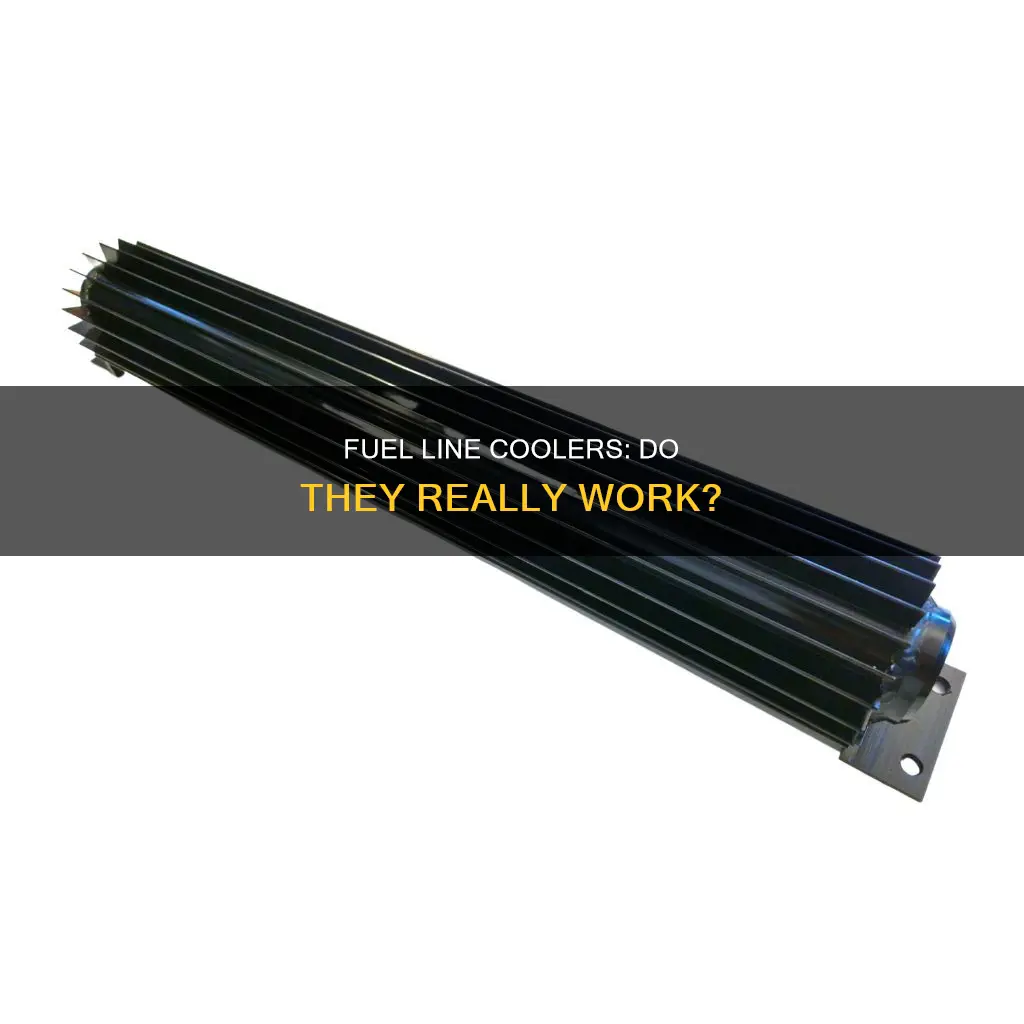
Fuel line coolers are an essential component in the automotive industry, designed to regulate the temperature of fuel before it reaches the engine. The primary function of these coolers is to prevent overheating, which can lead to engine performance issues and potential damage. This introduction aims to explore the effectiveness of fuel line coolers, examining their design, installation process, and the impact they have on engine performance and longevity. By understanding their inner workings and benefits, drivers can make informed decisions about whether fuel line coolers are a worthwhile investment for their vehicles.
What You'll Learn
- Design and Function: Fuel line coolers use heat exchangers to reduce engine temperature
- Performance Benefits: Cooler fuel improves engine performance and fuel efficiency
- Heat Dissipation: Efficient heat dissipation prevents fuel line overheating
- Durability: High-quality materials ensure coolers withstand extreme conditions
- Installation and Maintenance: Proper installation and regular maintenance are essential for optimal performance
Design and Function: Fuel line coolers use heat exchangers to reduce engine temperature
Fuel line coolers are an innovative solution designed to combat the issue of engine overheating, particularly in high-performance vehicles or those operating in extreme conditions. The primary function of these coolers is to regulate the temperature of the fuel before it reaches the engine, ensuring optimal performance and longevity. This is achieved through a clever design that incorporates heat exchangers, which are essentially devices that transfer heat from one medium to another.
The design of a fuel line cooler is quite intricate. It typically consists of a series of tubes or passages that are strategically arranged to facilitate the flow of fuel while also providing a path for heat exchange. These tubes are often made of materials with excellent thermal conductivity, such as aluminum or copper, to maximize heat transfer efficiency. The cooler is positioned in a location where it can effectively absorb heat from the fuel, usually near the fuel tank or along the fuel lines.
The function of the heat exchanger is at the heart of the fuel line cooler's performance. As the fuel passes through the cooler, it comes into contact with a cooling medium, often a liquid or air, which is circulated through the heat exchanger. This medium absorbs heat from the fuel, reducing its temperature. The design ensures that the fuel's temperature drop is gradual, preventing rapid cooling that could lead to fuel condensation, which is undesirable. The cooled fuel then continues its journey to the engine, where it is injected, ensuring a consistent and efficient combustion process.
One of the key advantages of fuel line coolers is their ability to maintain optimal engine temperature, especially during prolonged high-load operations. By keeping the fuel temperature in check, the engine's overall performance is enhanced, and the risk of fuel-related issues, such as pre-ignition or reduced power output, is minimized. This is particularly beneficial for racing cars, heavy-duty machinery, or any application where engine performance and reliability are critical.
In summary, fuel line coolers are designed to optimize engine performance by utilizing heat exchangers to reduce the temperature of the fuel. This design effectively manages the heat generated during engine operation, ensuring that the fuel remains within an optimal temperature range. By doing so, fuel line coolers contribute to improved engine efficiency, extended component life, and enhanced overall reliability, making them a valuable addition to any vehicle or machinery that demands consistent high-performance output.
Fox Body Fuel Line Fixes: A Comprehensive Guide to Restoring Performance
You may want to see also
Performance Benefits: Cooler fuel improves engine performance and fuel efficiency
The concept of a fuel line cooler is an intriguing one, especially for automotive enthusiasts and those looking to optimize their vehicle's performance. While it might seem counterintuitive to cool something that is already hot, the idea behind fuel line coolers is to maintain optimal fuel temperature, which can have a significant impact on engine performance and efficiency.
When fuel is heated, it expands, and this expansion can lead to a few performance issues. Firstly, the increased volume of heated fuel can result in a less precise fuel-air mixture, which is crucial for efficient combustion. This can cause a decrease in power output and a rise in fuel consumption, essentially negating the benefits of a high-performance engine. Secondly, heated fuel can lead to a loss of power, as the engine may not be able to extract the full potential from the fuel due to its elevated temperature. This is where the fuel line cooler comes into play, aiming to mitigate these problems.
By installing a fuel line cooler, you essentially create a mini-radiator system specifically for your fuel. As the fuel passes through the cooler, it loses heat, which helps to maintain a more stable and optimal temperature. This is particularly beneficial in high-performance vehicles or those operating in extreme climates, where fuel temperature can vary significantly. The cooler fuel ensures that the engine receives the most efficient and effective fuel-air mixture, leading to improved power delivery and a more responsive engine.
The performance benefits of a fuel line cooler are twofold. Firstly, it ensures that the engine operates at its peak efficiency, allowing for better power output and a more linear power delivery curve. This means that the engine can rev higher and faster without losing power, which is a significant advantage for racing or high-performance driving. Secondly, the cooler fuel can lead to improved fuel efficiency. With the fuel temperature regulated, the engine can burn the fuel more effectively, reducing waste and improving overall mileage. This is a crucial factor for those looking to optimize their vehicle's fuel economy without compromising on performance.
In summary, fuel line coolers offer a practical solution to maintaining optimal fuel temperature, which directly translates to improved engine performance and fuel efficiency. By keeping the fuel cool, these coolers ensure that the engine receives the best possible fuel-air mixture, resulting in increased power and better mileage. This simple yet effective modification can be a valuable addition to any vehicle, especially those seeking to extract the maximum potential from their engines.
Understanding the Key Differences: Brake vs. Fuel Lines
You may want to see also
Heat Dissipation: Efficient heat dissipation prevents fuel line overheating
The concept of fuel line coolers is an intriguing one, especially when considering the performance and longevity of engines. These devices are designed to address a critical aspect of engine management: heat dissipation. Efficient heat dissipation is crucial for preventing fuel lines from overheating, which can have detrimental effects on engine performance and overall reliability.
When fuel is injected into an engine, it undergoes a rapid combustion process, generating a significant amount of heat. This heat can cause the fuel lines to overheat, leading to a host of issues. Overheating fuel lines can result in reduced fuel pressure, poor atomization, and even fuel degradation. These problems can negatively impact engine performance, leading to decreased power output, reduced fuel efficiency, and, in extreme cases, engine failure.
To combat this, fuel line coolers are employed. These coolers are designed to absorb and dissipate the heat generated by the fuel, ensuring that the fuel lines remain at an optimal temperature. The primary function of a fuel line cooler is to provide a pathway for the heat to escape, preventing the fuel lines from becoming excessively hot. This is achieved through a combination of materials and design features that facilitate efficient heat transfer.
One key aspect of heat dissipation is the use of materials with high thermal conductivity. These materials, such as aluminum or copper, are strategically placed within the fuel line cooler to maximize heat transfer. By allowing heat to quickly move through the cooler, these materials ensure that the fuel lines are effectively cooled. Additionally, the design of the cooler may include fins or other surface enhancements to increase the surface area, further enhancing heat dissipation.
In summary, efficient heat dissipation is a critical component of fuel line coolers. By preventing fuel lines from overheating, these devices ensure that the fuel remains at an optimal temperature, promoting efficient combustion and engine performance. The use of materials with high thermal conductivity and strategic design features contributes to the overall effectiveness of heat dissipation, making fuel line coolers an essential component in maintaining engine health and longevity.
Unleash the Power: Milwaukee's Fuel Line Revolution
You may want to see also
Durability: High-quality materials ensure coolers withstand extreme conditions
Durability is a critical aspect of fuel line coolers, especially when it comes to ensuring their effectiveness and longevity in harsh environments. High-quality materials play a pivotal role in making these coolers robust and reliable. The extreme conditions that fuel lines and coolers often face include varying temperatures, pressure fluctuations, and exposure to corrosive elements. To combat these challenges, manufacturers utilize advanced materials that can withstand such demands.
One of the key materials used in constructing these coolers is high-density, heat-resistant plastics. These plastics are engineered to maintain their structural integrity under intense heat and cold, ensuring that the cooler can operate efficiently across a wide temperature range. Additionally, the use of reinforced polymers and composites provides excellent impact resistance, making the cooler less susceptible to damage from accidental bumps or collisions.
Metallic components, such as aluminum and stainless steel, are also integral to the durability of fuel line coolers. Aluminum is favored for its lightweight nature and excellent heat dissipation properties, allowing the cooler to manage high temperatures effectively. Stainless steel, on the other hand, offers superior corrosion resistance, which is crucial when the cooler is exposed to fuel, engine oil, or other potentially corrosive substances. The combination of these metallic materials with advanced plastics creates a robust and durable assembly.
Furthermore, the construction techniques employed in manufacturing these coolers are designed to enhance their durability. Welding and bonding processes are meticulously executed to ensure a strong and leak-proof seal, preventing any potential fuel leaks. The use of precision-engineered fittings and brackets further reinforces the structure, allowing the cooler to withstand the rigors of the road or trail.
In summary, the durability of fuel line coolers is a result of the careful selection of high-quality materials and the application of advanced manufacturing techniques. By utilizing materials that can endure extreme conditions, these coolers are built to last, providing reliable cooling performance for fuel lines in various automotive and recreational vehicle applications. This focus on durability ensures that the coolers can withstand the challenges of the real world, contributing to the overall efficiency and safety of the vehicle's cooling system.
Mastering the Art of Fuel Line Maintenance: A Guide to Running Your VT500C
You may want to see also
Installation and Maintenance: Proper installation and regular maintenance are essential for optimal performance
Proper installation and regular maintenance are crucial for ensuring the effectiveness of a fuel line cooler, as they play a vital role in enhancing engine performance and longevity. When installing a fuel line cooler, it is essential to follow the manufacturer's guidelines to ensure a secure and efficient setup. The cooler should be positioned in a location that provides easy access for maintenance and allows for adequate airflow to prevent overheating. During installation, pay close attention to the routing of the fuel lines. Ensure that the lines are not kinked or twisted, as this can restrict fuel flow and reduce the cooler's efficiency. Secure the lines with appropriate clamps or brackets to prevent movement and potential damage.
After installation, regular maintenance is key to keeping the fuel line cooler in optimal condition. Start by checking the cooler's temperature and pressure regularly. Over time, the cooler's performance may degrade due to the accumulation of contaminants and debris in the fuel. Clean the cooler periodically to remove any built-up grime. This can be done by flushing the system with a suitable fuel cleaner or by removing the cooler and cleaning it manually. It is recommended to consult the manufacturer's instructions for specific cleaning procedures. Additionally, inspect the cooler for any signs of damage, leaks, or blockages. Address any issues promptly to prevent further complications.
Regularly inspecting the fuel lines for wear and tear is also essential. Look for any cracks, punctures, or signs of corrosion. Replace damaged lines to maintain proper fuel flow and prevent potential engine issues. Furthermore, monitoring the engine's performance is crucial. Keep an eye on fuel consumption, engine temperature, and overall power output. If you notice any unusual behavior or a decline in performance, it may indicate a problem with the fuel line cooler or related components. Addressing these issues promptly can save you from potential engine damage and costly repairs.
In summary, proper installation and regular maintenance are critical to the success of fuel line coolers. By following installation guidelines, cleaning and inspecting the cooler and fuel lines, and monitoring engine performance, you can ensure that your fuel line cooler functions optimally, providing improved engine efficiency and longevity. Remember, regular maintenance is an investment in your vehicle's health and can help avoid potential breakdowns and costly repairs.
Troubleshooting: Ford Explorer Fuel Pump Issues and Fuel Line Removal
You may want to see also
Frequently asked questions
Fuel line coolers are designed to regulate the temperature of the fuel as it passes through the fuel lines, especially in high-performance engines or vehicles operating in extreme climates. They work by providing a longer path for the fuel to travel, allowing it to dissipate heat more efficiently. The cooler often consists of a heat exchanger, which can be a coil or a series of fins, that draws heat away from the fuel, keeping it cooler.
Fuel line coolers are beneficial in several scenarios. Firstly, they prevent fuel degradation, especially in high-temperature environments, which can lead to the formation of varnish and sludge in the engine. Secondly, they improve fuel efficiency by maintaining the fuel at an optimal temperature, ensuring it burns more efficiently. This can be particularly useful for diesel engines, where fuel temperature directly impacts performance and longevity.
While fuel line coolers are commonly used in performance-oriented vehicles, trucks, and boats, they can be installed on a wide range of vehicles. However, the installation process may vary depending on the vehicle's make and model. It is essential to choose a cooler that is compatible with your vehicle's fuel system and ensure it has the necessary mounting points and connections.
In some cases, fuel line coolers might introduce additional complexity and potential points of failure in the fuel system. If not installed or maintained properly, they could lead to fuel leaks or contamination. Additionally, the cost of a fuel line cooler and the associated installation might be a significant investment, especially for older vehicles that may require custom fabrication. Regular maintenance and monitoring of the cooler's performance are crucial to ensure its effectiveness and longevity.