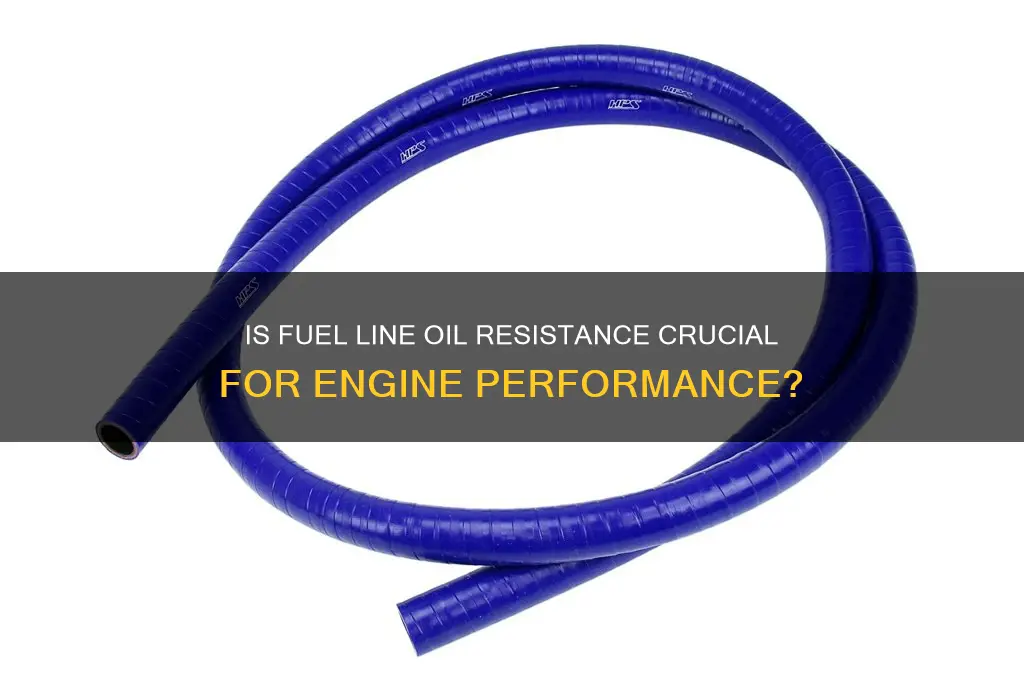
The question of whether fuel line oil resistance is a critical factor in vehicle maintenance is an important one. Fuel lines are a vital component of any vehicle's engine, responsible for transporting fuel from the tank to the engine. Over time, fuel lines can be exposed to various substances, including oil, which can lead to deterioration and potential engine damage. Understanding the resistance of fuel lines to oil is essential for ensuring the longevity and reliability of a vehicle's fuel system. This paragraph aims to explore the significance of this property and its impact on vehicle performance and maintenance.
Characteristics | Values |
---|---|
Material | Various materials are used for fuel lines, including rubber, plastic (such as PVC or EPDM), and synthetic materials like nitrile or fluoropolymer. |
Oil Resistance | Some materials are inherently more resistant to oil than others. For example, fluoropolymer-based materials like FEP or PTFE are highly resistant to oil and other chemicals. Rubber and certain plastics can also be formulated to provide good oil resistance. |
Temperature Range | Fuel lines should be able to withstand the temperature variations in the vehicle's engine compartment. Materials like EPDM and FEP offer good temperature resistance. |
Flexibility | Fuel lines need to be flexible to accommodate engine movement and vibrations. Materials like rubber and certain plastics provide the necessary flexibility. |
Durability | The fuel line should be durable enough to withstand the harsh engine environment, including exposure to heat, fuel, and oil. Materials like nitrile and fluoropolymer offer excellent durability. |
Compatibility | The material of the fuel line should be compatible with the fuel type and other fluids in the vehicle. Some materials may degrade or become brittle when exposed to certain fuels. |
Standard Sizes | Fuel lines are available in various standard sizes to fit different vehicle models and engine configurations. |
Installation | Proper installation techniques are crucial to ensure a secure and leak-free connection. |
What You'll Learn
- Fuel Line Material Compatibility: Which materials are resistant to fuel line oil
- Temperature Tolerance: Can fuel lines withstand high temperatures without oil degradation
- Flexibility and Durability: How flexible and durable are fuel lines against oil
- Oil Leak Prevention: What measures prevent oil leaks in fuel lines
- Longevity in Oil-Rich Environments: How long do fuel lines last in oil-rich conditions
Fuel Line Material Compatibility: Which materials are resistant to fuel line oil?
When it comes to choosing the right materials for fuel lines in vehicles, ensuring compatibility with the fuel and its components is crucial. One important aspect to consider is the resistance of these materials to fuel line oil, which can vary depending on the type of fuel and the specific requirements of the vehicle's fuel system. Here's an overview of some common materials used for fuel lines and their compatibility with fuel line oil:
Rubber and Silicone: Natural rubber and silicone compounds are widely used in fuel lines due to their flexibility and durability. These materials are generally resistant to most types of fuel line oil, including gasoline and diesel. Rubber and silicone can withstand the corrosive effects of these oils, making them suitable for long-term use in fuel systems. However, it's important to note that some high-octane fuels or those containing additives might require specific rubber compounds to ensure optimal performance and longevity.
Fluoropolymer (PTFE): Fluoropolymer, commonly known as Teflon, is an excellent choice for fuel lines due to its exceptional resistance to various fuels and their byproducts. PTFE is highly compatible with fuel line oil and can withstand the harsh conditions of fuel systems. Its non-stick properties and chemical inertness make it ideal for use in high-temperature and high-pressure environments. This material is often used in premium fuel systems and racing applications where performance and reliability are critical.
Braided Steel: Braided steel fuel lines are known for their strength and flexibility. The steel core provides excellent resistance to abrasion and pressure, while the braided design offers flexibility. While steel itself is not typically resistant to fuel line oil, the protective layer applied to the braided steel can be. This protective layer often consists of a rubber or synthetic material that ensures compatibility with the fuel. Braided steel lines are commonly used in high-performance vehicles and racing applications.
Copper and Copper Alloys: Copper and its alloys, such as brass, have been traditionally used in fuel lines due to their excellent conductivity and corrosion resistance. However, copper can be susceptible to fuel line oil, especially in the presence of moisture. To mitigate this, copper fuel lines are often lined with a protective material like rubber or synthetic compounds. These lined copper fuel lines offer improved resistance to fuel line oil and are suitable for most fuel types.
When selecting fuel line materials, it's essential to consider the specific fuel used in the vehicle, the operating conditions, and any additional requirements, such as temperature resistance or flexibility. Consulting the vehicle's manual or seeking advice from automotive experts can provide further guidance on the most suitable materials for fuel lines, ensuring optimal performance and longevity.
Mastering the Art of Splice: Nylon Fuel Line Repair Guide
You may want to see also
Temperature Tolerance: Can fuel lines withstand high temperatures without oil degradation?
The ability of fuel lines to withstand high temperatures without oil degradation is a critical aspect of their performance, especially in automotive and industrial applications. Fuel lines are typically made of materials that are resistant to oil, ensuring that the fuel remains pure and free from contamination. However, when it comes to temperature tolerance, the story becomes more complex.
In high-temperature environments, the performance of fuel lines is tested by the potential for oil degradation. Oil, a component of the fuel mixture, can break down at elevated temperatures, leading to several issues. One of the primary concerns is the formation of acidic compounds, which can corrode the fuel lines and cause damage over time. This corrosion can result in reduced fuel flow, engine misfires, and even complete engine failure. Therefore, it is essential to choose fuel lines that can withstand the operating temperatures of the specific application without compromising the integrity of the fuel.
Materials such as high-density polyethylene (HDPE) and polyvinyl chloride (PVC) are commonly used for fuel lines due to their oil resistance and temperature stability. HDPE, in particular, is known for its excellent resistance to both oil and heat. It can maintain its structural integrity and fluidity even at high temperatures, making it a popular choice for fuel lines in various industries. When selecting fuel lines, it is crucial to consider the maximum operating temperature of the application and choose materials that can handle those conditions without degradation.
Additionally, the design and construction of fuel lines play a significant role in temperature tolerance. Fuel lines should be designed to minimize the risk of heat transfer from the fuel to the line walls. This can be achieved through the use of insulating materials or by incorporating heat shields. Proper insulation ensures that the fuel lines remain at a stable temperature, preventing oil degradation and maintaining the overall performance of the fuel system.
In summary, temperature tolerance is a critical factor in the performance of fuel lines, especially in high-temperature applications. The choice of materials and design considerations are essential to ensure that fuel lines can withstand elevated temperatures without oil degradation. By selecting the right materials and implementing appropriate design strategies, engineers can ensure the reliability and longevity of fuel systems in various industrial and automotive settings.
Choosing the Right Fuel Line for Your Stihl 026 Chainsaw
You may want to see also
Flexibility and Durability: How flexible and durable are fuel lines against oil?
The flexibility and durability of fuel lines are critical factors in ensuring the safe and efficient operation of any vehicle's fuel system. When considering the impact of oil on these components, it becomes evident that the resistance of fuel lines to oil is a crucial aspect of their design and performance.
Fuel lines are typically made from materials that offer a balance between flexibility and strength. Rubber, for instance, is a common choice due to its inherent flexibility, which allows the lines to navigate the intricate layout of a vehicle's engine compartment. This flexibility is essential to accommodate the movement of the engine and various vehicle components during operation. However, the flexibility of rubber can be a double-edged sword when exposed to oil. While it ensures the lines can bend and conform to the engine's contours, it also means that oil can seep into the material over time, potentially leading to degradation and reduced performance.
To combat this issue, manufacturers often incorporate specialized coatings or protective layers on fuel lines. These coatings act as a barrier, preventing oil from directly contacting the inner surface of the line. Materials like synthetic rubber compounds, neoprene, or even specialized polymers are used to create these protective layers. These materials are carefully selected for their ability to resist oil penetration while maintaining the necessary flexibility. For example, neoprene, known for its oil resistance, is often used in high-performance applications where fuel lines are exposed to harsh conditions.
The durability of fuel lines against oil is a complex matter. While the aforementioned coatings provide excellent resistance, the overall durability of the line also depends on its construction and the quality of the materials used. Reinforced fuel lines, often featuring braided or woven components, offer enhanced strength and resistance to oil penetration. These designs are particularly useful in high-pressure fuel systems, where the risk of oil contamination is higher. Additionally, the choice of connectors and fittings is crucial, as they should be compatible with the fuel line material and resistant to oil degradation.
In summary, the flexibility and durability of fuel lines against oil are essential considerations in vehicle maintenance. While the inherent flexibility of rubber is advantageous, it requires careful material selection and protective coatings to ensure long-term performance. Manufacturers' attention to detail in fuel line design, including the use of specialized materials and protective layers, contributes to the overall reliability of the fuel system. Understanding these factors allows vehicle owners and mechanics to make informed decisions regarding fuel line maintenance and replacement, ensuring optimal engine performance and longevity.
Choosing the Right Fuel Line for Small Gas Engines: A Guide
You may want to see also
Oil Leak Prevention: What measures prevent oil leaks in fuel lines?
When it comes to preventing oil leaks in fuel lines, several measures can be taken to ensure optimal performance and longevity. Firstly, understanding the material composition of the fuel lines is crucial. Many modern fuel lines are made from materials that are inherently oil-resistant, such as certain types of rubber, silicone, or even specialized synthetic compounds. These materials are carefully selected to withstand the corrosive effects of oil over time, preventing deterioration and potential leaks.
One effective method to prevent oil leaks is through the use of protective coatings. These coatings are applied to the interior walls of the fuel lines, creating a barrier between the fuel and the line material. Common protective coatings include rubber, latex, or specialized polymers that are designed to be resistant to oil penetration. By applying these coatings, the risk of oil seeping through the walls of the fuel lines is significantly reduced.
Regular maintenance and inspections play a vital role in leak prevention. Over time, fuel lines can develop cracks or damage due to various factors such as age, temperature fluctuations, or physical stress. Conducting routine inspections allows for the early detection of any potential issues. Maintenance technicians can use specialized tools and techniques to identify cracks, punctures, or other forms of damage that may compromise the integrity of the fuel lines.
Another critical aspect is the use of high-quality fuel line connectors and fittings. These components should be made from materials that are compatible with the fuel being transported and resistant to oil degradation. Proper installation and regular tightening of these connectors ensure a secure seal, minimizing the chances of oil leaks at connection points.
Additionally, the use of fuel line guards or protective sleeves can provide an extra layer of defense. These guards are typically made from durable materials that can withstand the harsh conditions within the fuel system, including exposure to oil. By covering the fuel lines with these protective sleeves, the risk of physical damage and subsequent leaks is significantly reduced.
Mastering the Arnold Fuel Line Tool: A Comprehensive Guide
You may want to see also
Longevity in Oil-Rich Environments: How long do fuel lines last in oil-rich conditions?
The longevity of fuel lines in oil-rich environments is a critical consideration for vehicle owners and operators, especially in industries where machinery operates in harsh conditions. Fuel lines, which transport gasoline or diesel from the tank to the engine, are susceptible to degradation when exposed to oil, which can lead to leaks, reduced performance, and potential safety hazards. Understanding the factors that influence the durability of these lines is essential for maintaining reliable and safe operations.
In oil-rich conditions, fuel lines face a unique set of challenges. Oil is known to accelerate the deterioration of rubber, a common material used in fuel line construction. This is primarily due to the solvent action of oil, which can cause the rubber to become brittle and crack over time. As a result, the fuel lines may develop leaks, leading to fuel loss and potential engine misfires or stalls. The severity of this issue is often dependent on the type of oil, its viscosity, and the duration of exposure. For instance, heavy-duty diesel oil, with its higher viscosity, can be particularly damaging to fuel lines, causing rapid degradation.
Several factors contribute to the longevity of fuel lines in oil-rich environments. Firstly, the quality of the fuel lines themselves plays a significant role. High-quality lines, often made from advanced synthetic rubbers, are more resistant to oil degradation. These materials are engineered to maintain their flexibility and strength even when exposed to oil, ensuring a longer service life. Secondly, the installation process is crucial. Properly installed lines, with secure connections and minimal bends, reduce stress on the material, preventing premature wear and tear. Regular inspections and maintenance are also essential, as they allow for the early detection of any signs of damage or wear, enabling timely replacements.
To ensure the longevity of fuel lines in oil-rich conditions, several preventative measures can be implemented. One approach is to use fuel line protectants, which are additives designed to coat the interior walls of the lines, providing a barrier against oil infiltration. These protectants can significantly extend the life of the lines by reducing the direct contact between oil and the rubber. Additionally, regular cleaning and maintenance of the fuel system, including the lines, can help remove any accumulated oil residue, preventing further degradation.
In summary, the durability of fuel lines in oil-rich environments is a complex issue influenced by various factors. While oil exposure is a significant contributor to degradation, the use of high-quality materials, proper installation, and regular maintenance can significantly enhance the lines' longevity. By understanding these factors and implementing appropriate measures, vehicle owners and operators can ensure the reliable and safe operation of their machinery, even in demanding oil-rich conditions.
The Ultimate Guide to Choosing the Best Fuel Dock Line
You may want to see also
Frequently asked questions
Fuel lines are typically made from materials like rubber, vinyl, or specific types of plastic that are engineered to be resistant to oil and other petroleum-based substances. These materials are chosen for their ability to withstand the corrosive effects of oil, ensuring the longevity and reliability of the fuel system.
A simple test to check oil resistance is to expose the fuel line to a small amount of engine oil. If the line remains flexible and shows no signs of deterioration or softening after a period of time, it is likely oil resistant. This test can be performed in a controlled environment to assess the material's performance.
Regular inspection and maintenance are crucial. Look for any signs of cracking, brittleness, or discoloration in the fuel line. It is recommended to replace fuel lines periodically, especially in high-performance vehicles or those operating in harsh conditions. Additionally, using fuel line protectants can help maintain the integrity of the material and enhance its oil resistance.