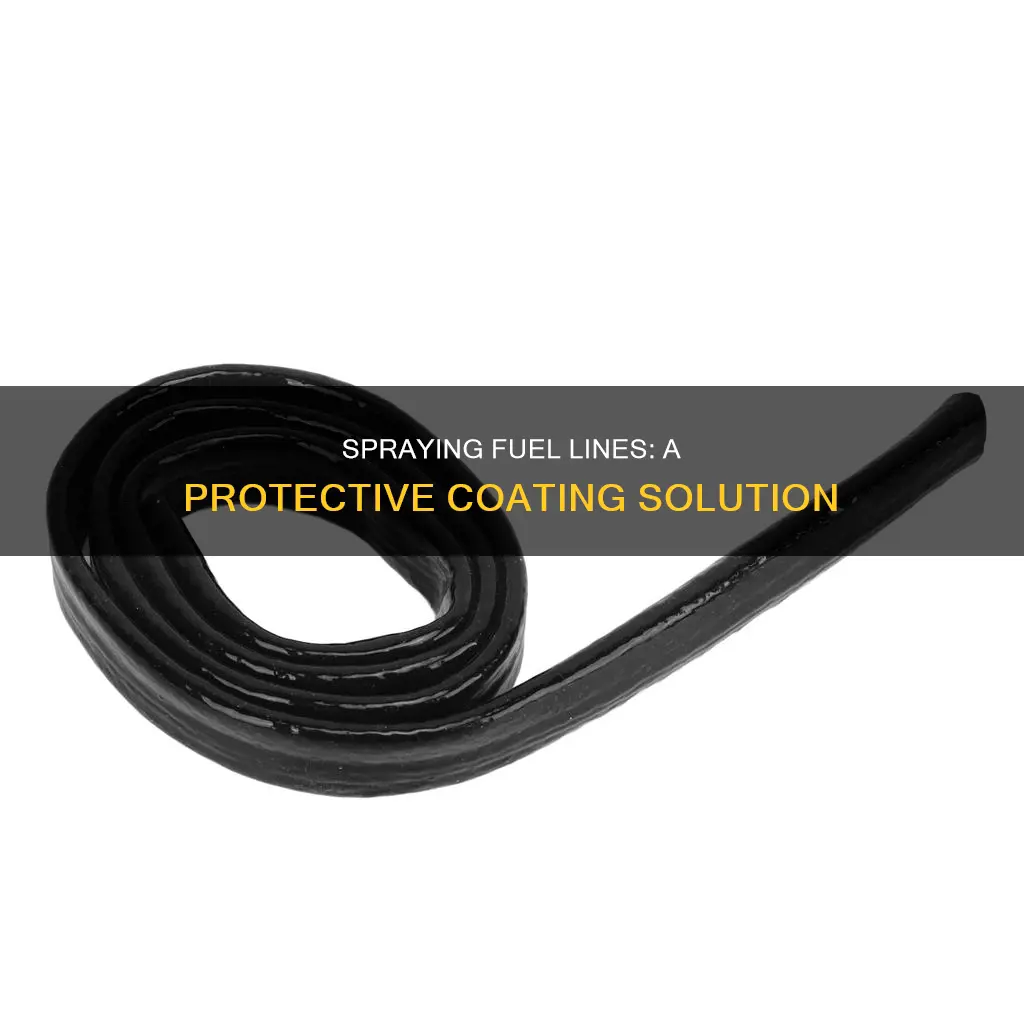
When it comes to maintaining and extending the lifespan of fuel lines in vehicles, one effective method is the application of protective coatings. This technique involves spraying a specialized coating material onto the fuel lines, creating a barrier that shields against wear and tear, corrosion, and other potential issues. By doing so, the fuel lines can be protected from the elements, ensuring optimal performance and longevity. This practice is particularly useful for vehicles that operate in harsh environments or those with frequent exposure to extreme temperatures and moisture. The protective coating acts as a safeguard, allowing fuel lines to maintain their integrity and functionality over time.
Characteristics | Values |
---|---|
Effectiveness | Can provide a protective layer against corrosion, oxidation, and fuel degradation. |
Application | Spraying a protective coating on fuel lines is a common practice in automotive maintenance. |
Materials | Various coatings are available, including polyurea, polyurethane, and epoxy-based sprays. |
Benefits | Reduces the risk of fuel leaks, improves fuel efficiency, and extends the lifespan of fuel lines. |
Considerations | Ensure the coating is compatible with the fuel type and line material. Some coatings may require specific application techniques. |
DIY vs. Professional | Can be done by DIY enthusiasts, but professional installation might be recommended for complex systems. |
Frequency | Periodic maintenance, especially after a certain mileage or age, is advised. |
Cost | Costs vary depending on the product and application method. |
Environmental Impact | Some coatings may have environmental concerns, so choose eco-friendly options if necessary. |
What You'll Learn
- Fuel Line Coating Materials: Identify suitable protective coatings for fuel lines
- Spray Application Techniques: Learn optimal methods for applying protective coatings
- Safety Precautions: Understand safety measures when using fuel line coatings
- Environmental Impact: Assess the environmental effects of fuel line coatings
- Longevity and Maintenance: Explore how coatings enhance fuel line longevity and maintenance
Fuel Line Coating Materials: Identify suitable protective coatings for fuel lines
When it comes to protecting fuel lines, the choice of coating material is crucial to ensure the longevity and reliability of the fuel system. Fuel lines are susceptible to various forms of degradation, including corrosion, fuel contamination, and mechanical damage, which can lead to costly repairs or system failures. Therefore, selecting the right protective coating is essential for maintaining the integrity of the fuel lines.
One of the most commonly used coating materials for fuel lines is a specialized epoxy-based paint. This type of coating is known for its excellent adhesion properties, providing a robust barrier between the fuel line and the surrounding environment. Epoxy coatings are highly resistant to corrosion, especially in the presence of fuel vapors and moisture, making them ideal for fuel system applications. The paint is typically applied in multiple thin layers to ensure complete coverage and a smooth finish, which is essential for maintaining the flexibility and durability of the fuel lines.
Another effective coating material is a zinc-rich primer followed by a polyurea topcoat. This combination offers superior corrosion resistance, especially in harsh environments. The zinc-rich primer acts as a sacrificial layer, protecting the fuel line from rust and corrosion, while the polyurea topcoat provides an additional layer of defense against fuel contamination and mechanical stress. This two-step process ensures a robust and long-lasting protective barrier.
For fuel lines exposed to high temperatures, a heat-resistant coating is necessary. Silicone-based coatings are an excellent choice for these applications, as they can withstand elevated temperatures without compromising their protective properties. These coatings are flexible and can accommodate slight movements, ensuring that the fuel lines remain protected even in dynamic environments. Additionally, silicone coatings are resistant to fuel evaporation and can help prevent fuel line deterioration over time.
In some cases, a combination of different coating materials may be employed to address specific concerns. For instance, a fuel line might benefit from a zinc-rich primer for corrosion protection, followed by a polyurea topcoat for additional resistance to fuel contamination. This layered approach ensures comprehensive protection against multiple potential issues. It is important to consider the specific operating conditions and the unique challenges of each fuel line installation when selecting the appropriate coating materials.
Fixing Fuel Line Rust: A Step-by-Step Guide to Prevent Engine Issues
You may want to see also
Spray Application Techniques: Learn optimal methods for applying protective coatings
Spray application is a highly effective method for applying protective coatings to fuel lines, offering a precise and efficient way to ensure optimal coverage. This technique is particularly useful for hard-to-reach areas and intricate fuel line configurations. The process involves using specialized equipment, such as an airbrush or a high-pressure spray gun, to deliver a fine mist of the protective coating material. This method allows for excellent control over the application, ensuring an even and consistent layer of protection.
When preparing for the spray application, it is crucial to ensure the fuel lines are clean and free of any contaminants. Start by disconnecting the fuel lines from the vehicle's system and allowing them to drain completely. Use a suitable degreaser or cleaner to remove any built-up grime, ensuring a clean surface for the coating. Rinse the lines thoroughly to eliminate any residue, and then allow them to dry completely before proceeding.
The choice of spray equipment is essential for achieving the best results. Airbrushes are ideal for small, intricate fuel lines, providing a very fine spray pattern that allows for precise application. High-pressure spray guns, on the other hand, are more powerful and can handle larger areas, making them suitable for bulk fuel lines. The key is to select a gun or airbrush that provides the right balance of pressure and spray pattern for the specific fuel line dimensions and coating material.
The application process begins with a light mist of the protective coating, ensuring an even coverage. Start at one end of the fuel line and work your way along, maintaining a consistent distance from the line to ensure uniform application. For hard-to-reach areas, you may need to disassemble the line further to gain better access. Take your time and be meticulous, as this will result in a more effective and long-lasting protection.
After the initial spray, allow the coating to cure according to the manufacturer's instructions. This may involve waiting for a specified period or using heat to accelerate the curing process. Once cured, inspect the fuel lines for any missed spots or uneven areas and apply additional coats as needed. This multi-coat process ensures maximum protection and can be especially beneficial for high-wear areas. Properly applied spray coatings can significantly extend the life of fuel lines and provide an additional layer of defense against corrosion and fuel-related degradation.
Mastering the Art of Stretching Nylon Fuel Lines: A Comprehensive Guide
You may want to see also
Safety Precautions: Understand safety measures when using fuel line coatings
When considering the application of protective coatings to fuel lines, it is crucial to prioritize safety to ensure the process is carried out effectively and without risk. Here are some essential safety precautions to keep in mind:
Ventilation and Respiratory Protection: Fuel line coatings often contain volatile organic compounds (VOCs) and other chemicals that can release fumes. Working in a well-ventilated area is imperative to minimize the inhalation of these fumes. If working indoors, ensure proper ventilation by opening windows and using exhaust fans. Consider wearing a respirator mask designed for organic vapor protection to further safeguard against inhaling harmful substances.
Personal Protective Equipment (PPE): Always wear appropriate PPE to protect your skin and eyes. This may include gloves, safety goggles, or a full-face shield to prevent direct contact with chemicals and potential splashes. Long-sleeved clothing and closed-toe shoes can also reduce the risk of skin irritation and chemical exposure.
Fire Safety: Fuel lines, when coated, can become flammable. It is essential to follow fire safety protocols. Keep the work area clear of open flames, sparks, or any potential ignition sources. Ensure that any heat sources used during the application process, such as heat guns or torches, are kept at a safe distance to avoid igniting the coating material. Have a fire extinguisher readily available, preferably rated for use on flammable materials.
Training and Instruction: Before starting the coating process, ensure that all personnel involved are properly trained and instructed. Provide clear guidelines on the correct application techniques, including the recommended spray patterns and distances to maintain safety. Training should also cover emergency response procedures in case of accidental exposure or ingestion.
Disposal and Waste Management: Proper disposal of used coating materials and waste is critical. Follow local regulations for the disposal of hazardous substances. Avoid disposing of used coatings in regular trash bins, as they may contain harmful chemicals. Consider using approved waste containers and seek guidance from waste management experts if needed.
By adhering to these safety precautions, you can create a secure environment when applying protective coatings to fuel lines, ensuring the well-being of both the workers and the surrounding ecosystem. It is always better to be cautious and prepared when dealing with potentially hazardous materials.
Bundy Fuel Line Connector: A Comprehensive Guide
You may want to see also
Environmental Impact: Assess the environmental effects of fuel line coatings
The environmental implications of fuel line coatings are an important consideration in the automotive and industrial sectors, especially as the focus on sustainability and eco-friendly practices intensifies. When assessing the impact of these coatings, it is crucial to examine both the benefits and potential drawbacks to ensure responsible use.
One of the primary advantages of applying protective coatings to fuel lines is the prevention of fuel leaks and spills. Fuel lines can deteriorate over time due to various factors, including heat, vibration, and chemical exposure. This degradation can lead to fuel leaks, which not only pose a fire hazard but also contribute to soil and water contamination. By using specialized coatings, the risk of leaks is significantly reduced, thereby minimizing the environmental impact of fuel spills. These coatings create a protective barrier that safeguards the fuel lines, ensuring the fuel remains contained and does not come into contact with the surrounding environment.
However, the environmental impact of fuel line coatings also extends to the choice of materials used in the coating process. Some traditional coatings may contain volatile organic compounds (VOCs), which are known to contribute to air pollution and have adverse effects on human health. The application of such coatings in enclosed spaces or areas with poor ventilation can lead to increased VOC emissions, potentially causing respiratory issues and other health problems for workers and nearby residents. Therefore, it is essential to choose coatings that are low in VOCs or even VOC-free to mitigate these health risks and reduce air pollution.
Furthermore, the disposal of used or spent fuel line coatings should be carefully managed to avoid environmental contamination. If not handled properly, the chemicals and solvents used in these coatings could leach into the soil and groundwater, leading to long-term ecological damage. Manufacturers and users should adhere to local regulations regarding the disposal of hazardous materials, ensuring that spent coatings are treated or recycled appropriately. This includes the use of specialized waste management systems and the implementation of safe disposal practices to prevent environmental degradation.
In summary, while fuel line coatings offer significant benefits in terms of preventing fuel leaks and extending the lifespan of fuel lines, the environmental impact should not be overlooked. The choice of coating materials, proper application techniques, and responsible disposal methods are all critical factors in minimizing the ecological footprint of these coatings. By addressing these aspects, the automotive and industrial sectors can contribute to a more sustainable approach to fuel line maintenance and protection.
Poulan Pro's Unique Fuel Line: Unlocking the Mystery
You may want to see also
Longevity and Maintenance: Explore how coatings enhance fuel line longevity and maintenance
The application of protective coatings to fuel lines is a valuable practice that significantly contributes to the longevity and maintenance of automotive systems. Fuel lines, being susceptible to wear and tear, benefit greatly from this preventative measure. Over time, fuel lines can degrade due to factors such as fuel contamination, heat, and mechanical stress, leading to potential performance issues and safety concerns. This is where protective coatings come into play, offering a layer of defense against these detrimental factors.
Coatings, when applied to fuel lines, create a barrier that shields the inner components from direct exposure to harsh elements. This protective layer can be made from various materials, each chosen for its specific properties to combat different challenges. For instance, some coatings are designed to resist fuel contamination, ensuring that the fuel remains clean and free from debris that could cause blockages or damage to the engine. Other coatings might focus on heat resistance, safeguarding the fuel lines from extreme temperatures that could lead to material degradation.
The process of applying these coatings is a precise and detailed procedure. It often involves cleaning the fuel lines to ensure a proper bond between the coating and the surface. This cleaning process might include the use of specialized solvents or brushes to remove any contaminants. Once prepared, the fuel lines are then coated using specialized equipment, ensuring an even and consistent layer of protection. This process is particularly useful in high-performance vehicles or those operating in harsh environments, where the fuel system is under constant stress.
The benefits of this maintenance practice are twofold. Firstly, it extends the lifespan of the fuel lines, reducing the likelihood of premature failure. This is especially crucial in vehicles where fuel lines are subject to constant vibration and movement, making them prone to damage. Secondly, it simplifies maintenance by minimizing the risk of fuel leaks, which can be costly and dangerous to repair. By keeping the fuel lines in optimal condition, the overall performance and reliability of the vehicle are improved, ensuring a smoother and safer driving experience.
In summary, the application of protective coatings to fuel lines is a practical and effective method to enhance their longevity and maintenance. It provides a simple yet powerful solution to common automotive challenges, ensuring that fuel lines remain in top condition. With proper application and care, this technique can significantly contribute to the overall health and longevity of a vehicle's fuel system.
Fuel Line Removal: A Guide for 87 Crown Victoria Owners
You may want to see also
Frequently asked questions
Yes, using spray-on protective coatings specifically designed for fuel lines is generally safe and effective. These coatings are formulated to withstand the harsh conditions of fuel systems, including heat, pressure, and chemical resistance.
The frequency of reapplication depends on various factors, such as the type of fuel used, operating conditions, and the specific coating product. As a general guideline, it is recommended to reapply the coating every 6 to 12 months or as per the manufacturer's instructions. Regular maintenance ensures optimal protection against fuel line degradation.
It's crucial to use products specifically designed for fuel line protection. These coatings are engineered to adhere well to fuel lines, provide insulation, and offer long-lasting protection. Look for coatings labeled as fuel-line protectants or fuel-line sealants, and always follow the manufacturer's guidelines for application.
While protective coatings can significantly reduce the risk of fuel line leaks, they are not a guaranteed solution. The coating helps prevent damage from corrosion and fuel degradation, but other factors like line wear, connections, and quality of installation also play a role. Regular inspections and maintenance are essential to identify and address potential leak sources.
Some spray-on fuel line coatings may contain volatile organic compounds (VOCs), which can have environmental implications. It is advisable to choose low-VOC or VOC-free products to minimize air pollution and ensure compliance with local regulations. Always read the product labels and consider the environmental impact during application.