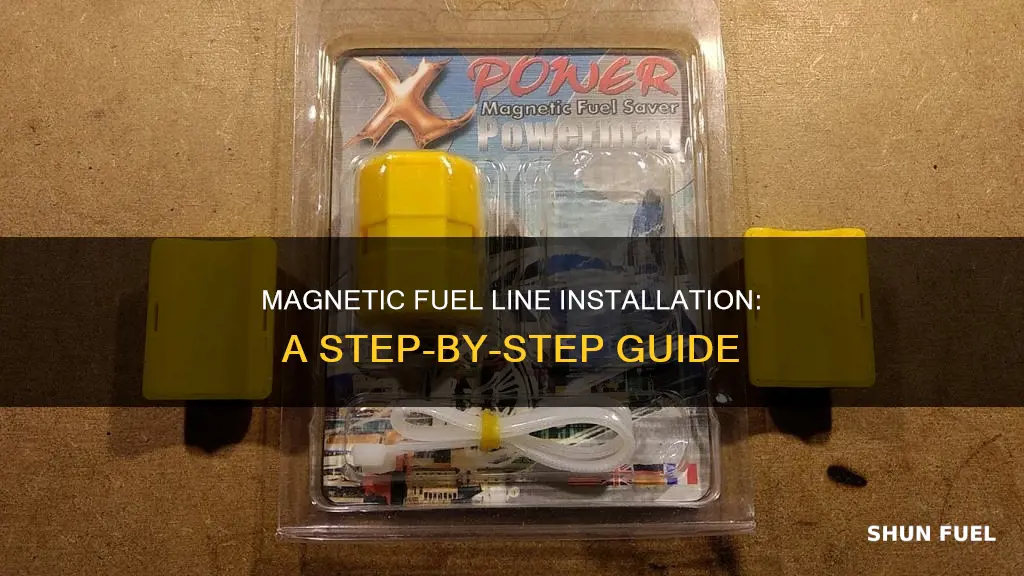
Installing magnets on fuel lines is a useful technique for preventing contamination and ensuring the longevity of your vehicle's fuel system. This process involves carefully placing magnets along the fuel line to attract and capture any metallic particles or contaminants that may be present in the fuel. By doing so, you can maintain the cleanliness of the fuel, which is crucial for optimal engine performance and longevity. This guide will provide a step-by-step process for installing magnets on your fuel line, ensuring a clean and efficient fuel supply.
What You'll Learn
- Fuel Line Preparation: Clean and inspect the fuel line to ensure it's free of debris and ready for magnet installation
- Magnet Selection: Choose the right magnet size and strength based on fuel line diameter and flow rate
- Installation Techniques: Explore various methods like welding, gluing, or using specialized clips for secure magnet attachment
- Safety Precautions: Follow safety guidelines to prevent fuel leaks and ensure proper ventilation during the installation process
- Testing and Adjustment: Verify magnet functionality by checking fuel flow and pressure, then fine-tune as needed
Fuel Line Preparation: Clean and inspect the fuel line to ensure it's free of debris and ready for magnet installation
Before you begin the process of installing magnets on a fuel line, it is crucial to ensure that the fuel line is clean and free of any debris or contaminants. This step is often overlooked but is essential for the success and safety of the installation. Start by removing the fuel line from the vehicle's fuel system, taking care not to damage the surrounding components. Once the fuel line is accessible, use a high-pressure water jet or a specialized fuel line cleaner to thoroughly rinse it. This process will help eliminate any dirt, rust, or old fuel residue that could interfere with the magnet's functionality.
After cleaning, inspect the fuel line for any signs of damage, such as cracks, punctures, or corrosion. Even a small tear or scratch can compromise the integrity of the fuel line and potentially lead to fuel leaks. If any damage is detected, it is best to replace the fuel line to ensure a secure and reliable installation. Pay close attention to the connections and fittings, as these areas are prone to accumulating debris and may require extra cleaning.
For a comprehensive inspection, consider using a magnifying glass or a small camera to examine the interior of the fuel line. This will allow you to identify any hidden debris, such as small metal particles or fuel contaminants, that might have been missed during the cleaning process. Ensuring that the fuel line is entirely clear of any foreign matter is vital to the magnet's performance and the overall safety of the vehicle's fuel system.
Once the fuel line is thoroughly cleaned and inspected, you can proceed with the magnet installation process, confident that the fuel line is now ready to support the new magnetic components without interference. Remember, proper preparation is key to a successful and long-lasting magnet installation.
Unraveling the Ultimate Marine Fuel Line Flexibility: A Comprehensive Guide
You may want to see also
Magnet Selection: Choose the right magnet size and strength based on fuel line diameter and flow rate
When installing magnets on a fuel line, selecting the appropriate magnet size and strength is crucial to ensure effective operation and prevent any potential issues. The goal is to create a strong magnetic field that can attract and hold the metal particles in the fuel without causing any blockages or interference. Here's a detailed guide on how to choose the right magnet for your fuel line:
Understanding the Fuel Line Parameters: Begin by assessing the specific characteristics of your fuel line. Measure the diameter of the fuel line as this will determine the size of the magnet required. Larger fuel lines will need more powerful magnets to handle the increased flow rate and potential debris. Additionally, consider the flow rate of the fuel. Higher flow rates might necessitate stronger magnets to maintain a consistent magnetic field throughout the line.
Magnet Size and Strength: The size and strength of the magnet should be proportional to the fuel line's diameter and flow rate. For smaller fuel lines with lower flow rates, a smaller neodymium magnet (e.g., 1/2" x 1/2" or 12mm x 12mm) might be sufficient. These magnets provide a good balance between attracting metal particles and not causing excessive drag, which could slow down the fuel flow. For larger fuel lines, consider using larger magnets like 1" x 1" (25mm x 25mm) or even custom-made magnets to ensure a strong magnetic field.
Material and Grade: Neodymium magnets are commonly used for fuel line applications due to their exceptional strength and resistance to demagnetization. Look for neodymium magnets with a high grade, such as N40 or higher, to ensure optimal performance. These magnets offer a good balance between strength and size, making them ideal for various fuel line diameters.
Testing and Adjustment: After installing the magnets, it's essential to test the system. Monitor the fuel flow and check for any signs of magnet interference, such as excessive noise or reduced flow rate. If needed, adjust the magnet placement or consider using multiple magnets along the fuel line to create a more uniform magnetic field.
Remember, the key to successful magnet installation is finding the right balance between magnet strength and fuel line requirements. By carefully selecting the magnet size and strength based on the fuel line's diameter and flow rate, you can effectively attract and hold metal particles, ensuring a smooth and efficient fuel supply while minimizing the risk of blockages.
Single Fuel Line Setup: LSX S10 Engine Optimization Guide
You may want to see also
Installation Techniques: Explore various methods like welding, gluing, or using specialized clips for secure magnet attachment
When it comes to installing magnets on a fuel line, there are several techniques to ensure a secure and reliable attachment. One common method is welding, which provides a strong and permanent bond. This process involves heating the magnet and the fuel line material to a high temperature, allowing the magnet to fuse with the fuel line. It is crucial to use a welding technique that is compatible with the specific fuel line material to ensure a strong and durable connection. For example, if the fuel line is made of steel, a steel-compatible welding process should be employed. This method is ideal for high-pressure applications where a strong and reliable connection is essential.
Another installation technique is gluing, which offers a more flexible approach. This method involves using a specialized adhesive that can withstand the harsh conditions of a fuel line environment. The adhesive is applied to the magnet and the fuel line, ensuring a strong bond. It is important to choose a glue specifically designed for high-temperature and fuel-resistant applications. This technique is suitable for situations where welding might be too invasive or time-consuming. The glue should be applied evenly and allowed to cure properly to ensure a secure attachment.
For a more discreet and less invasive approach, using specialized clips is an excellent option. These clips are designed to securely hold the magnet in place without causing any damage to the fuel line. The clips are typically made of durable materials that can withstand the fuel's pressure and temperature. They are easy to install and provide a reliable hold, making them a popular choice for many applications. Specialized clips are especially useful when working with fuel lines that have limited access or when a temporary installation is required.
In addition to these methods, it is essential to consider the specific requirements of the fuel line and the magnet's size and shape. Factors such as the fuel line's diameter, the magnet's strength, and the operating conditions will influence the chosen installation technique. For instance, a stronger magnet might require a more robust welding process or a specialized clip with a higher load-bearing capacity. Proper preparation and understanding of the fuel line's characteristics will ensure a successful and long-lasting installation.
Fuel Line Magnets: Myth or Magic? Unveiling the Truth
You may want to see also
Safety Precautions: Follow safety guidelines to prevent fuel leaks and ensure proper ventilation during the installation process
Before you begin the installation of magnets on a fuel line, it is crucial to prioritize safety to prevent any potential hazards. Fuel lines carry flammable substances, so any work involving them must be approached with caution. Firstly, ensure that the engine is turned off and the vehicle is in a secure location, away from any open flames or sparks. This is essential to avoid any accidental ignition of the fuel.
One of the primary safety measures is to prevent fuel leaks. When working with fuel lines, always inspect the connections and fittings for any signs of damage or corrosion. Tighten any loose connections securely, but be careful not to overtighten, as this can also cause damage. If you notice any cracks or leaks in the fuel line, it is imperative to replace the damaged section immediately. Even a small leak can lead to dangerous consequences, so do not compromise on this step.
Proper ventilation is another critical aspect of this process. Working in a well-ventilated area or outdoors is ideal to minimize the risk of inhaling fuel vapors. If working indoors, ensure the garage or workshop is equipped with a working exhaust system to remove any fumes. Always wear appropriate personal protective equipment (PPE), including gloves and a respirator mask, to protect yourself from inhaling harmful substances.
During the installation, be mindful of the magnet's placement. Magnets should be secured firmly but carefully to avoid any accidental dislodging. Ensure that the magnets do not come into contact with other metal components that could cause a short circuit or interference. Keep the work area clean and organized to reduce the risk of accidents.
Lastly, always refer to the vehicle's manual or consult a professional mechanic if you are unsure about any step. Safety should be the top priority when dealing with fuel systems, and it is better to seek expert advice to ensure a successful and safe installation. By following these safety precautions, you can minimize the risks associated with fuel line work and ensure a smooth installation process.
Fuel Line Flexibility: Adapting 1/4" to 5/8" Connections
You may want to see also
Testing and Adjustment: Verify magnet functionality by checking fuel flow and pressure, then fine-tune as needed
Before you begin the testing and adjustment process, it's crucial to understand the specific requirements and limitations of your vehicle's fuel system. This knowledge will guide your fine-tuning efforts and ensure the magnets are functioning optimally. Start by consulting your vehicle's manual or seeking professional advice to identify the ideal fuel flow and pressure parameters for your engine. This information will serve as a baseline for your testing.
The first step in verifying the magnet's functionality is to check the fuel flow. You can do this by monitoring the fuel pressure and volume during the engine's operation. Use a fuel pressure gauge to measure the pressure at various points in the system, including before and after the magnet. Compare these readings to the expected values for your engine. If the fuel flow is inconsistent or the pressure drops significantly, it may indicate a malfunction in the magnet or its installation.
Next, pay attention to the engine's performance. Start the engine and observe its behavior. A properly functioning magnet should ensure a steady and healthy fuel supply, resulting in smooth engine operation. Listen for any unusual noises, such as hissing or whistling, which could suggest a leak in the fuel system. Additionally, monitor the engine's response to acceleration and deceleration. A well-functioning magnet should provide a consistent and responsive power output.
If the initial checks reveal any issues, it's time to make adjustments. Fine-tuning the magnet's position or orientation might be necessary. Carefully realign the magnet to ensure it is correctly positioned relative to the fuel flow. Sometimes, a slight adjustment can significantly improve performance. After making any changes, re-test the fuel flow and pressure to ensure the magnet is now functioning as intended.
Remember, the key to successful testing and adjustment is patience and attention to detail. Take your time to carefully observe and measure the fuel flow and pressure. If adjustments are required, make small changes and re-test accordingly. This iterative process will help you fine-tune the magnet's performance and ensure it meets the specific needs of your vehicle's fuel system.
John Deere L110 Fuel Line Disconnect: A Step-by-Step Guide
You may want to see also
Frequently asked questions
Magnets are often installed on fuel lines to prevent ferromagnetic contaminants, such as metal particles or debris, from entering the fuel system. These contaminants can cause issues like engine misfires, reduced performance, and even damage to the fuel injectors or pump.
While it is possible to install magnets on a fuel line as a DIY project, it is recommended to have some mechanical knowledge and experience. If you are unsure or uncomfortable with the process, consulting a professional mechanic or automotive technician is advisable to ensure proper installation and avoid any potential risks.
The size and type of magnet will depend on various factors, including the fuel line diameter, the presence of any existing filters or strainers, and the specific requirements of your vehicle's fuel system. It's best to consult your vehicle's manual or seek advice from a professional to determine the appropriate magnet size and material (neodymium, ceramic, etc.) for your particular setup.
Yes, you will need a few tools to install magnets effectively. These may include a fuel line cutter or a fuel line repair kit, a fuel line crimper or clamp, and possibly a magnet holder or bracket. Having the right tools will ensure a secure and leak-free installation.
Magnets can be installed on various fuel line materials, but it's important to consider the compatibility and flexibility of the magnet and the fuel line. Some magnets may require a specific type of fuel line material, and extreme temperatures or pressure conditions might affect the installation process. Always refer to the manufacturer's guidelines or seek professional advice for the best results.