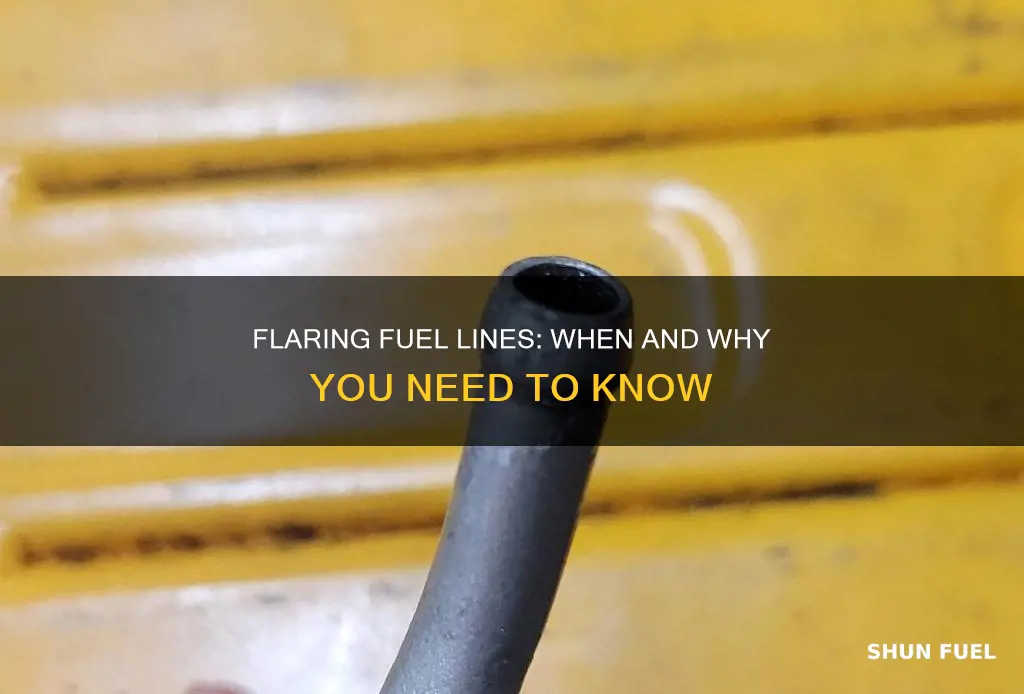
When it comes to vehicle maintenance, ensuring the proper functioning of fuel lines is crucial for optimal performance and safety. One common question that arises is whether it's necessary to flare fuel lines. This paragraph will delve into the importance of flaring fuel lines and its impact on the overall efficiency and longevity of your vehicle's fuel system. By understanding the role of flaring, readers will gain insights into why this process is essential and how it contributes to a well-maintained vehicle.
Characteristics | Values |
---|---|
Fuel Line Flare Purpose | To prevent fuel leaks, ensure a secure connection, and improve the overall performance of the fuel system. |
Fuel Line Material | Typically made of rubber, vinyl, or metal (e.g., steel, aluminum). |
Fuel Line Flare Tool | A special tool used to create a flare connection, often resembling a pair of pliers with a curved jaw. |
Flaring Process | Involves heating the fuel line to a specific temperature, then using the flare tool to form a flare connection. |
Fuel Line Diameter | The size of the flare connection depends on the fuel line diameter, typically measured in inches or millimeters. |
Flaring Standards | Various industry standards exist, such as SAE J1728, which provides guidelines for flare connections. |
Fuel Line Length | The length of the fuel line can influence the flare connection requirements, with longer lines potentially needing more complex flares. |
Fuel System Design | The overall design of the fuel system, including the engine and fuel tank, determines the necessary flare connections. |
Safety Considerations | Proper flaring ensures a tight seal, reducing the risk of fuel leaks and potential hazards. |
Maintenance and Repair | Flare connections may require maintenance or repair over time, especially in high-pressure or high-temperature environments. |
What You'll Learn
- Fuel Line Material: Consider the material of the fuel line to ensure compatibility with fuel type and temperature
- Flaring Technique: Learn proper flaring techniques to avoid damage and ensure a secure connection
- Fuel Line Routing: Plan the route to prevent damage from vibrations or other factors
- Fuel Line Length: Determine the appropriate length to avoid excessive pressure drop and potential leaks
- Fuel Line Inspection: Regularly inspect the fuel line for signs of wear, damage, or corrosion
Fuel Line Material: Consider the material of the fuel line to ensure compatibility with fuel type and temperature
When it comes to working with fuel lines, understanding the material is crucial for ensuring safety and performance. The choice of material directly impacts the compatibility of the fuel line with the type of fuel it will carry and the temperature variations it may encounter. Here's a detailed look at why this consideration is essential:
Compatibility with Fuel Type: Different fuels have unique chemical properties that can affect the material of the fuel line. For instance, gasoline-based fuels may require materials that are resistant to evaporation and degradation, while diesel fuel, being more corrosive, might necessitate a different approach. Ethanol-blended fuels, common in modern vehicles, can be particularly challenging due to their higher water content and potential for corrosion. The material of the fuel line must be able to withstand these specific fuel characteristics to ensure longevity and prevent leaks.
Temperature Considerations: Temperature plays a significant role in fuel line performance. Extreme temperatures, whether hot or cold, can impact the flexibility and integrity of the fuel line material. For instance, in cold climates, the fuel line material should be able to remain flexible and not become brittle, ensuring that the line can still function effectively even at sub-zero temperatures. Conversely, in hot environments, the material must be able to withstand elevated temperatures without degrading or becoming susceptible to fuel leaks. Materials like rubber, silicone, or specialized synthetic compounds are often chosen for their ability to maintain flexibility and integrity across a wide temperature range.
Common Materials Used: The most commonly used materials for fuel lines include rubber, silicone, and various synthetic compounds. Rubber is known for its flexibility and durability, making it suitable for a wide range of temperatures and fuel types. Silicone, on the other hand, offers excellent heat resistance and chemical inertness, making it ideal for high-temperature applications and fuels with corrosive properties. Synthetic compounds, often a blend of rubber and other materials, provide a balance of flexibility and strength, ensuring compatibility with various fuels and temperature conditions.
Customized Solutions: In some cases, customized fuel line materials may be required, especially for specialized applications or unique fuel types. This could involve using specialized coatings or additives to enhance the material's performance in specific conditions. For instance, a fuel line designed for high-performance racing applications might require a material that can withstand extreme temperatures and fuel pressures while maintaining flexibility.
In summary, the material of the fuel line is a critical factor in ensuring its compatibility with the fuel type and temperature conditions it will encounter. By carefully selecting the appropriate material, you can ensure the safety, reliability, and longevity of your fuel system.
Mastering Chainsaw Maintenance: The Ultimate Guide to Using a Fuel Line Tool
You may want to see also
Flaring Technique: Learn proper flaring techniques to avoid damage and ensure a secure connection
Flaring is a crucial process in plumbing and automotive work, especially when dealing with fuel lines. It involves bending and shaping metal or plastic tubing to create a secure and leak-free connection. While it might seem like a simple task, improper flaring can lead to significant issues, including fuel leaks, reduced performance, and even safety hazards. Therefore, understanding and mastering the proper flaring technique is essential for any professional or DIY enthusiast.
The primary goal of flaring is to create a smooth, uniform bend at the end of a tube, ensuring a tight seal when connected to another component. This process requires precision and the right tools to achieve a secure and reliable connection. One common mistake is using excessive force, which can cause the tube to kink or crimp, leading to potential damage. It's important to use the appropriate flaring tools for the specific material and size of the fuel line. For example, different types of flares, such as gas or oil flares, are designed for various diameters and materials.
To begin flaring, ensure you have the necessary tools, including the appropriate flaring tool, a mandrel (a cylindrical tool used to guide the flare), and a pair of pliers. Start by inserting the tube into the flaring tool, ensuring it is centered and aligned with the tool's jaws. Apply gentle force to create the initial bend, then gradually increase the pressure while rotating the tool. The goal is to create a 90-degree angle with a smooth, continuous curve. Avoid forcing the tool, as this can lead to an uneven flare. Instead, work slowly and steadily, ensuring the flare is consistent and symmetrical.
Once the initial flare is formed, it's crucial to check its quality. A well-flared connection should have a smooth, continuous curve without any sharp edges or kinks. Use the mandrel to guide the flare, ensuring it is centered and aligned. If the flare is uneven, carefully adjust the tool and try again. Take your time with this step, as rushing can result in a poor connection. After the flare is formed, inspect it for any defects and make any necessary adjustments.
After flaring, it's essential to test the connection to ensure its integrity. Connect the flared tube to the desired component and check for any leaks. If everything is secure, the system should be leak-free. However, if you notice any leaks, carefully inspect the flare and make any necessary adjustments. Proper flaring techniques will not only ensure a secure connection but also contribute to the overall safety and efficiency of your fuel system. Remember, practice makes perfect, and with time, you'll develop a keen eye for creating precise and reliable flares.
Kubota ZD21 Fuel Line Sizes: What You Need to Know
You may want to see also
Fuel Line Routing: Plan the route to prevent damage from vibrations or other factors
When it comes to fuel line routing, careful planning is essential to ensure the longevity and reliability of your vehicle's fuel system. The primary goal is to prevent damage from vibrations, which can occur due to engine movement, road conditions, and other factors. Here's a comprehensive guide to help you plan the optimal route for your fuel lines:
- Identify Potential Problem Areas: Begin by examining the vehicle's structure and layout. Look for areas where the fuel lines might be susceptible to vibrations, such as near the engine mounts, transmission, or suspension components. These areas often experience significant movement and can potentially cause the fuel lines to rattle or vibrate. Identifying these problem zones is crucial for determining the best routing strategy.
- Route the Fuel Lines Away from Vibrations: The key principle is to route the fuel lines away from these high-vibration areas. Aim to place the lines in a position where they are less likely to experience excessive movement. For example, if the engine mount is a concern, consider routing the fuel lines along the vehicle's frame or behind the firewall, where they will be protected from direct engine vibrations. This proactive approach can significantly reduce the risk of damage.
- Use Proper Support and Routing Techniques: Utilize appropriate support methods to secure the fuel lines. This may include using rubber hangers, metal brackets, or custom-made supports that absorb vibrations. Ensure that the lines are routed in a way that minimizes sharp bends or kinks, as these can lead to stress points and potential leaks. Keep the lines as straight and flat as possible, especially when running along the vehicle's frame or under the body.
- Consider the Environment: Take into account the surrounding environment and potential external factors. For instance, if the vehicle is used on rough terrain, the fuel lines should be protected from rocks, debris, or other obstacles that could cause physical damage. In such cases, routing the lines away from the ground or using protective covers might be necessary. Additionally, consider the temperature variations in the area, as extreme temperatures can affect the fuel lines' flexibility and integrity.
- Regular Inspection and Maintenance: Even with careful planning, it's essential to perform regular inspections to identify any signs of wear or damage. Check for any leaks, corrosion, or signs of vibration-induced stress. Promptly address any issues found during inspections to prevent further complications. Regular maintenance will ensure that your fuel system remains reliable and efficient over time.
By following these guidelines, you can effectively plan the fuel line routing to minimize the impact of vibrations and other factors, ultimately contributing to a more robust and durable fuel system in your vehicle. Remember, proper routing and maintenance are vital to avoiding costly repairs and ensuring the vehicle's overall performance.
Fuel Line for PCV: A Viable Option?
You may want to see also
Fuel Line Length: Determine the appropriate length to avoid excessive pressure drop and potential leaks
When it comes to fuel lines, ensuring the right length is crucial for optimal performance and safety. The length of the fuel line plays a significant role in maintaining the pressure required to deliver fuel efficiently to the engine. If the line is too short, it may result in a pressure drop, leading to reduced fuel flow and potential engine performance issues. On the other hand, an overly long fuel line can also cause problems, including excessive pressure drop and the risk of fuel leaks.
The ideal fuel line length is determined by several factors, including the engine's power output, the fuel pump's capacity, and the distance between the fuel tank and the engine. For high-performance engines, longer fuel lines might be necessary to ensure a consistent fuel supply, especially when the engine is located far from the fuel tank. However, longer lines can introduce challenges, such as increased pressure drop due to the greater distance and potential for more complex routing.
To calculate the appropriate length, consider the following: Start by measuring the distance from the fuel tank to the engine, ensuring you account for any bends or changes in direction. Then, add a buffer of approximately 10-15% to this distance to allow for potential routing complexities. This extra length will help accommodate any necessary bends or turns in the fuel line while minimizing pressure loss. It's important to strike a balance, as too much extra length can lead to unnecessary complications and potential leak points.
In addition to length, the diameter of the fuel line is another critical factor. Thicker fuel lines with larger diameters can reduce pressure drop and provide a more consistent fuel supply. However, larger lines may not be necessary for all applications and can increase system complexity. It's essential to choose the appropriate diameter based on the engine's requirements and the overall fuel system design.
Regular inspection and maintenance of fuel lines are also vital. Over time, fuel lines can develop cracks or become damaged, leading to leaks and potential engine issues. Inspecting the lines for any signs of wear, corrosion, or damage is essential, especially in high-pressure areas. Replacing fuel lines periodically or when necessary can help ensure the system's longevity and prevent costly repairs.
Stihl BR600 Fuel Line Hose: Unlocking the Secrets
You may want to see also
Fuel Line Inspection: Regularly inspect the fuel line for signs of wear, damage, or corrosion
Fuel lines are an essential component of your vehicle's fuel system, responsible for transporting fuel from the tank to the engine. Over time, these lines can deteriorate due to various factors, including age, environmental conditions, and the effects of fuel itself. Regular inspection of the fuel line is crucial to ensure the safe and efficient operation of your vehicle. Here's a comprehensive guide on how to inspect your fuel line for wear, damage, or corrosion:
Visual Inspection: Start by visually examining the fuel line for any visible signs of deterioration. Look for cracks, splits, or bulges along the length of the line. These defects can occur due to age, impact damage, or the presence of contaminants in the fuel. Pay close attention to areas where the line connects to the fuel tank and the engine, as these joints are more susceptible to wear. Check for any signs of corrosion, which may appear as a white or blueish-white powder-like substance along the line. Corrosion can weaken the fuel line and lead to leaks or fuel contamination.
Flexibility and Movement: Fuel lines should be flexible to accommodate the movement of the vehicle's engine and suspension. Inspect the line to ensure it can move freely without excessive bending or kinking. If the line appears rigid or has lost its flexibility, it may be due to internal damage or the accumulation of fuel contaminants. In such cases, the fuel line may need to be replaced.
Leakage and Moisture: Moisture in the fuel line is a clear indicator of a potential issue. Check for any signs of fuel leakage, especially around the connections and fittings. Even a small leak can lead to engine misfires, reduced performance, and potential damage to other engine components. If you notice any moisture or condensation inside the fuel line, it could be a sign of corrosion or a damaged fuel pump gasket.
Pressure Testing: Consider using a fuel pressure gauge to test the line's integrity. Connect the gauge to the fuel line and measure the pressure. If the pressure is significantly lower than the expected value, it may indicate a restriction or blockage in the line. This could be caused by corrosion, debris, or a damaged fuel pump. Regular pressure testing can help identify issues before they lead to complete fuel line failure.
Professional Inspection: For a thorough assessment, it is recommended to consult a professional mechanic. They can use specialized tools and techniques to inspect the fuel line, including pressure testing, diagnostic scans, and infrared thermography to detect heat signatures and potential issues. A professional inspection can provide a comprehensive report on the fuel line's condition and suggest appropriate repairs or replacements.
Remember, regular maintenance and inspection of the fuel line are vital to prevent unexpected breakdowns and ensure your vehicle's optimal performance. By following these guidelines, you can identify and address potential issues before they become major problems.
Fuel Line Removal: A Step-by-Step Guide for Your F-350
You may want to see also
Frequently asked questions
Flaring a fuel line is a process used in the automotive industry to ensure a safe and efficient fuel system. It involves the use of a specialized tool to create a small, controlled flame at the end of the fuel line, which helps to remove any excess fuel vapor and ensures a tight seal. This process is crucial for preventing fuel leaks and maintaining the overall performance and safety of the vehicle.
Fuel lines should be flared whenever there is a need for modifications or repairs to the fuel system. This includes situations like replacing a damaged fuel line, installing a new fuel pump, or modifying the fuel injectors. Flaring ensures a proper connection and prevents potential fuel leaks, which can cause engine misfires, reduced performance, and even safety hazards.
While it is technically possible for experienced DIY enthusiasts to flare a fuel line, it is generally recommended to seek professional assistance from a qualified mechanic or fuel system specialist. Flaring requires precision and knowledge of fuel system components to ensure a safe and effective connection. Professionals have the necessary tools and expertise to perform the task accurately, minimizing the risk of errors that could lead to fuel leaks or other issues.