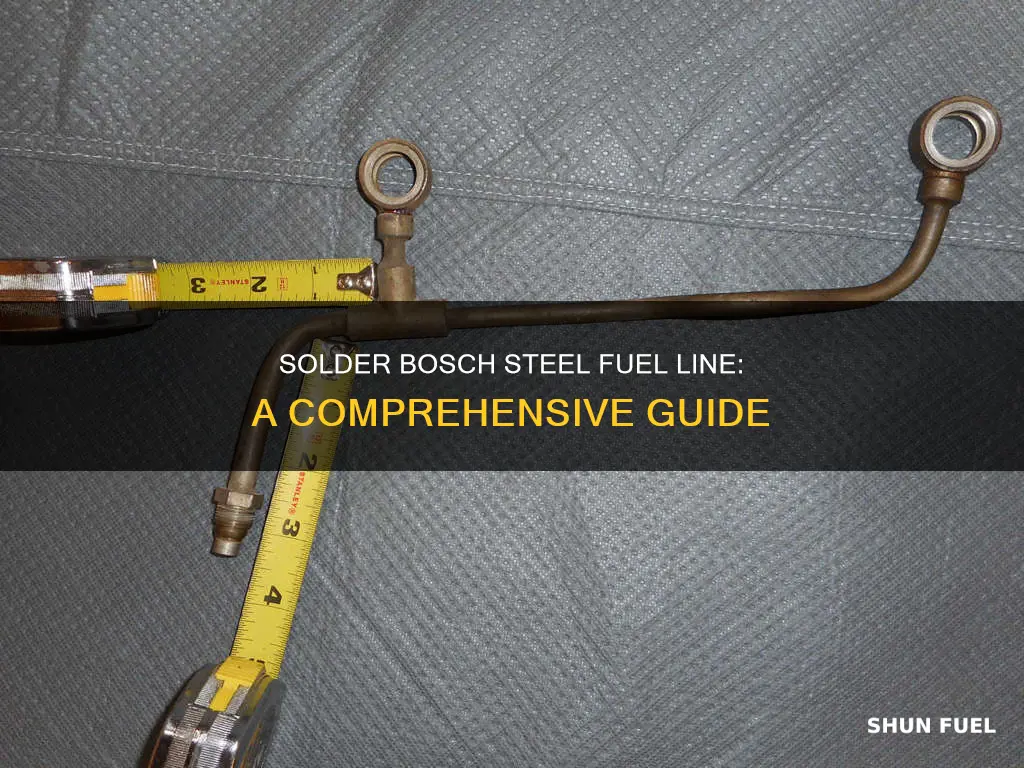
Soldered connections are a common method for joining fuel lines in vehicles, but it's important to consider the specific materials used. When it comes to Bosch steel fuel lines, soldering can be a viable option, but it requires careful preparation and the right materials. This introduction will explore the feasibility of soldering Bosch steel fuel lines, discussing the necessary steps, potential challenges, and best practices to ensure a secure and reliable connection.
Characteristics | Values |
---|---|
Material | Steel |
Brand | Bosch |
Purpose | Fuel Line |
Soldering | Not recommended |
Compatibility | Specific to Bosch systems |
Durability | High, suitable for high-pressure fuel systems |
Temperature Resistance | Varies, typically suitable for engine operation temperatures |
Flexibility | Moderate, can be bent to some extent |
Corrosion Resistance | Good, suitable for long-term use |
Installation | Requires specialized tools and techniques |
Safety | Not suitable for DIY repairs, professional installation advised |
What You'll Learn
- Safety Gear: Wear protective gear like gloves and goggles to avoid burns and chemical exposure
- Fuel Line Material: Ensure the fuel line is compatible with Bosch steel and has the correct diameter
- Soldering Tools: Gather necessary tools: flux, solder, heat shrink, and a soldering iron
- Preparation: Clean and prepare the fuel line and connection points for optimal solder flow
- Temperature Control: Use a controlled heat source to avoid overheating and damaging the fuel line
Safety Gear: Wear protective gear like gloves and goggles to avoid burns and chemical exposure
When working with soldering, especially for a potentially hazardous task like soldering a steel fuel line, it is crucial to prioritize safety. One of the most important safety measures is to wear appropriate protective gear. This includes gloves and goggles, which are essential to safeguard your hands and eyes from potential hazards.
Gloves are a critical component of your safety gear. They provide a barrier between your skin and the soldering process, which involves high temperatures and potentially harmful chemicals. Heat-resistant gloves made from materials like leather or specialized synthetic fabrics can withstand the extreme temperatures generated by soldering irons. These gloves will protect your hands from burns and potential chemical exposure from the soldering flux and solder itself. Look for gloves that offer a comfortable fit and allow for dexterity, ensuring you can still manipulate the fuel line and soldering tools with ease.
Goggles are equally important to protect your eyes from potential hazards. Soldering can release fumes and splashes that may contain harmful substances. These fumes can be particularly dangerous if inhaled, and any splashes or spills could cause eye irritation or damage. Wear safety goggles that provide a secure fit and full coverage to ensure your eyes are completely protected. Look for goggles with a comfortable design and a strap to keep them in place, ensuring they don't slip off during the soldering process.
In addition to gloves and goggles, consider other protective measures such as a respirator to protect your lungs from inhaling fumes, and heat-resistant aprons or clothing to shield your body from potential burns. It is also essential to work in a well-ventilated area or outdoors to ensure proper airflow and reduce the risk of inhaling harmful fumes.
Remember, taking the time to put on the right safety gear is a small price to pay for the protection it offers. It ensures that you can tackle the task of soldering a Bosch steel fuel line safely and effectively, minimizing the risk of injury or long-term health issues associated with exposure to heat and chemicals. Always prioritize safety and be aware of the potential risks involved in any DIY project.
Diagnosing Fuel Line Issues: A Step-by-Step Guide for Old Car Owners
You may want to see also
Fuel Line Material: Ensure the fuel line is compatible with Bosch steel and has the correct diameter
When working with Bosch steel fuel lines, it's crucial to choose the right material for the fuel line to ensure compatibility and optimal performance. The fuel line should be specifically designed to withstand the unique properties of Bosch steel, including its strength and resistance to corrosion. One of the key considerations is the diameter of the fuel line. The correct diameter is essential to maintain the necessary flow rate of fuel to the engine while also ensuring a secure connection.
Incompatible fuel lines may not have the same level of flexibility or durability as the Bosch steel, leading to potential issues over time. Using a fuel line with an incorrect diameter can result in restricted fuel flow, which can cause engine performance problems such as reduced power, poor acceleration, and even engine stall. Therefore, it is imperative to select a fuel line that matches the Bosch steel's specifications.
To ensure compatibility, consult the vehicle's manual or seek guidance from automotive experts. They can provide specific recommendations for fuel line materials and diameters that are compatible with Bosch steel. It is also advisable to use high-quality fuel line materials that are designed for fuel applications, as these will offer superior resistance to fuel degradation and ensure a longer lifespan.
When purchasing a fuel line, look for products that are explicitly labeled as compatible with Bosch steel or made from materials known to work well with this type of steel. Some common materials used for fuel lines include high-temperature rubber, silicone, or specialized fuel-resistant plastics. These materials are chosen for their ability to withstand the corrosive nature of fuel and the high temperatures it can reach.
In summary, when dealing with Bosch steel fuel lines, the choice of material and diameter is critical. Using the correct fuel line ensures compatibility, maintains optimal engine performance, and provides a secure connection. Always refer to vehicle manuals or consult experts to make informed decisions when selecting fuel line materials to guarantee the longevity and reliability of your fuel system.
Mastering the Art of Small Engine Fuel Line Removal: A Step-by-Step Guide
You may want to see also
Soldering Tools: Gather necessary tools: flux, solder, heat shrink, and a soldering iron
Before attempting to solder a Bosch steel fuel line, it's crucial to gather the right tools to ensure a successful and secure connection. Soldering is a precise process that requires specific materials and equipment to create a strong bond between the fuel line and the fitting. Here's a detailed guide on the essential tools you'll need:
Flux: Flux is a crucial component in the soldering process, especially when working with steel. It serves multiple purposes: it removes oxidation from the metal surface, prevents the formation of an oxide layer during soldering, and acts as a lubricant, making it easier to apply the solder. For steel fuel lines, a non-corrosive flux is ideal to avoid any potential damage to the metal. You can find flux specifically designed for steel soldering in hardware stores or online.
Solder: Solder is a metal alloy that melts at a lower temperature than the base metal (in this case, steel). It creates a strong bond when it cools, forming a joint that is often stronger than the original metal. Bosch steel fuel lines typically require a lead-free solder, which is safer and more durable. Look for a solder with a suitable melting point for your application; the packaging will usually provide this information.
Heat Shrink: Heat shrink tubing is an essential accessory for soldering. It provides insulation and protection to the soldered joint, ensuring it remains secure and sealed. After soldering, apply heat shrink over the joint to encapsulate it, which will then shrink tightly around the fuel line when heated, creating a reliable barrier against fuel leaks.
Soldering Iron: The heart of the soldering process is a soldering iron, a tool that applies heat to melt the solder. It should have a fine, controlled tip to allow for precise work. When choosing a soldering iron, consider the wattage; a higher wattage provides faster heating, which is beneficial for larger projects. Additionally, ensure the iron has a temperature control setting to allow you to adjust the heat for different materials.
Having these tools ready will enable you to tackle the soldering task with confidence. Remember, proper preparation and the right materials are key to a successful repair or modification of your Bosch steel fuel line.
Blue Uerathyane Fuel Line: Safe for Ethanol Gasoline?
You may want to see also
Preparation: Clean and prepare the fuel line and connection points for optimal solder flow
Before attempting to solder a Bosch steel fuel line, proper preparation is crucial to ensure a successful and reliable connection. Start by gathering the necessary tools and materials, including a fuel line cleaner, a wire brush, a sandpaper block, a flux compound, and a suitable solder. Bosch steel fuel lines are known for their durability, but they still require careful handling and preparation to ensure a strong bond.
The first step in the preparation process is to clean the fuel line and connection points thoroughly. Over time, fuel lines can accumulate dirt, grease, and corrosion, which can interfere with the soldering process. Use a fuel line cleaner specifically designed for this purpose, following the manufacturer's instructions. Apply the cleaner to the entire length of the fuel line, ensuring that it reaches all areas where the line connects to other components. Allow the cleaner to work for the recommended time, which typically involves a few minutes of contact with the surface.
After cleaning, it's essential to remove any remaining contaminants. Use a wire brush to scrub the fuel line and connection points, ensuring that you reach all the nooks and crannies. This step helps to create a rough surface, providing better adhesion for the solder. If there are any stubborn deposits or corrosion, gently sand the affected areas using a fine-grit sandpaper block. Take care not to apply too much pressure to avoid damaging the fuel line.
Once the fuel line and connections are clean and brushed, inspect the surface for any remaining contaminants. If you notice any residue or oxidation, repeat the cleaning process until the surface is free from debris. Proper preparation at this stage is vital, as it ensures that the solder will flow smoothly and create a strong bond.
Additionally, consider applying a small amount of flux to the connection points. Flux acts as a lubricant and helps to remove any remaining oxides, allowing the solder to make direct contact with the metal. Apply the flux carefully, ensuring it doesn't come into contact with the fuel, as it can contaminate the system. This step is especially important when dealing with Bosch steel, as it can be sensitive to oxidation. With the fuel line and connections now prepared, you are ready for the next stage of the soldering process, confident that your preparation has set the foundation for a successful repair or modification.
An6 Fuel Line Compatibility: 1997 Ford F150 Upgrade Guide
You may want to see also
Temperature Control: Use a controlled heat source to avoid overheating and damaging the fuel line
When working with fuel lines, especially those made of steel, temperature control is crucial to ensure the integrity and functionality of the system. Soldering a Bosch steel fuel line requires precision and care to prevent any potential damage. Here's a detailed guide on how to achieve this:
Understanding the Importance of Temperature Control:
Solder joints in fuel lines must be strong and reliable to withstand the pressure and temperature variations within the engine. Overheating can lead to several issues, including the melting of the solder or the base metal, which can result in a weak joint or even a complete failure. Bosch steel fuel lines are known for their durability, but improper soldering techniques can compromise their integrity.
Using a Controlled Heat Source:
The key to successful soldering is to employ a controlled heat source. A soldering iron or gun is the primary tool for this task. Here's how to use it effectively:
- Select a soldering iron with a temperature-controlled setting. Aim for a temperature range suitable for the type of solder you are using. For Bosch steel fuel lines, a temperature between 300°C and 400°C (572°F to 752°F) is generally recommended.
- Apply a small amount of flux to the fuel line connection. Flux helps to clean the surfaces and promote better solder flow. Ensure the flux is compatible with the materials used.
- Heat the soldering iron to the desired temperature and then touch the tip to the fuel line, applying heat directly to the joint. Hold the iron for a few seconds, allowing the heat to melt the solder and create a bond.
- Keep the heat source in contact with the joint for the recommended duration, ensuring the solder melts and forms a strong connection.
- Remove the iron and allow the joint to cool slightly before handling the fuel line.
Tips for Precision:
- Always use a steady hand and a controlled application of heat. Avoid overheating the fuel line or the surrounding areas.
- Practice on a small section of the fuel line before soldering the main connection to get a feel for the process.
- Ensure the fuel line is clean and free of any debris or contaminants before soldering.
- Consider using a heat shield or a temporary clamp to protect the fuel line from excessive heat during the soldering process.
By maintaining precise temperature control, you can ensure a successful solder joint on your Bosch steel fuel line, ensuring optimal performance and longevity. Remember, practice and attention to detail are essential when working with fuel systems.
Dodge Dakota Fuel Line Location: A Comprehensive Guide
You may want to see also
Frequently asked questions
Yes, you can use a soldering iron to repair a Bosch steel fuel line. However, it's important to note that soldering is not a recommended method for fuel lines due to the potential health risks associated with fuel exposure. If you choose to solder, ensure you follow safety guidelines and use a suitable flux and solder designed for fuel line applications.
Before soldering, thoroughly clean the fuel line to remove any contaminants. Use a degreaser or a mild acid solution to ensure a clean and dry surface. Rinse the line thoroughly and allow it to dry completely before attempting to solder.
When soldering Bosch steel fuel lines, it's crucial to use a low-temperature solder to avoid damaging the line. Apply a thin layer of flux to the joint and heat it gently with a soldering iron. Ensure the solder melts and forms a strong bond without overheating the surrounding areas. Practice precision and take your time to achieve a secure connection.