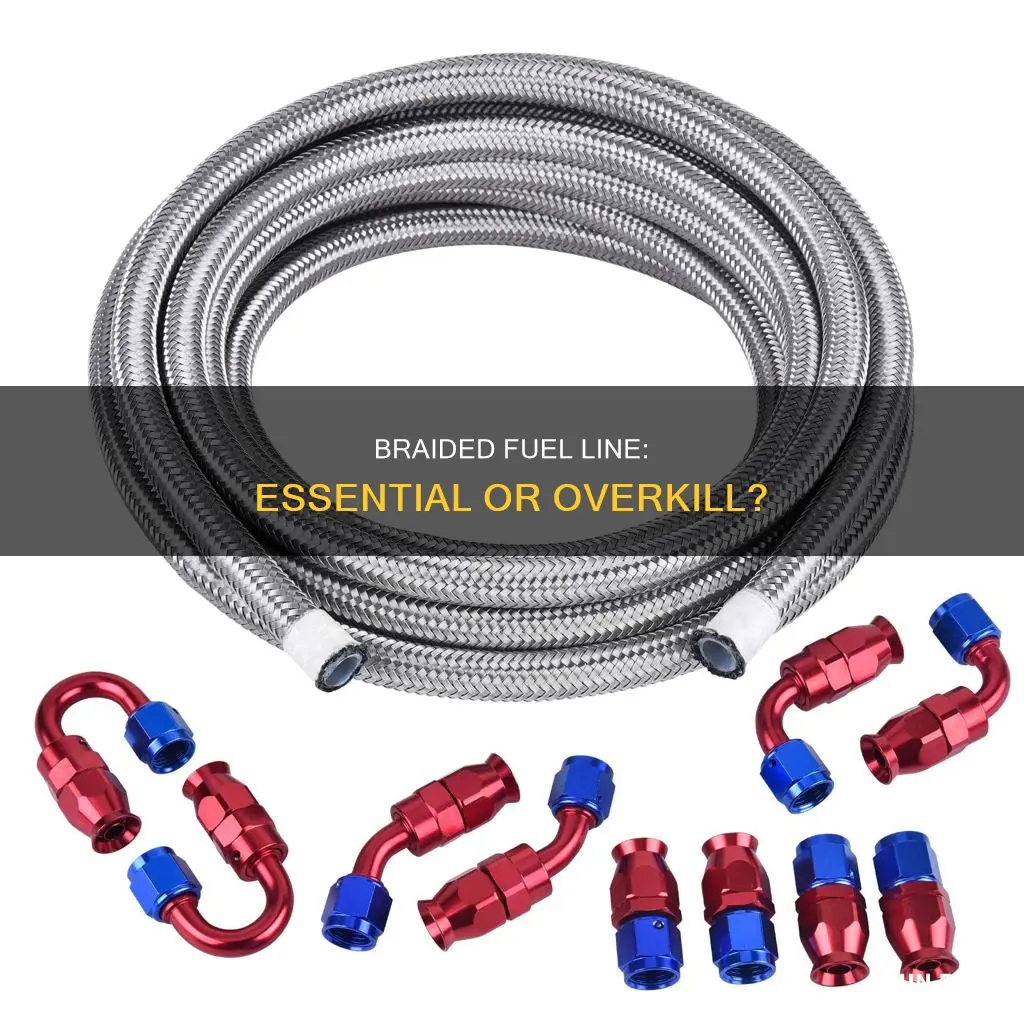
Fuel injection systems in modern vehicles have evolved to become more efficient and reliable, and one crucial component of this system is the fuel line. When it comes to choosing the right fuel line for fuel injection systems, braided lines have become a popular choice among automotive enthusiasts and mechanics. The question arises: does fuel injection require braided lines? This paragraph will explore the importance of fuel lines in fuel injection systems and delve into the benefits and considerations of using braided lines, providing insights into why they are often preferred for optimal performance and longevity.
Characteristics | Values |
---|---|
Fuel Injection System | Braided lines are often used in fuel injection systems, especially in high-performance applications. |
Braided Line Material | Braided lines are typically made from materials like steel, stainless steel, or synthetic fibers, ensuring durability and flexibility. |
Performance Benefits | Braided lines can improve fuel delivery, provide better response, and enhance overall engine performance. |
Durability | Braided lines are designed to withstand high pressure and temperature, making them suitable for racing and extreme conditions. |
Compatibility | These lines are compatible with various fuel injection systems, including electronic and mechanical setups. |
Installation | Proper installation is crucial; braided lines may require specific techniques to ensure a secure and leak-free connection. |
Maintenance | Regular inspection and maintenance are recommended to ensure the longevity of the braided fuel lines. |
Cost | Braided lines can be more expensive compared to standard rubber lines but offer superior performance and longevity. |
Availability | Braided fuel lines are widely available from automotive suppliers and specialty stores. |
What You'll Learn
- Braided Line Material: Braided lines are made from various materials, each with unique properties affecting fuel injection performance
- Line Diameter: The diameter of the braided line impacts fuel flow rate and pressure drop, influencing engine performance
- Flexibility and Durability: Braided lines offer flexibility and durability, ensuring reliable fuel delivery under various engine conditions
- Compatibility: Different fuel injection systems require specific braided line types for optimal performance and compatibility
- Installation and Maintenance: Proper installation and maintenance of braided lines are crucial for maintaining fuel injection system efficiency
Braided Line Material: Braided lines are made from various materials, each with unique properties affecting fuel injection performance
Braided lines are an essential component in fuel injection systems, playing a critical role in delivering fuel from the tank to the engine. The material used in these lines is crucial, as it directly impacts the performance and longevity of the fuel injection system. Braided lines are constructed using different materials, each with its own set of advantages and disadvantages.
One common material used in braided fuel lines is rubber. Rubber is known for its flexibility and durability, making it an ideal choice for fuel lines. It can withstand the high pressure and temperature fluctuations associated with fuel injection systems. Rubber braided lines are often used in high-performance applications due to their ability to absorb vibrations and reduce noise. However, rubber can be susceptible to degradation over time, especially when exposed to certain chemicals in fuel, which may lead to cracking or leaks.
Another popular material is silicone, which offers excellent heat resistance and flexibility. Silicone braided lines can handle extreme temperatures and are often used in racing applications where fuel temperatures can vary widely. This material is also resistant to UV radiation, making it suitable for outdoor use. Despite its advantages, silicone may not be as durable as other materials and can be more expensive.
Braided lines can also be made from materials like nylon or polyester. These synthetic fibers provide excellent strength and flexibility, ensuring the lines can withstand the rigors of fuel delivery. Nylon and polyester are often used in high-pressure applications and can handle the corrosive effects of fuel. Additionally, these materials are lightweight, contributing to improved fuel efficiency.
The choice of braided line material depends on various factors, including the specific engine requirements, environmental conditions, and performance expectations. For instance, in high-performance racing environments, materials like silicone or specialized synthetic blends might be preferred for their ability to handle extreme conditions. In contrast, for everyday use, rubber or a balanced synthetic blend could offer a cost-effective solution without compromising performance. Understanding the properties of different braided line materials is crucial for ensuring optimal fuel injection performance and maintaining the overall health of the engine.
Unclogging the Blower Fuel Line: A Step-by-Step Guide
You may want to see also
Line Diameter: The diameter of the braided line impacts fuel flow rate and pressure drop, influencing engine performance
The diameter of the braided fuel line is a critical factor in the performance of fuel injection systems, especially in high-performance engines. This component plays a vital role in ensuring that the fuel is delivered efficiently and effectively to the engine's combustion chambers. Here's a detailed breakdown of how line diameter influences engine performance:
Fuel Flow Rate: The diameter of the braided line directly affects the fuel flow rate. A larger diameter allows for a higher volume of fuel to pass through the line per unit of time. This is crucial for engines that require precise and rapid fuel delivery to meet performance demands. For instance, in high-performance racing cars, a larger line diameter can provide the necessary fuel flow to support the engine's power output, ensuring optimal performance during acceleration and high-speed maneuvers.
Pressure Drop: As fuel moves through the braided line, it experiences a pressure drop, which is the reduction in pressure from the source to the engine. The line diameter significantly influences this pressure drop. A smaller diameter will result in a more significant pressure loss, which can lead to reduced engine performance. When the pressure drop is too high, it may cause fuel atomization issues, leading to poor engine operation and reduced power output. Therefore, selecting the appropriate line diameter is essential to maintain the required pressure for efficient fuel injection.
Engine Performance Optimization: To optimize engine performance, it is essential to match the line diameter with the engine's requirements. Engineers and tuners often adjust the line diameter to fine-tune the fuel injection system. A larger diameter can improve low-end torque and overall engine response, while a smaller diameter might be used to reduce fuel consumption and improve fuel efficiency. This adjustment ensures that the engine operates at its peak performance while maintaining the desired fuel-air mixture.
In summary, the diameter of the braided fuel line is a critical consideration in fuel injection systems. It directly impacts the fuel flow rate and pressure drop, which, in turn, influence the engine's performance. By understanding and carefully selecting the appropriate line diameter, engineers can optimize fuel delivery, ensuring that the engine operates efficiently and delivers the required power output. This is particularly important in high-performance applications where every detail matters to achieve the best results.
Dissolving Fuel Line: Uncover the Mystery Behind Your Chainsaw's Malfunction
You may want to see also
Flexibility and Durability: Braided lines offer flexibility and durability, ensuring reliable fuel delivery under various engine conditions
Braided fuel lines are an essential component in the fuel injection system of modern vehicles, offering a range of benefits that contribute to optimal engine performance and longevity. One of the key advantages of braided lines is their flexibility and durability, which are crucial for reliable fuel delivery in various engine conditions.
Flexibility is a critical factor in fuel line design, especially in high-performance vehicles where engine movement and vibrations are common. Braided lines are constructed with multiple layers of materials, typically a rubber or synthetic compound, braided together to form a strong yet flexible structure. This design allows the lines to bend and move with the engine, ensuring that the fuel remains under pressure and is delivered efficiently to the injectors. The flexibility of braided lines is particularly important in high-performance applications, where sudden acceleration and deceleration can put significant stress on the fuel system.
Durability is another essential aspect of braided fuel lines. These lines are designed to withstand the harsh conditions of an engine bay, including extreme temperatures, vibrations, and chemical exposure from fuel and engine oil. The braided construction provides excellent resistance to wear and tear, ensuring that the lines remain intact and functional over extended periods. Braided lines are also less susceptible to damage from engine components, such as moving parts or sharp edges, which can occur in traditional rubber lines. This durability is vital for maintaining a consistent fuel supply, especially in high-demand situations, where a failure in the fuel system could lead to engine misfires or complete shutdown.
The flexibility and durability of braided lines contribute to the overall reliability of the fuel injection system. By ensuring a consistent and efficient fuel supply, these lines help maintain engine performance, fuel economy, and emissions standards. Additionally, the reduced risk of fuel leaks and the ability to withstand engine vibrations make braided lines a preferred choice for high-performance and racing applications.
In summary, braided fuel lines offer a unique combination of flexibility and durability, making them an indispensable part of modern fuel injection systems. Their ability to withstand engine conditions and deliver fuel reliably is essential for optimal engine performance and longevity, especially in demanding environments. Understanding the importance of these braided lines can guide vehicle owners and mechanics in making informed decisions regarding fuel system maintenance and upgrades.
Unveiling the Tvr Tasmin's Fuel Line Mystery: Size Matters!
You may want to see also
Compatibility: Different fuel injection systems require specific braided line types for optimal performance and compatibility
When it comes to fuel injection systems, the choice of braided fuel lines is a critical component that can significantly impact performance and longevity. The compatibility of these lines with the specific fuel injection system is essential to ensure optimal operation. Different fuel injection systems have unique requirements, and using the correct type of braided line is crucial to avoid potential issues.
Braided fuel lines are designed to withstand high-pressure environments and provide a flexible yet robust connection between the fuel pump and the engine. The compatibility aspect comes into play when considering the various fuel injection technologies available. For instance, a fuel injection system designed for a high-performance racing engine will have different pressure and flow rate demands compared to a standard production car's system. The braided line must be able to handle these specific requirements without compromising performance or reliability.
In the automotive industry, there are several types of fuel injection systems, including electronic, mechanical, and pump-line-injector (PLI) systems. Each of these systems has its own set of specifications and pressure requirements. For example, electronic fuel injection systems often operate at higher pressures and require braided lines with specific inner diameters and wall thicknesses to ensure efficient fuel delivery. On the other hand, mechanical fuel injection systems may have different pressure needs, and the braided line must be compatible with these lower-pressure environments.
The compatibility of braided fuel lines is also essential when considering the materials used. Braided lines can be made from various materials such as steel, stainless steel, or synthetic fibers. The choice of material depends on the specific fuel injection system and its operating conditions. For instance, high-temperature environments may require braided lines with materials that can withstand extreme heat without degradation. Similarly, the inner diameter and wall thickness of the braided line should match the system's requirements to ensure proper fuel flow and pressure regulation.
In summary, when dealing with fuel injection systems, it is imperative to understand the specific compatibility requirements of the braided fuel lines. Different systems have unique pressure, flow rate, and material needs. Using the correct type of braided line ensures optimal performance, reliability, and longevity of the fuel injection system. Always refer to the manufacturer's guidelines and specifications to choose the right braided line for your particular fuel injection setup.
Fixing Fuel Lines: A Guide to Replacing Homelite Chainsaw Lines
You may want to see also
Installation and Maintenance: Proper installation and maintenance of braided lines are crucial for maintaining fuel injection system efficiency
The installation and maintenance of braided fuel lines are essential aspects of ensuring optimal performance and longevity of the fuel injection system in vehicles. These lines play a critical role in delivering fuel from the tank to the engine, and any issues with their installation or upkeep can lead to decreased efficiency and potential engine problems.
When installing braided lines, it is imperative to follow the manufacturer's guidelines. These lines are designed to withstand high-pressure fuel flow and should be routed carefully to avoid sharp bends or kinks, which can restrict fuel flow and cause engine misfires. Proper crimping and securing of the lines to the fuel rail and injectors are also vital to prevent leaks and ensure a tight fit. Using the correct tools and taking the time to double-check connections can make a significant difference in the system's overall performance.
Maintenance is another key factor in keeping the fuel injection system in top condition. Regular inspections should be conducted to identify any signs of wear and tear, such as cracks, brittleness, or damage from rodents or debris. Braided lines can be susceptible to degradation over time due to fuel quality, temperature fluctuations, and exposure to sunlight. Replacing the lines periodically, especially if they show signs of deterioration, is essential to prevent fuel leaks and maintain the engine's performance.
In addition to visual inspections, monitoring the fuel pressure and flow rates can provide valuable insights into the system's health. If the pressure drops or flow rates deviate from the expected values, it may indicate a problem with the braided lines or other components. Addressing these issues promptly can prevent costly repairs and ensure the engine operates efficiently.
Lastly, using high-quality braided lines and adhering to the manufacturer's recommendations for installation and maintenance can significantly contribute to the long-term reliability of the fuel injection system. Proper care and attention to these details will result in a well-functioning engine, delivering improved performance and fuel efficiency.
John Deere LX255 Fuel Line Location: A Comprehensive Guide
You may want to see also
Frequently asked questions
Braided lines, also known as fuel lines, are used in fuel injection systems to ensure a consistent and reliable fuel supply to the engine. These lines are designed to withstand high pressure and temperature, providing a secure and flexible connection between the fuel pump and the engine's fuel injectors.
Braided lines offer several advantages over traditional rubber lines. They provide superior flexibility, making them easier to route through the engine compartment. The braided construction also ensures a longer lifespan, as it can handle higher pressure without cracking or deteriorating over time. This durability is crucial for maintaining a reliable fuel supply.
While standard rubber lines can be used, they are generally not recommended for fuel injection systems. Rubber lines may not withstand the high pressure and temperature fluctuations, leading to potential leaks or fuel contamination. Braided lines are specifically engineered to meet the demands of fuel injection, ensuring optimal performance and longevity.