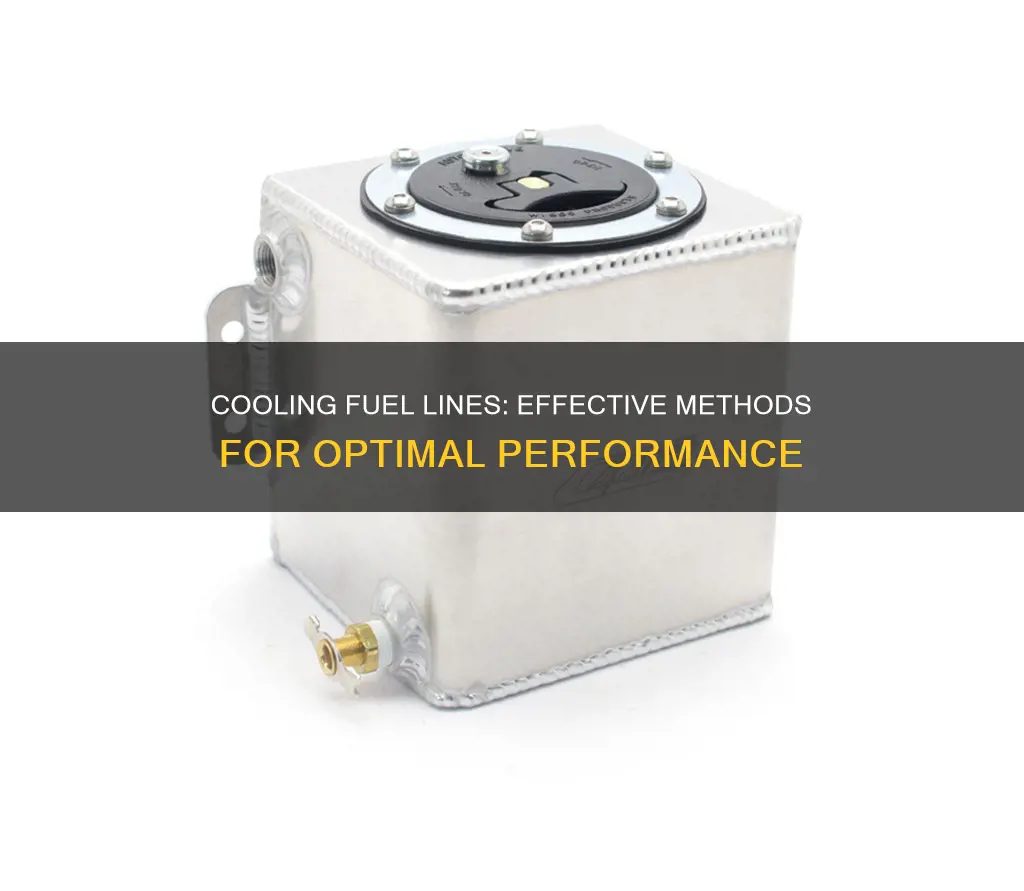
Cooling fuel lines is an important aspect of vehicle maintenance, especially for engines that operate in high-temperature environments or during extended periods of use. Proper cooling ensures that the fuel remains at an optimal temperature, preventing issues such as fuel degradation, engine misfires, and reduced performance. This guide will explore various methods and techniques to effectively cool fuel lines, including the use of heat shields, insulated sleeves, and cooling systems designed specifically for fuel lines. By implementing these strategies, vehicle owners can maintain the integrity of their fuel and enhance the overall reliability of their engines.
What You'll Learn
- Insulation: Wrap fuel lines with heat-resistant material to prevent overheating
- Routing: Route fuel lines away from hot components to avoid heat transfer
- Coolant Integration: Use a coolant system to absorb and dissipate heat from fuel lines
- Ventilation: Ensure proper ventilation to reduce heat buildup in enclosed spaces
- Regular Inspection: Check for damage and ensure proper connections to maintain cooling
Insulation: Wrap fuel lines with heat-resistant material to prevent overheating
Insulating fuel lines is a crucial step in ensuring the efficient and safe operation of any vehicle's fuel system. When fuel lines are exposed to high temperatures, they can overheat, leading to a variety of issues such as fuel degradation, reduced performance, and even potential safety hazards. One of the most effective methods to combat this problem is by wrapping the fuel lines with heat-resistant materials.
Heat-resistant insulation materials are specifically designed to withstand elevated temperatures without compromising their structural integrity. These materials can be made from various substances, including fiberglass, ceramic fibers, or specialized synthetic polymers. The choice of insulation material depends on factors such as the operating temperature range, the fuel's chemical properties, and the overall design of the fuel system. For instance, fiberglass insulation is commonly used due to its affordability and effectiveness in managing moderate to high temperatures.
The process of insulating fuel lines involves carefully wrapping the lines with the chosen heat-resistant material. This should be done in a neat and continuous manner, ensuring full coverage of the fuel lines. It is essential to follow the manufacturer's guidelines for the specific insulation product being used, as different materials may have unique application instructions. Proper insulation ensures that the fuel lines are protected from direct heat sources, such as exhaust systems or engine components, and also provides a barrier against environmental factors like sunlight and heat from nearby surfaces.
When applying the insulation, it's important to consider the flexibility of the material to accommodate any movement or expansion of the fuel lines. The insulation should be secure enough to prevent any potential damage but also allow for the lines to move freely without restriction. Additionally, the insulation should be sealed at the ends to prevent any exposure of the fuel lines to the environment.
By implementing this insulation technique, you can effectively prevent overheating of the fuel lines, ensuring the longevity and optimal performance of your vehicle's fuel system. This method is particularly beneficial in high-performance vehicles or those operating in extreme environmental conditions where fuel line cooling is critical. Regular inspection and maintenance of the insulation can further ensure its effectiveness and contribute to the overall reliability of the fuel system.
Gasket Sealer for Fuel Lines: A Quick Fix or a No-Go?
You may want to see also
Routing: Route fuel lines away from hot components to avoid heat transfer
When it comes to cooling fuel lines, proper routing is a critical aspect that can significantly impact the overall performance and longevity of your fuel system. The primary goal is to minimize heat transfer from hot engine components to the fuel lines, ensuring that the fuel remains at an optimal temperature for efficient combustion. Here's a detailed guide on how to achieve this:
Identify Heat Sources: Begin by understanding the sources of heat in your engine bay. Common hot components include the exhaust manifold, catalytic converter, and the engine block itself. These areas generate significant heat, and it's essential to route the fuel lines away from these potential heat sources. By doing so, you create a buffer zone that helps maintain the fuel's temperature, preventing overheating.
Strategic Placement: Route the fuel lines in a way that they are not in direct contact with the hot engine components. This can be achieved by using rubber or plastic protective sleeves or by placing the fuel lines in areas with better insulation. For example, you can run the fuel lines along the sides or top of the engine bay, away from the direct heat path. Ensure that the lines are not tightly against the engine block or manifold, as this can lead to heat absorption.
Use Insulated Materials: Consider using insulated fuel line kits, especially when routing lines near hot surfaces. These kits often include protective sleeves or jackets made from materials like rubber or foam, which provide an extra layer of insulation. Insulation helps retain the fuel's temperature, reducing the risk of vaporization and ensuring a consistent flow.
Maintain Adequate Clearance: Keep the fuel lines at a safe distance from the hot components. A general rule of thumb is to maintain at least a few inches of clearance. This spacing allows for better heat dissipation and prevents the fuel lines from becoming overheated. Adequate clearance also reduces the risk of damage to the fuel lines over time due to prolonged exposure to high temperatures.
Consider Engine Bay Layout: The layout of your engine bay plays a crucial role in effective routing. Take advantage of the available space and use it to your advantage. Route the fuel lines along areas with better airflow, as this can help dissipate heat more efficiently. Additionally, consider the placement of other components and ensure that the fuel lines do not interfere with their operation or maintenance.
By implementing these routing strategies, you can effectively minimize heat transfer and ensure that your fuel lines remain cool, even in high-temperature environments. Proper routing is a fundamental step in maintaining a healthy fuel system and optimizing engine performance.
Metal Fuel Tank Rust: Liner's Role Revealed
You may want to see also
Coolant Integration: Use a coolant system to absorb and dissipate heat from fuel lines
The integration of a coolant system is a highly effective method to manage and reduce heat in fuel lines, especially in high-performance vehicles or those operating in demanding conditions. This approach is particularly useful when dealing with fuel lines that are exposed to high temperatures, which can lead to fuel degradation, performance issues, and even safety concerns. By implementing a coolant system, you create a secondary cooling loop that works in conjunction with the primary cooling system of the engine.
Here's a detailed breakdown of the process:
- Coolant Selection: Choose a coolant that is compatible with your fuel system. Some coolants are specifically designed to handle the challenges of cooling fuel lines, including resistance to fuel degradation and corrosion. It's essential to follow the manufacturer's recommendations for coolant type and concentration.
- Coolant Reservoir and Pump: Install a dedicated coolant reservoir to store the coolant. This reservoir should be positioned in a way that allows for easy monitoring of coolant levels. A coolant pump is then used to circulate the coolant through the engine and fuel lines. The pump ensures a consistent flow, which is crucial for effective cooling.
- Coolant Circuit: The coolant circuit is designed to run parallel to the engine's cooling system. It typically includes a radiator, where the coolant can be cooled by the air, and a series of hoses that carry the coolant to and from the engine and fuel lines. The fuel lines are integrated into this circuit, allowing the coolant to absorb and transfer heat away from the fuel.
- Heat Exchange: As the coolant circulates through the engine and fuel lines, it absorbs heat from the fuel. This heat exchange process is facilitated by the close proximity of the coolant to the fuel lines, often with specialized heat exchangers or cooling jackets. The coolant then carries this heat to the radiator, where it dissipates into the surrounding air.
- Benefits: This method of coolant integration offers several advantages. Firstly, it provides a more controlled and efficient cooling solution for fuel lines, especially in high-performance applications. Secondly, it helps maintain fuel quality by preventing overheating, which can lead to fuel oxidation and contamination. Additionally, the secondary cooling loop can contribute to overall engine longevity by reducing the stress on the primary cooling system.
By implementing a coolant system for fuel line cooling, you create a robust and reliable solution to manage heat-related challenges, ensuring optimal performance and longevity of your vehicle's fuel system. This method is particularly valuable for applications where fuel lines are exposed to extreme temperatures, such as racing cars, off-road vehicles, or industrial machinery.
Mastering Fuel Line Sealing: The Ultimate Guide to Tube Nuts
You may want to see also
Ventilation: Ensure proper ventilation to reduce heat buildup in enclosed spaces
Ventilation is a critical aspect of managing heat buildup in enclosed spaces, especially when it comes to cooling fuel lines. Proper ventilation ensures that hot air and gases are effectively expelled, preventing the accumulation of heat and potential damage to the fuel lines and the overall system. Here's a detailed guide on how to ensure adequate ventilation:
Identify the Source of Heat: Before implementing any ventilation strategy, it's essential to understand the primary source of heat in the enclosed space. Fuel lines can generate heat due to the combustion process, engine operation, or even external factors like sunlight. Identify the specific areas where heat accumulation is most significant to target your ventilation efforts effectively.
Install Vents and Fans: Proper ventilation often involves the strategic placement of vents and fans. Vents should be positioned to allow for the free flow of air, ensuring that hot air can escape and cooler air can enter. Consider installing exhaust fans to create a powerful airflow, especially in areas with high heat generation. These fans can be designed to expel hot air and draw in cooler air from outside, providing a constant supply of fresh, cooler air to the fuel lines.
Utilize Natural Ventilation: In addition to mechanical ventilation, take advantage of natural processes. Open windows and doors to allow cross-ventilation, which can help regulate temperature. During cooler parts of the day or at night, when temperatures are lower, this can be an effective way to cool the enclosed space. Ensure that the openings are strategically placed to create a natural airflow, pushing hot air out and drawing cooler air in.
Consider Roof Vents: For larger enclosed spaces or industrial settings, roof vents can be highly effective. These vents allow hot air to rise and escape through the roof, providing a continuous ventilation system. Roof vents are particularly useful in preventing the buildup of heat in the upper parts of the space, which can then cascade down to cool the fuel lines and other components.
Regular Maintenance: Proper ventilation is an ongoing process that requires regular maintenance. Clean vents and fans to remove dust and debris that may obstruct airflow. Inspect and repair any damage to ventilation systems promptly to ensure their optimal performance. Regular maintenance will help maintain a consistent cooling effect on the fuel lines and prevent heat-related issues.
By implementing these ventilation strategies, you can effectively manage heat buildup in enclosed spaces, ensuring the longevity and optimal performance of fuel lines. Proper ventilation not only cools the fuel lines but also contributes to a safer and more efficient operating environment.
Fitech Fuel Line Sizing: Feed and Return Line Guide
You may want to see also
Regular Inspection: Check for damage and ensure proper connections to maintain cooling
Regular inspections of fuel lines are an essential part of vehicle maintenance to ensure optimal performance and prevent potential issues. By checking for damage and verifying the integrity of connections, you can maintain an efficient cooling system for your fuel lines. Here's a step-by-step guide to performing these inspections:
Start by visually examining the fuel lines for any signs of wear and tear. Look for cracks, punctures, or any visible damage along the length of the lines. Over time, fuel lines can deteriorate due to exposure to heat, chemicals, and mechanical stress. Inspecting the lines regularly helps identify issues early on. Check for any signs of corrosion or rust, especially if your vehicle is exposed to harsh weather conditions or operates in environments with high humidity. Corrosion can lead to reduced cooling efficiency and potential blockages.
Pay close attention to the connections between the fuel lines, the engine, and any associated components. Ensure that all fittings and clamps are secure and tight. Loose connections can result in reduced cooling performance and may even lead to fuel leaks. Carefully inspect the clamps and fittings for any signs of damage or wear. Replace any damaged components to maintain a proper seal and prevent fuel leakage, which could be dangerous.
When inspecting the fuel lines, also check for any signs of contamination or debris. Over time, fuel lines can accumulate dirt, rust, or other contaminants, especially if the fuel contains water or impurities. This buildup can restrict the flow of fuel and reduce the cooling efficiency. If you notice any debris or contamination, clean the fuel lines accordingly to restore optimal performance.
In addition to visual inspections, listen for any unusual noises during the engine's operation. Strange sounds, such as hissing or roaring, could indicate a problem with the fuel lines or the cooling system. These noises may suggest a leak or a blockage, requiring immediate attention. Addressing these issues promptly can prevent further damage and ensure the longevity of your vehicle's cooling system.
Remember, regular maintenance and inspections are key to keeping your fuel lines in good condition. By following these steps, you can identify potential problems early on and take the necessary actions to maintain an efficient cooling system for your fuel lines, ultimately ensuring the overall health and performance of your vehicle.
Bose's Fuel Line: A Revolutionary Audio Experience
You may want to see also
Frequently asked questions
One effective method is to insulate the fuel lines with a suitable material like a high-temperature rubber or plastic insulation. This insulation acts as a barrier, reducing the direct heat transfer from the engine to the fuel lines. Ensure the insulation is secure and covers the entire length of the lines, especially where they are exposed to hot engine components.
Fuel lines can overheat due to several factors. Prolonged exposure to high engine temperatures, especially in older vehicles with less advanced cooling systems, can lead to overheating. Additionally, a lack of insulation or damaged insulation allows heat to transfer directly to the fuel lines. Overheating can cause fuel to vaporize, leading to reduced performance and potential engine issues.
Yes, there are some simple DIY solutions. One popular method is to use a fuel line shield or heat shield, which is typically made of metal or heat-resistant material. These shields are placed over the fuel lines, protecting them from direct heat sources. You can also try wrapping the lines with a heat-resistant tape or using a custom-made insulation sleeve for a more tailored fit.
If you notice persistent overheating issues or experience a significant drop in engine performance, it's advisable to consult a professional mechanic. They can assess the situation and recommend appropriate solutions, such as installing a custom-made fuel line cooling system or modifying the existing cooling system to better accommodate the fuel lines. Professional help ensures a proper diagnosis and long-lasting solution.