat, and mechanical stress, so a robust material is essential. Butyl rubber's chemical resistance ensures it can withstand the corrosive nature of fuels, preventing degradation and maintaining its sealing properties. Additionally, its resistance to ozone and UV radiation makes it suitable for outdoor applications, where it can endure the elements without losing its effectiveness.
The flexibility and durability combination of butyl rubber make it a preferred choice for fuel line seals in various industries. Its ability to form a tight seal, even in challenging conditions, ensures that fuel lines remain secure and leak-free. This is especially critical in automotive applications, where fuel system reliability is essential for safe and efficient vehicle operation. By using butyl rubber, engineers can design fuel systems that are not only reliable but also cost-effective, as the material's longevity reduces the need for frequent replacements.
Furthermore, the versatility of butyl rubber allows for easy installation and customization. It can be easily molded or extruded to fit specific fuel line configurations, ensuring a precise and secure seal. This adaptability is a significant advantage, especially when dealing with complex fuel system designs. The material's flexibility also enables it to bridge small gaps or imperfections in the fuel lines, creating a robust and reliable seal.
In summary, butyl rubber's flexibility and durability make it an ideal material for sealing fuel lines. Its ability to withstand harsh conditions, resist wear, and provide a tight seal ensures long-lasting performance. By incorporating butyl rubber into fuel system designs, engineers can create reliable and cost-effective solutions, contributing to the overall safety and efficiency of vehicles and equipment. This makes it a popular choice for professionals in the automotive and industrial sectors.
Single Fuel Line Setup: LSX S10 Engine Optimization Guide
You may want to see also
Temperature Resistance: Butyl rubber maintains sealing integrity across a wide temperature range, including fuel system temperatures
Butyl rubber is an excellent choice for sealing fuel lines due to its exceptional temperature resistance. It can withstand a wide range of temperatures, making it ideal for fuel systems that experience varying thermal conditions. This material's ability to maintain its sealing integrity under extreme heat and cold is a critical factor in ensuring the safety and efficiency of fuel lines.
The temperature resistance of butyl rubber is a result of its unique molecular structure. It possesses a high degree of cross-linking, which provides excellent stability and flexibility. This property allows butyl rubber to retain its shape and sealing properties even when exposed to extreme temperatures, including those found in fuel systems. When fuel lines are subjected to high temperatures, the rubber can withstand the heat without softening or losing its structural integrity. Similarly, in cold environments, butyl rubber remains flexible and does not become brittle, ensuring a reliable seal.
In the context of fuel systems, temperature fluctuations can be significant. Engines generate heat during operation, and fuel lines may be exposed to these elevated temperatures. Butyl rubber's resistance to heat ensures that the fuel lines can maintain a secure seal, preventing any potential leaks. Additionally, during cold starts or in environments with freezing temperatures, butyl rubber's flexibility and resistance to brittleness are crucial. It can accommodate the expansion and contraction of the fuel lines without compromising the seal, thus preventing fuel leaks and potential engine damage.
The versatility of butyl rubber in temperature resistance is a key advantage in various applications. Its ability to perform consistently across a wide temperature range makes it a preferred choice for sealing fuel lines in automotive, aviation, and industrial settings. Engineers and designers can rely on butyl rubber to provide a long-lasting and reliable seal, ensuring the safe and efficient operation of fuel systems.
Furthermore, the compatibility of butyl rubber with fuels is another essential aspect. It does not react with or absorb fuel, ensuring that the sealing material remains unaffected by the presence of various fuels. This compatibility, combined with its temperature resistance, makes butyl rubber an ideal and trusted material for sealing fuel lines, contributing to the overall safety and performance of fuel systems.
Poulan Chainsaw Fuel Lines: Location and Installation Guide
You may want to see also
Resistance to Fuel Evaporation: It resists fuel evaporation, preventing degradation and maintaining sealing performance
Butyl rubber is an excellent choice for sealing fuel lines due to its exceptional resistance to fuel evaporation. This property is crucial in the automotive industry, where fuel lines are exposed to various environmental conditions and can be susceptible to degradation over time. When fuel is stored in a vehicle, it naturally evaporates, especially in warmer temperatures, leading to the formation of volatile organic compounds (VOCs). These VOCs can cause the fuel to degrade and lose its effectiveness, potentially leading to engine performance issues.
The unique structure of butyl rubber provides a robust barrier against fuel evaporation. It is a synthetic rubber compound known for its high molecular weight and long-chain structure, which contributes to its remarkable resistance to fuel-related degradation. This material's molecular composition creates a stable and resilient barrier that prevents fuel from coming into direct contact with the rubber, thus minimizing the risk of evaporation and subsequent degradation. As a result, butyl rubber-sealed fuel lines can maintain their integrity and sealing performance even in harsh operating conditions.
In the context of fuel lines, resistance to fuel evaporation is vital for several reasons. Firstly, it ensures that the fuel remains stable and does not break down, which is essential for optimal engine performance. Over time, fuel degradation can lead to reduced power, poor fuel efficiency, and even engine misfires. Secondly, this resistance helps prevent the release of harmful VOCs into the environment, contributing to a cleaner and more sustainable ecosystem. By maintaining the integrity of the fuel, butyl rubber-sealed lines can also reduce the risk of fuel leaks, which could have environmental and safety implications.
The effectiveness of butyl rubber in resisting fuel evaporation is attributed to its ability to form a tight seal around the fuel lines. This seal acts as a physical barrier, preventing fuel from coming into contact with the rubber's surface and minimizing the potential for evaporation. Additionally, butyl rubber's inherent chemical stability and resistance to various fuel components make it an ideal choice for sealing applications. It can withstand the corrosive nature of fuels without compromising its structural integrity, ensuring long-lasting performance.
In summary, butyl rubber's resistance to fuel evaporation is a critical factor in its suitability for sealing fuel lines. Its ability to form a protective barrier, coupled with its chemical stability, ensures that fuel remains stable and the sealing performance is maintained over extended periods. This makes butyl rubber an excellent material choice for automotive fuel line sealing, contributing to reliable engine operation and environmental protection.
Toyota Fuel Line Removal: A Step-by-Step Guide for Injector Access
You may want to see also
Compliance and Standards: Butyl rubber meets industry standards for fuel line sealing, ensuring safety and reliability
Butyl rubber is indeed a suitable material for sealing fuel lines, and its use is backed by industry standards and regulations. This is primarily due to its exceptional chemical and thermal stability, making it an ideal choice for applications where fuel is present. The rubber's resistance to various fuels, including gasoline, diesel, and aviation fuels, ensures that it can withstand the corrosive effects of these substances over time.
Compliance with industry standards is a critical aspect of using butyl rubber for fuel line sealing. One of the key standards that this material adheres to is the American Society for Testing and Materials (ASTM) standards. ASTM D1418, for instance, outlines the requirements for materials used in fuel lines, and butyl rubber meets or exceeds these specifications. This standard ensures that the rubber has the necessary properties to resist fuel permeation, aging, and degradation, thus maintaining the integrity of the fuel system.
In addition to ASTM standards, butyl rubber also complies with other industry guidelines, such as those set by the Society of Automotive Engineers (SAE). The SAE J1705 standard, for example, provides requirements for materials used in fuel system components, and butyl rubber is recognized as a suitable material for these applications. This compliance ensures that the rubber used in fuel lines meets the necessary performance criteria, including temperature resistance, flexibility, and resistance to fuel-related degradation.
The reliability and safety of butyl rubber in fuel line sealing are further emphasized by its ability to meet or exceed the performance requirements of various automotive and aviation industries. This includes compliance with the standards set by the National Highway Traffic Safety Administration (NHTSA) and the Federal Aviation Administration (FAA), which ensure that materials used in fuel systems are safe and reliable. By adhering to these standards, butyl rubber provides a robust and secure solution for sealing fuel lines, contributing to the overall safety and efficiency of fuel-powered systems.
In summary, butyl rubber's compliance with industry standards, such as ASTM and SAE specifications, ensures its effectiveness and safety in sealing fuel lines. Its chemical and thermal stability, coupled with its resistance to various fuels, make it an excellent choice for applications where fuel line integrity is crucial. By meeting these standards, butyl rubber provides a reliable and secure solution, contributing to the overall performance and safety of fuel-powered systems.
Fitting Fuel: Compatibility of 3/16 Fuel Lines with 1/4 Filters
You may want to see also
Frequently asked questions
Yes, butyl rubber is an excellent choice for sealing fuel lines due to its exceptional resistance to fuel oils, gasoline, and other petroleum-based products. Its chemical stability and ability to withstand high temperatures make it a reliable material for this application.
Butyl rubber offers several benefits. It has a very low permeability to fuels, ensuring that the lines remain sealed and preventing leaks. Additionally, it is known for its flexibility, durability, and resistance to aging, which are crucial factors for long-lasting fuel line seals.
Absolutely! Butyl rubber is highly resistant to heat and can withstand temperatures ranging from -40°F to 300°F (-40°C to 149°C). This makes it ideal for fuel lines, as it can handle the temperature fluctuations associated with fuel systems without compromising its sealing properties.
Butyl rubber's resistance to fuel oils and its ability to maintain flexibility over time contribute to the long-term integrity of fuel lines. It does not become brittle or crack easily, ensuring that the seals remain effective even after prolonged exposure to fuel. This makes it a preferred material for sealing fuel lines in vehicles and various industrial applications.