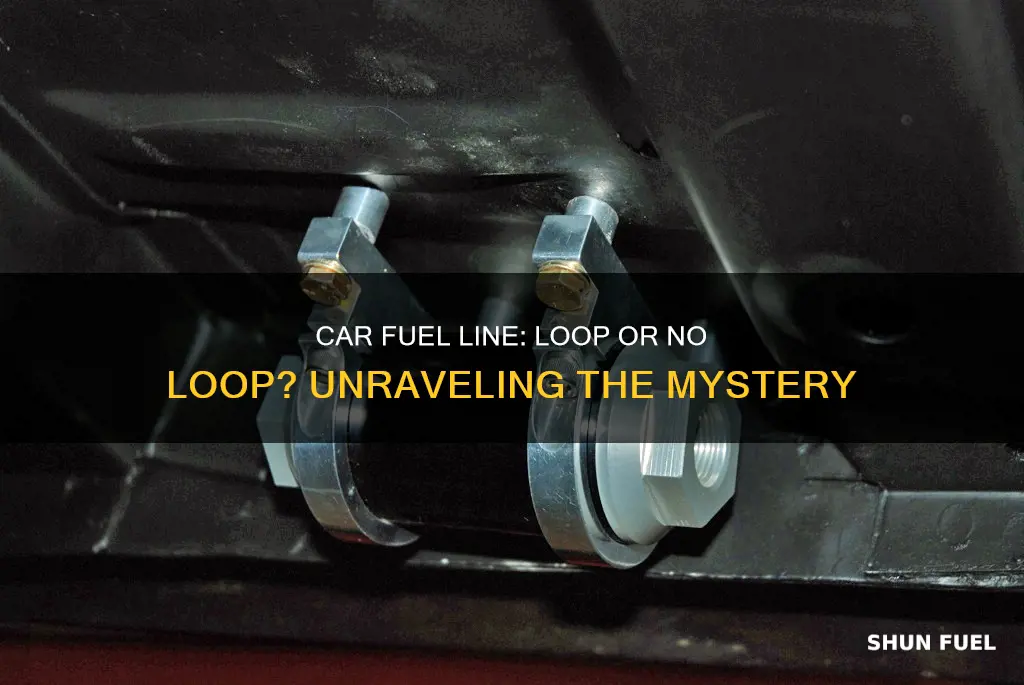
The fuel line on a car is a critical component that delivers fuel from the tank to the engine. One common question among car owners and mechanics is whether a fuel line needs a loop or a straight run. In this paragraph, we will explore the importance of loops in fuel lines and how they can impact the performance and safety of a vehicle. We will also discuss the potential risks of not having a loop and provide some guidelines on when and how to use loops in fuel lines.
Characteristics | Values |
---|---|
Loop Requirement | It is generally recommended to have a loop in the fuel line to prevent fuel from flowing back into the tank when the engine is off. This is especially important for vehicles with fuel injection systems. |
Fuel Line Material | The material used for the fuel line can impact the need for a loop. Flexible fuel lines may not require a loop, while rigid lines might need one to maintain a consistent path. |
Engine Type | Modern engines with electronic fuel injection often require a loop to ensure proper fuel delivery and prevent engine misfires. |
Fuel System Design | The design of the fuel system, including the location of the fuel pump and tank, can influence the need for a loop. |
Safety Considerations | Loops in fuel lines can provide an additional safety measure by allowing air to enter the system, which helps prevent fuel line collapse and ensures proper fuel flow. |
Regulations | Some regions may have specific regulations or recommendations regarding fuel line loops, especially for high-performance or racing vehicles. |
What You'll Learn
- Fuel Line Material: Different materials offer varying benefits and drawbacks for car fuel lines
- Loop Placement: The optimal location for a loop is critical to prevent fuel leaks
- Loop Size: Loops should be large enough to allow fuel flow but not overly large
- Loop Tension: Proper tensioning ensures the loop remains secure and functional
- Loop Inspection: Regular checks are essential to identify and fix potential issues
Fuel Line Material: Different materials offer varying benefits and drawbacks for car fuel lines
The choice of material for a car's fuel line is a critical aspect of vehicle maintenance, as it directly impacts the performance and longevity of the fuel system. Different materials offer unique advantages and disadvantages, and understanding these can help car owners make informed decisions when replacing or upgrading their fuel lines. Here's an overview of some common fuel line materials and their characteristics:
Rubber: Rubber fuel lines are a traditional and widely used choice. They are known for their flexibility, which allows them to accommodate the natural movement and expansion of the engine and fuel tank. Rubber is also resistant to most fuels, making it a suitable option for various vehicle types. However, one of the drawbacks is its susceptibility to cracking over time, especially in environments with extreme temperatures. Rubber fuel lines may also be more prone to leaks if damaged or worn.
Braided Steel: Braided steel fuel lines are renowned for their durability and strength. The steel core provides excellent resistance to fuel-related degradation and can withstand high pressure. This material is often used in high-performance vehicles or those with modified engines. While braided steel offers superior protection, it can be less flexible than rubber, making installation more challenging. Additionally, the material may be more susceptible to corrosion in certain environments.
Fluoropolymer (FEP): FEP is a synthetic material known for its exceptional resistance to chemicals and heat. It is often used in high-performance racing cars and vehicles that operate in harsh conditions. Fluoropolymer fuel lines offer excellent flexibility and can withstand extreme temperatures, making them a reliable choice. However, they are more expensive and less common in everyday vehicles due to their specialized application.
Copper: Copper fuel lines were popular in the past but have been largely replaced by other materials due to their higher cost and maintenance requirements. Copper is highly conductive, which can lead to issues with fuel vaporization and engine performance. It also requires careful installation to avoid damage, as it is relatively soft. Modern vehicles rarely use copper fuel lines, and its maintenance and installation complexities make it less practical.
When selecting a fuel line material, car owners should consider factors such as vehicle age, intended use, climate conditions, and the overall health of the fuel system. Each material has its own set of advantages and potential challenges, and consulting with automotive experts can provide valuable guidance in making the right choice.
Fuel Pressure Line: Can You Suck Through It?
You may want to see also
Loop Placement: The optimal location for a loop is critical to prevent fuel leaks
When it comes to fuel lines in a car, the placement of a loop is an essential consideration to ensure the safety and efficiency of the fuel system. The loop, also known as a fuel line loop or a fuel return line, is a crucial component that prevents fuel leaks and maintains optimal fuel pressure. Proper loop placement is critical, as it directly impacts the functionality and longevity of the fuel system.
The optimal location for the loop is typically near the fuel tank, just before the fuel pump. This placement ensures that the fuel returns to the tank efficiently, maintaining a consistent fuel level and pressure. By positioning the loop close to the tank, any potential leaks or spills are minimized, as the fuel is less likely to escape and cause contamination or damage. This strategic placement also allows for better control over the fuel flow, ensuring that the engine receives the required amount of fuel without wastage.
In the event of a fuel pump failure or a temporary shutdown, the loop plays a vital role in preventing fuel starvation. When the pump is not operational, the loop allows the fuel to return to the tank, ensuring that the system remains pressurized. This is particularly important during extended vehicle stops or when the engine is not running, as it prevents the fuel from settling and maintaining the overall health of the fuel system.
Furthermore, the loop's position near the fuel tank facilitates easy access during maintenance and repairs. This accessibility is crucial for mechanics and car enthusiasts who need to inspect or replace the fuel line components. Proper loop placement simplifies the process, reducing the time and effort required for maintenance, and ultimately contributing to the overall reliability of the vehicle.
In summary, the placement of a loop in a car's fuel line is a critical aspect of vehicle maintenance. By positioning the loop near the fuel tank, just before the pump, you ensure efficient fuel management, minimize leaks, and maintain optimal engine performance. This simple yet effective design feature is a testament to the importance of paying attention to even the smallest details in automotive engineering.
Fuel Line Flexibility: Adapting 1/4" to 5/8" Connections
You may want to see also
Loop Size: Loops should be large enough to allow fuel flow but not overly large
When considering the design of a fuel line for a vehicle, the inclusion of loops is an important aspect to ensure optimal performance and safety. The primary purpose of these loops is to prevent fuel line collapse and to facilitate smooth fuel flow. The size of these loops is a critical factor that can significantly impact the overall efficiency and reliability of the fuel system.
The loop size should be carefully calculated to strike a balance between allowing sufficient fuel flow and avoiding excessive loops that could lead to performance issues. A loop that is too small may restrict fuel flow, causing pressure drops and potential fuel starvation, especially during acceleration or when the engine demands higher fuel volumes. On the other hand, overly large loops can introduce unnecessary bends and twists, which might increase the risk of fuel line damage over time due to vibration and movement within the engine compartment.
An ideal loop should provide enough space for the fuel to flow freely while maintaining a smooth and direct path. This ensures that the fuel reaches the engine's intake system efficiently, promoting optimal combustion and engine performance. The loop's diameter and length should be determined based on the specific fuel flow requirements of the vehicle and the engine's design.
In practice, engineers often use a rule of thumb to determine the appropriate loop size. The general guideline is to make the loop large enough to accommodate the fuel flow rate, typically measured in gallons per minute (GPM), while keeping the loop's radius and length within a certain range. This range is usually defined by the manufacturer's specifications or industry standards to ensure compatibility with the vehicle's fuel system design.
In summary, the loop size in a car's fuel line is a critical design consideration. It should be large enough to facilitate smooth fuel flow without being overly large, which could lead to performance and safety issues. Finding the right balance ensures efficient fuel delivery to the engine, contributing to overall vehicle performance and reliability.
Can Fuel Lines Rust? Uncovering the Truth
You may want to see also
Loop Tension: Proper tensioning ensures the loop remains secure and functional
When it comes to car fuel lines, the concept of a 'loop' can be a bit confusing, as it's not a standard term used in automotive engineering. However, the idea of a loop might refer to a bend or a turn in the fuel line, which is a common design feature to ensure the line's flexibility and to prevent kinks or damage during installation and operation. Proper tensioning of these loops is crucial for the overall functionality and safety of the fuel system.
The primary purpose of a fuel line loop is to allow the line to move and adjust to the vehicle's various angles and vibrations during operation. This flexibility is essential to prevent the line from becoming damaged or dislodged, which could lead to fuel leaks or reduced performance. Loops are typically designed at specific intervals along the fuel line, ensuring that the line can expand and contract without putting excessive strain on the connections or the fuel pump.
To ensure proper tensioning, it's important to follow these steps:
- Identify the Loops: Locate the bends or loops in the fuel line. These are usually found where the line changes direction or where it connects to various components like the fuel tank, engine, or fuel pump.
- Check for Tightness: Ensure that each loop is tight enough to prevent the line from sagging or becoming loose. A loose loop can lead to fuel spillage and potential health hazards.
- Use the Right Tools: Utilize a tension gauge or a similar tool to measure the tension. The goal is to achieve a consistent and secure hold without causing damage to the fuel line.
- Consider the Environment: Take into account the vehicle's operating conditions. For example, in colder climates, the fuel line may need more tension to prevent freezing, while in warmer climates, it might require less tension to accommodate expansion.
- Regular Inspection: Periodically check the tension of the loops, especially after any maintenance or repairs. This ensures that the fuel line remains in optimal condition over time.
By paying close attention to loop tension, you can guarantee that the fuel line remains secure, functional, and capable of withstanding the various stresses it encounters during the vehicle's lifetime. Proper tensioning is a critical aspect of maintaining a safe and efficient fuel system, preventing potential issues that could arise from improper installation or neglect.
Can Black Iron Lines Carry Diesel Fuel? Unveiling the Truth
You may want to see also
Loop Inspection: Regular checks are essential to identify and fix potential issues
Loop inspection is a critical aspect of maintaining a vehicle's fuel system, ensuring optimal performance and safety. Regular checks are essential to identify and address potential issues that may arise with the fuel lines, especially when they are equipped with loops. These loops, often found in the fuel lines, serve a specific purpose and require careful examination to prevent problems.
The primary reason for inspecting these loops is to ensure the fuel lines are secure and free from damage. Over time, fuel lines can develop cracks or leaks due to various factors such as age, temperature changes, or physical stress. These issues can lead to fuel leaks, which are highly dangerous as they can result in fires or explosions. By regularly checking the loops, mechanics can identify any signs of wear and tear, corrosion, or damage, allowing for prompt repairs or replacements.
During the inspection, technicians should look for any visible signs of deterioration, such as rust, pitting, or discoloration. They should also feel for any soft spots or areas where the fuel line might be kinked or pinched. These loops are designed to provide flexibility and absorb minor vibrations, but excessive wear can compromise their functionality. It is crucial to ensure that the loops are not too tight, causing strain on the fuel line, or too loose, allowing for potential movement and damage.
Furthermore, loop inspection helps in maintaining proper fuel pressure. Loops can affect the fuel flow rate and pressure, which are critical for engine performance. If a loop is too tight, it may restrict fuel flow, leading to engine misfires or reduced power. Conversely, a loop that is too loose might cause fuel to stagnate, promoting the growth of harmful bacteria and leading to engine issues. Regular checks ensure that the loops are properly adjusted to maintain optimal fuel pressure and engine operation.
In summary, loop inspection is a vital part of fuel line maintenance. It allows mechanics to identify and rectify potential problems, ensuring the fuel system's integrity and the vehicle's overall performance. By regularly checking these loops, drivers can avoid costly repairs, enhance fuel efficiency, and most importantly, ensure their safety on the road. This simple yet effective practice should be a standard part of vehicle maintenance routines.
Hayabusa Fuel Line Removal: A Step-by-Step Guide for 2003 Models
You may want to see also
Frequently asked questions
A loop in the fuel line is an important safety feature designed to prevent fuel from being siphoned out of the tank. It creates a small air pocket in the line, which allows the engine to start and run efficiently. This loop also helps to maintain a consistent fuel pressure, ensuring optimal performance.
The loop is crucial because it prevents the formation of a vacuum in the fuel line when the engine is not running. Without the loop, fuel could be drawn out of the tank, leading to potential engine starvation and performance issues. The loop also helps to reduce the risk of fuel contamination and ensures a steady supply of fuel to the engine.
While it is technically possible to install a loop in a fuel line yourself, it is generally recommended to seek professional assistance. Fuel lines require precise installation to ensure a secure and leak-free connection. Automotive professionals have the necessary tools and expertise to ensure the loop is correctly positioned and secured, minimizing the risk of any potential issues.