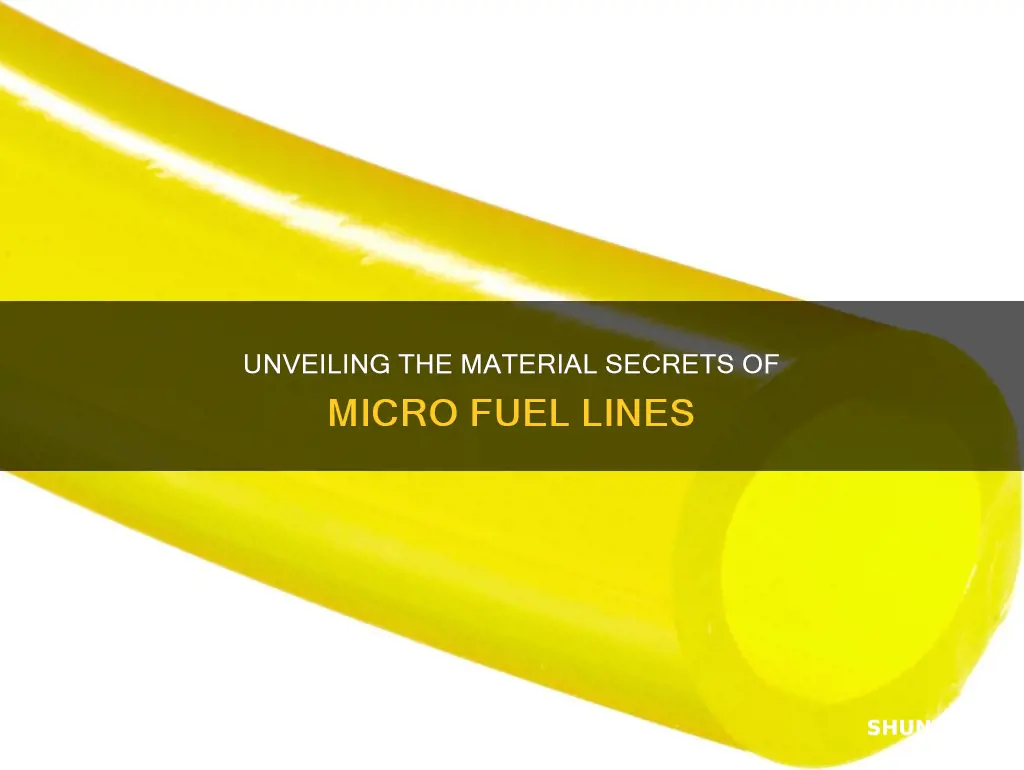
The micro fuel line is a crucial component in the delivery of fuel to an engine, and its material composition is essential for optimal performance and longevity. These lines are typically made from a variety of materials, each chosen for its unique properties to withstand the challenges of fuel transport. Common materials include high-density polyethylene (HDPE), which offers excellent chemical resistance and flexibility, making it ideal for the dynamic nature of fuel lines. Additionally, materials like stainless steel and aluminum alloys are used for their strength and durability, especially in high-pressure applications. The choice of material depends on factors such as the type of fuel, operating conditions, and the specific requirements of the engine system. Understanding the composition of micro fuel lines is key to ensuring their compatibility and reliability in various automotive and industrial settings.
Characteristics | Values |
---|---|
Material | Typically made of high-temperature plastics like PEEK (polyether ether ketone) or PEI (polyetherimide), or metals like stainless steel or aluminum. |
Temperature Range | Can withstand temperatures from -452°F (-269°C) to 572°F (300°C) or higher, depending on the material. |
Flexibility | Often designed to be flexible to accommodate engine vibrations and movement. |
Corrosion Resistance | Resistant to corrosion from fuels and engine fluids. |
Pressure Rating | Capable of withstanding high pressure, often up to 1000 psi or more. |
Size | Very small in diameter, typically ranging from 0.010" to 0.050" (0.25mm to 1.27mm). |
Length | Can be very long, often several feet in length, depending on the application. |
Compatibility | Compatible with various fuels, including gasoline, diesel, jet fuel, and biofuels. |
Weight | Lightweight to minimize the load on the engine. |
Manufacturing Process | Often produced using precision molding or extrusion techniques. |
What You'll Learn
- Materials: Micro fuel lines are typically made from materials like plastic, rubber, or metal alloys
- Flexibility: The choice of material ensures flexibility and durability for fuel transport
- Strength: Materials must withstand pressure and temperature changes in fuel systems
- Compatibility: Materials are chosen to be compatible with the fuel type and system
- Cost: Different materials offer varying costs, impacting the overall system's affordability
Materials: Micro fuel lines are typically made from materials like plastic, rubber, or metal alloys
Micro fuel lines are an essential component in the intricate network of a vehicle's fuel system, responsible for delivering fuel from the tank to the engine in a precise and controlled manner. These lines are designed to be compact and flexible, allowing them to navigate the complex layout of a vehicle's engine bay. The choice of material for these micro fuel lines is crucial, as it directly impacts their performance, durability, and compatibility with the fuel they carry.
The primary materials used for manufacturing micro fuel lines are plastic, rubber, and metal alloys. Each material offers unique advantages and is selected based on the specific requirements of the fuel system. Plastic, for instance, is a popular choice due to its lightweight nature and flexibility. It is often used for the inner lining of the fuel lines, providing a protective barrier between the fuel and the metal components. Plastic fuel lines are known for their resistance to corrosion and their ability to withstand high temperatures, making them suitable for a wide range of automotive applications.
Rubber, another common material, is valued for its excellent flexibility and resilience. It can accommodate the constant movement and vibration within a vehicle's engine bay without compromising its structural integrity. Rubber fuel lines are particularly useful in areas where sharp bends and tight spaces are prevalent, ensuring a reliable fuel supply even in challenging environments. The natural damping properties of rubber also help reduce fuel noise, contributing to a quieter and more comfortable driving experience.
Metal alloys, such as brass or stainless steel, are employed for their superior strength and durability. These materials are ideal for high-pressure fuel lines that require robust construction to handle the demanding conditions of an engine's fuel system. Metal fuel lines offer excellent resistance to corrosion and can withstand extreme temperatures, ensuring a long-lasting and reliable performance. However, they are generally more rigid and less flexible compared to plastic or rubber, which can be a consideration during installation.
The choice of material for micro fuel lines is a critical aspect of vehicle engineering, as it influences the overall performance, safety, and longevity of the fuel system. Each material brings its own set of advantages, and the decision is often based on a careful evaluation of factors such as fuel type, operating temperatures, space constraints, and the specific requirements of the vehicle's design. By selecting the appropriate material, engineers can ensure that the micro fuel lines function optimally, delivering fuel efficiently while maintaining the integrity of the entire fuel system.
Understanding Marine Fuel Lines: A Comprehensive Guide
You may want to see also
Flexibility: The choice of material ensures flexibility and durability for fuel transport
The choice of material for micro fuel lines is a critical aspect of their design, especially when considering the flexibility and durability required for fuel transport. These lines are typically made from specialized materials that offer a unique combination of properties to ensure efficient and safe operation. One of the key materials used is a high-performance polymer, often a type of polyolefin, which provides excellent flexibility. This flexibility is essential for the micro fuel lines' ability to navigate through tight spaces and bends in the vehicle's fuel system without kinking or breaking. The polymer's inherent flexibility allows it to withstand the various movements and vibrations experienced during vehicle operation, ensuring a reliable fuel supply.
In addition to flexibility, the material's durability is another critical factor. Fuel transport lines must be able to withstand the corrosive effects of fuel, especially in the presence of ethanol-blended gasoline. The chosen polymer should have excellent chemical resistance to prevent degradation and ensure the long-term integrity of the fuel line. This durability is further enhanced by the use of reinforcing materials, such as braided fibers or metal braids, which provide additional strength and protection against punctures or cuts. These reinforcing elements are strategically placed in areas where the fuel line is most susceptible to damage, such as at connections or bends.
The manufacturing process also plays a significant role in achieving the desired flexibility and durability. Techniques such as extrusion and molding are employed to shape the polymer into the required fuel line configuration. During extrusion, the polymer is heated and drawn through a die, allowing for precise control over its thickness and cross-sectional shape. This process ensures that the fuel line has a consistent and flexible profile, making it adaptable to various fuel system layouts. Additionally, the material's molecular structure is carefully considered to optimize its flexibility without compromising strength, ensuring the fuel line can withstand the rigors of fuel transport.
Furthermore, the choice of material can also impact the fuel line's resistance to temperature fluctuations. Micro fuel lines may be exposed to varying temperatures, especially in different climates or during rapid acceleration. The selected polymer should have a suitable temperature range to maintain its flexibility and structural integrity under these conditions. This ensures that the fuel line remains pliable and functional, even when subjected to extreme temperatures, which is crucial for overall system reliability.
In summary, the flexibility and durability of micro fuel lines are directly linked to the choice of material. High-performance polymers, combined with reinforcing elements, provide the necessary flexibility and strength to navigate through fuel systems while withstanding the corrosive effects of fuel. The manufacturing process, including extrusion and molding, further refines the material's properties, ensuring a consistent and reliable fuel transport solution. By carefully selecting and engineering the material composition, engineers can create micro fuel lines that meet the demanding requirements of modern vehicles, ensuring efficient and safe fuel delivery.
Backwards Fuel Lines: A Recipe for Disaster
You may want to see also
Strength: Materials must withstand pressure and temperature changes in fuel systems
The micro fuel lines, often referred to as high-pressure fuel lines, are an essential component in modern fuel injection systems, particularly in automotive applications. These lines are designed to transport fuel under high pressure from the fuel tank to the engine's fuel injectors. The primary challenge in designing such lines is ensuring they can withstand the extreme conditions within the fuel system, including varying temperatures and pressures.
The materials used for these lines must possess exceptional mechanical properties to meet these demands. One of the most common materials for this purpose is stainless steel, specifically types 304 or 316. These stainless steel alloys are renowned for their strength, corrosion resistance, and ability to maintain structural integrity under high stress and temperature fluctuations. The microstructure of stainless steel, with its austenitic or ferritic phases, provides excellent tensile strength and ductility, making it ideal for fuel lines that need to flex and bend during engine operation.
In addition to stainless steel, some manufacturers also utilize composite materials, such as braided stainless steel hoses with a synthetic inner lining. This design offers a balance between strength and flexibility. The braided stainless steel provides the necessary rigidity and pressure resistance, while the synthetic inner lining ensures the line can withstand the corrosive effects of fuel and maintain its shape.
Another critical aspect of material selection is the ability to resist fuel-related degradation. Fuel, especially when it contains ethanol or other additives, can be corrosive over time. Materials like fluoropolymers or specialized coatings are often applied to the inner surface of the fuel lines to create a protective barrier, preventing fuel from coming into direct contact with the metal and causing corrosion or degradation.
Furthermore, the design of the fuel lines themselves is crucial. Engineers often incorporate features like reinforced layers, braids, or helical winding to enhance the line's ability to withstand pressure and temperature changes. These design elements help distribute stress evenly and prevent localized failures, ensuring the fuel lines remain intact and functional over the long term.
Unveiling Ford's Fuel Supply Line Color: A Quick Guide
You may want to see also
Compatibility: Materials are chosen to be compatible with the fuel type and system
When designing and selecting materials for micro fuel lines, compatibility is a critical factor. The choice of materials directly impacts the performance, reliability, and longevity of the fuel system. Here's a detailed look at why compatibility matters and how it influences the composition of micro fuel lines:
Fuel Type Compatibility: Different fuels have unique chemical properties and characteristics. For instance, gasoline, diesel, and aviation fuels have varying compositions and boiling points. Micro fuel lines must be compatible with the specific fuel type to ensure optimal performance and prevent issues like fuel degradation, corrosion, or contamination. Materials that are resistant to the corrosive effects of the fuel are essential to maintain the integrity of the fuel system over time.
System Compatibility: Micro fuel lines are part of a larger fuel system, which includes fuel tanks, pumps, injectors, and other components. The materials used in these lines should be compatible with the entire system to avoid any adverse reactions. For example, certain plastics or metals might react with the fuel or other system components, leading to performance issues or material degradation. Therefore, careful consideration of material properties and their compatibility with the entire fuel system is necessary.
Chemical Resistance: The chosen materials should exhibit excellent chemical resistance to withstand the various chemicals present in different fuels. This resistance helps prevent fuel leaks, corrosion of the fuel system components, and potential health hazards. For instance, materials like stainless steel, aluminum alloys, and specific plastics are often used for their inherent chemical resistance, ensuring the micro fuel line can handle the specific fuel it is designed for.
Temperature and Pressure Considerations: Fuel lines must also be compatible with the temperature and pressure conditions they will encounter. Different fuels have varying temperature requirements and pressure levels. Materials should be able to maintain their structural integrity and performance within these ranges. For high-pressure systems, materials with excellent tensile strength and flexibility are preferred to ensure the line can withstand the forces without compromising its functionality.
Longevity and Durability: Compatibility also extends to the long-term durability of the fuel line. Materials should be chosen to ensure the fuel line's longevity, especially in harsh operating conditions. This includes resistance to UV radiation, ozone, and environmental factors that could accelerate material degradation. By selecting materials that are compatible with the fuel and system, engineers can ensure the fuel line's performance and reliability over an extended period.
In summary, compatibility is a key consideration when determining the composition of micro fuel lines. It involves selecting materials that can withstand the specific fuel's properties, react appropriately with the fuel system, and maintain performance under various conditions. This ensures the fuel line's reliability, safety, and efficiency in delivering fuel to the engine.
Understanding Fuel Injection Lines: A Comprehensive Guide
You may want to see also
Cost: Different materials offer varying costs, impacting the overall system's affordability
The composition of a micro fuel line is a critical aspect of its functionality and performance, especially in the context of cost. The material used in the construction of these lines plays a significant role in determining the overall affordability of the system. Different materials offer varying costs, and this can have a direct impact on the final price of the product.
For instance, one of the most common materials used for micro fuel lines is stainless steel. This metal is known for its durability and resistance to corrosion, making it an excellent choice for fuel lines that need to withstand harsh environments. However, stainless steel is generally more expensive than other materials, which can increase the overall cost of the system. On the other hand, materials like aluminum or brass might be more cost-effective, but they may not offer the same level of durability and corrosion resistance as stainless steel.
The choice of material also depends on the specific application and requirements of the fuel line. For high-performance engines or applications where the line is exposed to extreme temperatures, a more expensive material might be justified to ensure longevity and reliability. In contrast, for less demanding applications, a less expensive material could be used to keep costs down.
Additionally, the manufacturing process can also influence the cost. Some materials might require more complex manufacturing techniques, which can drive up the price. For example, lines made from materials like carbon fiber or advanced composites might be more expensive to produce but could offer superior performance and durability.
In summary, the material selection for micro fuel lines is a critical factor in determining the cost of the system. Different materials offer varying levels of performance, durability, and cost, and the choice should be made based on the specific requirements of the application. Balancing the need for performance with the budget constraints is essential to ensure the overall affordability and effectiveness of the fuel line system.
Houston Fuel Lines: Uncovering Hidden Issues and Solutions
You may want to see also
Frequently asked questions
Micro fuel lines, also known as small-diameter fuel lines, are typically made from materials like stainless steel, aluminum, or brass. These materials are chosen for their durability, corrosion resistance, and ability to withstand high temperatures and pressures commonly found in fuel systems.
The choice of material is crucial for micro fuel lines as they are exposed to harsh environments. Stainless steel offers excellent corrosion resistance, making it ideal for fuel lines in vehicles. Aluminum is lightweight and has good thermal conductivity, which can be beneficial in certain applications. Brass provides a balance of strength and corrosion resistance, ensuring the fuel line's longevity.
Yes, depending on the specific requirements of the fuel system and the vehicle, different materials can be used. For example, in high-performance applications, materials like stainless steel or aluminum alloys might be preferred for their strength and heat resistance. In some cases, flexible materials like rubber or silicone may be used for micro fuel lines, especially in areas with limited space or high flexibility demands.
The material selection directly influences the performance and reliability of micro fuel lines. Materials with high tensile strength ensure the lines can withstand fuel pressure without deforming. Corrosion-resistant materials prevent degradation over time, ensuring a longer lifespan. Additionally, materials with good thermal properties can help manage fuel temperature variations.
Yes, various automotive and industry standards dictate the materials and manufacturing processes for fuel lines. These standards ensure that the materials used meet specific requirements for safety, performance, and compatibility with fuels. Adhering to these standards is essential to guarantee the quality and reliability of micro fuel lines in different applications.