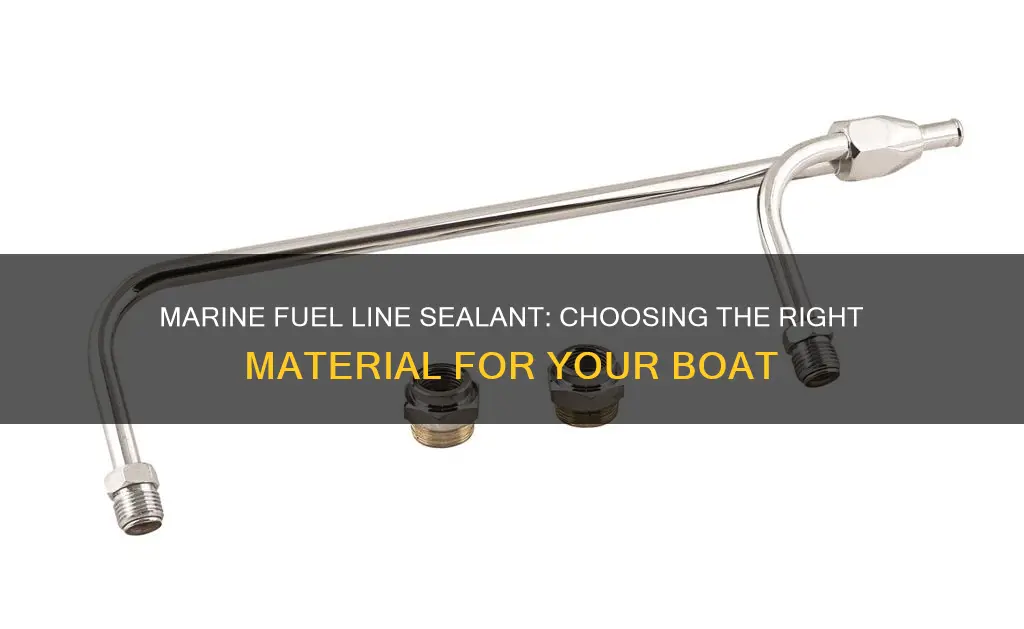
When it comes to marine fuel lines, choosing the right sealant is crucial for ensuring optimal performance and longevity. Marine environments present unique challenges, including exposure to saltwater, UV radiation, and varying temperatures. Therefore, the sealant must be able to withstand these harsh conditions while maintaining a tight seal. In this article, we will explore the different types of sealants available for marine fuel lines, their advantages, and how to select the most suitable one for your specific needs.
What You'll Learn
- Material Compatibility: Choose a sealant that is compatible with marine fuel types and materials
- Environmental Resistance: Select a sealant that can withstand marine environments, including UV exposure and saltwater
- Flexibility and Strength: Opt for a sealant that is flexible and strong to withstand movement and pressure
- Temperature Range: Ensure the sealant can handle the temperature extremes of marine environments
- Application Ease: Consider ease of application, including curing time and tool requirements
Material Compatibility: Choose a sealant that is compatible with marine fuel types and materials
When it comes to choosing the right sealant for marine fuel lines, material compatibility is a critical factor to consider. Marine environments are harsh and diverse, with various fuel types and materials used in construction. The chosen sealant must be compatible with these specific components to ensure long-lasting performance and prevent damage.
Marine fuel lines often carry different types of fuels, such as gasoline, diesel, or biofuels, each with unique chemical compositions. For instance, diesel fuel contains additives that can be corrosive to certain sealants. Therefore, it is essential to select a sealant that can withstand the specific fuel type used in the marine vessel. Look for sealants that are specifically formulated to resist the corrosive effects of marine fuels, ensuring the integrity of the fuel lines over time.
The materials used in marine fuel lines also play a significant role in sealant selection. Common materials include rubber, plastic, and metal. Rubber fuel lines, for example, may require a sealant that adheres well to rubber and can provide a flexible seal. On the other hand, plastic fuel lines might need a sealant that is compatible with the specific plastic type to avoid cracking or degradation. Some sealants are designed to be versatile and compatible with multiple materials, ensuring a reliable seal regardless of the fuel line composition.
To ensure compatibility, it is advisable to consult manufacturer guidelines and specifications. Many sealant manufacturers provide detailed information about the materials their products are compatible with. This information can be found on the sealant's packaging or through the manufacturer's website. By cross-referencing the fuel type and fuel line materials with the sealant's compatibility data, you can make an informed decision and select the most suitable sealant.
In summary, material compatibility is a crucial aspect when choosing a sealant for marine fuel lines. The sealant should be able to withstand the specific fuel types and materials used in the marine environment. By considering the unique characteristics of marine fuels and fuel lines, and referring to manufacturer guidelines, you can select a sealant that ensures a secure and long-lasting seal, contributing to the overall safety and efficiency of the marine vessel's fuel system.
Optimizing Performance: Choosing the Right Fuel Line Size for Your 3/8 Inline Filter
You may want to see also
Environmental Resistance: Select a sealant that can withstand marine environments, including UV exposure and saltwater
When it comes to choosing the right sealant for marine fuel lines, environmental resistance is a critical factor to consider. Marine environments present unique challenges due to their exposure to harsh conditions, including UV radiation and saltwater corrosion. These elements can significantly impact the performance and longevity of the sealant, as well as the overall integrity of the fuel line system.
To ensure optimal protection, it is essential to select a sealant that is specifically designed to withstand these marine conditions. Look for sealants that are labeled as marine-grade or marine-resistant. These specialized sealants are formulated to provide excellent resistance against UV rays, which can cause degradation and cracking over time. UV-resistant sealants will maintain their flexibility and adhesion properties, ensuring a reliable seal even in the harshest marine environments.
Saltwater exposure is another critical aspect. Marine fuel lines are constantly immersed in saltwater, which can lead to corrosion and the breakdown of traditional sealants. Opt for sealants that offer superior saltwater resistance, often achieved through the use of advanced polymer compositions. These specialized sealants can form a protective barrier that prevents corrosion and maintains the structural integrity of the fuel line.
Additionally, consider the temperature range and flexibility of the sealant. Marine environments can experience extreme temperature fluctuations, so the chosen sealant should be able to withstand these variations without becoming brittle or losing its sealing properties. Look for sealants that offer a wide operating temperature range and excellent flexibility to accommodate thermal expansion and contraction.
In summary, when selecting a sealant for marine fuel lines, prioritize those with proven resistance to UV exposure and saltwater corrosion. Marine-grade sealants, designed specifically for these challenging environments, will provide the necessary protection against degradation and corrosion. By choosing the right sealant, you can ensure the long-term reliability and performance of your marine fuel line system.
Understanding Rubber Fuel Line OD: A Comprehensive Guide
You may want to see also
Flexibility and Strength: Opt for a sealant that is flexible and strong to withstand movement and pressure
When it comes to choosing the right sealant for your marine fuel lines, flexibility and strength are crucial factors to consider. Marine environments are harsh and demanding, with constant movement and pressure on the fuel lines. Therefore, selecting a sealant that can adapt to these conditions is essential to ensure long-lasting performance and prevent potential issues.
Flexibility is a key attribute that should not be overlooked. Marine fuel lines often experience vibrations and movements due to engine operation and the vessel's motion. A flexible sealant can accommodate these movements without cracking or breaking, providing a reliable seal. Look for sealants that are specifically designed to be pliable and adaptable, allowing them to conform to the fuel line's shape and size. This flexibility will help maintain a tight seal, preventing fuel leaks and potential damage to the vessel's interior.
Additionally, strength is another critical aspect. Marine fuel lines carry high-pressure fuel, and any sealant used must be able to withstand this pressure without compromising its integrity. Opt for sealants that offer excellent tensile strength and resistance to abrasion. These properties will ensure that the sealant can handle the constant stress and strain placed on it, maintaining a secure and reliable seal over time. A strong sealant will also provide added protection against potential impacts or damage from marine life, ensuring the longevity of your fuel lines.
Consider sealants that are specifically formulated for marine applications, as they are designed to meet the unique challenges of this environment. These specialized sealants often have enhanced flexibility and strength, making them ideal for fuel line installations. They can provide a durable barrier that protects against fuel leaks, corrosion, and the elements, ensuring the safety and efficiency of your marine vessel's fuel system.
In summary, when selecting a sealant for your marine fuel lines, prioritize flexibility and strength. Look for sealants that can adapt to the dynamic nature of marine environments, providing a secure and reliable seal. By choosing the right sealant, you can ensure the long-term performance and safety of your fuel lines, allowing you to navigate the waters with confidence.
Stihl BR600 Fuel Line Hose: Unlocking the Secrets
You may want to see also
Temperature Range: Ensure the sealant can handle the temperature extremes of marine environments
When it comes to marine fuel lines, choosing the right sealant is crucial to ensure the integrity and longevity of the system. One of the most critical factors to consider is the temperature range that the sealant can withstand. Marine environments are known for their extreme temperature variations, from scorching hot summers to freezing cold winters, and the sealant must be able to handle these fluctuations without compromising its performance.
In the vast ocean, temperatures can vary significantly, especially when considering the depth and the sun's exposure. During the day, temperatures near the surface can reach scorching levels, often exceeding 30°C (86°F). Conversely, at night or in deeper waters, temperatures can drop to near-freezing, sometimes as low as 4°C (39°F). These extreme temperature swings can cause materials to expand and contract, leading to potential damage or failure if the sealant is not temperature-resistant.
For marine fuel lines, it is essential to select a sealant that can maintain its flexibility and adhesion across this wide temperature range. Silicone-based sealants are often a good choice due to their excellent temperature resistance. They can withstand both high and low temperatures without becoming brittle or losing their sealing properties. Silicone sealants are known for their durability and ability to form a strong, flexible bond, making them ideal for marine applications.
Another option to consider is epoxy-based sealants, which are known for their exceptional temperature stability. Epoxy resins can endure extreme temperatures, making them suitable for fuel lines that are exposed to harsh marine conditions. However, it is important to note that epoxy sealants may become brittle at very low temperatures, so a balanced approach is necessary to ensure they remain effective in all seasons.
In summary, when selecting a sealant for marine fuel lines, temperature range is a critical consideration. The chosen sealant should be able to handle the extreme temperatures found in marine environments, ensuring the system's reliability and safety. By choosing a sealant with excellent temperature resistance, such as silicone or epoxy-based options, you can protect your marine fuel line investment and maintain the integrity of your vessel's critical systems.
Turbo LS Fuel Line Sizing: Expert Guide for Optimal Performance
You may want to see also
Application Ease: Consider ease of application, including curing time and tool requirements
When it comes to choosing a sealant for marine fuel lines, application ease is a critical factor to consider, especially for DIY enthusiasts and professionals alike. The process should be straightforward and efficient to ensure a successful and long-lasting repair. Here's a breakdown of the key aspects to focus on:
Curing Time: One of the most important considerations is the curing time of the sealant. Marine environments can be harsh, with constant exposure to saltwater, UV radiation, and temperature fluctuations. Therefore, a sealant that sets quickly and cures within a reasonable timeframe is ideal. Look for products that offer rapid curing, typically within 24-48 hours, ensuring that the fuel line can be restored to full functionality without prolonged downtime. This is particularly crucial for vessels that require frequent use or those in busy harbors where time is of the essence.
Tool Requirements: The application process should be as tool-friendly as possible. Marine fuel lines often require access to tight spaces and hard-to-reach areas, making it essential to have a sealant that can be applied without specialized equipment. A sealant that can be easily squeezed out of a cartridge or tube and has a consistent consistency will be easier to work with. Some sealants might require additional tools like caulking guns or brushes, which can add complexity to the job. Opt for products designed for simple, mess-free application, ensuring that the process is efficient and user-friendly.
Additionally, consider the flexibility of the sealant. Marine fuel lines often experience vibrations and movement, so a flexible sealant that can adapt to these conditions is vital. This flexibility will also make the application process smoother, allowing for better coverage and adhesion.
In summary, when selecting a sealant for marine fuel lines, prioritize those that offer rapid curing times and require minimal tools for application. This ensures that the repair process is efficient, cost-effective, and less time-consuming, allowing you to get back to your marine adventures swiftly. Remember, the right sealant will not only provide a temporary fix but also contribute to the long-term reliability of your vessel's fuel system.
Engine Lines: Fuel Smell Causes and Solutions
You may want to see also
Frequently asked questions
Sealants are essential in marine fuel lines to prevent fuel leaks and ensure a tight seal between components. They provide a barrier that protects against fuel evaporation, corrosion, and contamination, thus maintaining the integrity of the fuel system.
The choice of sealant depends on various factors, including the specific fuel type, operating conditions, and compatibility with the materials used in the fuel line. For marine applications, silicone-based sealants are commonly used due to their flexibility, resistance to fuel chemicals, and ability to withstand varying temperatures.
While some general-purpose sealants may work, it's best to use a sealant specifically designed for marine fuel systems. Marine environments often involve exposure to fuel, water, and harsh conditions, so a dedicated sealant ensures optimal performance and longevity.
Over time, sealants can degrade due to fuel exposure, temperature fluctuations, or physical damage. Look out for fuel leaks, reduced fuel pressure, or visible damage to the sealant. Regular inspections and maintenance can help identify issues early and ensure the sealant's effectiveness.
Yes, it's crucial to choose environmentally friendly sealants that do not contain harmful chemicals. Some sealants may have volatile organic compounds (VOCs) that can be released into the marine environment, potentially affecting aquatic life. Opt for low-VOC or VOC-free sealants to minimize ecological impact.