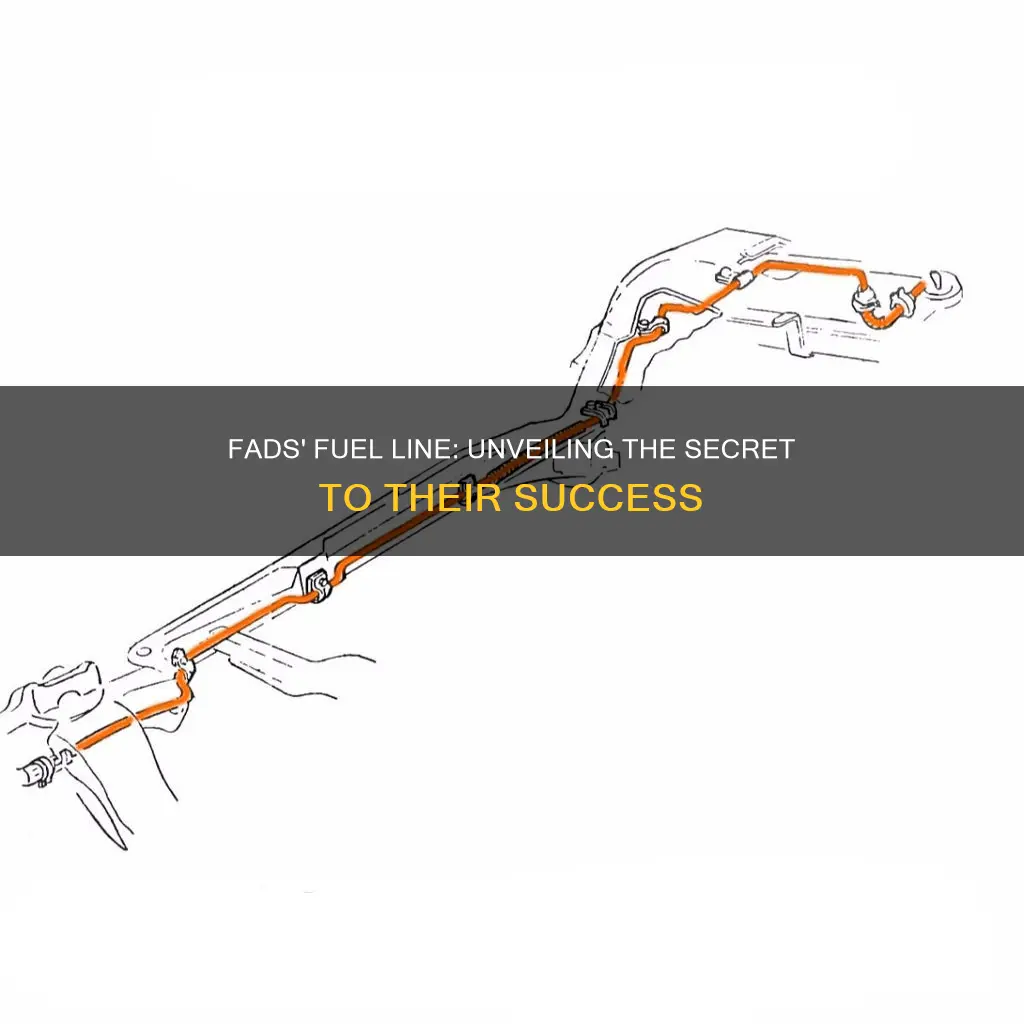
Fads, or fuel-air-direct systems, are innovative combustion technologies that have gained attention in the automotive industry. These systems aim to optimize engine performance and efficiency by directly injecting a precise mixture of fuel and air into the combustion chamber. Understanding the specific fuel lines used in these systems is crucial for their proper installation and maintenance. This paragraph will explore the fuel lines employed in fads, highlighting their unique characteristics and benefits.
What You'll Learn
- Fuel Line Material: FADS uses specific materials like steel or rubber for durability and performance
- Fuel Line Diameter: Different diameters are used to match engine requirements and optimize fuel flow
- Fuel Line Routing: Proper routing ensures fuel reaches the engine without contamination or restriction
- Fuel Line Connections: Fittings and clamps secure the line, preventing leaks and ensuring a tight fit
- Fuel Line Maintenance: Regular checks and cleaning maintain fuel quality and engine performance
Fuel Line Material: FADS uses specific materials like steel or rubber for durability and performance
When it comes to fuel lines, FADS (Fuel and Air Delivery Systems) prioritizes durability and performance, which is why they utilize specific materials for their fuel lines. One of the primary materials used is steel, known for its exceptional strength and resistance to corrosion. Steel fuel lines are ideal for high-performance applications where fuel needs to be delivered under pressure, ensuring a reliable and efficient flow. These lines are often used in racing cars and high-performance vehicles, where every second counts and fuel delivery needs to be precise.
In addition to steel, FADS also employs rubber as a fuel line material. Rubber is highly flexible and can withstand a wide range of temperatures, making it suitable for various automotive environments. This flexibility is crucial for fuel lines as it allows them to navigate through tight spaces and engine compartments without compromising performance. Rubber fuel lines are commonly used in everyday vehicles, providing a cost-effective solution without sacrificing reliability.
The choice of material depends on the specific requirements of the vehicle and the intended use. For high-performance applications, steel fuel lines offer superior strength and longevity, ensuring that fuel is delivered efficiently even under extreme conditions. On the other hand, rubber fuel lines provide a more versatile and cost-effective option for everyday vehicles, where flexibility and temperature resistance are essential.
FADS understands the importance of material selection in fuel line design, as it directly impacts the overall performance and longevity of the system. By using high-quality materials like steel and rubber, they ensure that their fuel lines meet the demands of various automotive applications, from high-performance racing to everyday commuting. This attention to detail in material choice sets FADS apart as a reliable and trusted brand in the automotive industry.
In summary, FADS utilizes a combination of steel and rubber for their fuel lines, each material serving a unique purpose. Steel provides strength and corrosion resistance for high-performance applications, while rubber offers flexibility and temperature tolerance for everyday vehicles. This strategic material selection ensures that FADS fuel lines deliver the required performance and durability, catering to a wide range of automotive needs.
Choosing the Right Color Fuel Line for Your Mower
You may want to see also
Fuel Line Diameter: Different diameters are used to match engine requirements and optimize fuel flow
The diameter of a fuel line is a critical factor in ensuring efficient and reliable fuel delivery to an engine, especially in high-performance applications like those found in FADs (Fuel-Air-Delivery) systems. The fuel line's diameter directly impacts the flow rate and pressure of the fuel, which in turn affects the engine's performance and overall efficiency. When designing or selecting fuel lines for an engine, engineers consider various factors to optimize the fuel flow and meet the specific requirements of the engine.
Fuel lines come in different diameters, typically measured in inches or millimeters, and the choice of diameter depends on several key considerations. Firstly, the engine's power output and performance demands play a significant role. High-performance engines often require larger fuel lines to accommodate the increased fuel flow needed to meet their power goals. For instance, a racing engine might use larger-diameter fuel lines to ensure a rapid and efficient supply of fuel to the engine's cylinders. Conversely, smaller fuel lines might be sufficient for lower-power applications, where the engine's fuel requirements are less demanding.
Engine displacement is another crucial factor. Larger engines with more cylinders and a higher displacement volume will generally require larger fuel lines to handle the increased fuel volume. This is because the engine's capacity to process fuel is directly related to its displacement, and larger engines need to manage a greater volume of fuel efficiently. As a result, fuel lines with larger diameters are often chosen to match the engine's needs.
Additionally, the fuel pressure within the system is a critical consideration. Different engine designs and operating conditions may require specific fuel pressures to ensure optimal performance. Fuel lines with varying diameters can be used to control and regulate the fuel pressure. Thicker fuel lines with smaller diameters can help maintain higher fuel pressures, which is essential for engines operating at elevated RPMs or in high-load conditions. On the other hand, thinner fuel lines might be used when lower fuel pressures are required, such as in certain marine or recreational vehicle applications.
In summary, the diameter of the fuel line is a critical design choice that directly influences the engine's performance and efficiency. Engineers carefully select the fuel line diameter based on the engine's power output, displacement, and specific operating conditions to ensure optimal fuel flow and pressure. This attention to detail in fuel line design is essential for maximizing the potential of modern engines, especially in high-performance applications where every component contributes to the overall performance and reliability of the system.
Fuel Line Injection: Unlocking Engine Power with Liquid Magic
You may want to see also
Fuel Line Routing: Proper routing ensures fuel reaches the engine without contamination or restriction
Fuel line routing is a critical aspect of vehicle maintenance that often goes overlooked, but it plays a vital role in ensuring optimal engine performance and longevity. Proper routing of the fuel lines is essential to prevent contamination, maintain fuel flow efficiency, and avoid potential engine issues. Here's an in-depth look at why and how to route fuel lines correctly:
Preventing Contamination: One of the primary concerns with fuel line routing is contamination. Fuel lines should be routed away from heat sources, such as exhaust manifolds, headers, and engine components that generate high temperatures. Heat can cause fuel to degrade and potentially lead to the formation of harmful contaminants. Additionally, fuel lines should be kept away from sharp edges, vibrations, and potential impact areas to prevent damage and ensure the fuel remains clean and free-flowing.
Maintaining Fuel Flow: Efficient fuel flow is crucial for engine performance. Fuel lines should be routed in a way that minimizes bends and kinks, as these can restrict the flow of fuel. The lines should be straight and as short as possible to reduce the risk of air bubbles and ensure that the fuel reaches the engine without any unnecessary resistance. Proper routing also helps maintain consistent fuel pressure, which is essential for accurate engine operation.
Avoiding Engine Issues: Incorrect fuel line routing can lead to various engine problems. For instance, if the fuel line is too close to a hot surface, it may cause the fuel to vaporize, leading to poor engine performance and potential misfires. Additionally, sharp bends or kinks in the fuel line can create areas where fuel can accumulate, leading to contamination and potential engine damage over time. Proper routing ensures that the fuel line is secure and free from any obstructions that could cause these issues.
Best Practices for Routing: When routing fuel lines, it is recommended to follow the manufacturer's guidelines and use the appropriate materials. Fuel lines should be made of materials that are resistant to fuel degradation and can withstand engine temperatures. The routing should be neat and organized, with clear labels to identify different lines. It is also essential to secure the fuel lines using appropriate clamps or ties to prevent movement and potential damage.
Regular Inspection: Regularly inspecting the fuel line routing is crucial for maintaining the health of your engine. Look for any signs of damage, contamination, or wear. Check for leaks, especially at connections and bends, as these can lead to fuel contamination and engine issues. By keeping a close eye on the fuel lines and addressing any problems promptly, you can ensure that your engine receives clean, efficient fuel delivery.
E85 Fuel Line Maintenance: What to Flush and Why
You may want to see also
Fuel Line Connections: Fittings and clamps secure the line, preventing leaks and ensuring a tight fit
Fuel lines are a critical component of any vehicle's fuel system, and proper connections are essential to ensure optimal performance and prevent leaks. When it comes to securing fuel lines, fittings and clamps play a vital role in maintaining a tight and secure fit. These components are designed to withstand the pressure and temperature fluctuations that fuel lines experience during operation, providing a reliable seal to prevent any unwanted fuel loss.
Fittings are typically made of durable materials such as brass, steel, or aluminum, ensuring they can withstand the corrosive nature of fuel. They come in various shapes and sizes, each designed for specific applications. For example, quick-connect fittings offer a convenient and efficient way to join fuel lines, allowing for easy installation and removal. These fittings often feature a locking mechanism that ensures a secure connection, preventing accidental disconnections. Threaded fittings, on the other hand, provide a more permanent solution, requiring precise threading to ensure a tight seal.
Clamps are another essential component of fuel line connections. They are used to secure the fuel line to various components, such as the fuel tank, engine, or fuel pump. Clamps are designed to apply pressure evenly around the fuel line, creating a tight seal and preventing any potential leaks. Different types of clamps are available, including metal and rubber varieties, each with its own advantages. Metal clamps, often made of stainless steel, offer excellent durability and resistance to corrosion, making them ideal for high-pressure applications. Rubber or silicone clamps, on the other hand, provide flexibility and insulation, which can be beneficial in certain engine compartments.
When installing fuel lines, it is crucial to follow the manufacturer's guidelines and use the appropriate fittings and clamps for the specific application. Proper alignment and secure fastening are essential to ensure a leak-free connection. Over-tightening should be avoided as it can damage the fuel line or fittings. Additionally, regular inspection of fuel line connections is recommended to identify any signs of wear, damage, or potential leaks.
In summary, fuel line connections rely on fittings and clamps to provide a secure and leak-free system. These components are designed to withstand the demanding conditions of a vehicle's fuel system, ensuring optimal performance and safety. By understanding the different types of fittings and clamps available and following proper installation techniques, mechanics can ensure that fuel lines are connected efficiently and securely, contributing to a reliable and efficient fuel supply throughout the vehicle's operation.
Braided Fuel Line Security: Tools and Techniques for a Tight Fit
You may want to see also
Fuel Line Maintenance: Regular checks and cleaning maintain fuel quality and engine performance
Maintaining the fuel lines in your vehicle is a critical aspect of regular car care that often goes overlooked. Fuel lines play a vital role in ensuring your engine receives the correct amount of fuel for optimal performance. Over time, these lines can become clogged, damaged, or degraded, leading to poor fuel quality and reduced engine efficiency. Regular maintenance and checks are essential to prevent such issues and ensure your vehicle runs smoothly.
The primary function of fuel lines is to transport gasoline or diesel from the fuel tank to the engine. These lines are designed to withstand high pressure and temperature changes, but they can still be susceptible to wear and tear. Clogging is a common problem, often caused by the accumulation of dirt, debris, and varnish (a sticky substance formed by fuel evaporation). When fuel lines become clogged, it restricts the flow of fuel, leading to reduced power, poor acceleration, and even engine misfires.
To maintain fuel line health, it is recommended to perform regular checks and cleaning. Start by inspecting the lines for any signs of damage, such as cracks, leaks, or corrosion. Look for any discolored or contaminated fuel, which could indicate a problem with the fuel lines or the fuel pump. It is also a good practice to check for any signs of fuel line vibration or movement, as this can lead to leaks over time.
Cleaning the fuel lines is a crucial step in maintenance. You can use a fuel line cleaner, which is typically a chemical solvent, to dissolve and remove any built-up varnish or deposits. This process can be done by running the cleaner through the lines using a fuel pressure regulator or by using a fuel line cleaner machine. It is important to follow the manufacturer's instructions for the correct usage and application of these cleaning products. Regular cleaning helps to ensure that the fuel lines remain clear and free-flowing, promoting better fuel quality and engine performance.
In addition to cleaning, regular fuel system inspections are essential. This includes checking the fuel filter, as a clogged filter can restrict fuel flow and cause similar issues as clogged lines. Changing the fuel filter at the recommended intervals can help maintain the overall health of the fuel system. Furthermore, keeping the fuel tank clean and free of contaminants is vital. Regularly removing any debris or water from the tank can prevent it from entering the fuel lines and causing issues.
By implementing a regular fuel line maintenance routine, you can ensure that your vehicle's fuel system remains in optimal condition. This proactive approach to car care will help improve engine performance, fuel efficiency, and overall longevity. Remember, proper maintenance can save you from potential costly repairs and keep your vehicle running smoothly for years to come.
Unveiling the Mystery: What's in the Fuel Line to Reduce NOx Emissions?
You may want to see also
Frequently asked questions
The fuel line is a crucial component that transports fuel from the tank to the engine, ensuring a steady supply of gasoline or diesel for combustion.
FADs are advanced fuel injection systems that optimize fuel delivery. The fuel line in this system is designed to provide precise fuel pressure and volume to the engine, enhancing performance and efficiency.
Standard fuel lines are typically made of rubber or plastic and are designed for basic fuel transport. In contrast, FADs use specialized fuel lines with higher pressure ratings and often incorporate flexible materials to accommodate the system's dynamic nature.
Yes, FAD systems demand fuel lines with excellent flexibility, durability, and the ability to withstand high pressure. These lines are often made of specialized materials like braided steel or reinforced rubber to ensure optimal performance.
Regular maintenance is essential. It is recommended to inspect the fuel line annually or every 50,000 miles. Replacing it every 10-15 years or when signs of damage or degradation are noticed is advisable to maintain the system's efficiency.