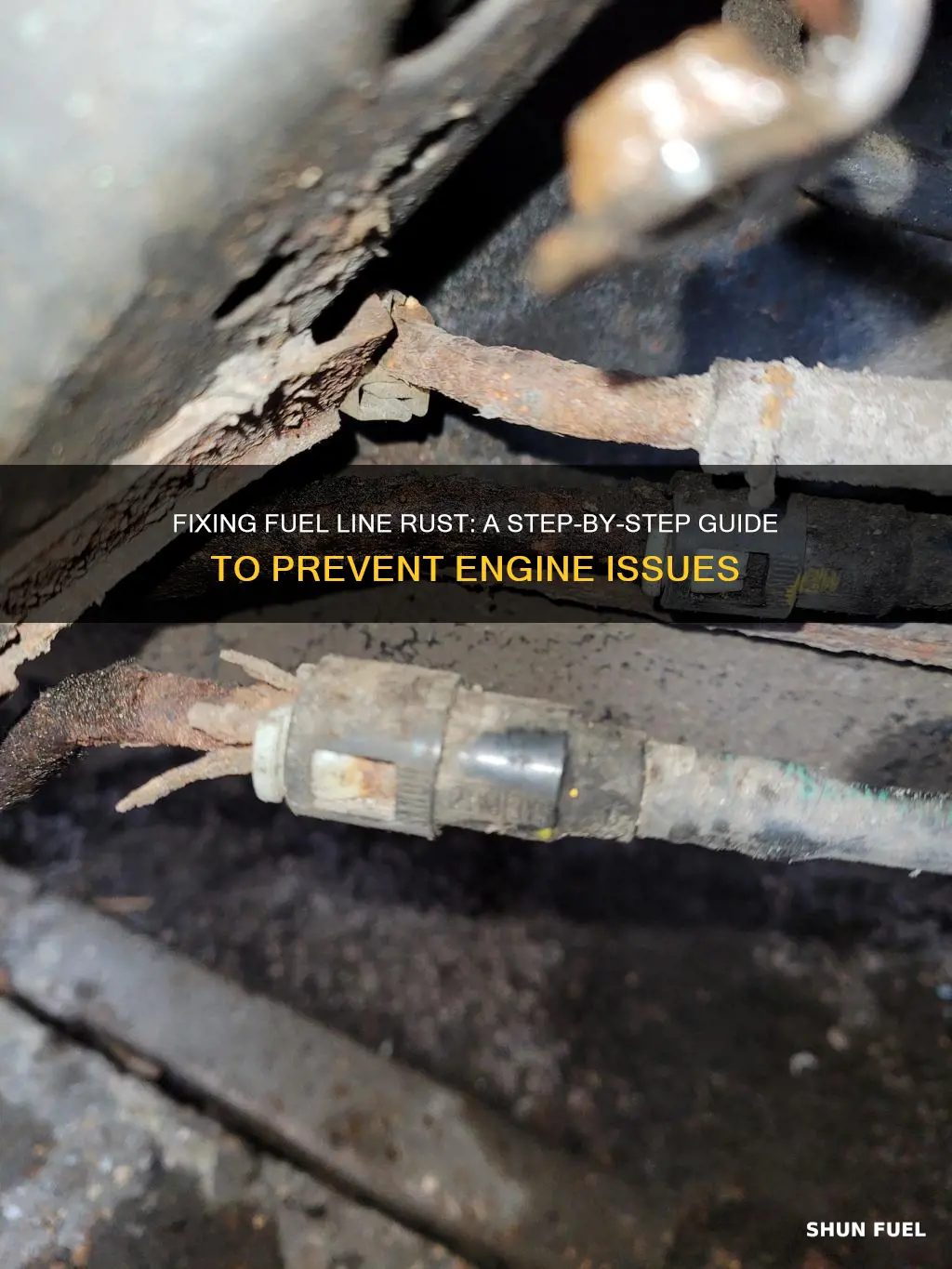
Fuel lines can corrode over time due to exposure to fuel, moisture, and other environmental factors. Rust in fuel lines can lead to reduced performance, engine misfires, and even engine damage. Repairing a rusted fuel line is a task that requires careful attention to detail and the right tools. This guide will provide a step-by-step process to effectively repair a rusted fuel line, ensuring your vehicle's engine runs smoothly and efficiently.
What You'll Learn
- Identify Rusted Fuel Line: Inspect for signs of corrosion, like discolored or flaky material
- Clean and Deburr: Use a wire brush or sandpaper to remove rust and sharp edges
- Apply Rust Inhibitor: Coat the fuel line with a suitable inhibitor to prevent future corrosion
- Replace Damaged Sections: If extensive rusting occurs, consider replacing the affected parts
- Test Fuel System: After repairs, ensure the fuel system functions properly to prevent leaks
Identify Rusted Fuel Line: Inspect for signs of corrosion, like discolored or flaky material
Identifying a rusted fuel line is crucial for maintaining the health of your vehicle's engine. Rust can lead to reduced fuel efficiency, engine performance issues, and even potential safety hazards. Here's a step-by-step guide to help you identify and address this problem:
Start by visually inspecting the fuel line for any visible signs of corrosion. Rust often appears as a discolored or flaky material along the surface of the fuel line. Look for areas where the metal appears to be deteriorating, turning a reddish-brown or orange color, or showing signs of oxidation. These visual cues are often the first indicators of rust formation. Check the entire length of the fuel line, paying extra attention to areas where it is exposed, such as under the vehicle or near the fuel tank.
Feel the fuel line for any texture changes. Rust can cause the metal to become rough and flaky, creating a gritty sensation when you run your fingers or a tool along the line. This tactile inspection can help you identify areas where rust has started to penetrate the surface. If you notice any areas that feel unusually soft or spongy, it could indicate internal corrosion and potential damage to the fuel line's integrity.
Look for any fuel leaks or unusual odors. Rusted fuel lines can lead to small holes or cracks, allowing fuel to leak. Check for puddles of fuel under your vehicle, especially after it has been parked for a while. Additionally, rust can cause the fuel to absorb moisture, resulting in a sweet or metallic smell. If you notice any unusual odors coming from the fuel system, it could be a sign of corrosion and potential damage.
Use a bright light and a mirror to inspect hard-to-reach areas. Rust may be hidden in tight spaces, so use a flashlight or a mirror to illuminate and inspect these areas. Shine the light along the fuel line to look for any discolored or flaky spots that might be missed during a visual inspection. This method can help you identify internal corrosion that may not be visible from the outside.
If you suspect rust, it's essential to take action promptly. Start by cleaning the fuel line to remove any loose rust particles. Use a wire brush or a specialized fuel line cleaner to scrub the affected areas. Then, consider replacing the fuel line if the corrosion is extensive or if you notice any significant damage. Regular maintenance and inspections can help prevent rust-related issues and ensure your vehicle's fuel system remains in optimal condition.
Harley 1200L Fuel Line O-Ring: Size Guide for Optimal Performance
You may want to see also
Clean and Deburr: Use a wire brush or sandpaper to remove rust and sharp edges
When dealing with a fuel line that has rusted, it's crucial to start by cleaning and deburring the affected area. This process ensures that the repair is not only effective but also safe. Here's a step-by-step guide on how to achieve this:
Step 1: Gather the Right Tools
You'll need a few essential tools to get started. A wire brush is an excellent choice for this task as it can effectively remove rust and debris. Alternatively, you can use fine-grit sandpaper, which provides a similar abrasive action. Ensure you have a variety of brush sizes or sandpaper grits to accommodate different areas and the extent of rusting.
Step 2: Prepare the Work Area
Before you begin, make sure the work area is well-ventilated and free from any potential hazards. Rust removal can release small particles into the air, so consider wearing a dust mask for protection. Additionally, have a supply of clean rags or towels ready to wipe away any debris and keep the work area tidy.
Step 3: Cleaning with a Wire Brush
Start by applying gentle, firm strokes of the wire brush to the rusted fuel line. Work in small sections to avoid overwhelming the task. The wire brush will help lift and remove loose rust particles, revealing the underlying metal. Be thorough but careful to avoid damaging the fuel line further. If the rust is particularly stubborn, you may need to apply more pressure, but always maintain control to prevent any sharp edges from forming.
Step 4: Sanding for Precision
For areas where the wire brush might not reach or for more delicate sections, sandpaper is the ideal tool. Use fine-grit sandpaper to carefully remove any remaining rust and sharp edges. Work in a similar manner to the wire brush, taking small sections at a time. This method allows for more precise control, ensuring that you don't create new imperfections. Remember to follow the direction of the fuel line's grooves to avoid any unintended damage.
Step 5: Final Inspection
Once you've completed the cleaning and deburring process, take a moment to inspect the fuel line thoroughly. Look for any remaining rust or sharp spots that might have been missed. If you find any, repeat the cleaning process in those areas until the fuel line is smooth and free from debris. A clean and deburred fuel line is essential to ensure a successful repair and to maintain the overall health of your vehicle's fuel system.
Choosing the Right Fuel Line for Your 25 HP Mercury Outboard
You may want to see also
Apply Rust Inhibitor: Coat the fuel line with a suitable inhibitor to prevent future corrosion
To effectively repair a fuel line that has rusted, one crucial step is to apply a rust inhibitor. This process is designed to create a protective barrier on the fuel line's surface, preventing further corrosion and ensuring the longevity of the repair. Here's a detailed guide on how to accomplish this:
Step 1: Choose the Right Inhibitor
Start by selecting a rust inhibitor specifically formulated for use on fuel lines. These inhibitors are typically designed to withstand the harsh conditions of fuel systems. Look for products that are compatible with your fuel type (gasoline or diesel) and the material of your fuel line. Common types of inhibitors include silicate-based, phosphate-based, and zinc-based formulas.
Step 2: Prepare the Fuel Line
Before applying the inhibitor, ensure the fuel line is clean and dry. Rinse the fuel line with a suitable solvent to remove any dirt, debris, or old inhibitor residue. This step is essential to ensure proper adhesion of the new inhibitor. If the fuel line is severely corroded, consider replacing a section of the line to prevent the spread of corrosion.
Step 3: Apply the Rust Inhibitor
- Spray Application: Use a spray bottle or a specialized spray gun to apply the inhibitor evenly along the length of the fuel line. Ensure you cover all exposed surfaces, including any bends or fittings. Spray in a steady, even manner, allowing the product to penetrate the surface.
- Brush Application: For hard-to-reach areas or intricate fuel line designs, use a small brush to apply the inhibitor. Dip the brush in the inhibitor solution and carefully coat the affected areas.
- Follow Instructions: Always adhere to the manufacturer's instructions for application rates and drying times. Different inhibitors may require specific techniques, so it's crucial to follow the provided guidelines.
Step 4: Allow Adequate Drying Time
After applying the inhibitor, allow sufficient time for it to dry completely. The drying time will vary depending on the product and environmental conditions. Avoid running the engine or handling the fuel line during this period to ensure the inhibitor sets properly.
Step 5: Reassemble and Test
Once the inhibitor is fully dried, reassemble the fuel line and secure it in place. Start the engine and let it run for a while to ensure the inhibitor is distributed evenly throughout the system. Check for any leaks or unusual noises, and verify that the fuel line is functioning correctly.
Applying a rust inhibitor is a proactive measure that not only repairs the existing corrosion but also provides long-term protection against future rust formation. Regular maintenance and inspection of the fuel system will further ensure its reliability and performance.
Jacob's Fuel Line Break: A Potential Catastrophe Unveiled
You may want to see also
Replace Damaged Sections: If extensive rusting occurs, consider replacing the affected parts
If you encounter significant rusting in your fuel line, it is crucial to address the issue promptly to prevent further damage and ensure the safe operation of your vehicle. In such cases, replacing the damaged sections becomes a necessary step in the repair process. Here's a detailed guide on how to approach this task:
Assess the Damage: Begin by thoroughly inspecting the fuel line to identify the extent of the rusting. Look for any visible signs of corrosion, such as a reddish-brown color or a powdery substance along the line. Measure the length of the affected area to determine the amount of replacement needed. It is essential to be meticulous in this step to ensure you order the correct replacement parts.
Gather the Required Tools and Materials: Before starting the replacement process, gather all the necessary tools and materials. You will typically need a fuel line cutter or a pair of sharp scissors or knives to carefully cut away the damaged section. Additionally, have a replacement fuel line section that matches the original specifications, including the correct diameter and material (usually metal or rubber). Don't forget to have a fuel filter and any necessary fittings or adapters to ensure a proper connection.
Prepare the Work Area: Set up your work area in a well-ventilated space, preferably outdoors, to avoid any potential hazards from fuel fumes. Ensure you have a stable surface to work on, and consider using a tarp or drop cloth to catch any debris or spills. It is also advisable to wear protective gear, including gloves and safety goggles, to safeguard yourself during the process.
Cut and Remove the Damaged Section: Using the fuel line cutter or your chosen cutting tool, carefully sever the damaged section of the fuel line. Make clean, precise cuts to avoid any sharp edges that could cause further issues. Once cut, slowly pull out the old section, being mindful of any remaining fuel or debris that may need to be drained or cleaned.
Install the New Fuel Line: Now, it's time to fit the replacement section. Start by attaching the new fuel line to the nearest fuel source or existing line using the appropriate fittings. Ensure a tight and secure connection, and consider using fuel line tape or a similar sealing compound to prevent any leaks. Follow the manufacturer's instructions for the specific make and model of your vehicle to ensure a proper fit.
Test and Verify: After installing the new fuel line, it is crucial to test the system to ensure there are no leaks or issues. Start the vehicle and check for any unusual noises or smells. Monitor the fuel gauge and ensure it functions correctly. If everything is in order, you've successfully replaced the damaged section and addressed the rusting problem. Regularly inspect the new fuel line for any signs of further corrosion and take preventive measures to maintain its condition.
Handholes for Diesel Fuel Lines: When and Why
You may want to see also
Test Fuel System: After repairs, ensure the fuel system functions properly to prevent leaks
After repairing a fuel line that has been damaged by rust, it is crucial to thoroughly test the fuel system to ensure its functionality and prevent any potential leaks. Here's a step-by-step guide to effectively test the fuel system post-repair:
Step 1: Inspect the Repaired Area: Begin by visually inspecting the section of the fuel line that was repaired. Check for any visible signs of damage, such as cracks, corrosion, or debris. Ensure that all connections and fittings are secure and free from any potential leaks. Look for any signs of moisture or condensation, as these could indicate a compromised seal.
Step 2: Perform a Pressure Test: A pressure test is an essential step to verify the integrity of the fuel line. Use a fuel line pressure tester or a similar tool designed for this purpose. Connect the tester to the fuel line, ensuring a tight seal. Gradually increase the pressure and monitor the gauge for any drops or fluctuations. A stable reading indicates a secure and leak-free connection. If any pressure loss is detected, investigate further and address any potential issues, such as damaged fittings or compromised seals.
Step 3: Start the Engine: With the fuel system prepared, it's time to test the engine. Start the vehicle and allow it to idle for a few minutes. Pay close attention to any unusual noises, such as hissing or bubbling sounds, which could indicate fuel leaks. Check for any fuel odors around the engine bay, as these can also signify a leak. Ensure that the engine runs smoothly and that there are no signs of excessive fuel consumption or smoke from the exhaust.
Step 4: Check for Leaks: Visually inspect the entire fuel system, including the repaired section, for any signs of fuel leakage. Look for wet spots or stains on the ground beneath the vehicle, as these could indicate a hidden leak. Inspect all connections, fittings, and fuel injectors for any signs of fuel seepage. If any leaks are detected, immediately address the issue by tightening connections or replacing damaged components.
Step 5: Monitor Fuel Levels: After the engine has been running for a while, check the fuel gauge to ensure it is functioning correctly. Verify that the fuel level is accurate and that the engine is not consuming fuel at an abnormally high rate. Any discrepancies in fuel levels could indicate a potential issue with the fuel pump or injectors.
By following these steps, you can ensure that the fuel system is functioning properly and that the repairs have been successful, minimizing the risk of fuel leaks and potential engine damage. Regular maintenance and testing are essential to maintaining a safe and efficient fuel system.
Goped Fuel Lines: Unlocking the Mystery of Dual Lines
You may want to see also
Frequently asked questions
Rust in fuel lines is often indicated by a decrease in fuel pressure, engine misfires, or a noticeable drop in engine performance. You may also notice a metallic taste in the fuel or see rust-colored deposits inside the fuel tank.
Fuel lines can rust due to exposure to moisture, especially in older vehicles or those with fuel tank issues. Moisture in the fuel can lead to corrosion, especially in steel or aluminum fuel lines.
Yes, minor rust damage can be repaired by replacing the affected section of the fuel line. However, for severe corrosion or if you're unsure about the process, it's recommended to consult a professional mechanic to ensure a proper and safe repair.
You'll need a new fuel line section that matches your vehicle's specifications, fuel line connectors, and possibly a fuel filter. Basic tools like wrenches, pliers, and a fuel line cutter will be required for the installation process.
Regularly check for any signs of moisture in the fuel tank and ensure the fuel system is properly sealed. Using a fuel stabilizer can also help prevent corrosion. It's essential to address any fuel-related issues promptly to maintain the integrity of the fuel system.