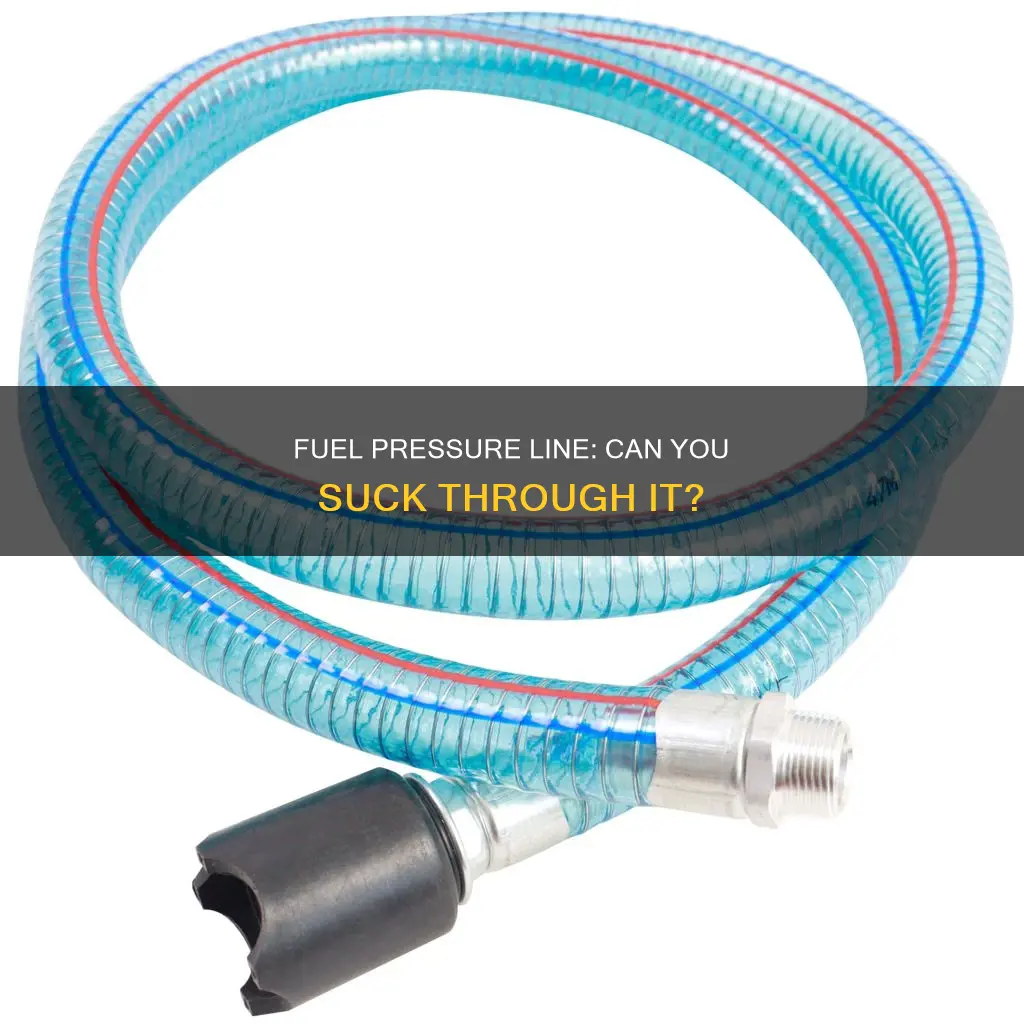
Are you able to suck through a fuel pressure line? This question might seem unusual, but it's a crucial aspect of understanding fuel systems in vehicles. The ability to create a vacuum or suction through a fuel pressure line is essential for ensuring proper fuel flow and delivery to the engine. This process is particularly important in older vehicles where the fuel system relies on atmospheric pressure to move fuel from the tank to the engine. Understanding the mechanics of this process can help in diagnosing and resolving issues related to fuel pressure and engine performance.
What You'll Learn
- Fuel Pressure Regulation: How fuel pressure is controlled and maintained in the system
- Line Design: The construction and materials used in fuel pressure lines
- Sucking Mechanism: The process of drawing fuel through the line using suction
- Line Integrity: Ensuring the line's structural integrity to prevent leaks
- Performance Testing: Methods to test the line's ability to handle suction and pressure
Fuel Pressure Regulation: How fuel pressure is controlled and maintained in the system
Fuel pressure regulation is a critical aspect of engine performance and efficiency, ensuring that the fuel system delivers the precise amount of fuel required for optimal combustion. This process involves maintaining a consistent and controlled fuel pressure within the engine's fuel system, which is essential for proper engine operation and longevity. The fuel pressure must be carefully managed to avoid issues such as excessive fuel consumption, engine misfires, and potential damage to the engine components.
In modern vehicles, fuel pressure is typically regulated by a fuel pressure regulator, an essential component in the fuel injection system. This regulator is designed to control and maintain the fuel pressure at a specific level, ensuring that the engine receives the correct amount of fuel. The regulator monitors the pressure and adjusts it accordingly to meet the engine's demands. When the engine is idling or running at low speeds, the fuel pressure regulator reduces the pressure to a lower level, allowing for better fuel economy. During high-speed or high-load conditions, the regulator increases the pressure to provide the engine with the necessary fuel for efficient operation.
The fuel pressure regulator operates based on a feedback control system. It continuously monitors the fuel pressure and makes adjustments to maintain the desired setpoint. This is achieved through a pressure-sensitive element, often a diaphragm or a piston, which moves in response to pressure changes. When the pressure deviates from the setpoint, the regulator's mechanism activates to either increase or decrease the pressure, ensuring stability. This dynamic regulation is crucial for adapting to varying engine loads and maintaining optimal performance.
In addition to the fuel pressure regulator, some systems employ a fuel pressure gauge, which provides real-time feedback to the driver. This gauge allows the driver to monitor the fuel pressure and ensure it remains within the specified range. By offering visual confirmation, the gauge helps in identifying potential issues or anomalies in the fuel pressure, enabling prompt maintenance or repair.
Proper fuel pressure regulation is vital for engine performance, fuel efficiency, and overall vehicle reliability. It ensures that the engine receives the correct fuel-air mixture, promoting efficient combustion and reducing emissions. Regular maintenance, including checking and replacing the fuel pressure regulator if necessary, is essential to guarantee consistent fuel pressure and optimal engine operation.
Replacing Fuel Lines on Poulan Chainsaw: A Step-by-Step Guide
You may want to see also
Line Design: The construction and materials used in fuel pressure lines
The design and construction of fuel pressure lines are critical components in any vehicle's fuel system, ensuring efficient and safe fuel delivery to the engine. These lines are designed to withstand high-pressure environments and maintain a consistent fuel supply, which is essential for optimal engine performance. The primary goal is to create a robust and reliable system that can handle the demands of the engine without compromising safety.
In terms of construction, fuel pressure lines are typically made from materials that offer a balance of strength, flexibility, and corrosion resistance. One of the most common materials used is high-density polyethylene (HDPE), known for its excellent chemical resistance and ability to withstand high-pressure conditions. HDPE is often reinforced with fibers to enhance its structural integrity, making it capable of withstanding the forces exerted by fuel pressure. The inner diameter of the line is carefully calculated to ensure minimal fuel loss and maintain a steady flow rate, which is crucial for engine operation.
The design of these lines often incorporates a series of bends and loops to reduce stress concentrations and prevent kinking, which could lead to fuel leaks or system failures. The bends are strategically placed to allow for expansion and contraction due to temperature changes, ensuring the line remains intact even in extreme conditions. Additionally, the lines may feature a protective outer layer or sheath made from materials like rubber or a specialized polymer blend to provide insulation and protect against external damage.
Another critical aspect of line design is the use of specialized fittings and connectors. These components are engineered to create a secure and leak-tight seal, ensuring that the fuel pressure is maintained throughout the system. Fittings made from materials like brass or stainless steel are commonly used due to their durability and ability to withstand high-pressure environments. The design of these fittings often includes O-rings or gaskets to create a tight seal, preventing any fuel from escaping.
Furthermore, the construction process involves precise manufacturing techniques to ensure consistency and quality. This includes the use of specialized machinery for welding and joining the various components, ensuring that the final product is free from defects. The lines are also subjected to rigorous testing, including pressure testing and fuel leakage checks, to ensure they meet the required standards and can safely operate under various conditions.
Evinrude 175 Fuel Line: Size Guide for 1986 Model
You may want to see also
Sucking Mechanism: The process of drawing fuel through the line using suction
The concept of using suction to draw fuel through a pressure line is an intriguing and practical approach to fuel management, especially in certain industrial and automotive applications. This method involves creating a vacuum or partial vacuum at the fuel source, which then pulls the fuel through the line, overcoming the natural flow due to pressure. Here's a detailed breakdown of the sucking mechanism:
When you initiate the suction process, the fuel pump, typically located within the fuel tank, activates. This pump is designed to create a low-pressure zone at the fuel inlet, which is usually located at the bottom of the tank. The pump's operation is crucial as it generates a vacuum, drawing air and fuel vapor into the tank. As the fuel vaporizes, it creates a mixture of fuel and air, which is then drawn through the pressure line. The pressure line acts as a conduit, allowing the fuel to travel from the tank to the engine or another fuel-consuming device.
The key to this mechanism is the pressure differential created by the pump. By generating a lower pressure at the fuel source compared to the surrounding atmosphere, the pump induces a flow of fuel. This process is similar to how a straw works when you suck on it; the air pressure inside your mouth becomes lower than the atmospheric pressure, causing the liquid to be drawn into your mouth. In the context of fuel transfer, the pump's role is to create this pressure difference, enabling the fuel to move through the line.
It's important to note that the efficiency of this sucking mechanism relies on several factors. The pump's capacity and the overall system design play a significant role in determining the success of the fuel transfer. Additionally, the pressure line's diameter and material can impact the flow rate and overall performance. Engineers and designers must carefully consider these elements to ensure optimal fuel delivery while minimizing potential issues like fuel degradation or contamination.
In summary, the sucking mechanism for drawing fuel through a pressure line is a fascinating process that utilizes suction to overcome natural pressure flow. By creating a low-pressure zone at the fuel source, the pump initiates a controlled transfer of fuel, ensuring a steady supply for various applications. Understanding this mechanism is essential for optimizing fuel management systems and can lead to innovative solutions in industries where efficient fuel handling is critical.
Mastering the Art of Chevy Truck Fuel Pump Line Removal
You may want to see also
Line Integrity: Ensuring the line's structural integrity to prevent leaks
The structural integrity of fuel lines is a critical aspect of vehicle maintenance, especially in preventing fuel leaks and ensuring optimal engine performance. When considering the ability to suck through a fuel pressure line, it's essential to understand the potential risks and the importance of line integrity. Fuel lines are designed to transmit fuel from the tank to the engine under pressure, and any compromise to their structure can lead to serious issues.
One of the primary concerns is the development of cracks or holes in the fuel line, which can occur due to various factors. Over time, fuel lines may experience wear and tear, especially in areas where they are more susceptible to damage, such as bends, joints, or where they are secured to the vehicle's body. These vulnerabilities can be exacerbated by factors like temperature fluctuations, vibration, and the presence of corrosive substances in the fuel. If a crack or hole forms, it creates a pathway for fuel to leak, which can have detrimental effects.
To ensure line integrity, regular inspections are vital. Visual inspections should be conducted to check for any visible signs of damage, such as cracks, corrosion, or kinks. It is also important to inspect the connections and fittings, ensuring they are tight and secure. Over time, fuel lines may become brittle, especially in older vehicles, so checking for any signs of brittleness or cracking is essential. In addition to visual inspections, pressure testing can be employed to identify potential issues. By applying pressure to the fuel system, any weak points or leaks can be detected, allowing for prompt repairs or replacements.
Another critical aspect of line integrity is the use of high-quality materials and proper installation techniques. Fuel lines should be made from materials that can withstand the corrosive nature of fuel and the mechanical stresses they endure. Modern vehicles often utilize synthetic rubber or specialized polymers for fuel lines, which offer improved durability and resistance to fuel degradation. Proper installation ensures that the lines are routed correctly, securely fastened, and free from sharp bends that could compromise their integrity.
In summary, maintaining the structural integrity of fuel lines is essential for preventing leaks and ensuring the safe operation of vehicles. Regular inspections, including visual checks and pressure testing, are key to identifying potential issues. Additionally, using high-quality materials and following proper installation procedures contribute to the overall reliability of the fuel system. By prioritizing line integrity, vehicle owners can minimize the risk of fuel leaks and maintain optimal engine performance.
Unveiling the Material Secrets of Micro Fuel Lines
You may want to see also
Performance Testing: Methods to test the line's ability to handle suction and pressure
The performance testing of fuel pressure lines is a critical aspect of ensuring the reliability and safety of fuel systems in vehicles. These lines are designed to transport fuel from the tank to the engine, and their ability to handle suction and pressure is essential for efficient and safe operation. Here's an overview of the methods used to test and evaluate the performance of these lines:
Suction Testing:
Suction testing is a fundamental process to assess the line's ability to draw fuel under negative pressure. This test involves creating a vacuum or suction on one end of the fuel line while monitoring the flow rate and pressure. The goal is to determine the line's capacity to handle suction and prevent fuel vaporization or air intrusion. During this test, technicians use specialized equipment to measure the line's performance, including flow meters and pressure gauges. They may simulate different suction levels to evaluate the line's response and ensure it meets the required specifications.
Pressure Testing:
Pressure testing is another crucial method to evaluate the integrity and functionality of fuel pressure lines. This test involves applying pressure to the line and measuring its response. Technicians use pressure gauges and pumps to gradually increase the pressure on the line and observe how it behaves. The test aims to identify any leaks, blockages, or weaknesses in the line's structure. By subjecting the line to various pressure levels, engineers can ensure it can withstand the demands of the fuel system, including high-pressure fuel pumps and engine requirements.
Flow Rate Measurement:
Measuring the flow rate is an essential part of performance testing. It involves monitoring the volume of fuel passing through the line per unit of time. Technicians use specialized flow meters to calculate the flow rate under different conditions, such as varying suction and pressure. This data helps in understanding the line's efficiency and identifying any restrictions or bottlenecks that might affect fuel delivery.
Leak Detection:
A critical aspect of performance testing is leak detection. Technicians use specialized equipment to identify any leaks in the fuel pressure lines. This can be done by applying a soapy water solution or using electronic leak detection tools. By simulating real-world conditions, engineers can ensure that the lines are free from leaks, which could lead to fuel loss, engine misfires, or even dangerous situations.
Durability and Longevity Testing:
Long-term performance is also evaluated through durability testing. This involves subjecting the fuel pressure lines to extreme conditions, simulating real-world usage over an extended period. By exposing the lines to temperature variations, vibrations, and other environmental factors, engineers can assess their longevity and resistance to degradation. This testing ensures that the lines can withstand the rigors of daily use and maintain their performance over time.
These performance testing methods are essential to guarantee that fuel pressure lines function optimally, providing efficient fuel delivery while maintaining the safety and reliability of the vehicle's fuel system. Each test provides valuable insights into the line's behavior, allowing engineers to make necessary adjustments or improvements to meet the required standards.
Air in Fuel Lines: Will Your Pump Fail?
You may want to see also
Frequently asked questions
A fuel pressure line is a crucial component in a vehicle's fuel system, responsible for delivering the correct amount of fuel pressure to the engine. It ensures that the engine receives the optimal fuel-air mixture for efficient combustion.
The fuel pressure line is connected to a fuel pump, which creates pressure to push fuel through the line. This pressure is regulated by a fuel pressure regulator to maintain the desired pressure at the engine's fuel injectors or carburetor.
Yes, it is possible for a fuel pressure line to be "sucked through" due to a vacuum or low pressure. This can occur if there is a leak in the system, a faulty fuel pump, or a problem with the fuel pressure regulator, causing a drop in pressure.
Common signs of a failing fuel pressure line include engine misfires, reduced power, poor fuel economy, and the engine may stall or have difficulty starting. If you notice any of these symptoms, it's essential to inspect the fuel pressure line for any damage or leaks.
Regular maintenance and inspections are key to preventing issues with the fuel pressure line. Check for any signs of corrosion, damage, or leaks. Ensure the fuel pump is working properly and that the fuel pressure is within the recommended range. If in doubt, consult a professional mechanic for a thorough inspection.