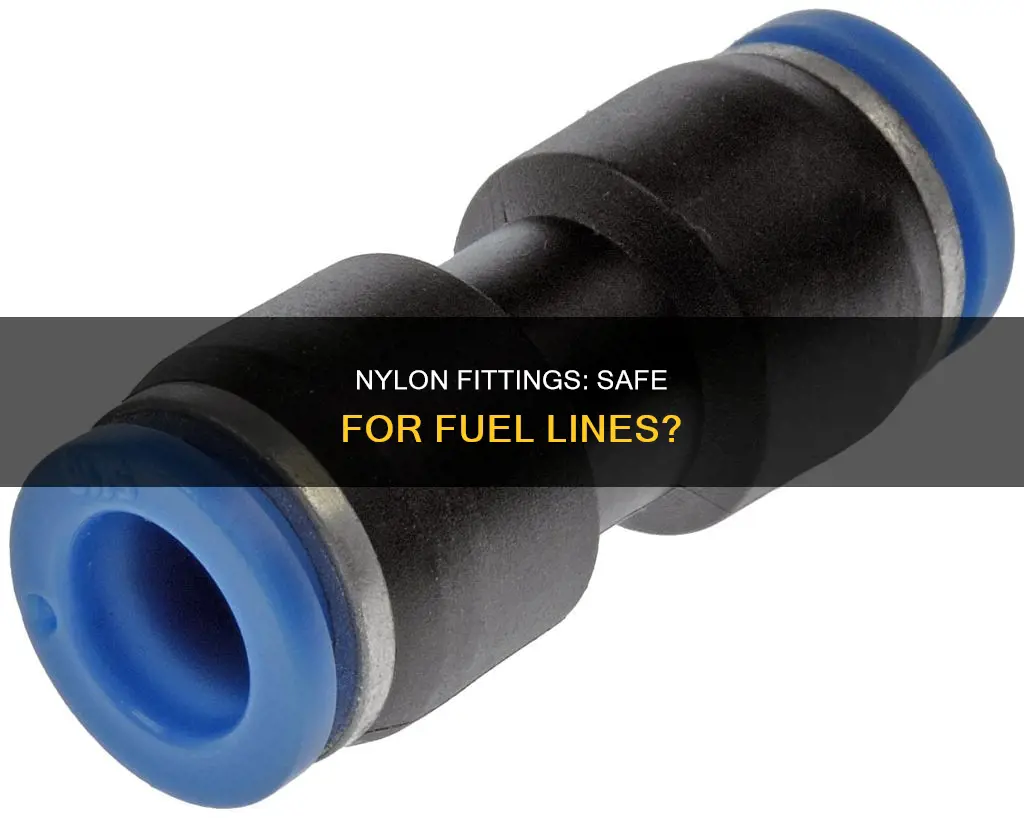
When considering the use of nylon fittings for fuel lines, it's important to evaluate their safety and compatibility. Nylon fittings are known for their flexibility and resistance to heat and chemicals, making them a popular choice for various applications. However, for fuel lines, which require strict adherence to safety standards due to the flammable nature of gasoline, the choice of material becomes even more critical. Nylon's ability to withstand high temperatures and its chemical inertness make it a viable option for some fuel line systems. Nonetheless, it's essential to ensure that the specific nylon fitting meets the required specifications and standards for fuel line applications to guarantee the safety and reliability of the fuel system.
Characteristics | Values |
---|---|
Material | Nylon |
Temperature Range | -40°F to 250°F (-40°C to 121°C) |
Pressure Rating | Up to 250 psi (17.2 bar) |
Flexibility | Good flexibility for easy installation |
Corrosion Resistance | Excellent resistance to fuel-related chemicals |
Compatibility | Suitable for gasoline, diesel, and biofuels |
Color | Typically black or white |
Application | Fuel lines, hoses, and connections |
Advantages | Lightweight, cost-effective, and easy to install |
Disadvantages | May not be as durable as metal fittings in extreme conditions |
Regulatory Compliance | Meets industry standards for fuel system components |
What You'll Learn
- Material Compatibility: Nylon fittings are safe for fuel lines if they are compatible with the fuel type
- Temperature Resistance: Nylon can withstand fuel line temperatures, but extreme heat may cause degradation
- Flexibility: Nylon's flexibility ensures it can accommodate fuel line movement without cracking
- Chemical Resistance: Nylon is resistant to common fuel line chemicals, ensuring long-term safety
- Installation Guidelines: Proper installation is crucial; follow manufacturer instructions for secure fuel line connections
Material Compatibility: Nylon fittings are safe for fuel lines if they are compatible with the fuel type
Nylon fittings can be a suitable choice for fuel lines in certain applications, but their safety and performance depend on the compatibility with the specific fuel type. When considering the use of nylon fittings for fuel lines, it is crucial to understand the material compatibility to ensure optimal performance and prevent potential issues.
Nylon, a synthetic polymer, offers several advantages for fuel line applications. It is known for its flexibility, durability, and resistance to various chemicals. These properties make nylon an attractive option for fuel systems, especially in environments where traditional metal or rubber components might not be ideal. However, the compatibility of nylon with different fuel types is essential to its success.
The compatibility of nylon with fuel lines is primarily determined by the type of fuel being used. Nylon fittings are generally safe and suitable for fuel lines that carry gasoline, methanol, or ethanol-blended fuels. These fuels have relatively low chemical reactivity and do not typically cause degradation or swelling in nylon materials. As a result, nylon fittings can provide a secure and reliable connection in these fuel systems.
On the other hand, nylon's compatibility is limited when it comes to fuels with higher chemical reactivity, such as diesel or certain synthetic blends. These fuels can cause nylon to degrade over time, leading to potential leaks, reduced performance, or even failure of the fuel line system. Therefore, it is crucial to consider the specific fuel type and its properties before selecting nylon fittings for fuel lines.
To ensure the safe and effective use of nylon fittings in fuel lines, it is recommended to consult manufacturer guidelines and specifications. These resources will provide detailed information on the compatibility of nylon with various fuel types, allowing for informed decisions. By carefully considering material compatibility, you can optimize the performance and longevity of your fuel line system.
Flue Liner Sizing Guide: Choosing the Right Fit for Your Multi-Fuel Stove
You may want to see also
Temperature Resistance: Nylon can withstand fuel line temperatures, but extreme heat may cause degradation
Nylon fittings are often considered a suitable and safe option for fuel lines in various applications, especially when it comes to temperature resistance. These fittings are known for their ability to handle the typical temperature ranges found in fuel systems, which is a crucial factor in ensuring the safety and efficiency of the entire setup.
The temperature resistance of nylon is primarily due to its chemical composition and molecular structure. Nylon, a type of polymer, has a unique ability to maintain its shape and structural integrity under varying thermal conditions. It can withstand the temperatures commonly associated with fuel, which often range from sub-zero cold starts to high-temperature operation during extended periods of use. This makes nylon an excellent choice for fuel lines, especially in environments where temperature fluctuations are common.
However, it is essential to recognize that while nylon can handle the temperatures found in fuel systems, there are certain limitations. Extreme heat, beyond the typical operating range, can cause degradation of the nylon material. When exposed to temperatures significantly higher than the recommended limits, nylon fittings may experience a loss of flexibility, becoming brittle and prone to cracking. This degradation can lead to potential fuel leaks and system failures, making it crucial to understand the temperature limits of nylon for fuel line applications.
To ensure the safe and efficient operation of fuel lines, it is recommended to adhere to the manufacturer's guidelines regarding temperature tolerance. Operating nylon fittings within the specified temperature range ensures their longevity and reliability. For instance, most nylon fittings can handle temperatures between -40°F and 250°F (-40°C and 121°C), but it is essential to check the specific product's data sheet for accurate details.
In summary, nylon fittings offer a reliable solution for fuel lines due to their temperature resistance, allowing them to withstand the typical thermal conditions of fuel systems. Nonetheless, extreme heat can cause degradation, emphasizing the need for careful consideration of temperature limits to ensure the safety and performance of the fuel line setup. Always refer to the manufacturer's specifications for the best results and to avoid any potential issues related to temperature-induced degradation.
Subaru Impreza 2010: Canister Fuel Line Location Guide
You may want to see also
Flexibility: Nylon's flexibility ensures it can accommodate fuel line movement without cracking
Nylon fittings are an excellent choice for fuel line applications due to their inherent flexibility, which is a crucial factor in ensuring the safety and longevity of the fuel system. The flexibility of nylon allows it to accommodate the natural movement and expansion of fuel lines, especially in high-temperature environments. This is particularly important in automotive and marine settings, where fuel lines are constantly subjected to vibrations, temperature fluctuations, and the natural settling and shifting of the vehicle or vessel.
When it comes to fuel lines, flexibility is key to preventing cracks and leaks. Rubber, a common material for fuel lines, can become brittle over time, especially when exposed to fuel's harsh chemicals. This brittleness often leads to cracks, which can result in fuel leaks and potential fire hazards. Nylon, on the other hand, retains its flexibility even in low-temperature conditions, ensuring that the fuel line can move and flex without the risk of cracking. This is especially beneficial in cold climates or when the vehicle is parked for extended periods.
The flexibility of nylon fittings is not just about preventing cracks; it also contributes to the overall durability of the fuel system. As the vehicle accelerates, decelerates, or undergoes sudden maneuvers, the fuel lines experience a range of movements. Nylon's ability to flex and bend without breaking ensures that the fuel lines remain intact, reducing the risk of damage and potential fuel loss. This is particularly important in high-performance vehicles or those with aggressive driving conditions.
Furthermore, the flexibility of nylon fittings allows for easier installation and maintenance. When compared to rigid materials, nylon fittings can be more easily manipulated to fit into tight spaces and around various engine components. This ease of installation not only saves time but also reduces the risk of damage to the fuel lines during the installation process. Additionally, when it's time for maintenance or repairs, the flexibility of nylon fittings makes it simpler to access and replace the fuel lines without causing unnecessary strain or damage.
In summary, the flexibility of nylon fittings is a critical advantage when considering their use in fuel line applications. It ensures that the fuel lines can withstand the rigors of daily use, from temperature variations to mechanical stress, without the risk of cracking or breaking. This flexibility, combined with nylon's durability and ease of installation, makes it an ideal choice for anyone looking to enhance the safety and performance of their fuel system.
Air Bubbles in Diesel Fuel Lines: A Cause for Concern?
You may want to see also
Chemical Resistance: Nylon is resistant to common fuel line chemicals, ensuring long-term safety
Nylon fittings are an excellent choice for fuel line applications due to their chemical resistance, which is a critical factor in ensuring the long-term safety and reliability of any fuel system. When it comes to fuel lines, the materials used must be able to withstand the corrosive effects of various chemicals present in gasoline, diesel, and other fuels. Nylon, with its unique chemical properties, excels in this regard.
The chemical resistance of nylon is a result of its molecular structure, which is resistant to degradation caused by common fuel line chemicals. These chemicals include various additives, stabilizers, and impurities found in fuels. For instance, gasoline often contains ethanol, which can be corrosive to certain materials, but nylon's resistance to ethanol makes it a suitable choice. Similarly, diesel, with its higher sulfur content, can also pose challenges to material integrity, but nylon's ability to resist sulfur compounds ensures its longevity in such environments.
In the context of fuel lines, the presence of these chemicals can lead to material breakdown, cracking, or leaching, which could result in fuel contamination and potential engine damage. Nylon's resistance to these chemicals means it can maintain its structural integrity over time, preventing such issues. This is particularly important in high-temperature environments, where nylon's resistance to heat and chemicals ensures it can handle the stresses of fuel systems without compromising performance.
Furthermore, the chemical resistance of nylon is not limited to the fuel itself but also extends to the various fluids and lubricants used in fuel systems. For example, engine oil, coolant, and transmission fluid can all contain chemicals that could potentially damage other materials. Nylon's resistance to these chemicals ensures that the fuel lines and fittings remain unaffected, providing a safe and efficient fuel delivery system.
In summary, the chemical resistance of nylon makes it an ideal material for fuel line fittings. Its ability to withstand common fuel line chemicals ensures the long-term safety and reliability of fuel systems, providing peace of mind to vehicle owners and operators. This property, combined with nylon's durability and flexibility, makes it a preferred choice for fuel line applications, offering a cost-effective and safe solution for managing fuel delivery in various vehicles and machinery.
Optimizing Performance: Choosing the Right Fuel Line for Your SBC 350
You may want to see also
Installation Guidelines: Proper installation is crucial; follow manufacturer instructions for secure fuel line connections
When it comes to fuel line connections, proper installation is paramount to ensure the safety and efficiency of your vehicle's fuel system. The use of nylon fittings is a common practice, offering a lightweight and flexible solution for fuel lines. However, it is essential to approach the installation process with caution and adhere to specific guidelines to guarantee a secure and reliable connection.
Nylon fittings are designed to provide a durable and corrosion-resistant connection, making them suitable for fuel line applications. These fittings typically feature a compression design, where the nylon material is compressed around the fuel line to create a tight seal. This compression ensures that the fuel line is securely held in place and prevents any potential leaks. To install these fittings, start by ensuring that the fuel line is clean and free of any debris or contaminants. This step is crucial as any foreign matter could compromise the seal.
The next step involves inserting the fuel line into the nylon fitting, ensuring that it is aligned correctly. Apply the manufacturer's recommended torque to the fitting's mounting hardware, being careful not to over-tighten, as this can damage the fuel line. The fitting should be snug, but not overly tight, to allow for a secure connection without causing any strain on the fuel line. It is essential to follow the manufacturer's instructions for torque specifications to avoid potential issues.
After the fitting is installed, inspect the connection for any signs of leakage. Apply a small amount of fuel or a suitable sealant to the connection and observe if there are any drips. If leakage is detected, carefully tighten the fitting further, ensuring that the seal is intact. Once the connection is secure, test the fuel system to ensure there are no further leaks.
Remember, proper installation is critical to the long-term performance and safety of your fuel system. Always refer to the manufacturer's guidelines and specifications for the specific nylon fitting you are using. These instructions will provide detailed information on torque values, installation techniques, and any unique considerations for your particular fuel line application. By following these guidelines, you can ensure a secure and reliable fuel line connection, minimizing the risk of fuel leaks and potential engine damage.
Mastering Napa Fuel Line Fixes: A Comprehensive Guide
You may want to see also
Frequently asked questions
Yes, nylon fittings can be used for fuel lines, especially in applications where flexibility and resistance to fuel-related chemicals are required. Nylon is known for its durability and ability to withstand various fuels, making it a popular choice for fuel system components.
Nylon fittings offer several benefits. They are lightweight, flexible, and resistant to corrosion, which is crucial for fuel lines as they often come into contact with different types of fuels. Additionally, nylon can provide a good seal, ensuring that fuel is contained and not leaked.
When installing nylon fittings, it is important to ensure a proper fit and secure connection. Nylon can be sensitive to extreme temperatures, so it's essential to use fittings that are designed for the specific fuel line application. Regular maintenance and inspection are also recommended to identify any signs of wear or damage.