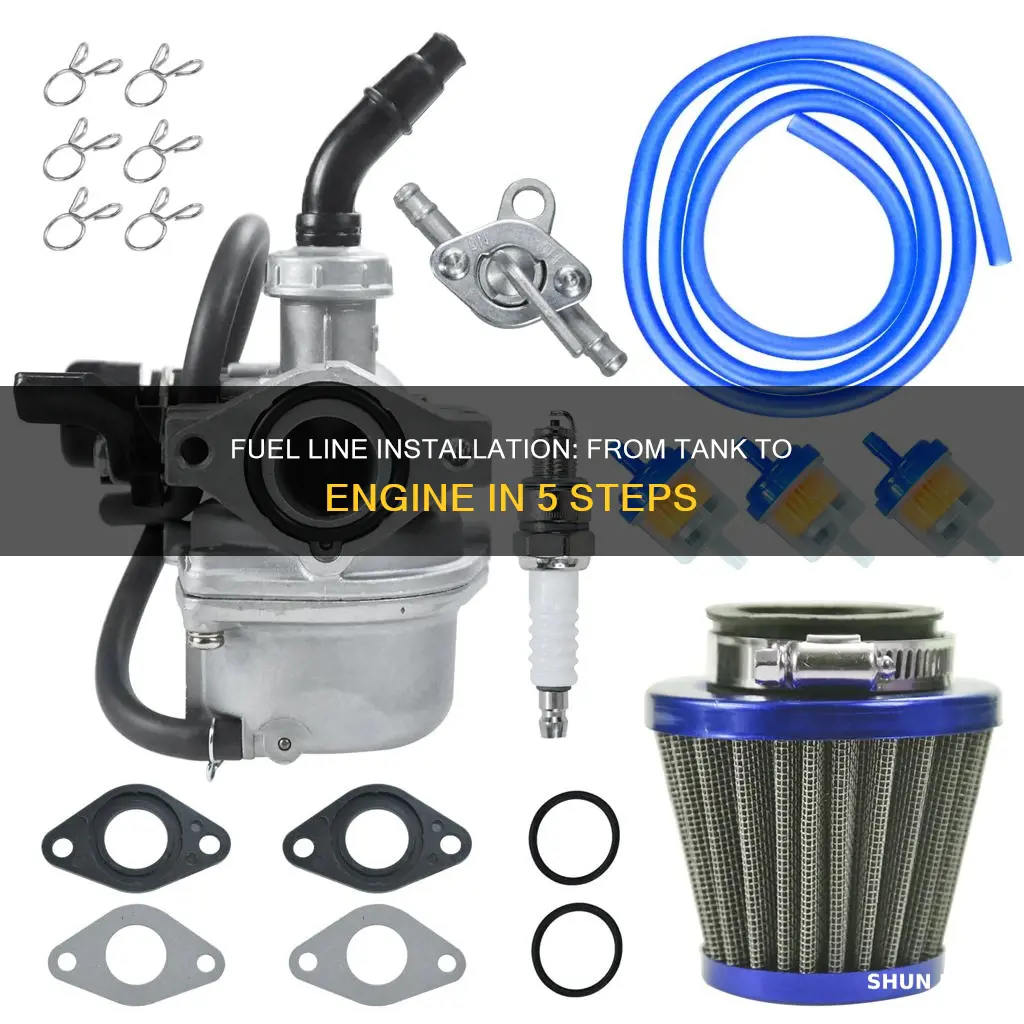
Installing a fuel line from the tank to the engine is a crucial step in ensuring your vehicle's performance and safety. This process involves connecting the fuel tank to the engine's fuel injection system or carburetor, allowing the engine to receive the necessary fuel for operation. In this guide, we will provide a step-by-step overview of how to install a fuel line from the tank to the engine, specifically focusing on the PZ19 engine model. By following these instructions, you can ensure a proper and secure fuel supply, optimizing your vehicle's performance and reliability.
Characteristics | Values |
---|---|
Fuel Line Material | Typically made of rubber or plastic, such as vinyl or EPDM. |
Fuel Line Diameter | Varies depending on the engine's fuel requirements, often ranging from 3/8" to 1/2" in diameter. |
Fuel Line Length | Determined by the distance between the fuel tank and the engine, usually measured in inches. |
Clamps | Used to secure the fuel line to the tank and engine, ensuring a tight and leak-free connection. |
Fittings | Special connectors to join the fuel line segments and allow for easy installation and removal. |
Flexibility | Essential for accommodating engine movement and vibrations. |
Pressure Rating | Must be able to withstand the fuel pressure in the system, often specified in pounds per square inch (PSI). |
Temperature Resistance | Capable of withstanding the operating temperatures of the engine and fuel. |
Installation Process | Involves cutting the fuel line to length, attaching fittings, and securely fastening it to the tank and engine. |
Safety Considerations | Proper installation is crucial to prevent fuel leaks, which can be dangerous and cause fires. |
What You'll Learn
- Fuel Tank Inspection: Check for damage, ensure proper fuel level and cleanliness
- Fuel Line Routing: Route the line through the engine compartment, following the manufacturer's diagram
- Fuel Pump Installation: Secure the pump and connect it to the fuel line
- Fuel Filter Placement: Install the filter in the line, ensuring a tight fit
- Fuel Line Testing: Use a pressure gauge to test for leaks and proper fuel flow
Fuel Tank Inspection: Check for damage, ensure proper fuel level and cleanliness
When inspecting the fuel tank, it's crucial to check for any signs of damage, as this can affect the overall performance and safety of your vehicle. Start by visually examining the tank for any visible cracks, corrosion, or signs of impact damage. Look for any areas where the tank might have been compromised, especially if there are any existing leaks or unusual noises. Ensure that the tank is securely mounted and that all mounting points are intact and tight.
Next, verify the fuel level. Check the fuel gauge to ensure it accurately reflects the amount of fuel in the tank. If the gauge is not functioning correctly, consider using a dipstick to manually check the fuel level. It's important to note the fuel level and compare it to the vehicle's specifications to ensure it falls within the optimal range.
Additionally, assess the cleanliness of the fuel tank. Over time, fuel tanks can accumulate sediment, water, and contaminants, which can lead to performance issues. Remove the fuel tank (if possible) and inspect the inside for any signs of corrosion, rust, or the presence of debris. If necessary, use a fuel filter to trap any contaminants and improve fuel quality. Regularly cleaning the fuel tank can help maintain engine performance and longevity.
For vehicles with complex fuel systems, such as those with electronic fuel injection, it's essential to consult the vehicle's manual for specific inspection procedures. Some vehicles may require additional checks, such as verifying the condition of the fuel pump and ensuring proper fuel pressure. Always refer to the manufacturer's guidelines to ensure you perform the correct inspections and maintenance.
By thoroughly inspecting the fuel tank, you can identify potential issues early on, ensuring that your vehicle operates efficiently and safely. Regular maintenance and attention to the fuel system are key to preventing costly repairs and maintaining optimal vehicle performance.
Mastering Plastic Fuel Line Removal: A Step-by-Step Guide
You may want to see also
Fuel Line Routing: Route the line through the engine compartment, following the manufacturer's diagram
When installing a fuel line from the tank to the engine, it's crucial to follow the manufacturer's diagram for the specific model, such as the PZ19. This diagram will provide detailed instructions tailored to your vehicle's design, ensuring a proper and safe installation. Here's a step-by-step guide on how to route the fuel line through the engine compartment:
Start by locating the fuel tank and identifying the fuel line that needs to be connected to the engine. The diagram will show the exact position of the fuel inlet on the engine and the path the line should take. Carefully trace the route from the tank to the engine, ensuring you understand the layout of the engine compartment. This step is critical to avoid any potential damage during the installation process.
Once you've studied the diagram, begin routing the fuel line through the engine compartment. Typically, the line will need to pass through various components like the firewall, engine mounts, or other engine parts. Use the appropriate tools, such as fuel line cutters and crimping tools, to ensure clean and secure connections. Take your time to carefully maneuver the line through the designated path, making sure it is not kinked or pinched, as this could lead to fuel leaks.
As you progress, pay close attention to any bends or turns in the line. The manufacturer's diagram will specify the required angles and radii for these bends to ensure a smooth and secure installation. Avoid sharp bends that could cause stress on the fuel line, as this may lead to cracks or leaks over time. Use fuel line clips or ties to secure the line in place, especially where it passes through tight spaces or near moving parts.
Finally, once the fuel line is routed through the engine compartment, connect it to the engine's fuel inlet using the appropriate fittings and connectors. Ensure a tight and secure connection to prevent any fuel loss. Double-check all connections and the overall routing to guarantee a safe and functional fuel system. Following the manufacturer's diagram will ensure a precise and reliable installation, minimizing the risk of future issues.
Nylon Fuel Line Repair: Quick Tips for a Successful Fix
You may want to see also
Fuel Pump Installation: Secure the pump and connect it to the fuel line
When installing a fuel pump, it's crucial to ensure a secure and proper connection to the fuel line to maintain optimal performance and prevent potential issues. Here's a step-by-step guide to securing the pump and connecting it to the fuel line:
Prepare the Components: Before you begin, ensure you have all the necessary components, including the fuel pump, fuel line, fittings, and any required tools. Inspect the fuel pump for any signs of damage or wear and check that it is compatible with your vehicle's specifications.
Mounting the Pump: Locate the designated mounting points on your vehicle's engine bay. Securely fasten the fuel pump using the appropriate mounting hardware. Ensure that the pump is positioned in a way that allows easy access for maintenance and has sufficient clearance from other components.
Connecting the Fuel Line: Start by attaching one end of the fuel line to the pump's outlet port. Tighten the fitting securely, ensuring a tight seal. Then, connect the other end of the fuel line to the vehicle's fuel rail or injection system, following the manufacturer's instructions for the specific connection. Use fuel line connectors or fittings that are compatible with the fuel type and system.
Testing and Verification: After connecting the fuel line, start the vehicle's engine and check for any leaks around the connections. Listen for any unusual noises from the fuel system. If everything is secure and functioning correctly, the engine should start smoothly. Monitor the fuel gauge and ensure it reads the correct fuel level.
Final Adjustments: If any adjustments are required, such as fuel pressure regulation, refer to the vehicle's manual or consult a professional mechanic. Fine-tune the fuel pump's settings to match the vehicle's requirements, ensuring optimal fuel delivery and engine performance. Regularly inspect the connections and fittings to maintain a secure and reliable fuel system.
Diagnosing Fuel Line Issues in Outboard Motors: A Comprehensive Guide
You may want to see also
Fuel Filter Placement: Install the filter in the line, ensuring a tight fit
To ensure a proper fuel filter installation, it's crucial to follow these steps for optimal performance and longevity of your fuel system. Begin by acquiring the correct fuel filter, one that fits your specific vehicle model and engine type. This ensures compatibility and the right size for a secure fit.
Locate the fuel line that connects your fuel tank to the engine, typically a flexible rubber or plastic hose. Identify the point where the filter will be installed, usually a few inches away from the tank. Carefully cut or punch a hole in the fuel line to accommodate the filter. Ensure the hole is clean and free of debris to prevent any blockages.
Now, take the fuel filter and slide it over the fuel line, aligning the filter's inlet and outlet ports with the fuel line's openings. Apply firm pressure to secure the filter in place, ensuring it is tightly fitted. A snug fit is essential to prevent fuel leakage and maintain a sealed connection. Check for any signs of fuel seepage around the filter connection to ensure it is properly sealed.
If you encounter any resistance or difficulty in sliding the filter onto the line, it may indicate a need for a slightly larger filter or a different installation approach. In such cases, consult the vehicle's manual or seek professional advice to ensure a proper fit.
Once installed, verify the filter's orientation and ensure it is not kinked or pinched, as this can restrict fuel flow. Regularly inspect the filter for any signs of wear or contamination, and replace it as recommended by the manufacturer to maintain optimal fuel system performance. Proper filter placement and a tight fit are key to a successful fuel line installation.
Unveiling the Standard Fuel Line Size: A Comprehensive Guide
You may want to see also
Fuel Line Testing: Use a pressure gauge to test for leaks and proper fuel flow
When it comes to ensuring the proper installation and functionality of a fuel line from the tank to the engine, testing is an essential step that should not be overlooked. One of the most effective methods for this task is using a pressure gauge. This tool allows you to check for any potential leaks and verify that the fuel is flowing correctly, ensuring optimal engine performance.
Here's a step-by-step guide on how to use a pressure gauge for fuel line testing:
- Preparation: Before you begin, ensure that the engine is off and the vehicle is in a secure position. Locate the fuel tank and the fuel line that connects it to the engine's fuel pump or injection system. Identify the pressure gauge's connection points, typically a male and female thread or a quick-connect fitting.
- Connect the Gauge: Securely attach the pressure gauge to the fuel line. Make sure it is tightly connected to avoid any potential leaks. Check that the gauge is functioning properly by reading the initial pressure. This initial reading will serve as a baseline for comparison later.
- Simulate Engine Operation: Start the engine and allow it to run for a few minutes. This step is crucial as it mimics the conditions when the fuel system is actively in use. During this time, the fuel pump should be drawing fuel from the tank, and the engine should be consuming it.
- Monitor Pressure: Keep an eye on the pressure gauge while the engine is running. The pressure should remain relatively stable, indicating that the fuel is flowing correctly. If you notice a significant drop in pressure, it could be a sign of a leak or restricted flow.
- Check for Leaks: After the engine has been running, turn it off and recheck the pressure gauge. Any drop in pressure after the engine is turned off suggests a potential leak in the fuel line. Inspect the connections and the fuel line for any signs of damage or corrosion.
- Adjustments and Re-testing: If a leak is detected, you may need to adjust the connections or even replace the fuel line. Once the issue is resolved, repeat the testing process to ensure the problem is fixed.
By following these steps, you can effectively use a pressure gauge to test the fuel line's integrity and performance. This method is a valuable tool for both DIY enthusiasts and professionals, ensuring that the fuel system is functioning optimally and safely. Remember, proper testing can help prevent potential engine issues caused by faulty fuel lines.
Classic BMW E28: Metal Fuel Line or Not?
You may want to see also
Frequently asked questions
The installation process involves several steps to ensure a secure and leak-free connection. First, you'll need to locate the fuel tank and identify the appropriate fittings and connectors for the fuel line. Then, cut the fuel line to the desired length and attach the necessary adapters or reducers to match the tank and PZ19 connections. Use fuel-resistant tape or clamps to secure the connections and prevent any leaks.
It's crucial to use fuel-rated lines designed for automotive applications. Regular garden hoses or plastic pipes are not suitable due to their lack of flexibility and resistance to fuel degradation. Opt for fuel-specific materials like rubber, vinyl, or braided steel to ensure longevity and compatibility with the fuel system.
Start by cleaning the surfaces of the fuel tank and PZ19 to remove any dirt or debris. Apply a suitable fuel-resistant sealant or tape to the threads or fittings. Tighten the connections securely, but be careful not to overtighten, as it may damage the components. Regularly check for leaks by applying a small amount of diesel or fuel to the connections and observing if any seepage occurs.
Yes, you'll need a few essential tools. A fuel line cutter or a sharp knife will help you measure and cut the fuel line accurately. Thread seal tape or pipe compound is essential for sealing the threads. You might also consider using a fuel line clamp or a hose clamp to secure the line in place. Having a fuel-resistant tape or compound for any additional sealing is also recommended.
If you face any challenges, such as difficult connections or leaks, it's best to consult a professional mechanic or automotive specialist. They can provide expert guidance and ensure the installation is done correctly. Always prioritize safety and proper functionality to avoid any potential hazards associated with fuel systems.