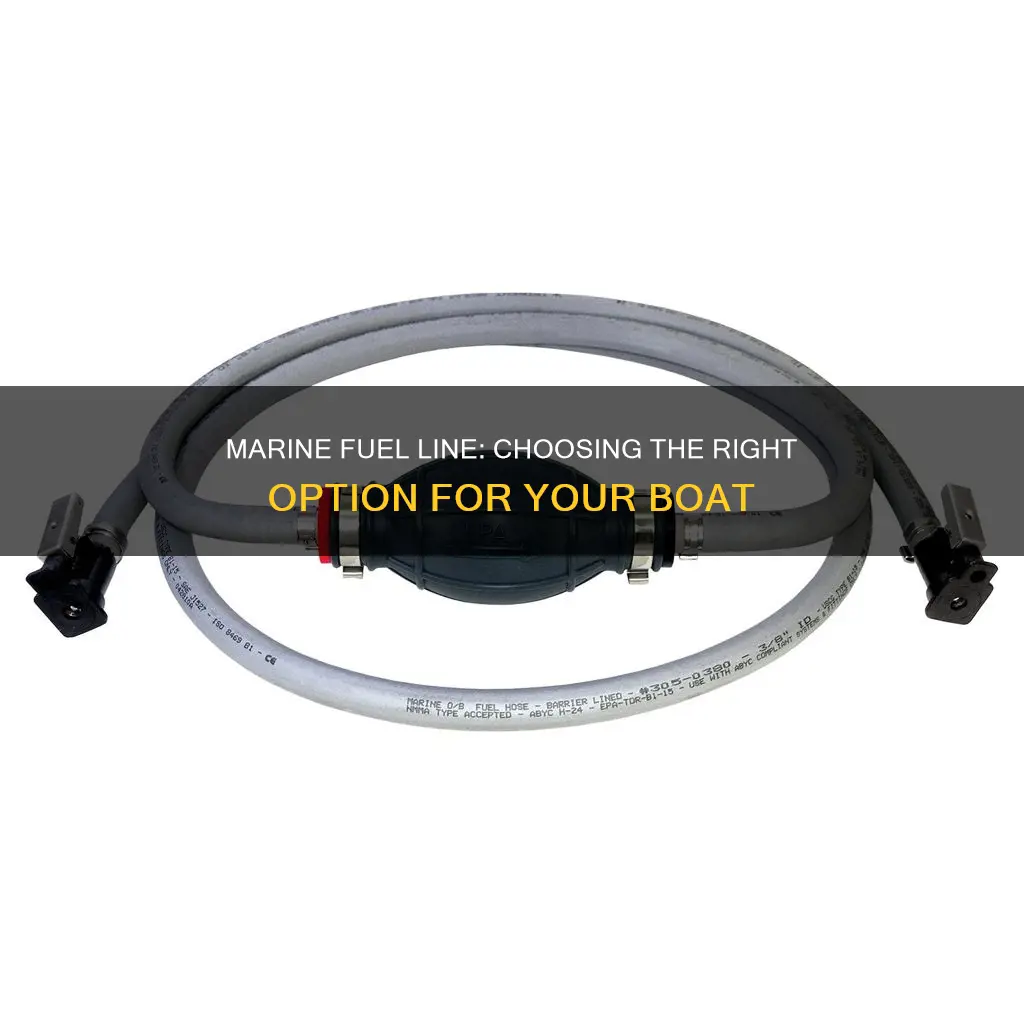
When it comes to marine applications, choosing the right fuel line is crucial for optimal performance and safety. Marine environments demand fuel lines that can withstand the harsh conditions of saltwater exposure, UV radiation, and temperature fluctuations. In this context, specific fuel lines are designed and rated for marine use, offering enhanced durability and resistance to corrosion. These specialized fuel lines are typically made from materials like stainless steel or high-density polyethylene, ensuring they can handle the unique challenges of marine environments. Understanding the requirements and characteristics of these marine-rated fuel lines is essential for boat owners and operators to ensure reliable and safe fuel delivery systems.
What You'll Learn
- Marine-grade fuel lines are designed for saltwater environments and resistant to corrosion
- These lines are often made from materials like stainless steel or brass
- They can withstand high pressure and temperatures, ensuring reliable fuel delivery
- Marine fuel lines are tested to meet industry standards for durability and performance
- Proper installation and maintenance are crucial for long-term reliability in marine applications
Marine-grade fuel lines are designed for saltwater environments and resistant to corrosion
Marine-grade fuel lines are specifically engineered to withstand the harsh conditions of saltwater environments, making them an essential component for any marine vessel. These fuel lines are designed to resist corrosion, ensuring longevity and reliability in the demanding marine setting. The unique challenges of saltwater exposure require a robust solution, and that's exactly what marine-grade fuel lines offer.
One of the key features of these fuel lines is their ability to resist corrosion, which is a critical factor in marine applications. Saltwater environments are highly corrosive due to the presence of salt, which can accelerate the deterioration of traditional fuel lines. Marine-grade fuel lines are constructed with materials that are inherently resistant to corrosion, ensuring they can withstand the constant exposure to saltwater. This resistance is achieved through the use of specialized coatings and compounds that create a protective barrier against the corrosive effects of salt and other marine elements.
The design and construction of marine-grade fuel lines also take into account the dynamic nature of marine operations. These fuel lines are flexible and durable, capable of withstanding the constant movement and vibrations experienced on a vessel. They are designed to resist kinking, twisting, and damage from marine life, ensuring a reliable fuel supply even in the most challenging conditions. The flexibility and strength of these fuel lines make them ideal for connecting fuel tanks to engines, providing a safe and efficient fuel delivery system.
In addition to corrosion resistance, marine-grade fuel lines also offer excellent resistance to UV radiation and temperature fluctuations. The harsh marine environment can expose fuel lines to intense sunlight and extreme temperatures, which can cause degradation over time. These fuel lines are engineered to maintain their integrity under such conditions, ensuring a consistent and reliable performance. The UV-resistant materials and temperature-stable compounds used in their construction provide an added layer of protection, making them suitable for long-term use in marine settings.
When selecting fuel lines for marine applications, it is crucial to choose those specifically rated for marine use. These lines are tested and certified to meet the rigorous standards required for saltwater environments. By opting for marine-grade fuel lines, vessel owners and operators can ensure the safety and efficiency of their fuel systems, contributing to the overall reliability of their marine operations. Proper installation and regular maintenance are also essential to maximize the performance and lifespan of these specialized fuel lines.
Unleash Engine Power: Understanding Fuel Line Cleaner's Magic
You may want to see also
These lines are often made from materials like stainless steel or brass
When it comes to choosing fuel lines for marine applications, the materials used play a crucial role in ensuring durability and reliability. These lines are specifically designed to withstand the harsh conditions of marine environments, including exposure to saltwater, varying temperatures, and potential corrosion. One of the primary materials used for this purpose is stainless steel.
Stainless steel is an excellent choice for marine fuel lines due to its inherent corrosion resistance. It is known for its ability to maintain its structural integrity even in the presence of saltwater, which is a common challenge in marine settings. This material is highly durable and can handle the constant flexing and movement associated with marine vessels. The stainless steel fuel lines are often preferred for their long-lasting performance and ability to resist rust and scale buildup, ensuring a consistent and reliable fuel supply.
Another popular material for marine fuel lines is brass. Brass is an alloy of copper and zinc, offering a unique combination of properties. It is highly resistant to corrosion, making it ideal for marine use. The natural protective oxide layer that forms on brass surfaces helps prevent further corrosion, ensuring the longevity of the fuel lines. Additionally, brass has excellent mechanical properties, including good tensile strength and ductility, allowing it to withstand the stresses of marine environments without compromising its structural integrity.
The choice between stainless steel and brass often depends on specific application requirements. Stainless steel is generally more expensive but offers superior corrosion resistance, making it suitable for long-term exposure to saltwater. On the other hand, brass can be a more cost-effective option for certain marine applications, especially when quick installation and ease of use are priorities. Both materials are readily available and can be easily fabricated to meet the unique needs of marine fuel systems.
In summary, marine fuel lines are often crafted from materials like stainless steel and brass, each offering distinct advantages. Stainless steel provides exceptional corrosion resistance, ensuring long-term durability, while brass offers a balance of cost-effectiveness and corrosion resistance. Understanding these material properties is essential for selecting the right fuel lines to ensure a safe and efficient marine fuel system.
Unraveling the Mystery: What's Beneath the Fuel Line in Elite: Dangerous
You may want to see also
They can withstand high pressure and temperatures, ensuring reliable fuel delivery
When it comes to marine applications, fuel lines play a critical role in ensuring the reliable delivery of fuel to the engine. One of the key requirements for fuel lines in this context is their ability to withstand high pressure and temperatures, which is a challenge given the harsh marine environment. Marine fuel lines are designed to meet these demanding conditions, providing a robust and reliable solution for fuel transport.
The construction of these specialized fuel lines involves using materials that can handle the extreme pressures and temperatures encountered in marine settings. High-pressure fuel lines are typically made from durable materials such as stainless steel or reinforced rubber compounds. These materials offer excellent resistance to abrasion, corrosion, and fatigue, ensuring that the fuel lines can withstand the constant flexing and movement associated with marine operations.
In addition to material selection, the design of marine fuel lines also plays a crucial role in their performance. These lines often feature a braided or reinforced construction, which provides additional strength and flexibility. The braids or reinforcements are strategically placed to handle the high-pressure environment, ensuring that the fuel lines remain intact even when subjected to significant stress. This design consideration is vital for maintaining a consistent and reliable fuel supply to the engine.
Furthermore, marine fuel lines are often equipped with protective coatings or sheathing to enhance their durability. These protective layers shield the fuel lines from potential damage caused by saltwater, UV radiation, and other marine-specific hazards. By incorporating such protective measures, the fuel lines can maintain their structural integrity and performance over extended periods of use.
In summary, marine fuel lines are engineered to excel in high-pressure and high-temperature environments, ensuring the reliable delivery of fuel to marine engines. Their construction, utilizing durable materials and strategic designs, enables them to withstand the challenges posed by the marine operating conditions. With proper installation and maintenance, these fuel lines provide a vital component for the efficient and safe operation of marine vessels.
Choosing the Right Diameter Fuel Line for Your Yamaha Outboard
You may want to see also
Marine fuel lines are tested to meet industry standards for durability and performance
Marine fuel lines are an essential component of any boat's fuel system, and their design and construction are subject to rigorous testing and industry standards to ensure optimal performance and longevity in the harsh marine environment. These fuel lines are specifically engineered to withstand the unique challenges posed by saltwater, UV radiation, temperature fluctuations, and mechanical vibrations.
The testing process for marine fuel lines involves a series of rigorous procedures to evaluate their durability and performance. One of the primary methods is subjecting the fuel lines to simulated marine conditions. This includes exposing the lines to saltwater, which can cause corrosion and degradation over time. By using specialized saltwater solutions, engineers can accelerate the aging process and assess the line's resistance to corrosion and material deterioration.
Additionally, fuel lines are tested for their ability to withstand extreme temperatures, both hot and cold. Marine environments can experience rapid temperature changes, and the fuel lines must remain flexible and intact under these conditions. This involves subjecting the lines to temperature cycles, simulating the extreme weather conditions boats may encounter during their journeys.
Another critical aspect of testing is evaluating the fuel lines' resistance to mechanical stress. Boats operate in dynamic environments, with constant movement and vibrations. The fuel lines must be able to withstand these forces without compromising their structural integrity. Engineers use specialized equipment to apply vibrations and simulate the mechanical stresses that the fuel lines will experience during normal boat operation.
Furthermore, marine fuel lines are tested for their ability to resist fuel contamination and maintain flow efficiency. The lines are designed to prevent the ingress of saltwater and other contaminants, ensuring that the fuel remains clean and free-flowing. This is crucial for engine performance and longevity, as contaminated fuel can lead to engine issues and reduced efficiency.
By adhering to these industry standards and conducting comprehensive testing, manufacturers can ensure that marine fuel lines meet the demanding requirements of the marine environment. This includes providing reliable fuel transport, withstanding harsh conditions, and maintaining performance over extended periods. The result is a fuel line system that is not only durable but also contributes to the overall safety and efficiency of marine vessels.
Honda Small Engine Fuel Line: Understanding the Fuel System
You may want to see also
Proper installation and maintenance are crucial for long-term reliability in marine applications
The proper installation and maintenance of fuel lines are critical aspects of ensuring the long-term reliability and performance of marine engines. Marine environments present unique challenges due to the exposure to saltwater, corrosion, and varying temperatures, which can accelerate wear and tear on fuel lines. Therefore, choosing the right fuel line rated for marine use is just the first step; the subsequent installation and maintenance processes are equally vital.
When installing fuel lines in a marine setting, it's essential to use high-quality materials that can withstand the harsh marine environment. This includes using fuel lines with a flexible, durable construction that can resist kinking, crushing, and damage from sharp objects. The lines should also be made from materials that are resistant to corrosion, such as those made from stainless steel or high-density polyethylene (HDPE). Proper routing is another critical aspect of installation. Fuel lines should be routed away from heat sources, such as exhaust systems and engine components, to prevent damage from heat. They should also be secured with appropriate clamps or ties to prevent movement and potential damage during operation.
Regular maintenance is equally important to ensure the continued reliability of marine fuel lines. This includes periodic inspections to check for signs of wear, damage, or corrosion. Inspecting the fuel lines for any cracks, leaks, or signs of deterioration is essential. If any issues are found, they should be addressed promptly to prevent further damage. Regular cleaning of the fuel lines can also help remove any built-up contaminants or debris that could affect performance. This can be done using a fuel line cleaner or by flushing the system with fresh fuel.
In addition to visual inspections, it's crucial to monitor the pressure and flow rates of the fuel system. Marine engines require a consistent and reliable fuel supply, and any deviations from the expected pressure and flow rates could indicate a problem with the fuel lines or other components. Regularly checking and adjusting the fuel pressure can help ensure optimal engine performance and prevent issues such as engine misfires or stalling.
Lastly, keeping detailed records of maintenance activities and inspections is beneficial. This documentation can help identify patterns or recurring issues and provide valuable information for future maintenance planning. By following these proper installation and maintenance practices, marine engine owners can ensure that their fuel lines remain reliable and perform optimally, even in the challenging marine environment.
Understanding Fuel Line Direction: The Switch's Crucial Role
You may want to see also
Frequently asked questions
The key factor is selecting a fuel line that is compatible with the fuel type used in marine engines. Different fuels, such as gasoline, diesel, or marine-specific blends, require specific fuel lines to ensure safe and efficient operation.
Yes, marine fuel lines are typically made from materials that can withstand the harsh marine environment. Common materials include high-density polyethylene (HDPE), cross-linked polyethylene (PE-X), or specialized rubber compounds that offer excellent resistance to fuel, UV radiation, and temperature variations.
Look for fuel lines specifically labeled as "marine-grade" or "marine-rated." These lines often have additional features like improved flexibility, resistance to corrosion, and the ability to handle higher fuel pressures, making them suitable for the demanding conditions of marine environments.
It is generally not recommended. Regular fuel lines may not meet the performance and durability requirements of marine applications. Marine-specific fuel lines are designed to handle the unique challenges of saltwater exposure, temperature changes, and fuel volatility, ensuring reliable operation and preventing potential engine damage.
The lifespan can vary depending on factors like fuel type, environmental conditions, and maintenance. However, with proper care and regular inspections, marine fuel lines can typically last between 5 to 10 years or more. Regular replacement is advised to ensure optimal engine performance and safety.