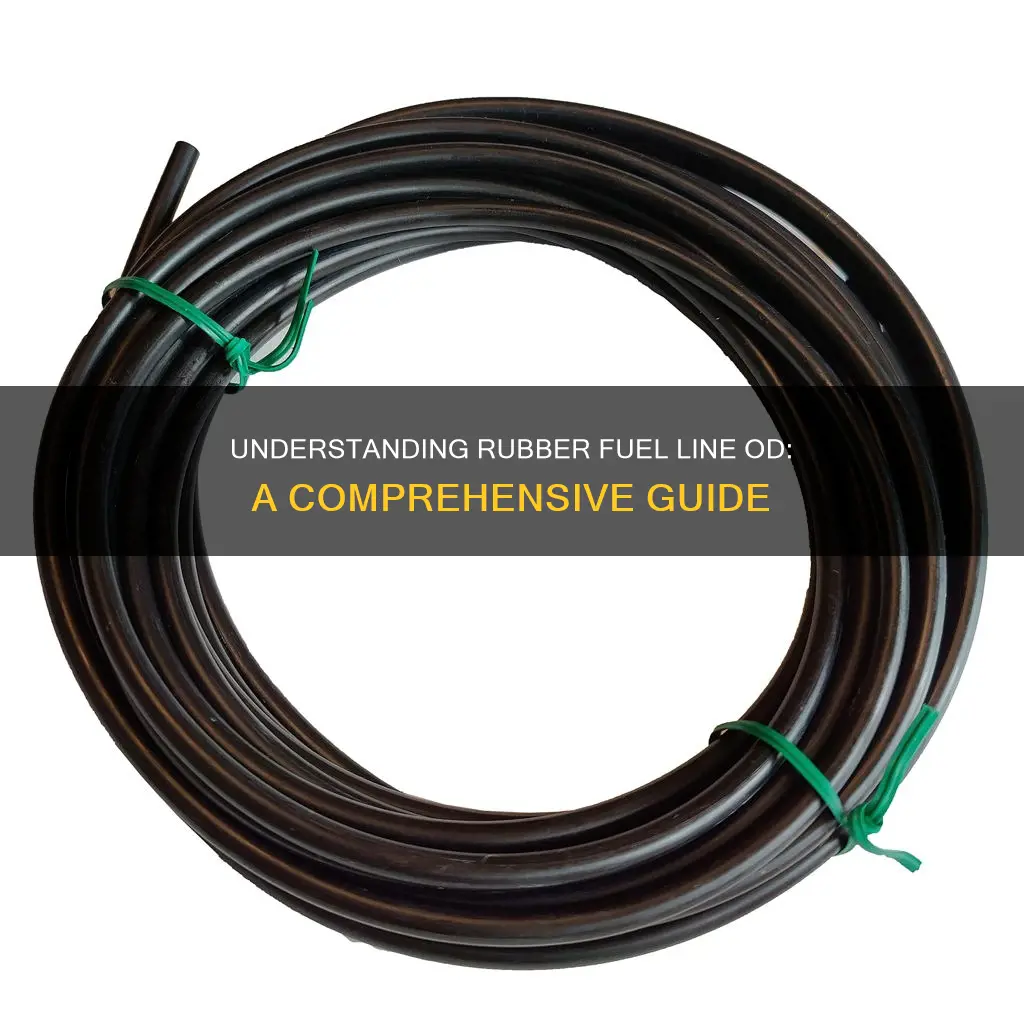
The OD, or outside diameter, of a rubber fuel line is a crucial measurement in the automotive and industrial sectors. It refers to the diameter of the rubber tube or hose, which is an essential component in fuel delivery systems. Understanding the OD is vital for ensuring proper fit and compatibility with various fuel lines, pumps, and fittings. This measurement is typically expressed in inches or millimeters and plays a significant role in determining the line's strength, flexibility, and ability to withstand fuel pressure and temperature changes.
What You'll Learn
- Construction: Rubber fuel lines are made from synthetic rubber compounds
- Flexibility: They offer flexibility to withstand engine vibrations and temperature changes
- Durability: Rubber fuel lines are resistant to fuel degradation and abrasion
- Compatibility: Rubber fuel lines are compatible with most fuel types
- Installation: Rubber fuel lines are easy to install and connect to fuel systems
Construction: Rubber fuel lines are made from synthetic rubber compounds
The construction of rubber fuel lines involves a meticulous process that utilizes synthetic rubber compounds to ensure durability and reliability in fuel transportation. These lines are an essential component in various industries, particularly in the automotive and aviation sectors, where they play a critical role in delivering fuel from the tank to the engine. The primary material used in their construction is synthetic rubber, which is carefully selected for its ability to withstand the demanding conditions of fuel transport.
Synthetic rubber compounds are engineered to possess specific properties that make them ideal for this application. These compounds are designed to be flexible, yet robust, allowing the fuel lines to navigate through tight spaces and absorb vibrations without compromising structural integrity. The process begins with the selection of a suitable synthetic rubber, such as neoprene or butyl rubber, known for their excellent resistance to fuel degradation and temperature fluctuations. These rubbers are then compounded with various additives to enhance their performance and longevity.
The manufacturing process involves several steps. Initially, the synthetic rubber is heated and mixed with the chosen additives, creating a homogeneous mixture. This mixture is then extruded through a die to form the desired shape of the fuel line. The extrusion process ensures that the line has a consistent cross-sectional profile, which is crucial for maintaining a steady fuel flow. After extrusion, the lines are cooled and cured to set their shape and properties.
Curing is a critical step in the construction process, as it involves exposing the rubber to controlled temperatures and atmospheres to initiate a chemical reaction that cross-links the polymer chains. This reaction makes the rubber more resilient and resistant to fuel permeation. The cured fuel lines are then inspected for any defects, ensuring they meet the required standards for fuel containment and transportation.
In summary, the construction of rubber fuel lines is a precise and intricate process that relies on synthetic rubber compounds to create a robust and reliable product. The careful selection of materials, combined with the manufacturing and curing techniques, ensures that these fuel lines can withstand the challenges of fuel transport, providing a safe and efficient system for various applications. This construction method is a testament to the engineering prowess required to meet the demanding needs of modern transportation systems.
Unveiling the Power of 8AN Fuel Lines: A Comprehensive Guide
You may want to see also
Flexibility: They offer flexibility to withstand engine vibrations and temperature changes
The flexibility of rubber fuel lines is a critical feature that ensures their longevity and reliability in automotive applications. Rubber is a natural material that inherently possesses a certain level of flexibility, which is essential for withstanding the various stresses and strains encountered within an engine's operating environment. This flexibility is particularly important in the context of engine vibrations and temperature changes, as it allows the fuel lines to adapt and maintain their structural integrity.
Engine vibrations can be quite intense, with rapid and often unpredictable movements. Rubber fuel lines are designed to absorb and dampen these vibrations, preventing excessive strain on the material. The flexibility of rubber enables it to bend and twist without permanent deformation, ensuring that the fuel lines remain intact and functional even in the most challenging conditions. This is crucial for maintaining a consistent fuel supply to the engine, as any damage or breakage in the fuel line could lead to engine misfires, reduced performance, or even complete engine failure.
Temperature changes are another significant factor that rubber fuel lines must accommodate. Engines operate within a wide range of temperatures, from extreme heat during high-performance driving to sub-zero conditions in colder climates. Rubber's flexibility allows it to expand and contract with temperature variations, reducing the risk of cracking or splitting. This is especially important in preventing fuel leaks, as any damage to the fuel line could result in fuel seeping into the engine compartment, potentially causing fires or other hazardous situations.
The flexibility of rubber fuel lines is further enhanced by the material's ability to resist aging and degradation over time. Rubber compounds are carefully formulated to maintain their elasticity and resilience even after prolonged exposure to harsh engine environments. This ensures that the fuel lines continue to perform optimally throughout the vehicle's lifetime, providing a reliable and consistent fuel supply.
In summary, the flexibility of rubber fuel lines is a vital characteristic that enables them to withstand the demanding conditions of an engine's operating environment. By offering the ability to absorb vibrations and adapt to temperature changes, rubber fuel lines ensure the safe and efficient delivery of fuel, contributing to the overall performance and reliability of the vehicle.
Unveiling the Milwaukee Fuel Line: Powering Your Projects
You may want to see also
Durability: Rubber fuel lines are resistant to fuel degradation and abrasion
Rubber fuel lines are an essential component in any vehicle's fuel system, and their durability is a critical aspect of their design. These lines are specifically engineered to withstand the harsh conditions present in a vehicle's engine bay, where they are exposed to various contaminants and environmental factors. One of the key advantages of rubber fuel lines is their inherent resistance to fuel degradation. Over time, fuel can break down due to exposure to air, heat, and light, leading to the formation of varnish and other harmful substances. Rubber, however, is a material that can effectively prevent this degradation process. It acts as a barrier, keeping the fuel contained and isolated from the air, thus minimizing the risk of fuel oxidation and the subsequent negative effects on engine performance.
The durability of rubber fuel lines is further enhanced by their ability to resist abrasion. These lines are often subjected to constant movement and friction as the vehicle's engine operates. Rubber's flexibility and resilience allow it to absorb shocks and vibrations, reducing the likelihood of damage from rubbing against other components or the engine block. This abrasion resistance is crucial, especially in high-performance vehicles or those with modified engines, where the fuel lines may experience more intense mechanical stress.
In the context of fuel lines, durability is not just about the material's strength but also its ability to maintain flexibility over a wide temperature range. Rubber fuel lines can withstand extreme temperatures, from the intense heat generated by the engine during operation to the cold temperatures encountered during winter. This flexibility ensures that the lines remain pliable and do not become brittle, which could lead to cracks or leaks.
The resistance to fuel degradation and abrasion is a direct result of the careful selection and formulation of rubber compounds used in manufacturing. Engineers choose specific rubber types, such as natural or synthetic rubbers, based on their properties. For instance, natural rubber is known for its excellent flexibility and resistance to abrasion, making it ideal for fuel lines. Synthetic rubbers, on the other hand, offer improved durability and resistance to heat and chemicals, ensuring the fuel lines can withstand the rigors of everyday use.
In summary, the durability of rubber fuel lines is a critical feature that ensures the reliable operation of a vehicle's fuel system. Their resistance to fuel degradation and abrasion allows them to maintain the integrity of the fuel, preventing harmful substances from entering the engine. This, in turn, contributes to better engine performance, fuel efficiency, and overall longevity, making rubber fuel lines a vital component in any vehicle's maintenance routine.
Wedeater Fuel Lines Reversed: A Recipe for Disaster?
You may want to see also
Compatibility: Rubber fuel lines are compatible with most fuel types
Rubber fuel lines are an essential component in the fuel delivery system of many vehicles and machinery. These lines are designed to transmit fuel from the tank to the engine, ensuring a continuous and efficient supply of power. One of the key advantages of rubber fuel lines is their compatibility with a wide range of fuel types, making them a versatile choice for various applications.
The compatibility of rubber fuel lines with different fuels is a result of the material's inherent properties. Rubber is naturally resistant to degradation caused by most common fuels, including gasoline, diesel, and even alcohol-based blends. This resistance ensures that the fuel lines can withstand the chemical composition of these fuels without breaking down or becoming brittle over time. As a result, rubber fuel lines can be used in a variety of vehicles and equipment, regardless of the specific fuel type employed.
In the automotive industry, compatibility is a critical factor when selecting fuel lines. Different vehicles may use various types of fuel, such as leaded or unleaded gasoline, diesel, or even alternative fuels like ethanol or biodiesel. Rubber fuel lines can accommodate these diverse fuel types, ensuring a reliable and safe fuel supply to the engine. This versatility is particularly important for classic car enthusiasts who often work with vehicles that use older, less common fuels.
Furthermore, rubber's flexibility and durability contribute to its compatibility with most fuel types. The material's ability to bend and stretch without compromising its structural integrity allows it to navigate the intricate routing within a vehicle's engine bay. This flexibility is especially beneficial in tight spaces, where other materials might not be able to withstand the physical demands of the fuel delivery system. Additionally, rubber's resistance to abrasion and impact damage ensures that the fuel lines remain intact and functional, even in challenging operating conditions.
In summary, rubber fuel lines are highly compatible with most fuel types due to the material's inherent resistance to degradation and its flexible yet durable nature. This compatibility makes rubber fuel lines a reliable choice for a wide range of vehicles and machinery, ensuring efficient and safe fuel delivery to the engine. Whether it's a modern gasoline-powered car or an older diesel engine, rubber fuel lines can provide the necessary connectivity without compromising performance or safety.
Unleash Engine Power: Discover the Magic of Inline Fuel Catalysts
You may want to see also
Installation: Rubber fuel lines are easy to install and connect to fuel systems
Rubber fuel lines are an essential component of any fuel system, providing a flexible and durable connection between the fuel tank and the engine. When it comes to installation, these lines offer a straightforward and efficient process, ensuring a reliable fuel supply to your vehicle's engine. The installation process typically begins with carefully selecting the appropriate rubber fuel line for your specific application. It's crucial to consider factors such as the length required, the diameter that matches your fuel system's specifications, and the overall quality of the material. High-quality rubber fuel lines are designed to withstand the rigors of the fuel system, including potential heat and pressure variations.
Once you have the right fuel line, the installation process becomes relatively simple. Start by locating the fuel tank and identifying the existing fuel lines that need to be replaced or connected to. Carefully remove the old lines, ensuring you have the necessary tools and a clear understanding of the layout to avoid any damage. Now, it's time to connect the new rubber fuel line. Begin by aligning the male and female ends of the line, ensuring a precise fit. Use the provided fittings or clamps to secure the line in place, making sure it is tightly fastened to prevent any fuel leaks. It's important to follow the manufacturer's guidelines for the specific type of fitting you are using.
When connecting the fuel line to the fuel tank, locate the appropriate port and ensure it matches the line's end. Insert the line into the port, pushing it until it is fully seated. Tighten the connection securely, but be careful not to overtighten, as this can damage the fuel line. Similarly, when connecting to the engine, locate the fuel rail or injection system and attach the line accordingly. Again, ensure a tight connection to prevent any fuel from escaping.
One of the key advantages of rubber fuel lines is their flexibility, which makes installation a breeze. These lines can easily conform to the existing fuel system's layout, allowing for a neat and efficient connection. Additionally, the use of fittings and clamps ensures a secure and long-lasting bond, providing peace of mind that your fuel system is reliable and safe.
In summary, installing rubber fuel lines is a manageable task that can be accomplished with relative ease. By carefully selecting the right size and quality of the line, following the manufacturer's instructions, and ensuring secure connections, you can effectively upgrade or repair your fuel system. This installation process highlights the practicality and reliability of rubber fuel lines, making them an excellent choice for maintaining a robust and efficient fuel supply in various vehicles.
Engine Trouble: What Happens When Your Fuel Line Seals Fail
You may want to see also
Frequently asked questions
The OD rubber fuel line is a crucial component in fuel delivery systems, especially in automotive applications. It is designed to transport fuel from the tank to the engine while providing flexibility and durability. The OD refers to the diameter of the rubber tube, which determines its capacity to hold and convey fuel efficiently.
The OD rubber fuel line stands out due to its specific construction and material. It is typically made from high-quality rubber compounds that offer excellent resistance to fuel chemicals, ensuring the integrity of the fuel over time. The OD measurement is critical as it allows for a precise fit with fuel injectors, pumps, and other fuel system components.
OD rubber fuel lines provide several benefits. Firstly, their flexibility allows for easy installation and routing around engine components. Secondly, the rubber material is resistant to cracking and aging, ensuring a long-lasting fuel supply. Additionally, the OD design enables a secure connection to fuel system parts, minimizing fuel leaks and improving overall system efficiency.
Yes, OD rubber fuel lines are often used as replacements for standard fuel lines. However, it is essential to ensure that the OD of the new fuel line matches the existing fuel system components. Proper sizing and compatibility are crucial to avoid any performance issues or fuel leaks. Consulting the vehicle's manual or seeking professional advice is recommended for accurate replacement.
Regular maintenance is essential to ensure the longevity of OD rubber fuel lines. It is advised to inspect the lines for any signs of damage, cracks, or swelling regularly. Fuel lines should be kept away from heat sources and sharp objects to prevent deterioration. Cleaning the fuel system periodically can also help maintain the performance and cleanliness of the fuel lines.