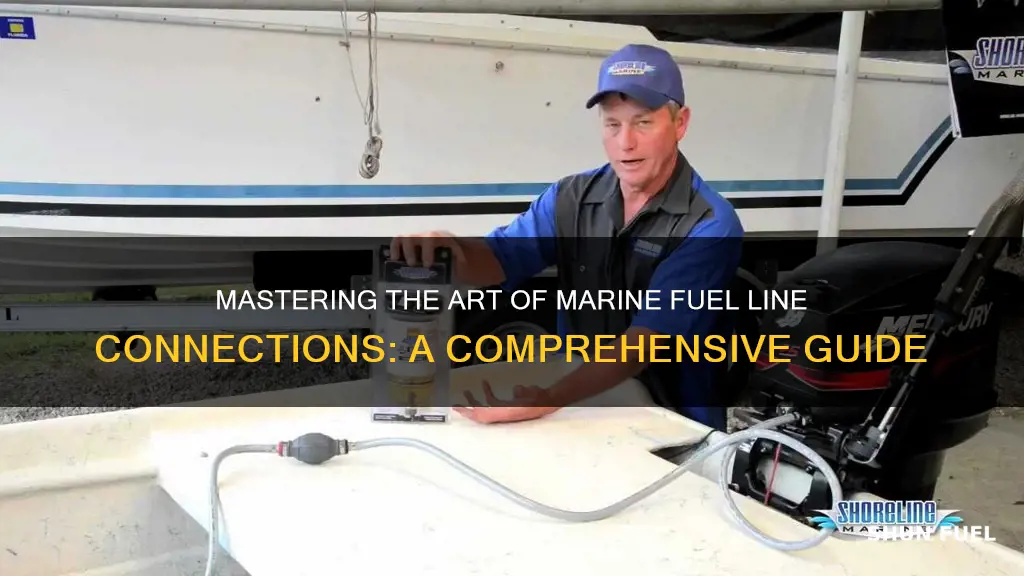
Installing a marine fuel line connector is a crucial step in ensuring the safe and efficient operation of your boat's fuel system. This process involves connecting the fuel line to the engine or fuel tank, and it requires careful attention to detail to prevent leaks and ensure a secure fit. In this guide, we will walk you through the step-by-step process of installing a marine fuel line connector, providing tips and best practices to help you complete the task with confidence and precision.
What You'll Learn
- Prepare Tools: Gather necessary tools like wrenches, pliers, and fuel line connectors
- Clean Connections: Ensure marine fuel line ends are clean and free of debris
- Align Components: Properly align fuel line and connector, ensuring a tight fit
- Secure with Clamps: Tighten fuel line clamps securely to prevent leaks
- Test for Leaks: Inspect connections for leaks after installation
Prepare Tools: Gather necessary tools like wrenches, pliers, and fuel line connectors
When it comes to installing a marine fuel line connector, having the right tools is essential to ensure a successful and secure connection. Here's a step-by-step guide on how to prepare the necessary tools:
Gather Wrenches and Pliers: Start by collecting a set of wrenches and pliers that are appropriate for the size of your fuel lines and connectors. Marine fuel lines often require specific tools due to their unique dimensions and threading. You'll typically need a set of adjustable wrenches to accommodate various sizes and a pair of adjustable pliers for gripping and turning. Ensure these tools are in good condition and can provide a firm grip without slipping.
Fuel Line Connectors: Obtain the appropriate fuel line connectors for your application. These connectors should be compatible with the type of fuel you are using and the specific requirements of your marine engine. Different engines may have unique connector designs, so it's crucial to match the connector to your engine's specifications. Consider the material of the connector, as some are made from durable plastics or metals, ensuring they can withstand the pressures and temperatures associated with fuel systems.
Additional Tools: Besides the primary tools, it's a good practice to have some extra items on hand. This includes thread seal tape or compound to ensure a tight and leak-free connection. You might also want to have a small brush or cloth to clean any debris or fuel residue from the fuel lines and connectors. Additionally, consider using a fuel line inspection mirror to visualize any hard-to-reach areas during the installation process.
By gathering these tools, you'll be well-prepared to tackle the installation of a marine fuel line connector. Remember, having the right equipment not only makes the job easier but also ensures a professional and safe connection for your marine fuel system.
C1500 Fuel Lines: A Comprehensive Guide to Identification
You may want to see also
Clean Connections: Ensure marine fuel line ends are clean and free of debris
When preparing to install a marine fuel line connector, it's crucial to ensure that the ends of the fuel lines are clean and free of any debris or contaminants. This step is often overlooked but is essential for a secure and reliable connection. Here's a detailed guide on how to achieve clean connections:
- Inspect the Fuel Line Ends: Begin by carefully examining the ends of both the fuel line and the connector. Look for any visible dirt, rust, corrosion, or debris. These contaminants can interfere with the connection and lead to potential issues during installation. Pay attention to any small crevices or openings where dirt might accumulate.
- Cleaning Process: Use a fine-bristled brush or a specialized cleaning tool designed for fuel lines. Gently scrub the ends of the fuel lines to remove any built-up dirt or grime. For more stubborn deposits, you might need to use a small wire brush or a tool with a wire brush attachment. Ensure that you clean both the inside and outside of the fuel line ends. If there is any corrosion, consider using a rust remover or a mild acid-based cleaner, but always test it in a small area first to avoid damage.
- Rinse and Dry: After cleaning, thoroughly rinse the fuel line ends with freshwater to remove any remaining cleaning agents or debris. Make sure there is no residue left. Then, allow the areas to dry completely. You can use a soft cloth or air to speed up the drying process. Moisture on the connector ends can cause issues during installation, so ensure they are entirely dry.
- Lubrication (Optional): Depending on the type of connector and your preference, you might consider applying a small amount of marine-grade lubricant to the threads or sealing surfaces of the connector. This step can improve the ease of installation and provide a tighter seal. However, be cautious not to over-lubricate, as excess lubricant can attract dirt and cause issues.
By following these steps, you'll ensure that the fuel line ends are clean and ready for a secure connection when installing the marine fuel line connector. This process is a critical part of marine maintenance to prevent potential fuel leaks and ensure the longevity of your vessel's fuel system.
Optimizing Performance: Choosing the Right Fuel Line for Your Honda GX 630
You may want to see also
Align Components: Properly align fuel line and connector, ensuring a tight fit
When installing a marine fuel line connector, proper alignment of the components is crucial to ensure a secure and leak-free connection. Here's a step-by-step guide to achieving this:
Start by carefully examining the fuel line and the connector. Ensure that the fuel line is free of any bends or kinks that could impede the installation process. The connector should be in good condition, with no visible damage or wear. Check for any manufacturer-specific instructions or guidelines provided with the connector, as some may have unique alignment requirements.
Begin the alignment process by positioning the fuel line along the connector. The fuel line should be routed in a way that allows for a smooth and continuous connection. Avoid any sharp bends or twists that could cause stress on the fuel line. Ensure that the fuel line is not too tight or too loose; it should fit snugly within the connector's housing.
Now, carefully align the connector onto the fuel line. Pay close attention to the orientation of the connector. It should be positioned in a way that allows for a secure and tight fit. The connector's threads or locking mechanism should be aligned with the fuel line's corresponding features. Gently push the connector onto the fuel line until it is fully seated. You should feel a distinct click or hear a slight snap, indicating a proper connection.
To ensure a tight fit, apply a small amount of thread sealant or fuel line tape around the connector's threads or locking mechanism. This additional step provides extra security and helps prevent leaks. Once the sealant is applied, give the connector a final twist to ensure it is fully engaged and locked in place.
By following these alignment steps, you can guarantee a secure and reliable connection for your marine fuel line. Proper alignment ensures that the fuel line is protected from potential damage and that the connector functions effectively, providing a safe and efficient fuel supply for your vessel. Remember, taking the time to align components correctly is essential for a successful and long-lasting installation.
Fuel Line Liter Valve: Location and Function
You may want to see also
Secure with Clamps: Tighten fuel line clamps securely to prevent leaks
When installing a marine fuel line connector, ensuring a secure and leak-free connection is crucial to prevent any potential issues on the water. One of the key steps to achieving this is by properly securing the fuel line with clamps. Here's a detailed guide on how to tighten fuel line clamps effectively:
Start by ensuring you have the right type of clamp for your fuel line. Marine fuel lines often require specialized clamps that are designed to withstand the harsh marine environment. These clamps should be made of durable materials like stainless steel or marine-grade aluminum to resist corrosion and provide a reliable seal. Once you have the appropriate clamp, locate the fuel line and position the clamp over it. Make sure the clamp is centered and covers the entire length of the fuel line where it connects to the connector.
Now, it's time to tighten the clamp securely. Use a wrench or a specialized fuel line clamp tool to apply firm pressure and tighten the clamp in a clockwise direction. Start with a gentle force and gradually increase the pressure, ensuring that the clamp makes firm contact with the fuel line. The goal is to create a snug fit without overtightening, as this can damage the fuel line. You should feel a resistance when turning the wrench, indicating that the clamp is securely in place.
To check the tightness, gently wiggle the fuel line to ensure the clamp doesn't move. If there is any play, you may need to tighten it further. However, be cautious not to over-tighten, as this can cause the fuel line to kink or damage the connector. A properly tightened clamp should provide a firm, yet flexible, hold, allowing the fuel line to move slightly without coming loose.
Remember, a secure connection is vital for the safe operation of your marine vessel. By following these steps and ensuring the fuel line clamps are tightened correctly, you can effectively prevent fuel leaks and ensure a reliable fuel supply to your engine. Regularly inspect the clamps and fuel lines during maintenance to identify any signs of wear or damage and replace them if necessary.
Mysterious Engine Issues: Uncover Air in Diesel Fuel Line Symptoms
You may want to see also
Test for Leaks: Inspect connections for leaks after installation
After installing the marine fuel line connector, it is crucial to conduct a thorough leak test to ensure the system's integrity. This step is often overlooked, but it is essential to verify that the connections are secure and free from any potential leaks. Here's a detailed guide on how to inspect for leaks:
Step 1: Gather the Necessary Tools
Before beginning the inspection, ensure you have the required tools. You will need a reliable method to detect fuel leaks, such as a fuel leak detector or a soapy water solution. These tools will help identify any small leaks that might not be visible to the naked eye.
Step 2: Apply a Leak Detection Method
Start by applying the chosen leak detection method to the fuel line connections. If using a fuel leak detector, spray it onto the connections and observe for any signs of bubbles or discoloration, indicating a leak. Alternatively, for a more visual approach, use soapy water and carefully examine the areas around the connectors. Look for any bubbles or foam forming, which would signify a leak.
Step 3: Inspect Each Connection
Carefully inspect every connection point, including the fuel line, the connector, and the engine's fuel injection system. Pay close attention to the threads, O-rings, and gaskets, as these are common areas where leaks can occur. Check for any signs of fuel seeping or dripping around the connections. Even a small leak can lead to significant issues over time.
Step 4: Document and Address Leaks
If you detect any leaks, it is crucial to address them immediately. Document the location and nature of the leak for future reference. Tighten any loose connections and ensure proper alignment. If the leak persists, consider replacing the affected components, such as O-rings or gaskets, to prevent further issues.
Step 5: Re-test and Verify
After making any necessary repairs or replacements, re-test the system to ensure the leak has been successfully resolved. Repeat the leak detection process to confirm that no further issues exist. This thorough inspection process ensures that your marine fuel system is reliable and safe for operation.
Remember, proper leak testing is a critical aspect of maintaining a marine fuel system's performance and longevity. It ensures that your vessel's fuel supply remains secure and efficient, contributing to a safer and more enjoyable boating experience.
Thawing Diesel Fuel Lines: Optimal Temperature for Winter
You may want to see also
Frequently asked questions
You will need a set of wrenches or spanners, a fuel line cutter or tool, and a fuel line crimping tool or connector kit. It's also recommended to have a fuel line cleaner and a rag for a neat and secure installation.
Start by cleaning the fuel lines to remove any dirt or debris. Cut the fuel line to the desired length, ensuring there is enough excess to crimp the connector. Use the fuel line cleaner to treat the cut end, then carefully insert it into the connector, following the manufacturer's instructions for the specific connector type.
It is not recommended to use regular connectors designed for other purposes, as they may not withstand the corrosive nature of marine fuel. Marine fuel line connectors are specifically designed to handle the unique challenges of fuel systems, including resistance to fuel degradation and corrosion.
One common mistake is not cleaning the fuel lines properly, which can lead to leaks. Another is using the wrong type of connector or not following the manufacturer's guidelines, potentially resulting in a poor connection. Always ensure you have the correct tools and take your time to follow the steps carefully for a successful installation.