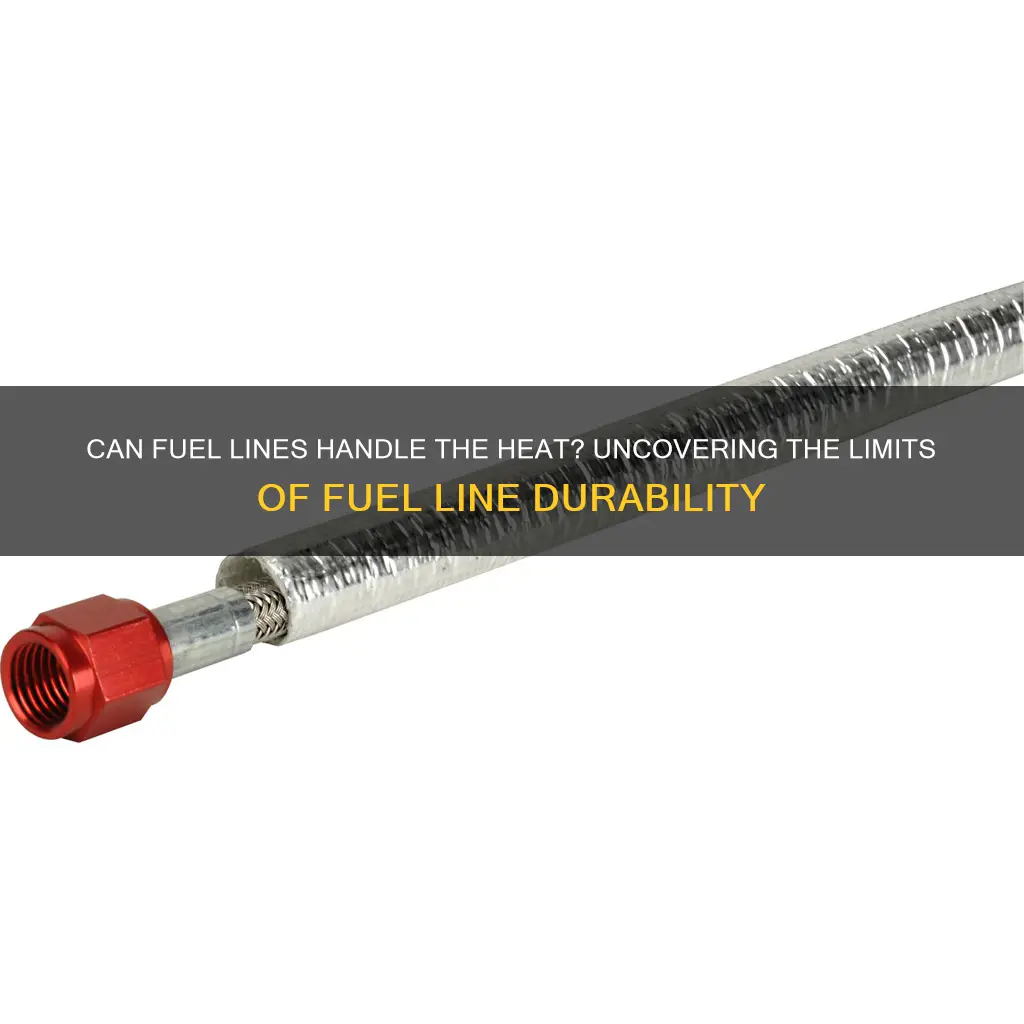
Fuel lines play a critical role in the performance and safety of any vehicle, but can they withstand the intense heat generated during operation? This question is crucial for understanding the reliability and longevity of fuel systems, especially in high-performance engines or vehicles operating in extreme conditions. The ability of fuel lines to resist heat is essential to prevent damage, ensure efficient fuel delivery, and maintain the overall health of the vehicle's engine. This introduction sets the stage for an exploration of the thermal properties of fuel lines and their impact on vehicle performance.
Characteristics | Values |
---|---|
Heat Resistance | Fuel lines are designed to withstand high temperatures, typically up to 250°F (121°C) without degradation. |
Flexibility | They are flexible and can bend without kinking, ensuring they can navigate through engine compartments and under various vehicle components. |
Material | Common materials include rubber, silicone, and nylon, each chosen for their ability to resist heat and chemicals in fuel. |
Durability | High-quality fuel lines are often reinforced with braided steel or stainless steel to prevent punctures and ensure long-term reliability. |
Compatibility | They are engineered to be compatible with various fuel types, including gasoline, diesel, and aviation fuel. |
Length | Available in various lengths to accommodate different vehicle layouts and engine positions. |
Installation | Easy to install, often requiring no special tools, and can be connected using standard fuel line connectors. |
Maintenance | Low maintenance, with regular inspections recommended to check for signs of wear or damage. |
Standards | Adhere to industry standards and regulations to ensure safety and performance. |
What You'll Learn
- Fuel Line Material: Different materials have varying heat resistance, affecting fuel line durability
- Fuel Line Diameter: Thicker lines can withstand higher temperatures without compromising performance
- Fuel Line Length: Longer lines may require additional insulation to manage heat effectively
- Fuel Line Routing: Proper routing prevents heat damage and ensures optimal fuel flow
- Fuel Line Temperature Limits: Understanding temperature limits is crucial for fuel line selection and maintenance
Fuel Line Material: Different materials have varying heat resistance, affecting fuel line durability
When it comes to fuel lines, the material used plays a crucial role in determining their durability and performance, especially in high-temperature environments. Different materials offer varying levels of heat resistance, which directly impacts the fuel line's ability to withstand the intense conditions it may encounter. This is particularly important in applications where fuel lines are exposed to high temperatures, such as in racing vehicles, industrial machinery, or even in the automotive industry.
One of the most common materials used for fuel lines is rubber. Rubber is known for its flexibility and resilience, making it a popular choice for fuel lines. However, it is important to note that not all rubbers are created equal when it comes to heat resistance. Natural rubber, for instance, has a relatively low heat tolerance and may degrade or become brittle over time when exposed to high temperatures. On the other hand, synthetic rubbers, such as neoprene or silicone, offer improved heat resistance, making them more suitable for demanding applications. These synthetic rubbers can withstand higher temperatures without compromising their flexibility, ensuring the fuel lines remain pliable and functional.
Another material often utilized in fuel line construction is vinyl. Vinyl fuel lines are known for their cost-effectiveness and moderate heat resistance. They can handle moderate to high temperatures, making them a popular choice for everyday applications. However, it is essential to consider that vinyl may not be as durable as other materials in extremely high-temperature environments. In such cases, combining vinyl with a heat-resistant protective layer or using it in conjunction with other materials can enhance its performance.
For applications requiring the highest level of heat resistance, materials like stainless steel or braided stainless steel are often employed. These materials are known for their exceptional durability and ability to withstand extreme temperatures. Stainless steel fuel lines are commonly used in racing and high-performance vehicles, where fuel temperatures can soar. The use of stainless steel ensures that the fuel lines remain intact and functional, even under intense heat, providing peace of mind to enthusiasts and professionals alike.
In summary, the choice of material for fuel lines is critical to ensure optimal performance and longevity. Different materials offer varying heat resistance, and selecting the appropriate one depends on the specific application and environmental conditions. Whether it's the flexibility of rubber, the cost-effectiveness of vinyl, or the extreme heat resistance of stainless steel, understanding the heat tolerance of various materials is essential for making informed decisions when it comes to fuel line installation and maintenance.
The Ultimate Guide to Choosing the Best 1-2 Fuel Line
You may want to see also
Fuel Line Diameter: Thicker lines can withstand higher temperatures without compromising performance
The diameter of a fuel line is a critical factor in determining its ability to handle heat without sacrificing performance. Thicker fuel lines, typically measured in inches or millimeters, offer several advantages in this regard. Firstly, a larger diameter provides a greater surface area, which is crucial for heat dissipation. When a fuel line is exposed to high temperatures, the increased surface area allows for more efficient heat transfer, preventing the line from overheating and potentially failing. This is especially important in high-performance engines or applications where fuel temperatures can soar.
In terms of material composition, thicker fuel lines often utilize high-quality materials that are specifically designed to resist heat. These materials, such as reinforced rubber or specialized polymers, have excellent thermal stability, ensuring that the fuel line can withstand the extreme conditions without becoming brittle or degrading over time. The construction of these thicker lines often involves multiple layers or braiding techniques, further enhancing their heat resistance and overall durability.
One of the key benefits of thicker fuel lines is their ability to maintain performance even under intense heat. Thicker lines can handle higher pressure differentials without compromising flow rates, ensuring a consistent and reliable fuel supply to the engine. This is particularly important in racing or high-performance applications where every second counts, and a well-maintained fuel system is essential for optimal power delivery.
Additionally, thicker fuel lines often feature improved flexibility, allowing them to navigate through engine compartments and underhood obstacles with ease. This flexibility, combined with their heat resistance, ensures that the fuel lines remain intact and functional, even in tight spaces or when subjected to vibrations during operation.
In summary, when considering fuel lines for high-temperature environments, opting for thicker lines is a wise choice. The increased diameter provides better heat dissipation, while the use of specialized materials and construction techniques ensures longevity and performance. By investing in thicker fuel lines, vehicle owners and enthusiasts can have peace of mind, knowing that their fuel system is capable of handling the demands of extreme conditions without sacrificing efficiency.
Aztek Fuel Disconnect: Step-by-Step Guide to Removing the Center Line
You may want to see also
Fuel Line Length: Longer lines may require additional insulation to manage heat effectively
When it comes to fuel lines, their length can significantly impact their performance, especially in terms of heat management. Longer fuel lines present a unique challenge as they are more susceptible to heat-related issues. The primary concern is that prolonged exposure to high temperatures can lead to several problems, including reduced fuel efficiency, potential fuel degradation, and even safety hazards. This is particularly critical in high-performance vehicles or applications where fuel temperatures need to be carefully controlled.
As the length of the fuel line increases, the distance between the fuel source and the engine grows, which means the fuel must travel a longer path. This extended route increases the time the fuel spends in the line, making it more vulnerable to heat absorption from the surrounding environment. Over time, this can result in the fuel reaching the engine at a higher temperature, which may not be ideal for optimal performance.
To address this issue, additional insulation becomes a crucial consideration. Insulation materials, such as foam or rubber, can be applied to the fuel lines to provide a protective barrier against heat transfer. This insulation helps to maintain the fuel's temperature, ensuring it remains at a consistent and optimal level for combustion. Proper insulation can also prevent the fuel lines from overheating, which could lead to the deterioration of the line's material and potential leaks.
The insulation process involves carefully wrapping the fuel line with the chosen material, ensuring complete coverage. This methodical approach guarantees that the entire length of the line is protected, providing uniform heat resistance. It is essential to use high-quality insulation that can withstand the specific temperature ranges encountered in the application to ensure long-term reliability.
In summary, longer fuel lines require special attention to heat management. By implementing appropriate insulation techniques, the potential risks associated with heat exposure can be mitigated, ensuring the fuel lines function efficiently and safely. This is a critical aspect of vehicle maintenance, especially for those operating in demanding conditions or requiring precise fuel temperature control.
Camaro Fuel Line: The Perfect Diameter for Power and Performance
You may want to see also
Fuel Line Routing: Proper routing prevents heat damage and ensures optimal fuel flow
Fuel lines are a critical component of any vehicle's fuel system, and their proper routing is essential for maintaining optimal performance and preventing potential issues. When it comes to heat resistance, fuel lines play a vital role in withstanding the high temperatures generated by the engine and various vehicle components. Here's an in-depth look at the importance of fuel line routing and how it can prevent heat damage:
Understanding Heat Resistance: Fuel lines are typically made of materials like rubber, plastic, or metal, which must be able to endure the intense heat generated during engine operation. Prolonged exposure to high temperatures can cause these materials to degrade, leading to cracks, leaks, or even fuel line failure. This is especially critical as fuel lines are responsible for transporting fuel from the tank to the engine, and any damage can result in reduced performance or even engine stall.
Proper Routing Techniques: The key to preventing heat damage lies in the careful routing of fuel lines. Here are some best practices:
- Direct Routing: Fuel lines should be routed directly from the fuel tank to the engine, minimizing the length of the line. Longer lines are more susceptible to heat damage due to increased surface area exposed to engine heat.
- Insulation: Insulating the fuel lines with heat-resistant materials is crucial, especially in areas close to the engine. This insulation acts as a protective barrier, preventing direct contact with hot engine components.
- Avoid Tight Spaces: Fuel lines should be routed away from tight spaces and sharp bends, as these can restrict flow and cause stress on the lines, potentially leading to damage.
- Secure Mounting: Properly secure the fuel lines to ensure they don't rub against moving parts or get caught in vibrations. This prevents wear and tear, especially in high-temperature areas.
Benefits of Optimal Routing: When fuel lines are correctly routed, several advantages are gained:
- Improved Fuel Flow: Proper routing ensures a smooth and efficient flow of fuel, allowing the engine to operate optimally. This results in better performance, faster acceleration, and improved overall efficiency.
- Heat Protection: By keeping fuel lines away from direct heat sources, you minimize the risk of heat-related damage, ensuring the longevity of the fuel system.
- Reduced Stress: Well-routed fuel lines experience less stress, reducing the chances of cracks or leaks, which can be costly to repair.
In summary, fuel line routing is a critical aspect of vehicle maintenance that directly impacts performance and reliability. By implementing proper routing techniques, you can ensure that fuel lines withstand the heat generated by the engine, providing optimal fuel flow and contributing to the overall efficiency and longevity of the vehicle's fuel system. Regular inspection and maintenance of fuel lines are also recommended to identify and address any potential issues promptly.
Craftsman 316292621 Fuel Line: Size Guide for Optimal Performance
You may want to see also
Fuel Line Temperature Limits: Understanding temperature limits is crucial for fuel line selection and maintenance
Understanding the temperature limits of fuel lines is essential for ensuring the safe and efficient operation of any vehicle or equipment that relies on a fuel system. Fuel lines are designed to withstand specific temperature ranges, and exceeding these limits can lead to a variety of issues, including reduced performance, system failures, and even safety hazards. Here's a detailed guide to help you navigate the complexities of fuel line temperature limits:
Temperature Limits for Fuel Lines:
Fuel lines are typically rated for specific temperature ranges, which can vary depending on the material and design. Common temperature limits for fuel lines include a maximum operating temperature and a minimum temperature threshold. These limits are often specified by the manufacturer and are critical to consider during installation and maintenance. For example, a fuel line designed for gasoline may have a maximum temperature limit of 150°F (65.5°C) and a minimum limit of 32°F (0°C). Exceeding these temperatures can cause the fuel line to degrade, become brittle, or even fail.
Impact of High Temperatures:
High temperatures can have detrimental effects on fuel lines. When exposed to excessive heat, fuel lines may experience thermal expansion, leading to increased pressure and potential damage to the fuel system. This can result in fuel leaks, reduced fuel flow, and even engine misfires. In extreme cases, high temperatures can cause the fuel line to melt or become dislodged, posing a significant safety risk. It's important to note that high temperatures are not just a concern during engine operation; prolonged exposure to high ambient temperatures can also affect fuel lines, especially in outdoor environments.
Consequences of Low Temperatures:
Low temperatures present their own set of challenges. When fuel lines are exposed to freezing temperatures, the fuel can become sludgy or form ice crystals, leading to blockages and reduced fuel flow. This can result in engine starting difficulties, poor performance, and potential damage to the fuel system. In extreme cold, fuel lines may become brittle and more susceptible to cracking or splitting. Proper insulation and the use of compatible fuels are essential to mitigate these issues.
Material Considerations:
The material of the fuel line plays a significant role in determining its temperature limits. Common materials include rubber, vinyl, and various types of hoses. Each material has its own temperature tolerance, and selecting the right material for the specific application is crucial. For instance, rubber fuel lines may have different temperature limits compared to vinyl, and these differences should be considered during installation and maintenance.
Maintenance and Inspection:
Regular maintenance and inspections are vital to ensuring that fuel lines operate within their temperature limits. This includes checking for signs of damage, wear, or degradation. Inspecting fuel lines for cracks, brittleness, or any visible signs of heat-related stress is essential. Additionally, monitoring the fuel system's performance, such as fuel pressure and flow, can help identify potential issues related to temperature extremes. Proper maintenance practices, such as using fuel stabilizers in cold weather, can also contribute to the longevity of fuel lines.
Honda Rancher 420 Fuel Line Removal: A Step-by-Step Guide
You may want to see also
Frequently asked questions
Fuel lines are designed to withstand elevated temperatures, typically up to 250°F (121°C) without any issues. They are constructed using materials like stainless steel or high-temperature-resistant rubber compounds, ensuring flexibility and durability even in extreme heat conditions.
Prolonged exposure to excessive heat can potentially cause fuel lines to degrade over time. However, this is usually a concern for fuel lines operating at temperatures above the recommended limits or in environments with frequent temperature fluctuations. Proper installation, using suitable materials, and regular inspections can help prevent such damage.
Yes, there are a few indicators that your fuel lines might be failing due to heat. These include fuel leaks, engine misfires, reduced engine performance, and, in extreme cases, visible damage like melting or warping of the fuel lines. Regular maintenance and monitoring of the vehicle's performance can help catch these issues early.
To maintain the integrity of fuel lines in hot climates, consider using fuel line insulators or heat shields to protect them from direct exposure to high temperatures. Regularly inspecting the fuel system for any signs of damage or wear is also essential. Additionally, ensuring that the fuel system is properly vented and that the fuel tank is not overfilled can help prevent issues related to heat expansion.