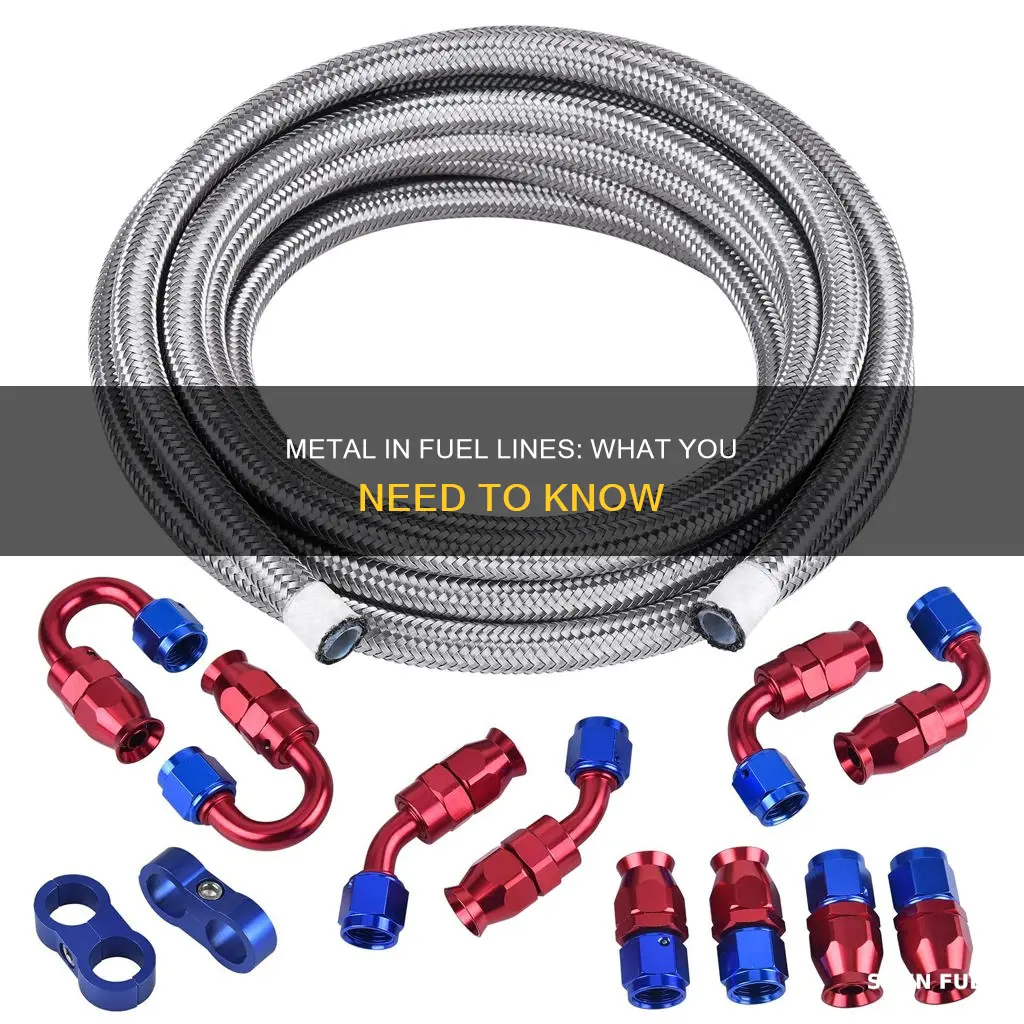
Adding metal to a fuel line is a topic that requires careful consideration and understanding of the potential risks and benefits. While some may suggest using metal components in fuel lines, it is generally not recommended due to the potential for corrosion, contamination, and reduced fuel efficiency. Metal can react with fuel, leading to the formation of harmful byproducts and potentially causing engine damage. Additionally, metal particles can be released into the fuel system, causing blockages and performance issues. It is crucial to consult with automotive experts or professionals to explore safe and effective alternatives for fuel line maintenance and modification.
What You'll Learn
- Safety Precautions: Always disconnect the fuel line and ensure proper ventilation before adding metal
- Fuel Line Material: Choose compatible metal, like brass or copper, to avoid corrosion
- Fitting Techniques: Use appropriate fittings and ensure a tight seal to prevent leaks
- Flow Control: Consider adding a fuel filter or restrictor to regulate metal particle flow
- Maintenance: Regularly inspect and replace metal components to ensure optimal fuel system performance
Safety Precautions: Always disconnect the fuel line and ensure proper ventilation before adding metal
When considering the idea of adding metal to a fuel line, it is crucial to prioritize safety and follow essential precautions. One of the most critical steps is to disconnect the fuel line to ensure that the fuel supply is completely isolated. This process should only be attempted by individuals with the necessary knowledge and experience, as it requires a thorough understanding of the vehicle's fuel system. By disconnecting the fuel line, you eliminate the risk of fuel spilling or leaking, which could lead to hazardous situations.
After disconnecting the fuel line, proper ventilation becomes a vital aspect of the process. Working in a well-ventilated area or outdoors is highly recommended to avoid inhaling potentially harmful fumes. Fuel and its vapor can be extremely flammable, and proper ventilation helps to disperse these gases, reducing the risk of fire or explosion. It is essential to take this step seriously and ensure that the work area is free from any ignition sources, such as open flames or sparks, to maintain a safe environment.
Before proceeding with any modifications or additions to the fuel line, it is imperative to inspect the line for any signs of damage or wear. Metal inserts or additives should only be considered if the fuel line is in excellent condition and free from leaks. Any pre-existing issues with the fuel line could be exacerbated by the introduction of metal, leading to potential safety hazards. Therefore, a thorough assessment of the fuel line's integrity is necessary to ensure a safe and successful outcome.
Additionally, it is advisable to consult the vehicle's manual or seek professional advice when dealing with fuel system modifications. Different vehicles may have specific requirements or recommendations regarding fuel line maintenance and modifications. Following the manufacturer's guidelines can help prevent any unintended consequences and ensure that the vehicle's performance and safety are not compromised.
In summary, when contemplating the addition of metal to a fuel line, safety should always be the top priority. Disconnecting the fuel line and ensuring proper ventilation are essential steps to mitigate potential risks. By taking these precautions, you create a safer working environment and reduce the chances of accidents or fuel-related incidents. It is a responsible approach to vehicle maintenance and ensures the well-being of both the individual and the vehicle's performance.
Fuel Line Options for 2009 Silverado: Who's the Best Supplier?
You may want to see also
Fuel Line Material: Choose compatible metal, like brass or copper, to avoid corrosion
When it comes to choosing the right material for your fuel line, compatibility with the fuel type and the metal itself are crucial factors to consider. One of the best options for fuel lines is the use of compatible metals, such as brass or copper. These materials are highly recommended due to their inherent resistance to corrosion, which is a common issue when dealing with fuel systems.
Brass, for instance, is an excellent choice for fuel lines because it offers a good balance of strength and corrosion resistance. It is known for its ability to withstand the corrosive effects of various fuels, including gasoline, diesel, and even ethanol blends. The use of brass ensures that the fuel line remains durable and reliable over an extended period, even in harsh operating conditions. Its natural resistance to oxidation and the formation of rust makes it an ideal material for fuel systems.
Similarly, copper is another metal that can be used for fuel lines, especially in applications where high conductivity is required. Copper has excellent electrical conductivity, which is beneficial for certain fuel systems that utilize electronic sensors and controls. However, it is important to note that copper may be more susceptible to corrosion compared to brass, especially in the presence of certain fuels. Therefore, it is essential to consider the specific fuel type and the environment in which the fuel line will operate.
In both cases, the key is to ensure that the chosen metal is compatible with the fuel being transported. Incompatible metals can lead to corrosion, which may result in fuel leaks, reduced performance, and potential safety hazards. By selecting brass or copper, you are taking a proactive approach to maintaining the integrity of your fuel system and ensuring its longevity.
Remember, when dealing with fuel lines, it is always best to consult with professionals or refer to manufacturer guidelines to determine the most suitable material for your specific application. The goal is to choose a metal that not only withstands the corrosive nature of fuels but also provides the necessary strength and durability required for the fuel line's function.
Mastering the Art of Fuel Line Clip Removal: A Step-by-Step Guide
You may want to see also
Fitting Techniques: Use appropriate fittings and ensure a tight seal to prevent leaks
When modifying or repairing a fuel line, it's crucial to focus on fitting techniques to ensure a secure and leak-free connection. The primary goal is to create a tight seal that can withstand the pressure and temperature changes associated with fuel transport. One effective method is to use specialized fittings designed for fuel lines. These fittings are often made from materials like brass or stainless steel, ensuring durability and compatibility with fuel. The key is to select the appropriate size and type of fitting that matches the fuel line's diameter and material. For instance, if you're working with a steel fuel line, you might opt for a steel fitting or a fitting with a steel insert to ensure a strong mechanical bond.
The process begins with thorough cleaning and preparation of both the fuel line and the fitting. Any dirt, grease, or old fuel residue must be removed to ensure a proper seal. This can be achieved using a suitable solvent or a high-pressure air blast to remove contaminants. Once prepared, the fitting should be inserted into the fuel line, ensuring it is centered and aligned correctly. Applying a thin layer of fuel-resistant sealant around the fitting's base can provide an additional layer of protection against leaks.
Tightening the fitting is a critical step, and it should be done with precision. Over-tightening can damage the fuel line, while under-tightening may result in an inadequate seal. The recommended torque value for the specific fitting and fuel line combination should be followed. This ensures that the fitting is secure without causing any damage. It's essential to check the torque regularly, especially if the vehicle is subjected to vibrations or extreme conditions, to ensure the seal remains intact.
In addition to the fitting itself, the connection between the fitting and the fuel line requires careful attention. Soldered joints or mechanical clamps can be used, but they must be applied correctly to avoid leaks. For soldered joints, ensure the fuel line and fitting are clean and free of oxide, then apply a flux to facilitate the soldering process. Allow the solder to cool and harden, creating a strong, permanent bond. Mechanical clamps, on the other hand, should be tightened evenly to apply consistent pressure, preventing any gaps that could lead to fuel leakage.
Finally, after the fitting and connection are in place, it's crucial to test the system for leaks. This can be done by applying pressure to the fuel line and checking for any signs of fuel escaping at the fitting or connection points. If any leaks are detected, the fitting or connection should be tightened or re-soldered as necessary. Regular maintenance and inspections will help ensure the fuel system remains leak-free, providing reliable performance and safety.
Ford Fuel Line Retention: A Step-by-Step Guide to Removing Clips
You may want to see also
Flow Control: Consider adding a fuel filter or restrictor to regulate metal particle flow
When considering the addition of metal to a fuel line, it's crucial to address the potential issues related to metal particle flow. Metal particles can be introduced into the fuel system through various means, such as wear and tear from the fuel pump, fuel injectors, or even the fuel tank itself. These particles can have detrimental effects on engine performance and longevity. To mitigate these risks, implementing flow control measures is essential.
One effective method to regulate metal particle flow is by installing a fuel filter. Fuel filters are designed to trap contaminants, including metal particles, from entering the engine. They act as a barrier, ensuring that only clean fuel reaches the engine's combustion chamber. Regularly replacing the fuel filter is vital to maintaining its effectiveness. Over time, filters can become clogged with accumulated particles, reducing their ability to filter out contaminants. Therefore, it is recommended to check and replace the fuel filter at regular intervals as per the vehicle manufacturer's guidelines.
In addition to fuel filters, fuel restrictors can also be employed to control metal particle flow. Fuel restrictors are devices that limit the amount of fuel entering the engine, which indirectly helps in managing metal particle concentration. By reducing the fuel flow rate, restrictors minimize the potential for metal particles to circulate and cause damage. This method is particularly useful in high-performance engines or applications where metal contamination is a concern. However, it's important to note that fuel restrictors should be used in conjunction with other filtration methods for optimal results.
When implementing flow control measures, it is essential to consider the specific requirements of your fuel system. Different engines and fuel configurations may necessitate unique solutions. Consulting the vehicle's manual or seeking professional advice can provide valuable insights into the most suitable filtration and restriction methods. Additionally, regular maintenance and monitoring of the fuel system can help identify and address any issues related to metal particle contamination.
In summary, adding metal to a fuel line can lead to significant problems, and implementing flow control measures is crucial. Fuel filters and restrictors play a vital role in regulating metal particle flow, ensuring that the engine operates efficiently and reliably. By incorporating these measures into your maintenance routine, you can minimize the risks associated with metal contamination and extend the lifespan of your fuel system. Remember, proper maintenance and regular inspections are key to keeping your engine in optimal condition.
Fuel Line Removal: A Step-by-Step Guide for LBZ Owners
You may want to see also
Maintenance: Regularly inspect and replace metal components to ensure optimal fuel system performance
Maintaining the fuel system in your vehicle is crucial for optimal performance and longevity. One critical aspect of this maintenance is the regular inspection and replacement of metal components within the fuel system. These components, including fuel lines, filters, and injectors, are susceptible to wear and tear over time, and proper care can prevent costly repairs and ensure efficient fuel delivery.
Metal components in the fuel system are particularly important as they are responsible for transporting fuel from the tank to the engine. Over time, these lines and filters can develop cracks, leaks, or become corroded, leading to reduced performance and potential safety hazards. Regular inspections are essential to identify any issues early on. You should check for any signs of damage, such as cracks, brittleness, or corrosion, especially in areas where the fuel lines connect to the tank and the engine. Look for any leaks or moisture in the lines, as these could indicate a compromised seal or a need for replacement.
When inspecting the fuel system, pay close attention to the metal components. Check the fuel lines for any visible damage or deterioration. Ensure that all connections are secure and free from corrosion. It is also a good practice to inspect the fuel filter, as a clogged or damaged filter can restrict fuel flow and cause engine performance issues. If you notice any signs of wear or damage, it is imperative to replace the affected components immediately. Delays can lead to further complications and potential engine damage.
Replacing metal components is a straightforward process, but it requires some mechanical knowledge and the right tools. Start by draining the fuel tank to avoid spills during the replacement process. Carefully remove the old fuel lines and filters, ensuring you have the correct replacement parts. When installing new components, ensure a tight fit and secure all connections. After the replacement, refill the fuel tank and test the system for any leaks. Regular maintenance and timely replacements will ensure your fuel system operates efficiently, providing optimal engine performance and reliability.
In summary, regular maintenance of the fuel system, particularly the metal components, is vital for vehicle owners. By inspecting and replacing worn-out parts, you can prevent fuel-related issues and maintain the overall health of your engine. Remember, proper care and attention to these details can save you from potential breakdowns and costly repairs in the long run.
Visual Guide: Kinked Fuel Line for 2008 LMM Duramax
You may want to see also
Frequently asked questions
It is not recommended to add any metal components directly to your fuel line. Metal can corrode and cause damage to the fuel system, leading to potential leaks and engine performance issues. It's best to consult a professional mechanic for any modifications or repairs to ensure the safety and efficiency of your vehicle.
Using metal in fuel lines can lead to several problems. Metal can cause blockages, restrict fuel flow, and create pressure points, which may result in fuel leaks. Additionally, metal components can come loose over time, leading to potential engine damage and costly repairs.
Yes, there are alternative materials that can be used for fuel lines, such as rubber, plastic, or composite materials. These materials are designed to withstand the corrosive effects of fuel and provide a reliable seal. It's important to choose the right material for your specific fuel type and vehicle requirements.
To ensure compatibility, it is crucial to consult the vehicle's manual or seek professional advice. Different vehicles may have specific requirements or recommendations for fuel line modifications. Using the right tools and materials for the job is essential to avoid any potential issues and ensure the longevity of your fuel system.