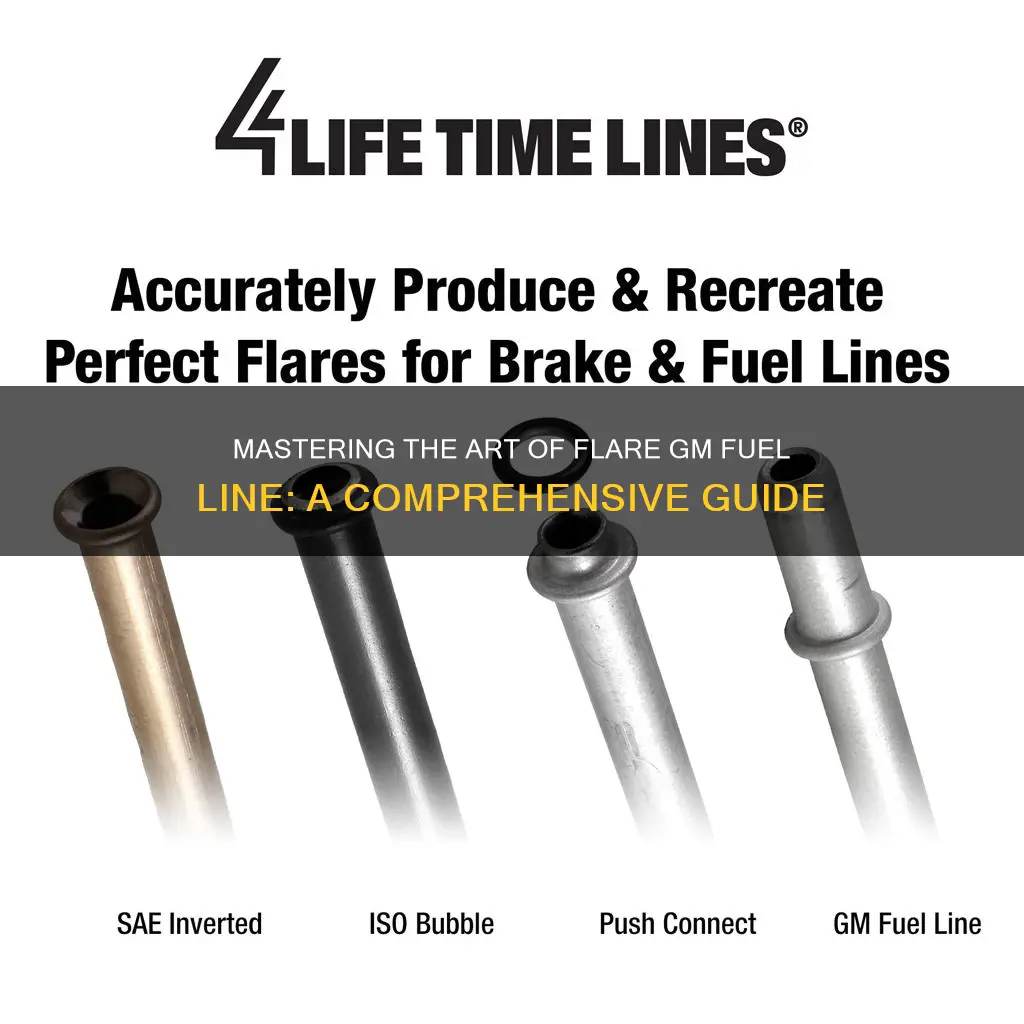
Flaring a GM fuel line is a crucial step in the process of troubleshooting or repairing a vehicle's fuel system. This technique involves using a specialized tool to temporarily seal off the fuel line, allowing for safe and controlled release of pressure. By following a few simple steps, you can effectively flare a GM fuel line, ensuring a secure and leak-free connection. This process is essential for maintaining the vehicle's performance and safety, especially when dealing with high-pressure fuel systems.
What You'll Learn
- Fuel Line Inspection: Check for damage, kinks, or clogs using a flashlight and a mirror
- Flaring Tools: Gather necessary tools: flare gauge, die, and mandrel
- Flaring Process: Follow a step-by-step guide for precise flare creation
- Safety Precautions: Wear protective gear and ensure a well-ventilated workspace
- Testing and Adjustment: Test the flare for tightness and make adjustments as needed
Fuel Line Inspection: Check for damage, kinks, or clogs using a flashlight and a mirror
When inspecting the fuel lines on a GM vehicle, it's crucial to ensure they are in good condition to prevent potential fuel system issues. Here's a step-by-step guide on how to inspect the fuel lines using basic tools and a bit of visual acuity:
Gather Your Tools: You'll primarily need a flashlight and a mirror, preferably a small, handheld mirror with a good reflective surface. A bright LED flashlight is ideal for this task as it will help you see into tight spaces.
Locate the Fuel Lines: Start by locating the fuel lines under the hood. These lines are typically black or dark-colored and can be found running from the fuel tank to the engine. Identify the primary fuel line, which is usually the largest, and the smaller return lines.
Examine for Damage: Carefully inspect each fuel line for any signs of damage. Look for cuts, punctures, or tears in the rubber casing. Check for any cracks or brittleness, especially at the points where the lines connect to the fuel tank and the engine. Also, inspect the lines for any signs of corrosion or rust, particularly if the vehicle has been exposed to harsh weather conditions.
Check for Kinks and Clogs: Use your mirror to peer into the fuel lines and look for any kinks or bends that might restrict fuel flow. Ensure that the lines are not pinched or crushed against any hard surfaces. Additionally, check for any clogs or blockages. If you notice any debris or contaminants in the lines, it could indicate a potential issue.
Test for Leaks: While inspecting, also check for any signs of fuel leaks. If you notice any wet spots or fuel residue around the fuel lines, it could indicate a leak. Leaks can be caused by damage, corrosion, or loose connections. If you identify a leak, it's essential to address it promptly to prevent further damage and potential safety hazards.
Record Any Issues: As you inspect, make a mental note or jot down any issues you find. This could include the location of damage, kinks, or leaks. If you're unsure about the severity of an issue, it's best to consult a professional mechanic for advice.
Regular fuel line inspections are an essential part of vehicle maintenance, ensuring that your GM car's fuel system operates efficiently and safely. By following these steps, you can identify potential problems early on and take the necessary actions to keep your vehicle in optimal condition.
Can Fuel Lines Handle the Heat? Uncovering the Limits of Fuel Line Durability
You may want to see also
Flaring Tools: Gather necessary tools: flare gauge, die, and mandrel
Before you begin the process of flaring a GM fuel line, it's crucial to gather the right tools to ensure a successful and safe outcome. Flaring is a technique used to create a smooth, bent transition at the end of a fuel line, allowing it to fit securely into various components of the fuel system. Here's a detailed guide on the essential tools required for this task:
Flaring Gauge: This is the primary tool for flaring. It is a specialized measuring device designed to ensure the fuel line is bent to the correct angle and radius. The flare gauge typically consists of a ruler-like body with adjustable arms that can be set to the desired flare angle and radius. When using a flare gauge, you'll position it along the fuel line, aligning the arms with the line's curvature, and then adjust the gauge to match the required specifications. This tool is crucial for achieving the precise flare needed to connect the fuel line to various components without causing damage or leaks.
Die: A flare die is a cylindrical tool with a specific flare profile. It is used in conjunction with the flare gauge to create the desired flare. The die is inserted into the end of the fuel line, and as you apply force, it forms the line to the required shape. Different dies are available for various flare angles and sizes, ensuring compatibility with different GM fuel line specifications. It's essential to select the appropriate die for your specific flare requirements.
Mandrill: A mandrel is a cylindrical mandrel that provides support and guidance during the flaring process. It is inserted into the fuel line before flaring, ensuring that the line maintains its shape and doesn't collapse or kink. The mandrel is especially useful for larger fuel lines or when creating more complex flares. After flaring, the mandrel is removed, leaving the fuel line with the desired flare. This tool is particularly handy for achieving consistent and accurate flares, especially in tight or hard-to-reach areas.
Gathering these tools is the first step in mastering the art of flaring GM fuel lines. Each tool plays a specific role in ensuring the flare is precise, safe, and compatible with the fuel system's requirements. With the right equipment, you'll be well-prepared to tackle flaring tasks efficiently and effectively.
Signs of Frozen Fuel Lines: A Winter Checklist
You may want to see also
Flaring Process: Follow a step-by-step guide for precise flare creation
The flaring process is a crucial step in creating a precise and effective flare for your GM fuel line. It involves shaping the metal to fit the desired flare angle and size, ensuring a secure and leak-free connection. Here's a step-by-step guide to help you master this technique:
- Prepare Your Materials: Begin by gathering the necessary tools and materials. You'll need a metal flare tool, which is specifically designed for this purpose, and a length of fuel line that matches the diameter of your existing line. Ensure you have the correct flare angle specified for your application, typically 45 degrees for GM fuel lines.
- Clean and Prepare the Surface: Before starting, ensure the end of the fuel line is clean and free of any debris or contaminants. Use a wire brush or a small wire brush attachment on your power drill to gently clean the area. This step is essential to ensure a strong bond during the flaring process.
- Position the Fuel Line: Hold the fuel line in place with one hand, and use the metal flare tool to apply pressure and shape the metal. Start by bending the line at a 45-degree angle, ensuring the flare is symmetrical. You can use a pair of pliers to hold the line in place temporarily while you work on the flare.
- Create the Flare: With the tool, apply firm pressure to the end of the fuel line, bending it further until it forms a tight, smooth flare. The flare should be long enough to provide a secure connection but not so long that it becomes difficult to manage. Take your time and use steady, controlled movements to avoid distorting the flare.
- Check for Precision: Once the flare is created, inspect it carefully. The flare should be free of any sharp edges or uneven bends. Use a magnifying glass or a bright light to ensure the flare is smooth and consistent. If any adjustments are needed, carefully reshape the flare using the flare tool, taking care not to over-bend the metal.
- Secure the Connection: After achieving the desired flare, secure the connection by inserting a flare nut onto the flare. Tighten the nut by hand first, then use a wrench to ensure a snug fit. Check for any leaks around the flare by applying a small amount of diesel fuel or a suitable sealant to the connection and observing if any seepage occurs. If there are no leaks, your flare is complete and ready for use.
Remember, practice makes perfect when it comes to flaring. Take your time, be patient, and don't rush the process. With these steps, you'll be able to create precise and reliable flares for your GM fuel line connections.
Choosing the Right Material for Your Motorcycle's Flexible Fuel Line
You may want to see also
Safety Precautions: Wear protective gear and ensure a well-ventilated workspace
When working on your vehicle's fuel system, especially when flaring a GM fuel line, safety should always be your top priority. This involves taking several precautions to protect yourself and those around you. Firstly, it is crucial to wear appropriate protective gear. Safety goggles are essential to shield your eyes from any potential splashes or debris that could occur during the flaring process. Additionally, consider wearing gloves to protect your hands from sharp edges or hot surfaces. A respirator or dust mask is also recommended to prevent inhaling any harmful fumes or fuel vapor.
A well-ventilated workspace is another critical aspect of safety. Ensure that your work area has proper ventilation to avoid the buildup of hazardous gases. Open windows or use a fan to create a constant flow of fresh air. If working in a confined space, consider using a portable air purifier to maintain a safe breathing environment. This is particularly important when dealing with flammable substances like fuel.
Before beginning the flaring process, inspect your workspace for any potential hazards. Remove any obstacles or tripping hazards that could cause accidents. Keep the area clean and organized to minimize the risk of injury. It is also advisable to work in a well-lit area to ensure you can see the flaring process clearly and make any necessary adjustments.
Remember, taking these safety precautions is not just a recommendation but a necessity. Fuel lines can be under pressure, and the process of flaring involves heat and sharp tools. By wearing the right protective gear and ensuring a safe working environment, you significantly reduce the risks associated with this task. Always prioritize your well-being and that of those around you to make the project a success.
Mastering Metal Fuel Line Cutting: A Comprehensive Guide
You may want to see also
Testing and Adjustment: Test the flare for tightness and make adjustments as needed
When working on a GM fuel line flare, ensuring the proper tightness is crucial to maintaining a secure and leak-free connection. Here's a step-by-step guide on how to test and adjust the flare for optimal performance:
Testing for Tightness:
- Visual Inspection: Begin by visually examining the flare connection. Look for any visible signs of damage, cracks, or deformities in the flare or the fuel line. Ensure that the flare is not bent or distorted, as this could affect its ability to seal properly.
- Thread Engagement: Check the thread engagement between the flare and the fuel line. The threads should be fully engaged, with no gaps or spaces between them. Use a thread gauge or a caliper to measure the thread depth and ensure it meets the manufacturer's specifications.
- Leak Test: Perform a leak test to verify the integrity of the flare connection. Apply a small amount of diesel fuel or a suitable lubricant to the flare and fuel line interface. Then, tighten the flare further by hand, ensuring it is snug. Finally, release the flare and observe if any fuel escapes. If there are no leaks, the flare is likely tight enough.
Adjusting the Flare:
- If the leak test reveals any fuel leakage, it indicates that the flare may not be tight enough. In this case, you'll need to make adjustments:
- Loosen the flare connection slightly, being careful not to strip the threads.
- Reapply the lubricant to the flare and fuel line.
- Tighten the flare by hand, ensuring it is secure but not over-tightened.
- Repeat the leak test to confirm the flare is now tight and leak-free.
- It's important to use the right amount of force when tightening the flare. Over-tightening can damage the fuel line or flare, while under-tightening may result in leaks.
- Consider using a torque wrench for precise tightening, especially if you're working on multiple flare connections. This ensures consistency and helps prevent over-tightening.
Remember, the goal is to achieve a secure and tight connection without causing any damage. Regularly testing and adjusting the flare connections will help ensure the longevity and reliability of your GM fuel line system. Always refer to the vehicle's manual or manufacturer guidelines for specific torque specifications and recommendations.
Flaring Fuel Lines: When and Why You Need to Know
You may want to see also
Frequently asked questions
Flaring a fuel line is a process used to create a precise bend or flare in the line, which helps to improve the flow of fuel and ensure a secure connection. This technique is commonly employed in automotive repair to optimize fuel delivery and prevent leaks.
Here's a general process: First, ensure you have the necessary tools, including a flare tool, a fuel line, and a suitable solvent. Cut the fuel line to the desired length and clean the ends. Then, apply the solvent to the ends and insert them into the flare tool. Adjust the tool to create the desired flare angle, typically 45 degrees. Finally, secure the flare using a flare nut and torque it according to the vehicle's specifications.
It's important to use the correct flare angle for your specific fuel line size and application. Over-flaring can lead to reduced fuel flow, while under-flaring may result in leaks. Always refer to the vehicle's manual for the recommended torque specifications. Additionally, ensure the fuel line is free of any debris or contaminants before flaring to achieve a secure and reliable connection.