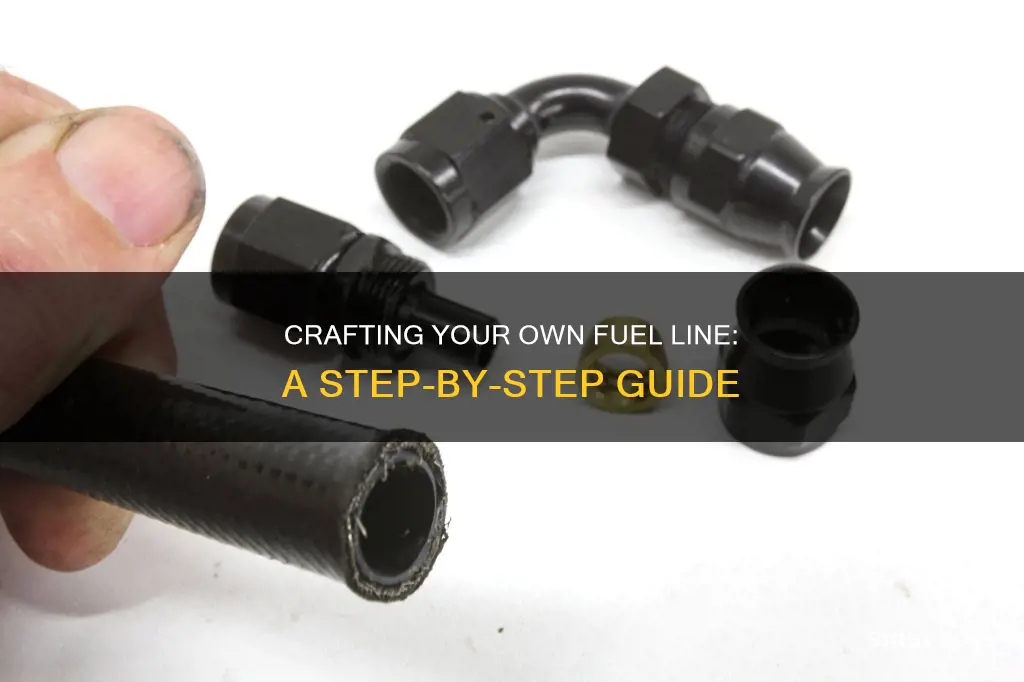
Creating fuel lines is a specialized process that requires careful consideration of materials, design, and manufacturing techniques. It involves selecting appropriate materials such as high-quality hoses, fittings, and adapters that can withstand the pressures and temperatures encountered in fuel systems. The design phase is crucial, as it involves determining the optimal route for the fuel line, considering factors like engine placement, vehicle layout, and safety requirements. Manufacturing involves precise cutting, bending, and joining of the materials, often using specialized tools and techniques like crimping, swaging, or welding. Quality control is essential to ensure the fuel line meets industry standards and can safely transport fuel without leaks or damage. This process demands expertise in engineering, materials science, and manufacturing to produce reliable and efficient fuel lines for various applications, from automotive to aviation.
What You'll Learn
- Fuel Line Materials: Choose appropriate materials like steel, rubber, or plastic based on fuel type and vehicle requirements
- Fuel Line Routing: Plan the route to avoid sharp bends and ensure easy access for maintenance
- Fuel Line Fittings: Use compatible fittings and connectors for secure connections and leak prevention
- Fuel Line Testing: Inspect for leaks and ensure proper pressure and flow using pressure gauges and fuel testers
- Fuel Line Maintenance: Regularly check for damage, corrosion, and contamination to ensure optimal performance
Fuel Line Materials: Choose appropriate materials like steel, rubber, or plastic based on fuel type and vehicle requirements
When it comes to creating a fuel line for your vehicle, selecting the right materials is crucial for ensuring optimal performance and longevity. The choice of material depends on various factors, including the type of fuel used and the specific requirements of your vehicle. Here's a detailed guide on choosing the appropriate materials:
Steel:
Steel is a robust and durable material commonly used for fuel lines. It is an excellent choice for vehicles that operate in harsh environments or those that require high-pressure fuel systems. Steel fuel lines are known for their strength and ability to withstand extreme temperatures. However, they can be heavier and more rigid compared to other options. This material is often used in high-performance vehicles or classic cars where a classic look is desired. When using steel, ensure that the fuel line is properly insulated to prevent corrosion and maintain the integrity of the fuel system.
Rubber:
Rubber fuel lines are a popular and cost-effective choice for most vehicles. They offer flexibility, making them ideal for accommodating the natural movement and vibrations within a vehicle's engine compartment. Rubber is resistant to most fuels, including gasoline and diesel, making it a versatile option. This material is also lightweight and easy to install. Look for high-quality rubber that is reinforced with braided steel or nylon to enhance its strength and flexibility. Rubber fuel lines are a safe and reliable choice for everyday vehicles.
Plastic (Polyethylene or PVC):
Plastic fuel lines, often made from materials like polyethylene or PVC, are lightweight and flexible. They are an excellent choice for vehicles that require a more lightweight fuel system or those with limited space under the hood. Plastic is generally resistant to most fuels and is less susceptible to corrosion. However, it may not be as durable as steel or high-quality rubber, so it is essential to choose a reputable brand to ensure longevity. Plastic fuel lines are often used in modern vehicles with fuel-efficient engines.
When selecting materials, consider the following:
- Fuel Type: Different fuels have varying properties, and some materials may be more compatible than others. For example, ethanol-blended fuels might require specific materials to prevent degradation.
- Vehicle Requirements: Take into account the vehicle's engine size, power output, and operating conditions. High-performance vehicles may demand more robust materials.
- Climate and Environment: Consider the typical climate and environmental conditions your vehicle will encounter. Extreme temperatures or harsh weather may impact material choice.
- Safety and Regulations: Ensure that the chosen materials comply with local regulations and safety standards, especially for fuel-related components.
Fuel Filter's Role: Ensuring Supply Line Efficiency
You may want to see also
Fuel Line Routing: Plan the route to avoid sharp bends and ensure easy access for maintenance
When designing the fuel line for a vehicle or any machinery, proper routing is crucial to ensure optimal performance and longevity. One of the key considerations is to avoid sharp bends in the fuel line. Sharp bends can restrict fuel flow, cause pressure drops, and even lead to fuel aeration, which can result in poor engine performance and potential fuel system issues. Here's a step-by-step guide to planning the fuel line route:
- Identify the Starting Point and Destination: Begin by clearly understanding the source and destination of the fuel line. Locate the fuel tank and identify the points where fuel needs to be supplied, such as the engine, fuel pump, or any fuel-fed components. This initial assessment will help you determine the overall length and direction of the fuel line.
- Plan the Route: Design a route that minimizes sharp turns and tight spaces. The ideal path should be as straight as possible, allowing the fuel line to maintain a consistent flow. Consider the vehicle's or machinery's structure and available space. Aim for a route that provides easy access to the fuel line for maintenance and inspection. Avoid running the fuel line along the edges of panels or under tight spaces where it might be damaged or restricted.
- Use Flexible Materials: Opt for flexible fuel line materials that can accommodate slight bends without kinking or restricting flow. This flexibility is essential to ensure the line can adjust to the planned route without causing issues. Modern fuel lines are often made from materials like rubber or synthetic compounds, designed to be durable and flexible.
- Consider Maintenance Access: Ensure that the fuel line route allows for easy access during maintenance and repairs. This is critical for regular maintenance tasks and in case of any issues. Avoid routing the fuel line in areas that would require extensive disassembly to reach, making maintenance more challenging and time-consuming.
- Secure the Line: Properly secure the fuel line to prevent movement and potential damage. Use appropriate clamps or ties to attach the line to the vehicle or machinery's structure, ensuring it remains in place without causing any interference. Secure it at regular intervals to maintain tension and prevent sagging, which can lead to fuel leaks or contamination.
By following these guidelines, you can create a fuel line routing system that is efficient, durable, and easy to maintain, ultimately contributing to the overall reliability of the vehicle or machinery. Proper planning and attention to detail in the routing process are essential to avoid common issues associated with fuel lines.
Unraveling GM Fuel Line Plastics: A Comprehensive Guide
You may want to see also
Fuel Line Fittings: Use compatible fittings and connectors for secure connections and leak prevention
When constructing a fuel line, ensuring the use of compatible fittings and connectors is crucial for maintaining a secure and leak-free system. The primary goal is to create a robust connection that can withstand the pressure and temperature variations associated with fuel transport. Here's a step-by-step guide to achieving this:
Choose the Right Fittings: Select fittings that are specifically designed for the type of fuel line you are working with. Different fuels have varying properties, and using the appropriate fittings ensures compatibility and prevents potential issues. For instance, if you're dealing with gasoline, opt for fittings made from materials like brass or aluminum alloys, which offer good corrosion resistance and durability.
Consider the Connection Type: There are various connection types, such as quick-connect couplings, compression fittings, and clamp-style fittings. Each has its advantages and is suited to different applications. Quick-connect couplings provide a fast and easy way to join fuel lines but may not be as secure as other methods. Compression fittings offer a tight seal and are commonly used in automotive applications. Clamp-style fittings provide excellent flexibility and are ideal for routing fuel lines around tight spaces.
Ensure Proper Sizing: Fittings and connectors should be the correct size to ensure a snug fit. Using fittings that are too small can lead to reduced flow and potential pressure buildup, while larger fittings might not provide adequate sealing. Always refer to the manufacturer's specifications to determine the appropriate size for your fuel line diameter.
Prepare the Fuel Line: Before connecting the fittings, ensure the fuel line is clean and free of any debris or contaminants. Use a suitable cleaner to remove any old fuel or contaminants from the line. This step is essential to ensure a proper seal and prevent any leaks. Additionally, inspect the fuel line for any damage or wear, replacing it if necessary.
Install the Fittings Securely: When connecting the fittings, follow the manufacturer's instructions carefully. Apply the correct amount of sealant or tape to the threads or sealing surfaces to create a reliable bond. Tighten the fittings securely, but be cautious not to over-tighten, as this can damage the fuel line. A good rule of thumb is to use a wrench or tool that provides a controlled amount of force to ensure an even connection.
Test for Leaks: After installing the fittings, it's crucial to test the fuel line for any leaks. This can be done by applying pressure to the system and checking for any signs of fuel escaping. Use a soapy water solution or a specialized leak detection kit to identify any potential issues. If leaks are found, carefully inspect the connections and tighten or replace the fittings as needed.
By following these guidelines, you can ensure that your fuel line fittings are compatible, securely connected, and capable of preventing fuel leaks, which is essential for the safe and efficient operation of any fuel-powered system.
Mastering the Art: A Step-by-Step Guide to Removing Fuel Line Connectors from Nylon Hoses
You may want to see also
Fuel Line Testing: Inspect for leaks and ensure proper pressure and flow using pressure gauges and fuel testers
Fuel line testing is a critical step in ensuring the safety and efficiency of your vehicle's fuel system. It involves a thorough inspection to identify any potential issues with the fuel lines, such as leaks, blockages, or pressure-related problems. Here's a detailed guide on how to test your fuel lines for leaks and maintain optimal pressure and flow:
Leak Detection: Start by visually inspecting the fuel lines for any signs of damage, cracks, or corrosion. Look for any visible leaks or moisture around the fuel lines, especially where they connect to the fuel tank, engine, and injectors. You can use a simple soap solution or a specialized fuel line leak detector to make this process easier. Apply the soapy mixture along the length of the fuel lines and watch for bubbles, which indicate a leak. If you find any leaks, it's crucial to repair or replace the affected fuel line promptly to prevent fuel loss and potential engine damage.
Pressure Testing: Proper pressure is essential for efficient fuel delivery to the engine. Use a mechanical or digital fuel pressure gauge to measure the pressure at the fuel rail or injectors. The ideal pressure can vary depending on your vehicle's specifications, so consult your vehicle's manual for the correct range. If the pressure is too low, it may indicate a restricted fuel line or a problem with the fuel pump. Conversely, excessive pressure could be a sign of a blocked fuel filter or a faulty pressure regulator. Adjustments or repairs may be necessary to bring the pressure within the optimal range.
Flow Testing: Ensuring a smooth and consistent fuel flow is vital for engine performance. You can perform a basic flow test by starting the engine and monitoring the fuel pressure gauge. If the pressure remains stable and there are no sudden drops or spikes, it suggests good fuel flow. However, if the pressure fluctuates or drops significantly, it may indicate a restriction in the fuel line or a problem with the fuel pump's ability to deliver fuel at the required rate. In such cases, further investigation and potential repairs are warranted.
Using Fuel Testers: Specialized fuel testers can provide more accurate readings and help identify specific issues. These testers often have multiple functions, including leak detection, pressure measurement, and flow rate assessment. Connect the fuel tester to the fuel line and follow the manufacturer's instructions for accurate readings. Fuel testers can help pinpoint problems like blocked fuel lines, faulty fuel pumps, or issues with the fuel injection system.
Remember, regular maintenance and testing of your fuel lines are essential to keep your vehicle running smoothly and efficiently. By following these steps and using the appropriate tools, you can ensure that your fuel system is in optimal condition, reducing the risk of breakdowns and improving overall engine performance.
Fixing Fuel Lines: The Role of RTV
You may want to see also
Fuel Line Maintenance: Regularly check for damage, corrosion, and contamination to ensure optimal performance
Fuel lines are a critical component of any vehicle's fuel system, and proper maintenance is essential to ensure optimal performance and longevity. Regular checks and inspections can help identify potential issues before they become major problems, saving you from costly repairs and ensuring your vehicle runs smoothly. Here's a comprehensive guide on how to maintain your fuel lines effectively:
Inspect for Damage: Visual inspections are a simple yet crucial part of fuel line maintenance. Start by examining the fuel lines for any visible signs of damage. Look for cracks, punctures, or tears in the rubber or plastic material. Over time, fuel lines can degrade due to heat, sunlight, and the corrosive effects of fuel itself. Check the lines for any brittleness or discolouration, especially at points where they are under stress, such as near the engine and along the frame. If you notice any damage, it's important to address it promptly. Minor tears or cracks can often be temporarily sealed with specialized repair tape or compound, providing a temporary fix until a more permanent solution is implemented.
Check for Corrosion: Corrosion is a common enemy of fuel lines, especially in older vehicles or those exposed to harsh environmental conditions. Moisture and fuel can create an ideal environment for corrosion, leading to the deterioration of metal components within the fuel lines. Inspect the fuel lines for any signs of rust or corrosion, particularly at connections and fittings. If you find any corrosion, it's best to replace the affected sections. In some cases, you might need to flush the entire fuel system to remove any corrosive substances and then refill it with fresh fuel to prevent further issues.
Monitor for Contamination: Fuel contamination can significantly impact engine performance and longevity. Over time, fuel can absorb moisture, leading to the formation of sludge and varnish, which can clog fuel injectors and carburetor passages. Regularly check for any signs of contamination, such as a milky appearance in the fuel tank or the presence of sediment at the bottom of the tank. If contamination is detected, drain and clean the fuel tank, and consider using a fuel system cleaner to remove any built-up deposits. It's also a good practice to use a fuel stabilizer when storing vehicles for extended periods to prevent contamination.
Regular Maintenance Schedule: Establishing a regular maintenance routine is key to preventing fuel line issues. Create a schedule to inspect and test the fuel lines at regular intervals, especially before and after long journeys or during seasonal changes. This routine should include checking for leaks, ensuring proper fuel pressure, and verifying the functionality of fuel pumps and injectors. By staying proactive, you can identify and rectify potential problems before they cause performance issues or expensive repairs.
Remember, fuel line maintenance is an essential aspect of vehicle care. By following these simple yet effective practices, you can ensure that your fuel system operates efficiently, providing reliable performance and potentially extending the life of your vehicle. Regular attention to these details can save you from unexpected breakdowns and keep your engine running smoothly.
Dissolving Fuel Line: Uncover the Mystery Behind Your Chainsaw's Malfunction
You may want to see also
Frequently asked questions
Fuel lines are typically made from materials like rubber, vinyl, or synthetic compounds such as ethylene propylene rubber (EPR) or thermoplastic elastomers (TPE). These materials are chosen for their flexibility, durability, and resistance to fuel degradation.
To ensure a proper fit, it's crucial to measure the fuel line carefully and compare it to the vehicle's specifications. Use the appropriate tools, such as a fuel line cutter or a fuel line adapter, to achieve a precise length. Ensure that the fuel line is routed correctly, avoiding sharp bends or kinks, and securely attach it to the fuel tank and engine using the recommended fittings and clamps.
While it's possible to transfer a fuel line from one vehicle to another with similar engine and fuel system specifications, it's essential to verify the compatibility. Different vehicles may have unique fuel line configurations, so always refer to the vehicle's manual or consult a professional to ensure the correct part is used. Using the wrong fuel line can lead to fuel leaks, engine performance issues, or even safety hazards.