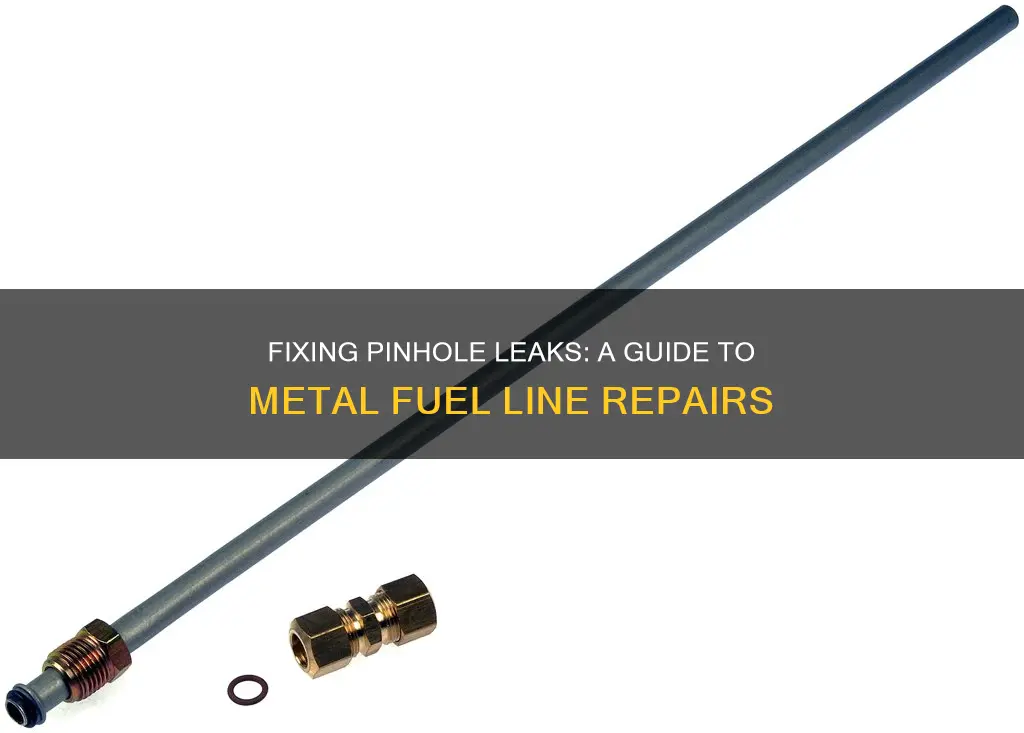
Fixing a pinhole in a metal fuel line requires careful attention to ensure the system remains safe and functional. This guide will outline the necessary steps to repair the damage, including identifying the pinhole, preparing the area, and applying the appropriate repair method. Whether you're a car enthusiast or a professional mechanic, understanding how to address this issue is crucial for maintaining the integrity of your vehicle's fuel system.
What You'll Learn
- Identify the Pinhole: Inspect the fuel line for a small hole or crack
- Prepare Materials: Gather necessary tools: welding equipment, flux, and replacement parts
- Weld Repair: Use a suitable welding process to seal the pinhole securely
- Test for Leaks: After welding, check for any fuel leaks around the repair
- Replace if Necessary: If the damage is extensive, consider replacing the affected section of the fuel line
Identify the Pinhole: Inspect the fuel line for a small hole or crack
When dealing with a pinhole in a metal fuel line, the first crucial step is to identify the exact location and nature of the damage. This process requires a careful and methodical inspection of the fuel line. Start by visually examining the fuel line for any visible signs of damage. Look for small holes, cracks, or any other abnormalities that might indicate a pinhole. These defects can often be found where the fuel line bends, near connections, or at points where it has been subjected to stress or friction.
Pay close attention to the metal surface of the fuel line. A pinhole might appear as a tiny dark spot or a small indentation. It could be a result of corrosion, fatigue, or even a manufacturing defect. In some cases, the pinhole might be covered by a thin layer of fuel or debris, making it even more challenging to spot. If you suspect a pinhole, use a bright light source to illuminate the area and inspect it from different angles to get a clearer view.
For a more thorough inspection, consider using a magnifying glass or a small flashlight to help you see the area more clearly. Carefully run your fingers along the length of the fuel line to feel for any sharp edges or irregularities that might indicate a pinhole. This tactile inspection can be particularly useful in identifying small defects that might not be visible to the naked eye.
If the fuel line is accessible, you can also consider removing it from the vehicle to get a better view and a more comprehensive inspection. This might be necessary if the pinhole is located in a hard-to-reach area or if the fuel line is part of a complex system. Once you've identified the pinhole, you can proceed with the appropriate repair or replacement measures to ensure the integrity of the fuel system.
Transmission Oil Cooler Hose: A Fuel Line Substitute?
You may want to see also
Prepare Materials: Gather necessary tools: welding equipment, flux, and replacement parts
Before you begin the repair process, it's crucial to gather all the necessary tools and materials to ensure a successful fix. For welding a pinhole in a metal fuel line, you'll need a few essential items. Firstly, welding equipment is a must-have. This includes a welding torch, which provides the heat required to melt and join the metal. Ensure you have a suitable torch for the type of welding you plan to do, such as a gas-powered torch for more precise work. Additionally, a welding helmet with a shade suitable for the welding process is essential for eye protection.
Flux is another critical component. It is a substance applied to the welding area to protect the metal from oxidation and to facilitate the welding process. Choose a flux suitable for the metal type you are working with, as different metals require specific fluxes. You can find flux in various forms, such as powders, pastes, or rods, depending on your welding method.
Replacement parts are also necessary to ensure a proper repair. If the pinhole is significant, you might need to replace a section of the fuel line. Gather a length of replacement metal fuel line that matches the diameter and material of the original line. It's a good idea to have a few extra inches to allow for any adjustments during the welding process. Additionally, consider having some metal filler rod that matches the fuel line's material for any minor repairs or touch-ups.
Ensure you have a sturdy workbench or a stable surface to set up your welding equipment. Having a well-organized workspace will make the repair process more efficient. With these materials and tools prepared, you'll be ready to proceed with the welding process and effectively fix the pinhole in the metal fuel line. Remember to always prioritize safety and follow proper welding procedures to ensure a successful and secure repair.
Mastering Chainsaw Maintenance: A Guide to Replacing Fuel Lines
You may want to see also
Weld Repair: Use a suitable welding process to seal the pinhole securely
When dealing with a pinhole in a metal fuel line, a secure and effective repair method is welding. This process involves using a welding technique to create a strong, permanent seal, ensuring the integrity of the fuel line and preventing any potential leaks. Here's a step-by-step guide on how to approach this repair:
Step 1: Prepare the Materials and Equipment
Gather the necessary tools and materials for the welding process. You'll need a welding machine or torch with the appropriate power source (e.g., gas-powered or electric) and a suitable welding rod or wire. Choose a welding rod that matches the base metal's composition to ensure compatibility and strength. Additionally, have a flux-core wire if you plan to use a flux-core welding process, which is ideal for outdoor applications due to its self-fluxing nature.
Step 2: Clean and Prepare the Pinhole
Before welding, ensure the pinhole is clean and free from any debris or contaminants. Use a wire brush or a small wire brush attachment to gently clean the area around the hole. Remove any rust or corrosion that might interfere with the welding process. It's crucial to have a clean and dry surface for optimal welding.
Step 3: Apply Welding Technique
There are various welding techniques you can employ, such as gas welding, flux-core welding, or shielded metal arc welding (SMAW). For a pinhole repair, a flux-core process is often preferred for its simplicity and ease of use. Here's a basic outline:
- Set up your welding machine and adjust the settings according to the manufacturer's instructions.
- Position the welding rod or wire at a slight angle to the pinhole, ensuring it is perpendicular to the surface.
- Initiate the weld by striking an arc and maintaining a consistent flame or heat source.
- Move the torch along the pinhole, creating a bead of weld around the hole. Ensure the weld bead is clean and free of any defects.
- For a stronger bond, consider adding a second pass of weld in the opposite direction, overlapping the first pass slightly.
Step 4: Post-Welding Care
After the welding process, allow the weld to cool and solidify. Avoid immediate stress or pressure on the repaired area to ensure the integrity of the weld. Once cooled, inspect the weld for any defects or imperfections and consider using a post-weld heat treatment to further strengthen the metal.
Welding is a powerful method to repair pinholes in metal fuel lines, providing a reliable and long-lasting solution. It is essential to follow safety protocols and guidelines when working with welding equipment and materials. With the right techniques and precautions, you can effectively seal the pinhole and restore the fuel line's functionality.
Fuel Lines: Unveiling the Differences and Their Impact
You may want to see also
Test for Leaks: After welding, check for any fuel leaks around the repair
After completing the welding process to repair a pinhole in a metal fuel line, it is crucial to conduct a thorough test for leaks to ensure the integrity of the repair. This step is essential to prevent potential fuel leaks, which can lead to hazardous situations and costly damage. Here's a detailed guide on how to perform this critical test:
Preparation: Before beginning the leak test, ensure that the fuel line is completely cooled and that all welding equipment and tools are properly cleaned and stored. It is also advisable to wear protective gear, such as gloves and safety goggles, to minimize any potential risks during the testing process.
Visual Inspection: Start by visually inspecting the welded area. Look for any signs of uneven welding, excessive heat damage, or visible cracks. These issues could potentially lead to leaks, so any problems should be addressed before proceeding. If you notice any defects, carefully remove the weld and re-weld the area, ensuring a strong and consistent joint.
Soapy Water Test: This is a simple and effective method to detect leaks. Fill a bucket or basin with soapy water, ensuring a generous amount of soap is present. Carefully submerge the repaired fuel line section into the soapy water, ensuring it is fully covered. Observe the water surface for any bubbles or soap suds forming around the welded area. Bubbles indicate the presence of air, which could be a sign of a potential leak. If bubbles are observed, it is crucial to investigate further and identify the source of the air entry.
Pressure Test: For a more comprehensive assessment, a pressure test can be performed. This method involves using a pressure gauge and a suitable fluid, typically a non-corrosive liquid like water or a specialized fuel line testing fluid. Attach the pressure gauge to the fuel line, ensuring a secure connection. Gradually increase the pressure in the line and monitor the gauge. A successful repair should maintain the pressure without any significant drops. If the pressure drops or if you notice any hissing sounds, it indicates a potential leak and requires further investigation.
Professional Assistance: If you are unsure about any aspect of the leak test or if the repair seems complex, it is highly recommended to seek professional assistance. Automotive mechanics or fuel line specialists can provide expert guidance and ensure the job is done safely and effectively.
By following these steps, you can effectively test for leaks after welding a pinhole repair in a metal fuel line, ensuring a safe and reliable fuel system.
Fuel Rail Disconnection: A Step-by-Step Guide to a Smooth Process
You may want to see also
Replace if Necessary: If the damage is extensive, consider replacing the affected section of the fuel line
If you've identified that the damage to your metal fuel line is extensive and cannot be effectively repaired, the best course of action is to replace the affected section. This is a crucial step to ensure the safety and efficiency of your vehicle's fuel system. Here's a detailed guide on how to approach this replacement:
Assess the Damage: Before proceeding, thoroughly inspect the fuel line to understand the extent of the damage. Look for any visible holes, tears, or corrosion that might have compromised the line's integrity. Note the location of the damage and measure the length of the affected section. This assessment will help you determine the appropriate replacement size and ensure a proper fit.
Gather the Necessary Tools and Materials: Replacing a fuel line requires a few essential tools and materials. You'll need a new metal fuel line of the appropriate size, a fuel line cutter or a suitable cutting tool, a fuel line primer and solvent, and a fuel line clamp or fitting. Ensure you have the correct specifications for your vehicle's fuel line to avoid any compatibility issues.
Prepare the Work Area: Choose a suitable location for the repair, preferably a well-ventilated area away from open flames or sparks. Lay down a clean, flat surface to work on, and gather all the necessary tools and materials within reach. It's essential to work efficiently and safely to minimize any potential hazards.
Cut and Prepare the New Fuel Line: Using the fuel line cutter or your chosen cutting tool, carefully cut the new fuel line to the required length, ensuring it is slightly longer than the damaged section to allow for proper installation. Remove any excess material, leaving a clean, straight edge. If necessary, use the fuel line primer and solvent to ensure a secure connection between the new line and the existing fuel system.
Install the New Fuel Line: Start by inserting the new fuel line into the vehicle's fuel system, connecting it to the appropriate ports or fittings. Ensure a tight, secure fit by using the fuel line clamp or fitting. Follow the manufacturer's instructions for the specific vehicle model to guarantee a proper installation.
Test and Inspect: Once the new fuel line is installed, start the vehicle's engine and check for any leaks. Ensure that the fuel system is functioning correctly and that there are no signs of fuel leakage. Inspect the entire fuel line for any signs of strain or improper installation, addressing any issues promptly.
Remember, replacing a fuel line is a specialized task, and it's recommended to seek professional assistance if you're unsure about any step. Proper installation is crucial to maintain the safety and performance of your vehicle's fuel system.
Fuel and Brake Line Costs: A Breakdown of Expenses
You may want to see also
Frequently asked questions
Pinholes in metal fuel lines can be caused by various factors, including corrosion, oxidation, or physical damage. Over time, the metal can deteriorate due to exposure to fuel, moisture, or harsh environmental conditions, leading to tiny holes or cracks.
For a temporary fix, you can use a metal repair clamp or a temporary patch. Clean the affected area, apply a thin layer of epoxy or silicate-based adhesive, and then carefully place the clamp or patch over the hole to seal it. This will provide a short-term solution while you consider more permanent repairs.
1. Drain the fuel line to prevent any spills. 2. Cut out the damaged section of the line. 3. Clean and prepare the metal surfaces. 4. Use a metal repair compound or a specialized metal welding kit to fill and repair the hole. 5. Ensure a proper bond by following the manufacturer's instructions. 6. Test the repair by refilling the line and checking for leaks.